Corrugated iron sheet roll forming machines efficiently transform metal coil stock into roofing panels featuring a distinctive waved pattern used extensively across industrial and residential building projects globally thanks to longevity benefits in wet climates. This guide offers metal fabricators, panel installers and construction companies detailed insights on corrugated roll former line types, key technical specifications, Chinese equipment suppliers, pricing, installation best practices and total cost of ownership comparisons against alternate corrugated sheet production methods.
Overview of Corrugated Iron Sheet Roll Forming Equipment
Roll forming machinery incrementally converts coiled steel or aluminum through consecutive roller dies progressively shaping strip metals into various symmetrical cross-sectional panel profiles for roofing, bridges, warehouse cladding and agricultural building projects where large surface areas get covered.
Table 1: Background on Corrugated Iron Sheet Roll Formers
Parameter | Description |
---|---|
Working Principle | Continuous bending through sequential roller dies |
Key Components | Decoiler, forming stations, hydraulic system, cutoff shear |
Source Materials | Prepainted steel, aluminum, zinc alloy coated coils |
Wave Patterns | Sinusoidal, trapezoidal and custom profiles |
Width Capacity | Up to 2.5 meter possibilities |
Output Speed | 6 – 20 meters per minute |
Primary Applications | Industrial roofing and siding for factories, warehouses, livestock shelters |
Unlike alternative fabrication approaches requiring fixed dies like press braking or stamping, the incremental bending nature of roll forming allows cost effective short, medium or mass production runs once initial tooling gets developed – ideal for the repetitive corrugations characterizing metal envelope solutions for larger new buildings or re-cladding retrofit projects.
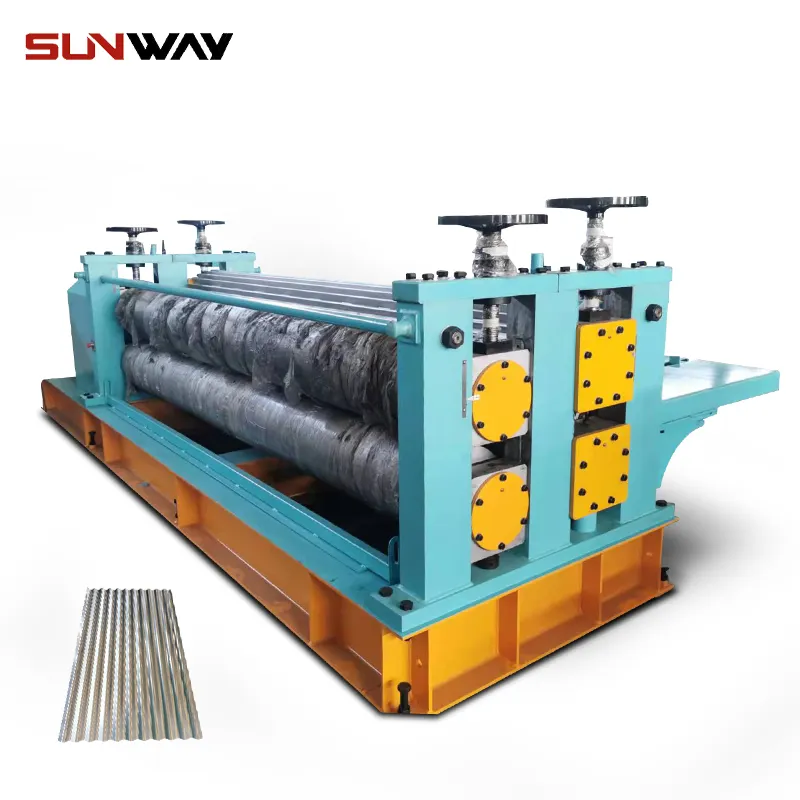
Working Principle of Corrugated Roll Forming Machines
Corrugated roll forming machinery converts coiled metals into roofing or panels featuring a distinctive waveform profile by progressing stock through consecutive roller die bending stations with automated feeding and cutoff.
Table 2: Overview of Corrugated Profile Roll Former Subsystems
Section | Purpose | Considerations |
---|---|---|
Decoiler mechanism | Feeds rolled coil stock | Tension control for optimal straightening |
Guiding rollers | Stage material into first forming rollers | Lubrication to minimize scratching |
Forming stations | Gradually shape wave profile through bending sequences | More complex shapes need additional stands |
Hydraulic system | Provide accurate roller closure pressures | Prevent ripping while fully contouring |
Cutoff shear | Chop corrugated sheet at fixed durations | Minimize burrs influencing bonding |
Control panel | Monitor line adjustments | Centralized parameter and diagnostics access |
Innovations around CNC-controlled roller adjustment mechanisms, servo motor powered decoilers able to rapidly switch materials, plus quick connect forming stand changes provide avenues for custom short-run solutions beyond traditional manually configured machinery focused on high volume runs alone.
