ماكينات تشكيل ألواح الأسقف هي معدات أساسية لتصنيع ألواح الأسقف المعدنية ومكونات المباني الأخرى. يفحص هذا الدليل الشامل كبرى الشركات المصنعة لماكينات تشكيل ألواح الأسقف، وأنواع الماكينات، والمواصفات الرئيسية، واعتبارات التصميم، ويقدم نصائح لاختيار المورد المناسب.
نظرة عامة على معدات تشكيل ألواح السقف
التشكيل بالدلفنة عبارة عن عملية ثني مستمرة تقوم بتشكيل ركيزة اللفائف المعدنية إلى مقاطع جانبية مخصصة. تقوم ماكينات تشكيل ألواح الأسقف بالدلفنة بتحويل الصفائح المعدنية المسطحة إلى مقاطع تسقيف مختلفة مثل الدرزات القائمة، والمموجة، وألواح التزيين وما إلى ذلك.
فيما يلي الأشياء الأساسية التي يجب معرفتها عن هذه الآلات:
- إنتاج أطوال طويلة من الألواح تصل إلى 300 قدم بدون توقف من الفولاذ الملفوف والألومنيوم وغيرها.
- تعمل محطات التشكيل المزودة بقوالب أسطوانية على تشكيل الشريط تدريجيًا إلى أضلاع ودرزات الألواح
- تسمح أدوات التحكم المحوسبة بالتبديل السريع للقوالب لمختلف التشكيلات
- تقديم أحجام إنتاج عالية تصل إلى 16,000 قدم مربع/ساعة للأسقف والجوانب
- تتراوح من الوحدات المحمولة إلى خطوط الإنتاج المتكاملة بطول 100 قدم
- تتطلب عمليات القطع والتقطيع والتثقيب والتثقيب وعمليات التشطيب الأخرى
توفر ألواح السقف المشكلة بالدرفلة العديد من المزايا مقارنةً بالهياكل المبنية في الموقع:
- أخف وزناً، ونسبة قوة إلى وزن أعلى
- جودة متسقة مع العملية الميكانيكية
- انخفاض نفايات المواد وتكاليف العمالة
- تركيب سريع وتقليل وقت البناء
- مرونة في التصميم - يمكن أن تكون الألواح منحنية أو مدببة وما إلى ذلك.
وهذا يجعل من القوالب الدوارة خيارًا شائعًا للمباني المعدنية الجاهزة والأسقف التجارية والجدران ومرابط السيارات الشمسية والهياكل المعمارية.
تقدم الشركات الرائدة في مجال التصنيع كتالوجات قياسية ومعدات تشكيل اللفائف المخصصة لتطبيقات الأسقف في جميع أنحاء العالم.
الأنواع الرئيسية لـ ماكينات تشكيل ألواح الأسقف
هناك فئتان أساسيتان من القوالب الدوارة المستخدمة في إنتاج ألواح الأسقف:
ماكينات التشكيل بالدلفنة المحمولة
- وحدات مدمجة وقابلة للنقل مع 2-10 محطات تشكيل
- تغذية المواد يدوياً أو بالطاقة حتى طول 10 أقدام
- أحجام الإنتاج حوالي 400-800 قدم مربع/ساعة
- أقل تكلفة حوالي $15,000-$60,000
- مثالية للطلبات الصغيرة، والألواح المخصصة، والتشكيل في الموقع
خطوط التشكيل بالدرفلة عالية الإنتاجية
- خطوط متكاملة مع أكثر من 10 إلى 20 رأس تشكيل
- تلقيم آلي يصل طوله إلى 100 قدم طول الملفات
- سرعات تشكيل تزيد عن 15,000 قدم مربع في الساعة
- تسوية ثلاثية الأبعاد متقدمة وضوابط عملية متقدمة ثلاثية الأبعاد
- نطاق التكلفة $100,000-$500,000
- لإنتاج الألواح ذات الحجم الكبير في المصانع
من حيث التكوين، الأنواع الرئيسية هي:
- إطار على شكل حرف C - محطات تشكيل مثبتة على إطار على شكل حرف C
- I-Beam - محطات متصلة بهيكل ناقل I-beam
- هرمي - محطات مائلة على ترتيب هرمي
- عمودي - المحطات الرأسية للملامح الخاصة
تتوفر أيضاً أنماط أخرى مثل الإطارات الدائرية والعجلات والإطارات المخصصة.
