Roll forming is a metal working process that involves continuously bending a long strip of sheet metal into various cross-sectional profiles. One of the most common roll formed products is steel roofing and wall panels, which provide an efficient and lightweight covering for buildings. IBR (Inverted Box Rib) is a popular type of architectural panel profile that is produced on roll forming machines.
What is an IBR Sheet Roll Forming Machine?
An IBR sheet roll forming machine is a complex piece of equipment specifically designed to form sheet metal into the distinctive IBR panel shape. IBR stands for Inverted Box Rib, which refers to the unique profile of raised and lowered sections running lengthwise along the sheet.
IBR roll forming machines utilize a series of roller dies to progressively shape flat sheet metal stock into the final IBR profile. As the material passes through each roller station, it is gradually bent into the alternating ribs and valleys that characterize the IBR panel. Modern IBR roll formers are fully automated and some are capable of speeds exceeding 130 feet per minute.
Key Components of an IBR Sheet Roll Former
An IBR sheet roll forming machine consists of several key components engineered to work together to form the IBR panel profile:
- Uncoiler: This device holds a large coil of flat sheet metal and feeds it into the first roller station to start the forming process. The uncoiler must provide stable and consistent tension on the material.
- Roller dies: These steel rollers have machined contours that progressively bend the sheet to the IBR shape as it passes from station to station. The roller dies come in top and bottom pairs that are precision-grounded to account for metal thickness and material springback.
- Forming stations: Most IBR roll formers have between 12 and 16 forming stations, each with a set of top and bottom roller dies. The rolling force applied at each station incrementally forms the IBR panel. Stations early in the process make longer, gradual bends while later stations finalize the profile shape.
- Drive system: This powers the rotation of the forming rollers and precisely coordinates the speed and position of each station. Servo motors with programmable controls are commonly used for the drive system.
- Support rollers: Additional rollers that don’t actively form the metal but provide support and stability between forming stations.
- Shear station: Once the full IBR profile is formed, a flying shear cuts the panels to length based on operator input. A precise cut helps avoid snagging during panel installation.
- Controller: Sophisticated automation allows the operator to set up recipes and running parameters. The controller coordinates all machine movements and provides feedback on production.
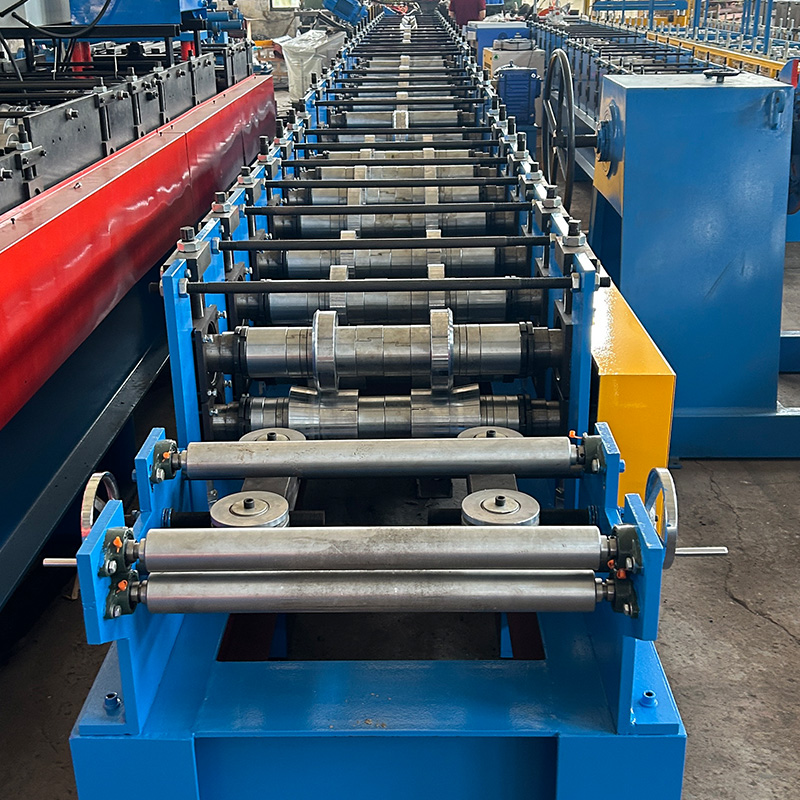
IBR Roll Former Capacity and Speeds
IBR sheet roll formers are available in a range of capacities suited for different production environments:
- Light-duty: These compact IBR machines are designed for low-volume job shops or intermittent IBR production runs. They typically handle material thicknesses from 0.4mm to 1.5mm and have maximum speeds around 40 feet per minute.