Types of Corrugated Profile Roll Forming Machines
While all corrugated roll form lines share fundamental feedstock shaping principles, categories emerge based on part intricacy needs, length variations, production speed goals and operator skill levels influencing desired automation.
Table 3: Common Types of Corrugated Roll Formers
Machine Class | Description | Typical Uses |
---|---|---|
Manual lines | Fixed speed mechanical actuators | Small job shops doing custom short runs |
Servo motor control | Programmable roller positions | Mid volume roofing for distribution centers |
Fully automatic | Touchscreen recipe selection | High speed lines for major big box retail and industrial projects |
Single layer | Basic machine method | Starter option gradually upgrading over time |
Double layer | Sandwiching insulative cores | Refrigeration, cleanrooms or conditioned spaces |
Additional options like inline notching or hole punching systems avoid secondary production steps for finished panels immediately installable pulled right off the exit tables.
Technical Specifications
Configuring corrugated roll form layouts balancing tolerances, feature intricacy, line speeds and material flexibility requires appropriately weighing key performance attributes per application requirements.
Table 4: Key Corrugated Iron Roll Former Specifications
Parameter | Typical Range | Key Factors |
---|---|---|
Forming speed | 6-25 meters per minute | Throughput targets, operator pace |
Forming thickness | 0.4mm to 2mm | Strength needs, available coil stock |
Forming width | 1000mm – 2500mm | Standard building material dimensions |
Corrugation type | Sinusoidal, trapezoid, custom | Visual preferences, structural loading |
Quick changeover | Manual to fully automatic | Short run customization requirements |
Line automation | Mechanical actuators to sophisticated servo/PLC control | Operator skill level, changeover speeds |
Getting appropriate power transmission ratios between the powered forming rollers and decoiler mechanisms ensures smooth interlocks with consistent feeding into the dies without tearing or jamming.
Establishing rated production speeds, thickness capabilities and dimensional plan constraints upfront appropriately sizes lines balancing project scalability against quality.
-
বৈদ্যুতিক মন্ত্রিসভা ফ্রেম রোল গঠনের মেশিন
-
দিন রেল রোল ফর্মিং মেশিন
-
তারের মই রোল ফর্মিং মেশিন
-
পিভি মাউন্টিং বন্ধনী সি শেপ প্রোফাইল রোল ফর্মিং মেশিন
-
তারের ট্রে রোল ফর্মিং মেশিন
-
পিভি মাউন্টিং ব্র্যাকেট রোল ফর্মিং মেশিন (HAT / ওমেগা প্রোফাইল)
-
পিভি মাউন্টিং বন্ধনী জেড শেপ প্রোফাইল রোল ফর্মিং মেশিন
-
সোলার মাউন্টিং স্ট্রট চ্যানেল রোল তৈরির মেশিন
-
স্ট্রুট চ্যানেল রোল ফর্মিং মেশিন
China Corrugated Roll Forming Manufacturers
Top Chinese metalworking machinery builders provide cost competitive corrugated roll form lines catering small to large part size requirements – featuring configurable modular ancillary gear to fulfill secondary fabrication steps required for finished panels.
Table 5: Leading China Corrugated Profile Roll Forming Manufacturers
প্রতিষ্ঠান | Maximum Width | Line Offerings |
---|---|---|
Fangda | 2500mm | High end lines featuring European components |
Jinpu | 2200mm | Affordable systems balance automation against flexibility |
Formtek | 2000mm | Premier corrugated lines featuring climate control systems to stabilize precision |
Gasparini | 1500mm | Entry level corrugation lines on tight budgets |
Bluesky | 1300mm | Containerized mobility options taking production onsite |
These innovative metalworking machinery producers offer versatile solutions spanning manual through fully automated galvanized roll formed panels for straightforward to sophisticated waveform contours – complete with customizable hole punching, slotting and notching to suit unique building material requirements.
And thanks to extensive sheet metal fabrication expertise nurtured catering goods exporting partnerships plus economist equipment costs from substantial local skilled labor pools, 30-50% savings gets realized over comparable European or American built machinery with equivalent corrugated production capacities and features.
corrugated iron sheet roll forming machine Cost Analysis
Delivering compelling value propositions with baseline machinery pricing lower by 25-50% over costlier western lines, China built corrugated roll formers enable attractive 2-4 year ROI timeframes for most purchasing organizations after factoring regional labor expenses and expected utility usage.