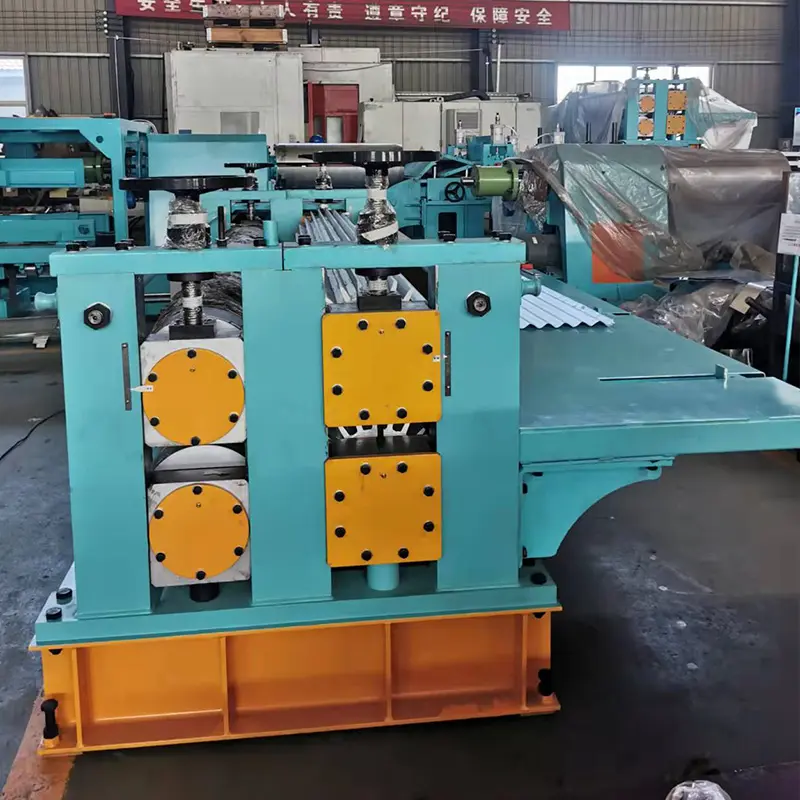
تطبيقات ماكينات تشكيل ألواح الأسقف
تُستخدم ألواح الأسقف المشكلة بالدلفنة في تطبيقات المباني المختلفة:
نظام التسقيف | أنماط اللوحة النموذجية |
---|---|
التماس الواقف | ألواح متشابكة عمودية مع طبقات مرتفعة |
مموج | الألواح الجيبية أو الضلعية المنحنية |
تجعيد 5 فولت | صفيحة مضلعة شبه منحرفة ذات درزات مجعدة |
التزيين | ألواح خشبية مخددة أو ألواح سطح السفينة الماسية |
الألواح الخشبية | نسخ متشابكة من الأسفلت أو الألواح الأسفلتية أو الألواح المعدنية المتشابكة |
لوح مركب | ألواح التسقيف الإردواز الاصطناعية |
من الممكن أيضاً الحصول على تصاميم معمارية وزخرفية للأسقف ذات تصميمات فريدة من نوعها.
يتم تركيب هذه الألواح كأنظمة تسقيف كاملة أو كمناطق تسقيف مميزة. تشمل أنواع الأسقف الرئيسية التي يتم إنشاؤها باستخدام الألواح المشكلة باللفائف ما يلي:
- السقوف المعدنية للمنازل والجراجات والسقائف
- الأسقف التجارية ذات الدرزات القائمة
- إعادة تأهيل الأسقف فوق الهياكل القائمة
- المباني الزراعية ومآوي الماشية
- هياكل تسقيف الألواح الشمسية/مرآب السيارات
- أشكال الأسقف المنحنية أو المتخصصة
تتيح إمكانيات تشكيل ألواح السقف الدوارة للمهندسين المعماريين مرونة واسعة في التصميم لتصميم الأسقف.