- Mid-duty: Offering more power and faster production speeds, mid-duty IBR roll former max out around 90 to 100 FPM. They can readily handle sheet thicknesses from 0.7mm to 2.0mm.
- High-capacity: Built for high-volume roofing manufacturers, these heavy-duty IBR forming machines can achieve speeds over 130 FPM. They are capable of running material up to 3.0mm thick.
In additional to thicker material capabilities, high-production IBR roll formers offer faster acceleration, quicker die change-overs, and features like automatic coil reloading to minimize downtime.
Key Benefits of Using an IBR Sheet Roll Former
Some of the main advantages of using a dedicated IBR sheet roll forming machine include:
- Highly efficient profile forming – The precision machining and proper sequencing of the roller dies ensure continual and smooth shaping through the entire IBR panel length.
- Flexibility – IBR roll formers can typically accommodate a range of material thicknesses and widths. Operators can quickly set up different IBR configurations.
- Consistent output – Automated IBR roll formers produce each panel to the same exacting tolerances without deformations across long production runs.
- Rapid production – Modern high-capacity IBR machines can roll form over 130 feet per minute enabling large volume output.
- Superior finish – The roller dies only contact the outer 5% of the strip material, resulting in low friction forming that leaves a pristine IBR panel appearance.
- Low maintenance – Advanced bearing designs minimize wear on roll forming components leading to less machine downtime.
For manufacturers looking to efficiently produce quality IBR roofing panels, a dedicated IBR sheet roll forming machine is an ideal fabrication solution.
Understanding the IBR Panel Profile
The unique shape of the Inverted Box Rib (IBR) panel comes from its distinctive profile featuring raised and lowered sections alternating along the length of the sheet:
- Ribs – The higher angled sections (ribs) provide strength and structural support when installed. The inclined ribs also aid in drainage.
- Valleys – The lower sections (valleys) between the ribs allow panels to interlock when installed side-by-side. The valleys also enhance drainage compared to flat sheet.
- Web – This refers to the near-vertical faces along the sides of each rib. The height and width of the ribs and valleys can be adjusted.
- Radius – A tight inside bend radius is essential for achieving a crisp and uniform IBR profile. The roller dies are precision machined to prevent cracking.
- Flange – Some IBR panels include an extended flat flange section along one or both edges. The flange provides a surface for fastening the panels during installation.
IBR roll formed panels are available in a range of materials including galvanized steel, aluminum, and zinc with quality finishes like Kynar paint coatings. The IBR shape gives architectural metal roofing and siding added advantages of strength, spanning ability, weather-resistance and design aesthetics.
Typical Materials for Roll Forming IBR Panels
While steel is the predominant material used for roll formed IBR panels, manufacturers may also work with aluminum or even copper depending on the performance and appearance requirements:
Galvanized Steel
- Most common material choice due to good forming properties, durability, and cost.
- Sheet thicknesses between 0.4mm to 0.8mm are typical for roofing.
- Galvanized coating protects against corrosion and provides a reflective appearance.
Pre-painted Steel
- Roll formed after paint coating is applied for uniform coverage and consistent appearance.
- Kynar 500 PVDF resin-based paint systems provide excellent exterior durability.
- Wide range of colors available for architectural metal products.
Aluminum
- Aluminum IBR panels are lighter weight but also stronger than steel.
- More expensive material cost but provides corrosion resistance without coatings.
- Well-suited for coastal or demanding environments.
Copper
- Prized for its natural patina, distinctive look, and exceptional longevity.
- Difficult to form into IBR profiles and requires very gradual forming stages.
- Mostly used for high-end architectural accents due to premium cost.
When choosing an IBR sheet roll former, make sure the machine’s material thickness capacity, widths, and coil weights match your intended metal materials.
Comparing Inline vs. Standalone IBR Roll Formers
IBR sheet roll forming equipment is available in both inline and standalone configurations:
- Inline – The IBR roll former is integrated directly into a continuous process line after a sheet coil slitter or leveler. This allows immediate sequential forming after initial coil processing.
- Standalone – These are self-contained IBR roll formers that act as an isolated production step. Coils must be moved manually or using coil cars between equipment.