Table 6: China Corrugated Profile Roll Former Line Price Considerations
Type | Price Range | Key Applications |
---|---|---|
Manual and mechanical control | $18,000 – $55,000 | Small scale builds, limited quick adjustment needs |
Servo electric actuation | $35,000 – $120,000 | Medium output scenarios balancing automation against quick changeovers |
Fully automatic high speed lines | $55,000 – $250,000 | High volume projects for large warehouses, retail Buildings |
Ancillary cross-cut saws, punching & counting systems | $3,000+ per station | Reduces secondary processing steps |
Requiring substantially less upfront capital investment commitments than comparative European equipment allows small construction firms or regional material distributors easier entry into self-managed building envelope supply alternatives – or frees up cash flow for additional competitive differentiation investments like customized logistics delivery or locally branded custom color availability.
Smooth Production Practices
Appropriate installation paired with preventative monitoring facilitates rated corrugated iron sheet output over decades of extended China roll former equipment service life.
Table 7: Recommended Corrugated Panel Line Practices
Activity | বিস্তারিত |
---|---|
Dimensional validation | Confirm alignments match technical drawings |
Control calibration | Test maximum speeds don’t trigger faults |
Parameter refinement | Balance ram pressures against tearing/creasing risks |
Operator training | Ensure safety knowledge plus troubleshooting preparedness |
Maintenance | Follow daily, monthly rigging/chain regreasing guidance |
Upgrades budgeting | Plan ancillary future punching/counting stations as needed |
In particular, lubrication quality, tensioning consistency, plus monitoring key subassembly condition factors like:
- Structural rigging integrity without developing sway during operation
- Decoiler rollers surface wear resisting damage scratching finished coil stock
- Shear blade gaps maintained preventing undesired burring
Proves vital for uninterrupted high speed production paired with dimensional tolerance conformance across mass order cladding projects.
Prioritizing preventative care maximizes equipment return on investment measured in functional lifespan – consistently achieving rated throughput year over year.
Ideal Partner Selection Principles
Discerning reputable corrugated roll former machinery builders against prudent benchmarks offers clarity ensuring chosen collaborators provide robust solutions meeting current expectations while offering future production scaling capabilities matching long term manufacturing objectives.
Table 8: China Partner Selection Criteria for Corrugated Lines
Evaluation Aspect | Specifics | Rationale |
---|---|---|
Portfolio suitability | Sufficient options across manual and high automation lines? | Matches short and long run scenarios |
Engineered quality | Robust welding and machining fabrication expertise? | Maximizes fatigue life for 24×7 high speed capacity |
Established reputation | Years serving roofing or building sectors? Safety focus? | Reduces potential business continuity risks |
Support capabilities | Installation guidance? Inspection recommendations? Virtual troubleshooting tools? | Accelerates technicians productivity minimizing downtimes |
Site references | Client sample material runs? Similar line inspections? | Confirms specifications and longevity claims |
Requesting production facility tours while vetting after sales support Southeast Asia accessibility demonstrates responsive commitments better catering subsequent upgrading budgeting or regional expertise augmentation needs as in-market order demand patterns evolve.
Entering relationships with trust in capabilities paves mutually prosperous collaborations during unforeseen circumstances – maximizing speed to resolution.
Buying Considerations for China Lines
While considerable advantages exist around economical China corrugated sheet line pricing and customization freedom, logistical complexities introduce pre-purchase considerations requiring deliberation.
Table 9: Pros vs Cons of China Corrugated Profile Roll Form Machines
Advantages | Considerations to Overcome |
---|---|
Very cost competitive equipment pricing | Extended 3-6 month lead times |
Custom engineering matching unique requirements | Communication barriers mandate persistence |
Short run and rapid profile changeover capable | Internal engineering expertise needed specifying details |
Automated lines for high speed mass production up to 25 meters per minute | Challenging to facilitate urgent short term order requests |
Ancillary punching and cross-cutting fabrication flexibility | Complicated shipping/customs logistics mandates oversight |
While significant capex motivated incentives exist accessing extensive Chinese metalworking equipment expertise at substantial discounts, buyers must temper value-based emotional appeal against pragmatic project execution realities requiring planning and qualified partners.
However with upfront technical diligence conveying clear specifications, plus delegating shipping/tax logistics to experienced import agents, procurement risks get mitigated – paving opportunities localizing previously challenging fabrication steps bringing greater competitive differentiation.
Careful scoping of long term scaling roadmaps combined with initial small batch pilot testing improves visibility around measurable efficiencies when substituting dated western legacy equipment.