مواصفات ماكينات تشكيل ألواح الأسقف
تتميز معدات التشكيل بالدلفنة بتكوينات وخيارات متنوعة. فيما يلي المواصفات الرئيسية التي يجب مراعاتها عند اختيار معدات تشكيل ألواح السقف بالدلفنة:
أبعاد الماكينة | تفاصيل |
---|---|
الطول | 10 أقدام إلى 100 قدم |
الارتفاع | 8 أقدام إلى 12 قدمًا للخطوط الأكبر حجمًا |
العرض | 4 أقدام إلى 10 أقدام حسب التكوين |
الوزن | 4,000 رطل إلى 80,000 رطل |
حجم التشكيل | مقاطع جانبية بعرض 16 بوصة إلى 80 بوصة |
سُمك التشكيل | صفائح من 18 جم إلى 3/16 بوصة (0.04 بوصة إلى 0.19 بوصة) |
سرعة التشكيل | 10 أقدام/دقيقة إلى 130 قدم/دقيقة |
حجم الإنتاج | 400 قدم مربع/ساعة إلى 16,000 قدم مربع/ساعة |
نظام القيادة | هيدروليكي، مؤازر كهربائي، تروس حلزونية |
محطات التدحرج | من 4 إلى 24 رأس تشكيل |
تغذية المواد | الفك اليدوي أو الآلي |
عناصر التحكم | PLC، HMI، محوسبة |
السلامة | مغلق بالكامل مع حراسة |
خيارات خاصة: آلات التفكيك، والتثقيب المسبق، والتثقيب المسبق، والتثقيب، والحزّ، والتهذيب، والعقص، والقطع، والتكديس
العوامل الرئيسية التي تحدد معدل الإنتاج هي سرعة الخط، وعرض المظهر الجانبي، ومقياس المواد.
اعتبارات التصميم لماكينات ألواح السقف
يعد الاختيار والتخطيط السليم للماكينة أمرًا بالغ الأهمية لتصنيع ألواح الأسقف بكفاءة. فيما يلي عوامل التصميم الرئيسية التي يجب مراعاتها:
- الملفات الشخصية المطلوبة - حجم وشكل وخصائص أنماط ألواح السقف المطلوبة
- ركيزة معدنية - الصف، والعرض، والمقياس، وتغليف اللفائف
- حجم الإنتاج - معدل الأقدام في الساعة لمطابقة متطلبات المشروع
- تدفق المنتج - تخطيط للتقطيع والتثقيب والتكديس المضمنة
- سرعة الخط - توازن خطوات العملية للحصول على إنتاجية عالية
- معايير الجودة - الأدوات والأتمتة لتحقيق الاتساق
- وقت التغيير - إمكانية التغيير السريع للقالب من أجل المرونة
- كفاءة الفضاء - بصمة مدمجة لتحسين المنشأة
- الميزانية - قيود التكلفة الإجمالية وأهداف عائد الاستثمار
أ برنامج تصميم التشكيل بالدلفنة أداة مفيدة لتصميم الماكينة والمحاكاة قبل التصنيع.
التخطيط الدقيق للتدفق الكلي للعملية يقلل من مناولة المواد ويحسن تخطيط المصنع.
اختيار الشركة المصنعة لألواح السقف القابلة للطي
يعد اختيار الشركة المصنعة للمعدات الأصلية المؤهلة لتصنيع ماكينات تشكيل الأسقف أمرًا أساسيًا لنجاح خط إنتاج ألواح الأسقف. فيما يلي نصائح لاختيار مورد ماكينات تشكيل ألواح الأسقف:
- السمعة - سجل مثبت من الخبرة والموثوقية
- خبرة - سنوات من الخدمة مع العديد من المنشآت
- النطاق - كتالوج متنوع من الماكينات القياسية والمخصصة
- الجودة - التفاوتات الصارمة والمكونات الدقيقة
- الدعم - فريق الخدمة الفنية المتجاوب
- المعرفة - الخبرة في عمليات تشكيل المعادن
- تمرين - تدريب المشغلين والموارد التعليمية
- انتشار عالمي - المبيعات والدعم عبر المناطق
- البيانات المالية - شركة مستقرة ذات بيانات مالية قوية
- التكلفة - أسعار تنافسية وخيارات القيمة
- المهلة الزمنية - سرعة تنفيذ الطلبات وتوصيلها
الشركات المصنعة ذات السمعة الطيبة مثل ماتي للتقنيات الدقيقة تقدم حلولاً جاهزة بدءاً من التصميم وحتى التركيب وتوفر الدعم المستمر طوال فترة عمل الماكينة.
يضمن الاستثمار في معدات متطورة من شركة منتجة مجربة إنتاج ألواح الأسقف بكفاءة وجودة عالية.