Here are some factors when deciding between inline vs. standalone IBR roll formers:
- Production flow – Inline supports high-volume automated processes while standalone allows more flexibility.
- Line balancing – Inline roll forming speed must match the slowest upstream process rate.
- Floor space – Standalone units take up more linear space on the production floor.
- Installation – Inline roll formers require foundations and integration into existing lines.
- Upgrades – Standalone machines can more easily be replaced or added to over time.
Carefully considering current and future needs will determine which roll former configuration best fits your IBR panel production environment.
Key Options for Customizing IBR Roll Formers
While all IBR sheet roll formers produce the same essential Inverted Box Rib panel profile, there are numerous options available for customizing and optimizing the equipment:
- Coil capacity – Larger uncoilers allow loading more coil weight and minimizing changeovers.
- Forming speeds – Match machine speed to your real production needs for efficiency.
- Quick die change – Minimize downtime by rapidly switching profiles with quick-change cassette roller stations.
- Auto oiler – Centralized oil lubrication with remote fill points simplifies maintenance.
- Material edge restraints – Guide rolls prevent buckling on thin or narrow stock.
- Safety guarding – Full-length shields safeguard operators from pinch points and moving components.
- Sound enclosure – For quieter operation and improved working conditions.
- Decoilers – Automatically recoil formed panels for easy bundling and staging.
- Embossing – Add unique embossed textures by modifying specific roller dies.
Review all available options with your IBR roll former manufacturer to maximize functionality for your specific production environment and business goals.
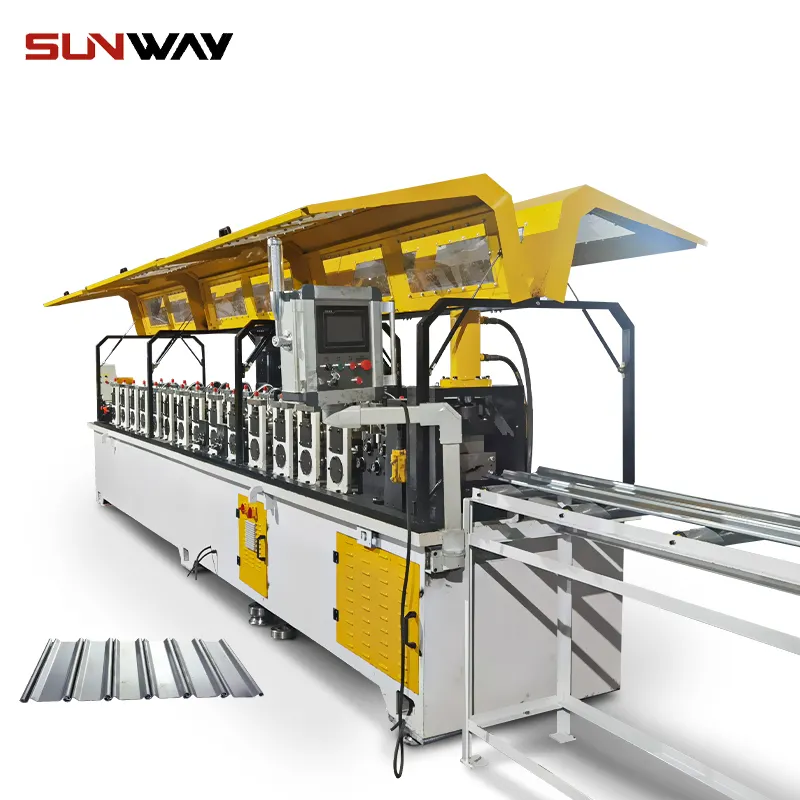
Understanding IBR Roll Former Safety
Working safely around an IBR sheet roll forming machine requires awareness and caution. These large and powerful machines have numerous potential hazards:
- Pinch points – Take care around roller dies and moving coil stock entering and exiting the process.
- Cuts and abrasions – Wear proper gloves when handling formed panels with sharp edges.
- Moving parts – Tie back loose hair and clothing before operating or walking near the equipment.
- Noise – Use hearing protection as prolonged noise exposure can lead to hearing loss.
- Falls – Maintain solid footing when climbing on the machine for maintenance activities.
- Crushing – Coil stock and roll formed panels placed improperly can tip and fall. Use appropriate racks.
- Lifting – Use proper lifting techniques and get help when moving heavy coils.
