ভূমিকা
Roll forming is a metal forming process used to produce long sheet metal sections with constant cross-sections. It is an efficient and cost-effective method of producing parts with consistent accuracy and quality. The introduction of computer numerical control (CNC) technology has further enhanced the capabilities and versatility of roll forming machines.
CNC roll forming machines are now widely used across various industries to manufacture metal components for diverse applications. This article takes a detailed look at CNC roll forming and its widespread use across manufacturing sectors.
What is CNC Roll Forming?
Roll forming is a continuous bending process in which sheet or strip metal is gradually formed into a desired cross-sectional profile through a series of consecutive roller stations. As the material passes through each roller station, it is incrementally shaped into the desired form.
CNC roll forming incorporates computer numerical control technology to automate the roll forming process. CNC systems control all aspects of the roll forming machine, including roller position, metal feed rate, and other parameters. Operators simply program the desired specifications into the CNC controller and the machine automatically adjusts the roller stations to shape the material accordingly.
Some key benefits of CNC roll forming:
- Highly accurate and consistent output. CNC automation ensures every part meets specifications.
- Flexible and easy changeovers between different cross-sections. Operators just load a new program.
- Higher throughput and productivity compared to manual roll forming.
- Minimal operator supervision required after initial setup.
- Capable of complex profiles that would be difficult with manual roll forming.
CNC enables roll forming machines to deliver precision and efficiency beyond the capabilities of manual operations. This has led to the widespread adoption of CNC roll forming technology across many industries.
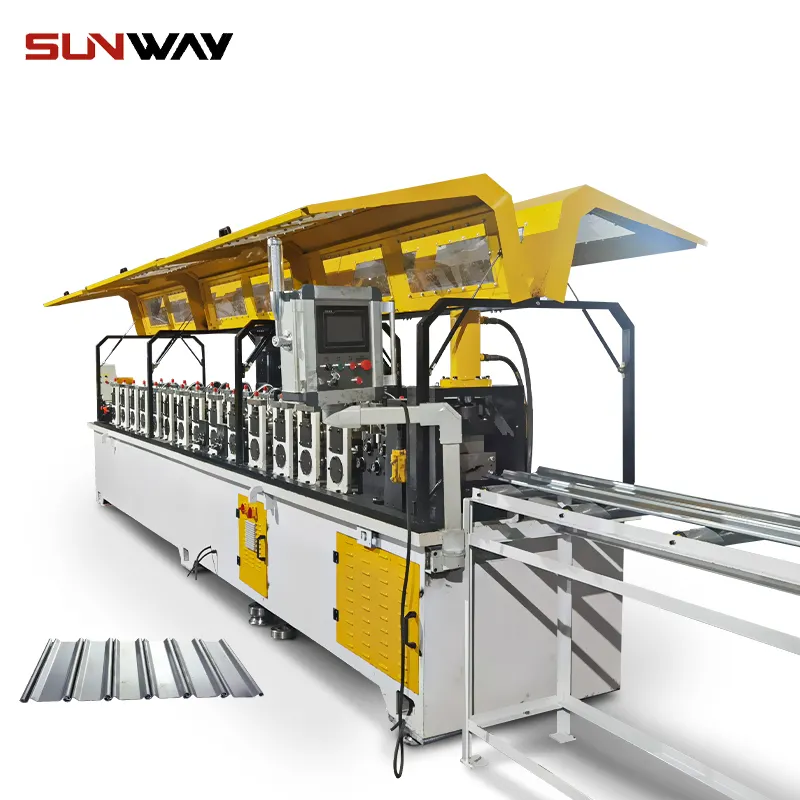
Major Application Areas of CNC Roll Forming
CNC roll forming machines have become ubiquitous in manufacturing sectors where long sheet metal components are required. Some of the most common applications include:
Building and Construction
CNC roll forming is widely used to produce metal studs, joists, purlins, wall panels, roofing, decking, and various architectural claddings. Construction applications require long, lightweight sections that can be mass-produced efficiently.