مقارنة الشركات المصنعة لماكينات تشكيل ألواح السقف
هناك العديد من الشركات المصنِّعة لألواح تشكيل الأسقف على مستوى العالم التي تقوم بتوريد معدات ألواح الأسقف. وفيما يلي نظرة عامة تقارن بين كبار الموردين:
شركة | الموقع | موديلات ألواح السقف | نطاق التكلفة |
---|---|---|---|
ماتي للتكنولوجيا الدقيقة | الولايات المتحدة الأمريكية | سلسلة PYRAMID حتى 24 محطة | $100k - $500k |
بيريدج | الولايات المتحدة الأمريكية | سي، زي، زي، هاي ديك | $250k - $750k |
ميتفورم | كندا | I-BEAM 12-20 محطة | $150k - $400k |
ديميكو | هولندا | ج-إطار 10-16 محطة 10-16 | $200k - $600k |
قوة ZZN | الصين | محطات CF Series 4-16 4-16 | $50k - $250k |
عوامل التمايز الرئيسية:
- رفيق توفر تسوية ثلاثية الأبعاد متقدمة وأوسع مجموعة منتجات بما في ذلك القوالب الدوارة المحمولة والمخصصة
- بيريدج يركز على التشكيلات الجانبية للألواح المعمارية ذات التشطيبات المتخصصة
- ميتفورم تتميز بهيكل متين على شكل عوارض I-beam وحلول مخصصة لأمريكا الشمالية
- ديميكو توفر معدات هندسية أوروبية عالية الجودة
- قوة ZZN توريد خطوط صينية منخفضة التكلفة للغاية مع ضمان أقصر
معايير الاختيار:
- النطاق من الماكينات القياسية والمخصصة
- الجودة المكونات، والتفاوتات المسموح بها، والمنتج النهائي
- الدعم الفني للخدمة والصيانة
- التكلفة الاعتبارات - السعر المبدئي والشحن والقيمة مدى الحياة
- سرعة الإنتاج مطلوب لمخرجات لوحة السقف
- الموثوقية ووقت التشغيل من مورد حسن السمعة
عند الاستثمار في المعدات الرأسمالية، فإن تكلفة الشراء الأولية هي مجرد عامل واحد فقط. وتشمل الاعتبارات الإضافية قدرات الماكينة والجودة والإنتاجية وعمر الخدمة وقيمة إعادة البيع. تعمل الشراكة مع شركة مصنعة راسخة مثل Mate Precision Technologies على تحسين الأداء والعائد على الاستثمار على المدى الطويل.
نصائح لشراء معدات تشكيل ألواح الأسقف
فيما يلي بعض النصائح الأساسية لشراء أدوات تشكيل ألواح السقف بفعالية:
- إرسال طلب عرض الأسعار مع مواصفات المنتج المطلوبة وأحجام الإنتاج
- قارن الخيارات من 5-6 موردين مختارين
- مراجعة كتالوج الماكينات القياسية والقدرات المخصصة
- ضع في اعتبارك الأنماط السابقة القابلة للنقل والدائمة على حد سواء
- تقييم سرعة الخط، والعرض، وقدرات سماكة المادة
- افحص هيكل البناء - الإطار C، والعارضة I، والهرم، والتكوينات الرأسية
- طلب محاكاة تشكيل ثنائي الأبعاد/ثلاثي الأبعاد من الموردين
- اطلب رسومات معتمدة قبل بدء الإنتاج
- جدولة اختبار قبول المصنع للماكينات قبل الشحن
- تضمين الإشراف على التركيب والتدريب من خبراء تصنيع المعدات الأصلية
- طلب حزمة قطع غيار لمكونات التآكل الحرجة
- التفاوض على فترة ضمان أطول لزيادة التغطية
- لا تقبل سوى المكونات الكهربائية المعتمدة من CE و UL/CSA فقط
- تأكد من توفر الخدمة والدعم المحليين بعد التثبيت
إن الفحص الدقيق لجودة الماكينة والتحقق من صحة الأداء من خلال عمليات المحاكاة والاختبار يوفر مفاجآت مكلفة في المستقبل. إن الاستثمار في المعدات عالية الدقة والمتينة منذ البداية يقلل من تكاليف الصيانة مدى الحياة ويوفر عائدًا فائقًا على الاستثمار.