- Lockout – De-energize all power to the machine during service or adjustments to avoid accidental startup.
- প্রশিক্ষণ – Only qualified personnel should operate the IBR roll former after receiving thorough instruction.
Remaining alert and following safety protocols around the machine at all times ensures maximum personnel protection.
Maintaining Peak IBR Roll Former Performance
To keep an IBR sheet roll forming machine running at optimal efficiency, operators should perform regular maintenance activities:
- Daily cleanup – Remove any metal shavings or debris especially around roller dies and the drive train.
- Lubrication – Apply oil to all lubrication points according to manufacturer specifications to reduce friction.
- Inspections – Check for any leaking hydraulics, loose fasteners, or unusual noises and repair immediately.
- Roller condition – Verify rollers are clean and replace any that are excessively worn or damaged.
- Bearings and seals – Monitor bearings for adequate rotation and lubrication. Replace worn seals promptly.
- Drive system – Confirm proper chain or belt condition and tension. Inspect electrical cabinets for dust buildup.
- Level – Periodically validate machine leveling to avoid twisting or skewing of the IBR panel.
- Testing – Run sample material routinely to confirm forming quality has not changed over time.
With proper operation and preventative maintenance, IBR roll formers provide years of reliable service and quality IBR panel production.
Leading Manufacturers of IBR Sheet Roll Forming Equipment
Several machinery companies have extensive expertise when it comes to producing high-performance IBR sheet roll formers:
- স্যামকো মেশিনারি – Offers the R1000 IBR forming system with quick changeover and PLC control. Over 50 years of roll forming experience.
- Bradbury Group – The VersaRoll and VeryCorr lines are configurable for IBR profiles. High production speeds up to 180 FPM.
- Shanghai Metal Corporation – Comprehensive range of light, medium, and heavy duty IBR roll forming equipment. CE certified.
- Joubert Productions – South African company focused on robust IBR machines up to 3mm capacity and 200 ton capacity uncoilers.
- Metform – Custom IBR roll former design and manufacturing. Machines can incorporate embossing, punching, corner crimping, and more.
When investing in an IBR sheet roll former, be sure to evaluate machine capabilities, experience, service, and overall value from reputable leading manufacturers.
IBR Roll Formed Panel Installation Tips
Once roll formed on an IBR sheet forming machine, the panels must be properly installed on the roof or building walls to achieve lasting performance:
- Overlap panels by one rib spacing to prevent leakage at the side lap joints. Use lap fasteners (screws) with gaskets to ensure a tight seal.
- Allow 1/8″ gap between panel ends for thermal expansion. End laps require butyl sealant inside the overlap for water tightness.
- Fasten the panels at the top of every rib using long-life fasteners appropriate for the supporting structure. Do not over tighten.
- On steep pitched roofs, use cleats to help keep panels aligned. Cleats distribute the panel weight across multiple ribs.
- When cutting panels, use nibblers, shears or circular saws to avoid deforming the IBR profile edges. Make straight cuts.
- Use proper lifting equipment and technique when raising panels onto roofs. Avoid dragging panels across other finished surfaces.
- For end walls, trim excess panel length and add hemmed flashing secured into the wall to close off exposed rib cavities.
Correct handling and installation of IBR panels made on precision roll forming machines results in many years of lasting performance for roofs and buildings.
IBR Roll Formed Panel Maintenance Tips
Like any building envelope surface, IBR panels benefit from periodic inspection and maintenance:
- Remove any accumulated dirt or debris on panels to prevent moisture traps and staining. Use soft bristle brushes and low pressure rinse.
- Check lap sealants and replace any that are cracked or deteriorated. Re-tighten any loose fasteners.
- Inspect for signs of damage including dents, scrapes, cracks, or perforations and repair immediately to prevent leaks.
- For repainting, use a compatible metal primer and paint formulated for exterior use. Follow preparation and application instructions.
- Galvanized finishes can be touched up with cold galvanizing compound to prevent corrosion at cut edges or scratches.
- Clear gutters and downspouts regularly to prevent overflow drainage across IBR panels leading to leaks.
- Ensure ventilation and condensation control systems are operating properly to avoid moisture buildup inside buildings.
Taking time to properly maintain roll formed IBR panels ensures the roofing or siding retains its intended performance and aesthetic qualities.