- Metal studs – Load-bearing interior wall framing members. CNC lines can produce galvanized steel studs in different thicknesses and lengths.
- Roofing and siding – Roll formed metal panels for roofs, exterior walls, and façades. CNC lines produce long sheets with specialized ribbing for strength and interlocking.
- Solar mounting structures – Formed metal parts for solar panel frames and sun tracking systems. Complex CNC profiles required for structural stability.
Transportation
Automotive, truck, trailer, and railcar manufacturers utilize roll formed sections for vehicle frames, interiors, and exterior body panels. CNC roll forming allows high-volume production with precision.
- Chassis frames – Roll formed side rails and cross members used in truck and trailer bodies. CNC enables complex bends.
- Automotive panels – Exterior body panels are roll formed into smooth, aerodynamic shapes.
- Interiors – Interior door frames, seat frames, and roof arches are roll formed for cars and trains.
Appliances
Home appliances often contain roll formed metal enclosures, frames, and structural components. The housings of refrigerators, washers, dryers, air conditioners, and many other appliances are produced on CNC roll lines.
- Washing machine drums – Formed end caps and tub frames maintain roundness.
- Refrigerator liners – Interior stainless steel liners shaped to exact dimensions.
- Air conditioner chassis – Structural side frames and bottom panels.
Infrastructure
From light poles to guardrails, infrastructure projects utilize a range of roll formed sections. CNC automation allows mass production of consistent street furniture components.
- Light poles – Tapered pole shafts and arms are formed from sheet steel.
- Traffic barriers – Guardrails and highway barriers made of roll formed steel.
- Utility poles – Transmission line poles and cell tower shafts require angled profiles.
Furniture
Many modern furniture designs incorporate metal frames and structural elements that are ideal for roll forming. CNC allows both long production runs and custom short runs.
- Desks – CNC lines produce sturdy steel desk legs and structural beams.
- Chairs – Formed seat and back support frames for metal chairs.
- Shelving – Upright support posts and horizontal shelves.
Key Components of CNC Roll Forming Lines
A CNC roll forming system contains a number of key components that work together to shape sheet metal stock into the desired forms. Here are some of the main elements:
Feed Mechanism
The feed mechanism provides consistent feeding of sheet or coil stock into the roll forming section. This typically consists of powered pinch roller feeds or servo-motor driven feeds. The CNC control coordinates the feed rate to match the forming speed.
Forming Section
The forming section consists of a series of roller stations that progressively bend and shape the strip stock. Advanced CNC roll forming lines have servo-driven roller stations that can be digitally positioned for precision forming and rapid changeovers.
CNC Controller
The CNC controller executes the roll forming program and coordinates all machine motions and functions. Operators simply call up programs for different parts or profiles. The CNC ensures repeatable and accurate execution.
Cutoff Station
A final cutoff press or shear cuts the finished roll formed parts to the desired lengths as they exit the machine. The cutoff operation can also be integrated into the CNC control programming.
Outfeed Equipment
Outfeed tables, conveyors, stacking systems, or robotic arms manage and collect finished parts as they are produced. This automation can be integrated with the overall CNC control system.
Safety Enclosure
Full perimeter guarding and safety fencing ensures operator protection. Advanced systems have interlocks preventing the machine from operating without guards in place.
By combining all these elements under integrated CNC control, modern roll forming lines achieve rapid changeover, high productivity, and precision output during unattended production.
Advantages of CNC Roll Forming Technology
CNC roll forming machines deliver significant benefits that explain their widespread adoption across manufacturing:
Enhanced Precision and Consistency
With CNC control, roll forming machines produce parts within extremely tight tolerances of 0.005 inches (0.127mm) or better. This precision ensures consistency across high production volumes.
Flexible and Efficient Changeovers
Operators can switch to new roll formed profiles in minutes by simply selecting new programs. No hardware changeovers required.