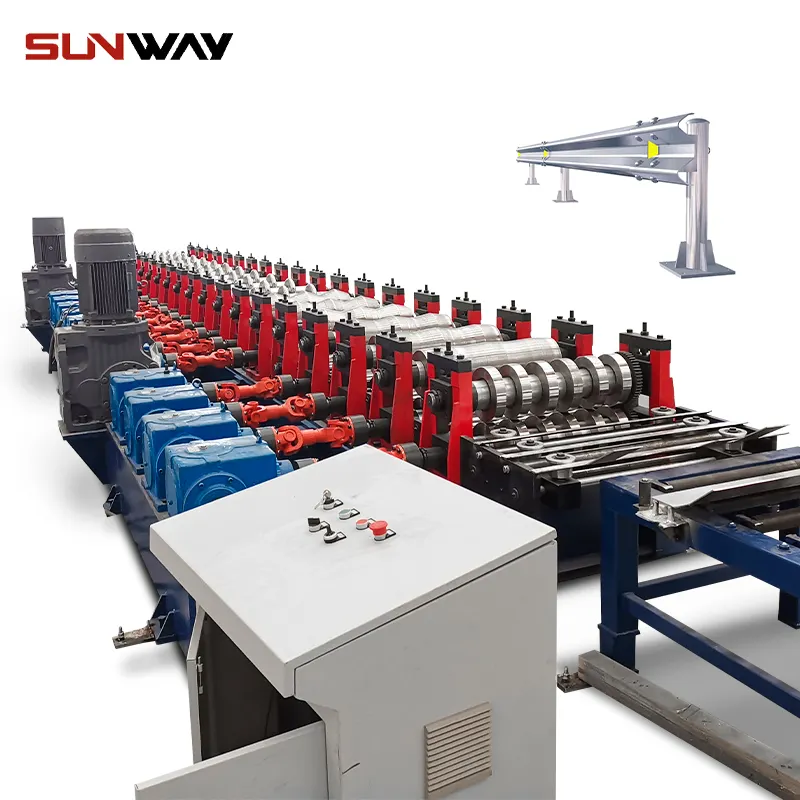
التشغيل والصيانة ماكينات تشكيل ألواح الأسقف
لتحقيق أقصى قدر من الإنتاجية وطول العمر الافتراضي لماكينات تشكيل ألواح السقف:
- إجراء الصيانة الوقائية المجدولة حسب إرشادات الشركة المصنعة للمعدات الأصلية
- التنظيف اليومي الكامل للبكرات ومحطات التشكيل
- تشحيم المحامل والمكونات المتحركة
- افحص سلاسل المحرك والتروس للتحقق من الشد المناسب
- التحقق من مستويات السائل الهيدروليكي والترشيح
- افحص دبابيس رفع الأسطوانة الأسطوانة والشرائح بحثًا عن وجود تآكل
- راقب البكرات والقوالب عن كثب بحثًا عن علامات التلف
- استبدل المكونات البالية أو التالفة بسرعة لمنع الخدش
- قم بتخزين الأدوات الاحتياطية بشكل صحيح لتجنب الشقوق والتآكل
- حافظ على حاويات الإلكترونيات نظيفة ومغلقة بإحكام
- تأكد من سلامة التأريض الكهربائي والأسلاك الكهربائية
- تسجيل ساعات التشغيل ومخرجات المنتج
- الامتثال لجميع إجراءات السلامة أثناء التشغيل والصيانة
- حدد موعداً سنوياً للخدمة المتعمقة من فنيي تصنيع المعدات الأصلية
تشتمل الماكينات المتقدمة على التشخيص والتشخيص التشخيصي والتنبؤات لتحسين الصيانة. يؤدي اتخاذ خطوات لإطالة عمر الماكينة إلى تقليل تكاليف التشغيل الإجمالية.
كيفية اختيار المورد المناسب لماكينة تشكيل ألواح السقف المناسبة
يتضمن اختيار الشريك المثالي لماكينة التشكيل بالدرفلة ما يلي:
- تحديد الشركات المصنعة للمعدات ذات السمعة الطيبة
- البحث قدراتهم وخبراتهم وتجاربهم وخبراتهم
- المقارنة مجموعة المنتجات والجودة والقيمة العمرية
- طلب مراجع من العملاء الحاليين
- التحقق من صحة الكفاءات الفنية والنتائج
- فحص لفة الجودة والبناء السابقة مباشرة
- المراجعة بيانات أداء اختبار القبول في المصنع
- تقييم سهولة الصيانة والتشغيل
- الفحص توافر مخزون قطع الغيار والخدمة المحلية
- التفاوض التسعير، وشروط الضمان، والمهلة الزمنية
- التحقق شهادات CE، وUL/CSA، وISO، وغيرها من الشهادات الأخرى
- مناقشة التدريب والدعم بعد التثبيت
يصبح أفضل الموردين شركاء موثوقين على المدى الطويل يستثمرون في نجاح إنتاجك. إن استثمار الوقت مقدمًا للتحقق من صحة الموردين يوفر عليك المتاعب لاحقًا.