Future Global Metal Building Material Demand Outlook
Strengthening GDP forecasts across developing East Asian and African territories paired with favorable demographic shifts towards urbanization promises lucrative outlooks for continued corrugated sheet demand supporting both residential plus commercial infrastructure projects over the next decade.
Table 10: Global Metal Panel Market Expansion Projections Through 2026
Region | Forecasted Market Size | Construction Sector Trends |
---|---|---|
East Asia | $650 billion | Rapid developing economy infrastructure investments |
South Asia | $500 billion | Expanding middle class and manufacturing plants |
Southeast Asia | $400 billion | Transitioning low cost manufacturing and improving tourism |
Middle East & Africa | $375 billion | Young demographics, increasing consumer buying power |
With robust tailwinds from government backed infrastructure commitments through most territories combined with resilient global ecommerce trends even despite periodic broader cyclical economic fluctuations promises sustainable demand for pre-engineered modular cladding systems using stamped, rolled or corrugated sheet alternatives.
This durable demand outlook points towards strong continued machinery investment activity migrating aging western equipment towards revolutionary latest automated Chinese metal fabrication production lines offering radical per panel cost savings and quality consistencies at previously unimaginable throughputs.
Careful scoping of initial pilot projects improves financial visibility and confidence around projected 3-5 year scaling roadmaps empowering prudent capital investment decisions.
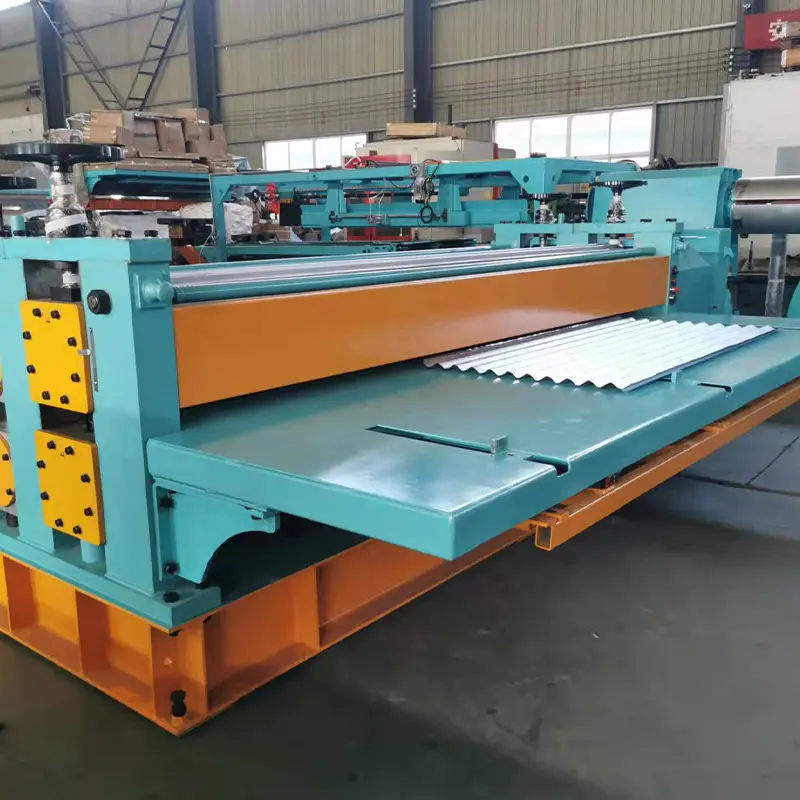
FAQ
Q: What risks around corrugated roll form lines need addressing?
A: Rotational draw rollers, exposed electrical busbars and hydraulic clamp motions pose safety risks needing emergency stop integration plus maintenance procedures.
Q: What metal thickness range typically accommodates cost effectively?
A: 0.4 – 1.0mm finished metal thicknesses balances load capacity against pricing affordability for general low rise applications. Architectural projects allow heavier gauge usage.
Q: What ancillary line equipment provides additional benefits?
A: Common complementary equipment includes punching, dimpling protrusions, corner folding stations and layering lines helping reduce secondary production steps for finished panels.
Q: What real-world equipment lifecycle timeframes justify budgeting?
A: With adequate preventative maintenance including scheduled wear item replacement like roller dies and shear blades – 20-25 year machine usefulness assumptions are reasonable before performance upgrades become necessary.
Q: When should in-house lines get considered over outsourcing?
A: Below ~15,000 sq. meter monthly demand, outsourcing proves typically recommended avoiding overhead costs. Above that threshold, ownership gains increasing quality control and aesthetic differentiation appeal while better reacting against fluctuating market demand.