Increased Throughput
CNC automation enables roll forming lines to operate at high production speeds around 100 ft/min (30 m/min) while maintaining synchronous material feed.
Ability to Form Complex Shapes
With servo-controlled roll stations, even intricately shaped sections with multiple bends along multiple axes can be roll formed.
Minimal Material Waste
CNC programming compensates for material springback, resulting in accurate forms with less trial and error and material waste.
Reduced Labor Requirements
Automated CNC roll forming lines require just one or two operators for setup and supervision during production.
Lower Operational Costs
Consistent quality and high output with less labor results in lower overall part costs.
With all these advantages, it’s easy to see why CNC roll forming represents the state of the art in metal forming technology.
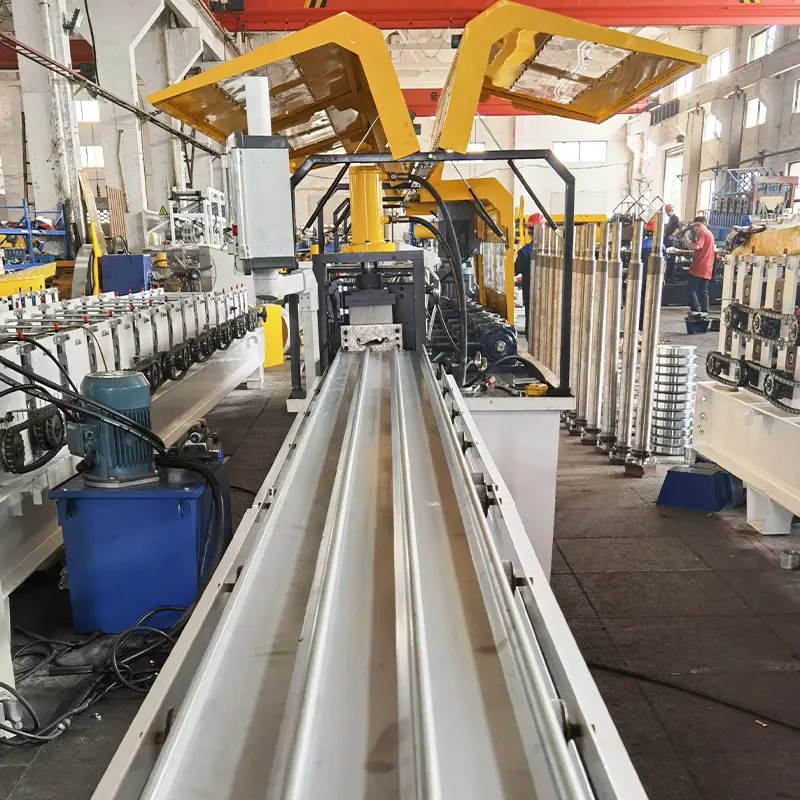
CNC Roll Forming Machine Configurations
CNC roll forming machines are built in different configurations to suit various production needs. Key factors determining machine design include part length, material thickness, and output rates.
Continuous vs Cut-to-Length
Continuous roll forming produces strip stock of indefinite length, wound onto a takeup reel. Cut-to-length lines shear finished parts at predetermined intervals.
Horizontal vs Vertical Orientation
Horizontally fed machines occupy less floor space while vertical machines allow gravity-assisted feeding.
Single vs Multi-Profile
Some lines produce a single profile while tandem and modular machines can quickly switch between different forms.
In-Line vs Standalone
In-line machines are integrated into larger production systems while standalone configurations allow for flexible use.
Heavy-Gauge Capability
Some roll forming lines specialize in heavier gauge metals or stainless steels using more robust components.
With experience and expertise, roll forming machine builders can configure CNC lines optimized for customer requirements. Customized lines ensure optimal productivity.
Programming and Setups
Efficient CNC roll former operation relies on proper programming and setup. Machine builders offer programming services and CAD software options to facilitate the process.