إيجابيات وسلبيات ماكينات تشكيل ألواح الأسقف
المزايا:
- أحجام إنتاج عالية تصل إلى 16,000 قدم مربع/ساعة
- انخفاض نفايات المواد تحت 1%
- جودة متسقة مع العملية الميكانيكية
- القدرة على إنشاء ملفات تعريف مخصصة
- الإنتاج في الوقت المناسب من تغذية اللفائف
- تقليل العمالة والوقت اللازمين لبناء السقف
- ألواح أخف وزناً وأقوى مقارنةً بالألواح المبنية في الموقع
- تتعامل مع مختلف المعادن - الصلب والألومنيوم والنحاس وغيرها.
- مرونة للتغييرات في تصميم اللوحة
- تكاليف أقل على المدى الطويل من الطرق الأخرى
القيود:
- استثمار رأسمالي كبير مطلوب
- التركيبات الثابتة الدائمة لمصانع الأسطح
- الفنيون المهرة اللازمون للبرمجة والتشغيل والصيانة
- وقت التغيير المطلوب عند تبديل الملفات الشخصية
- القدرة محدودة بعرض الماكينة وسرعتها وتغذيتها
- احتمالية وجود عيوب في اللفائف تفسد اللوحات
- قدرة تشكيل محدودة تتجاوز نسبة التمدد 1:1
- العمليات النهائية مثل التقطيع والتكديس اللازمة
عندما تتوافق المتطلبات مع إمكانيات الماكينة، توفر القوالب الدوارة إنتاج ألواح الأسقف بسرعة واقتصادية.
الأسئلة الشائعة
س: ما هي سماكة الصفائح المعدنية التي يمكن لماكينات تشكيل ألواح السقف الدوارة معالجتها؟
ج: ماكينات قياسية لتشكيل الصفائح من 18 جرامًا إلى 3/16 بوصة. تتوفر نطاقات موسعة للمعادن الأرفع/الأسمك.
**س: ما هي مدة إنتاج ألواح التسقيف؟ **
ج: إنتاج أطوال تصل إلى 300 قدم بدون توقف من تغذية الصلب الملفوف. ألواح مقطوعة بأطوال محددة.
س: ما هي تكلفة معدات تشكيل ألواح السقف؟
ج: تتراوح الأسعار على نطاق واسع من $50,000 إلى أكثر من $500,000 حسب السرعة والحجم والميزات.
س: ما هي أجهزة السلامة المضمنة؟
ج: واقيات مغلقة بالكامل، ومفاتيح إيقاف طوارئ، ومفاتيح أمان يدوية مزدوجة، ودوائر قطع للحماية.
سؤال: ما مدى سرعة تغيير القوالب عند تبديل التشكيلات؟
ج: حوالي 15-30 دقيقة للمشغلين المهرة. تصميمات التغيير السريع للقالب تقلل من الوقت.
س: ما هي أنواع المعادن التي يمكن تشكيلها في ألواح الأسقف؟
ج: الفولاذ المجلفن والألومنيوم والنحاس والزنك والفولاذ المقاوم للصدأ. بعض الماكينات من التيتانيوم.
س: هل يمكنني الحصول على تشكيلات أو أدوات مخصصة لألواح السقف؟
ج: نعم، يقدم الموردون ذوو السمعة الطيبة خدمات تصميم الملامح والأدوات حسب الطلب.
س: ما الذي يحدد سرعة الإنتاج أو المخرجات؟
ج: تحدد سرعة الخط، وعرض المظهر الجانبي، وسُمك المادة، وكفاءة الماكينة معدل الإنتاج.
س: ما هي متطلبات الطاقة؟
ج: عادةً ما يكون النظام الكهربائي الرئيسي 480 فولت، 3 أطوار، 50-60 هرتز. وتتوفر أنظمة أخرى عند الطلب.
س: هل تحتاج ماكينات ألواح السقف إلى أساسات؟
ج: تتطلب خطوط اللف الدائمة أسساً مناسبة. يمكن أن تعمل الماكينات المحمولة على أسطح مستوية.
س: ما هي العوامل التي تؤثر على تكلفة ألواح السقف اللفافة السابقة؟
ج: تؤثر السرعة والحجم والميزات والخيارات والعلامة التجارية والجودة وحجم الطلب على الأسعار أكثر من غيرها.