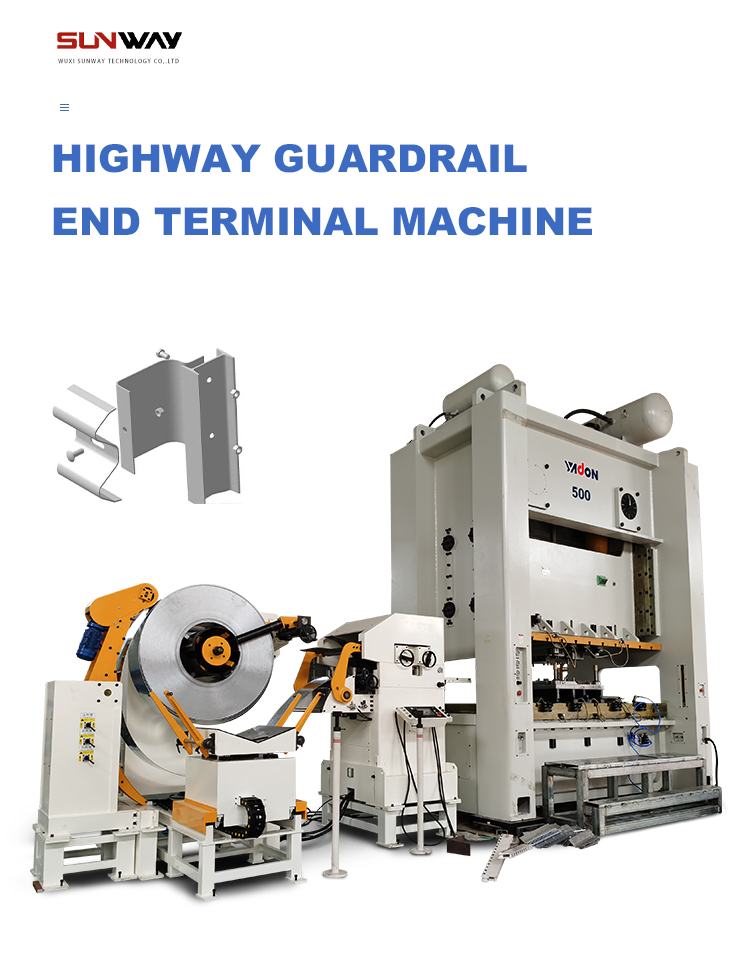
Common Problems and Troubleshooting for IBR Roll Forming
Operators may encounter occasional issues when running IBR panels on a roll former. Here are some common problems and troubleshooting tips:
Inconsistent profiling – Rollers may be dirty or worn. Check and replace any out of spec rollers. Verify correct roller sequencing.
Panels jamming – Increase roller box separation slightly or reduce forming pressure. Check material alignment entering the rolls.
Twisted panels – Insert edge guides to prevent material wandering. Confirm level machine bed.Check for racked roll tooling.
Flared end ribs – Increase material hold down pressure before shear to prevent lifting. Check for worn shear blades.
Profile distortion – Forming speed may be too fast for material thickness. Reduce speed and allow more gradual forming.
Excessive tooling wear – Use recommended lubricants on roller dies. Increase lubrication frequency. Replace worn bearings/seals promptly.
With attention and experience, most IBR roll forming problems can be rapidly diagnosed and corrected to restore optimal machine performance.
FAQ
- What sizes of IBR panels can be formed on the machines?
- IBR roll formers can produce panel widths ranging from 2 feet up to 5 feet or more. Lengths depend on factory space but commonly range from 10 to 50 feet. Maximum coil width limits the panel width.
- Can you change the IBR profile rib height or shape?
- Yes, by changing out some or all of the roller dies, the rib height and shape can be modified along with the width of the flats between ribs.
- What safety equipment should be used with an IBR roll former?
- At minimum, workers near the machine should use proper gloves, steel-toe boots, hearing protection, and safety glasses. Fully enclosed models allow safe operation.
- How long does it take to completely form each IBR panel?
- The total forming time depends on the length of IBR panel being produced but is typically just a few seconds for most machines running at full speed.
- Can other profiles besides IBR be produced on the machines?
- In some cases alternate profiles are possible but may require significant roller die change outs. Most machines are designed specifically around IBR.
- What maintenance is required on IBR roll forming machines?
- Daily cleanup, regular lubrication, inspection of wear items, and keeping mechanisms properly adjusted per the manual. Good preventative maintenance prevents issues.