3D Model to Machine Program
Part designs are modeled in 3D CAD and then software converts geometries into machine code for each roller position.
Machine Calibration
Roller stations go through automatic initial calibration routines to align positions to CNC zero points and axes.
Material Properties
Unique material characteristics like modulus of elasticity are input into software to factor in material springback.
Forming Sequence Optimization
The order of bends and forms can be optimized to avoid material defects and stresses.
Simulation and Emulation
Offline programming can simulate machine movements and detect interferences before live runoff.
Tooling Design
Specialized tooling like bend rolls, presses, guides, and gauges may be required for certain profiles.
With the proper preparation, CNC roll forming machines can accurately produce a new profile on the first pass.
Quality Control Systems
To leverage the full potential of CNC roll forming lines, automated quality control systems are often implemented. These include:
Servo Rollforce Monitoring
Force sensors on servo rolls detect fluctuations indicating defects. The CNC control can adjust in real-time or flag bad parts.
Automatic Dimensional Inspection
Laser or optical sensors mounted along the line inspect key dimensions and check for forming errors.
Post-Production Gauge Testing
Sample parts are measured against precision gauges. Automated gauges can be integrated into the production line.
Vision Inspection
Machine vision systems check for surface defects and inconsistencies in the material. Automated sorting systems cull bad parts.
CMM Part Scanning
Sample parts are placed in a CMM scanner for 360-degree dimensional analysis. Data informs process improvements.
Advanced CNC roll forming lines function as fully-automated turnkey systems with integrated quality verification at every stage. This represents the pinnacle of roll forming technology.
Latest Advancements in CNC Roll Forming
As an evolving technology, CNC roll forming systems are continually incorporating the latest innovations and enhancements. Some current developments include:
Servo Electric Actuation
Replacing traditional hydraulic roller positioning with fast and precise servo electric actuation for higher speeds and accuracies.
On-the-Fly Adjustments
Real-time monitoring and automatic roller adjustments on the fly to compensate for material variations and improve consistency.
Advanced Safety Features
Innovations like multi-spectrum 3D vision fully eliminate potential contact points through proactive detection and controlled shutdown.
Connected Remote Access
Monitoring line status and part quality metrics in real-time from anywhere. Making live programming adjustments remotely.
Rapid Changeover Tooling
Quick release tooling systems and fast roller change carts enable profile adjustments in under 10 minutes.
Energy Efficient “Green” Machines
Next-generation lines leverage efficiencies of servo-electric actuation for reduced energy consumption and lower environmental impact.
Customized Smart Factories
Fully-tailored Industry 4.0 production lines integrate data collection, connected sensors, analytics, and machine learning capabilities.
With constant material and technological innovations, CNC roll forming systems will continue pushing boundaries and exploring new applications across manufacturing.
Roll Forming Versus Other Metal Fabrication Methods
While roll forming provides substantial advantages, it is just one of many metal working processes available. Other common fabrication methods include:
Stamping
Stamping utilizes presses and dies to form sheet metal with high tonnages of pressure. Lower volumes due to higher tooling costs.
Hydroforming
Forming metal into complex tubular and enclosed shapes using highly pressurized fluid. Limited profile shapes but ideal for automotive pipes and tubes.
Welding Fabrication
Joining metal pieces together along seams through arc or spot welding. Labor intensive technique.
Brake Forming
Bending sheet metal into forms using mechanical braking press. Slower and more tooling intensive than roll forming.
Casting
Pouring molten metal into molds to create solidified forms. Ideal for high-volume parts with detailed features like engine blocks.
Extrusion
Squeezing metal through a die to create lengths with fixed cross-section. Limited to simplistic profiles.
For producing long lengths of sheet metal into open symmetric cross-sections, roll forming provides distinct advantages over these other processes.
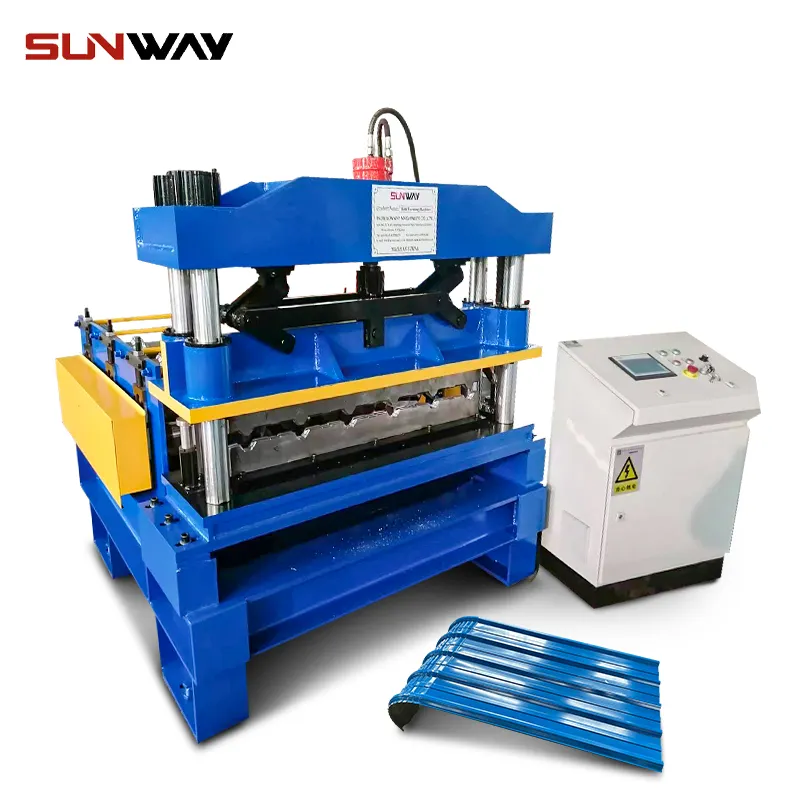
FAQ
What types of metals can be roll formed?
Most ductile metals can be roll formed, including steel, stainless steel, aluminum, copper, and brass. The ability to withstand bending without cracking is the key requirement.
What are common roll formed end product examples?
Gutters, roofing, siding, racks, rails, framing studs, vehicle panels, highway signage, billboards, shelving, enclosures, solar panel frames, and LED light housings are some examples of roll formed end products.
What thicknesses of metals can be roll formed?
Standard roll formers can typically process metal from 26 gauge (0.017”) up to about 14 gauge (0.075”) thickness. Extended ranges up to 1⁄4” thick material are also possible with heavy-gauge roll forming machines.
How are complex roll formed shapes possible?
By shaping material progressively through a series of bending steps in multiple directions rather than all at once, even intricate forms can be produced. The ultimate form is the sum of numerous small incremental bends.
Can a single roll forming machine make different profiles?
Some configurable or modular machines can be equipped with additional tooling sets and CNC programs to enable quick profile changeovers. Standardized designs also allow retrofitting existing lines with new tooling.
What size production runs are optimal for roll forming?
Long production runs over 50,000 linear feet is where the efficiency of CNC roll forming provides the most advantage. However, short prototype and small batch runs are also feasible.
How does roll forming compare to 3D metal printing?
While additive manufacturing can produce highly complex one-off shapes, roll forming is superior for mass production of simple long metal sections in the 1,000+ piece range. The two technologies can complement each other.
উপসংহার
CNC roll forming provides transformative benefits for producing metal parts with long, open cross-sections. With unparalleled efficiencies, flexibility, precision, and cost-effectiveness, CNC roll forming machines have become integral to manufacturing across diverse industries.
Ongoing advancements are unlocking even greater potential for this technology. As engineering innovations continue, CNC roll forming systems will take on more applications and play an expanding role in automated smart factories of the future. The widespread adoption of this technology is a testament to the capabilities it brings to the manufacturing sector.