تخيل ماكينة يمكنها تحويل صفيحة معدنية مسطحة إلى أشكال معقدة، مثل مكونات البناء، أو الإطارات، أو حتى حواجز حماية الطرق السريعة. هذا هو سحر آلة تشكيل لفةوفي قلب هذا التحول المعدني يكمن لاعب أساسي: الصفيحة الفولاذية المدرفلة على البارد.
قوة التدوير البارد: نظرة عامة
ألواح الصلب المدرفلة على البارد (CRS) هي صفائح الصلب التي خضعت لعملية الدرفلة على البارد. وعلى عكس الدرفلة على الساخن، والتي تنطوي على تشكيل الفولاذ الساخن الأحمر، يتم تشكيل ألواح الصلب المدرفلة على البارد في درجة حرارة الغرفة. وتضفي هذه العملية العديد من المزايا الرئيسية:
- لمسة نهائية فائقة: تتميز CRS بسطح أملس ونظيف ومثالي للتطبيقات التي تتطلب مظهراً مصقولاً أو تشكيل دقيق.
- دقة الأبعاد: يضمن الدرفلة على البارد تفاوتات أكثر إحكاماً وسماكة أكثر اتساقاً مقارنةً بالفولاذ المدرفل على الساخن.
- قوة معززة: تعمل عملية الشغل على البارد على تقوية الفولاذ، مما يجعله مناسبًا للتطبيقات الحاملة.
- تعدد الاستخدامات: تأتي CRS في مجموعة واسعة من السماكات والعروض والتشطيبات، مما يلبي احتياجات التشكيل بالدلفنة المتنوعة.
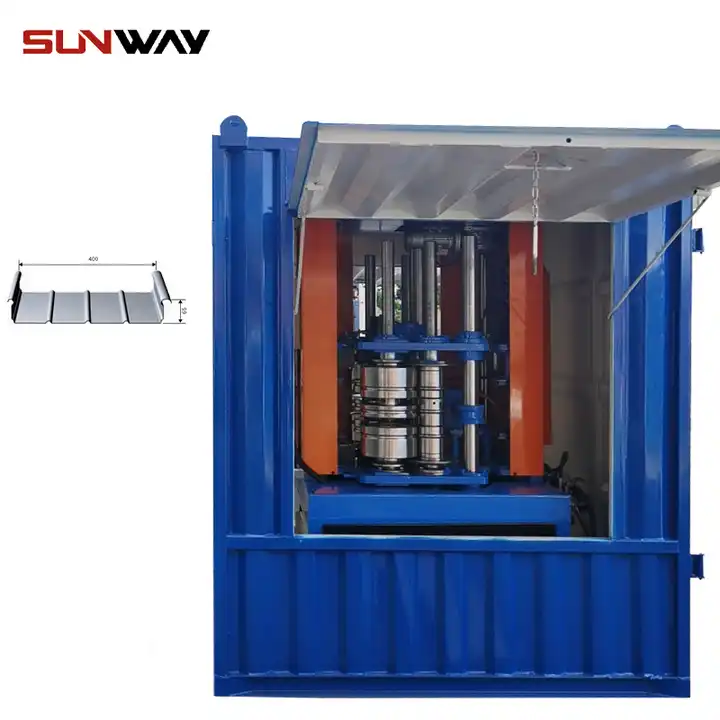
ميزة CRS: تحليل وظيفي
فيما يلي نظرة عن كثب على كيفية مساهمة لوحات CRS في وظيفة آلة تشكيل لفة:
الوظيفة | الوصف | المزايا |
---|---|---|
مواد لفات التشكيل | ألواح CRS هي اللبنات الأساسية لمحطات التشكيل داخل الماكينة. تعمل هذه اللفات المشغولة بدقة على ثني الصفيحة المعدنية وتشكيلها تدريجياً إلى الشكل الجانبي المطلوب. | * المتانة: يوفر CRS قوة ممتازة ومقاومة ممتازة للتآكل لتحمل الضغط المستمر لتشكيل المعدن. * قابلية التشكيل: تعمل عملية الشغل على البارد على تعزيز مرونة الفولاذ، مما يسمح بإنشاء أشكال معقدة. * قابلية التشغيل الآلي: يسهل سطح CRS الأملس والسماكة المتناسقة للكرات القابلة للتشكيل بدقة. |
إمكانات التخصيص | تعتمد القدرة على إنشاء مقاطع جانبية مخصصة في ماكينات التشكيل بالدلفنة اعتمادًا كبيرًا على ألواح CRS. فمن خلال تصميم وتصنيع أخاديد وأشكال محددة على الألواح، يمكن للمصنعين إنتاج مجموعة كبيرة من التشكيلات الجانبية. | * مرونة التصميم: يسمح نظام CRS بإنشاء أشكال معقدة لا يمكن تحقيقها باستخدام التشكيلات القياسية. * تعدد استخدامات المنتج: وهذا يفتح الأبواب أمام مجموعة واسعة من التطبيقات للمنتجات المشكلة بالدرفلة. |
الصيانة والصيانة | يمكن لألواح CRS، بسبب قوتها المتأصلة، أن تتحمل سنوات من التشغيل. ومع ذلك، فإن البلى والتلف أمر لا مفر منه. | * صيانة فعالة من حيث التكلفة: غالبًا ما يكون استبدال بكرات تشكيل CRS الفردية أكثر توفيرًا من إصلاح الماكينة بأكملها. * مواد متاحة بسهولة: تعتبر CRS مادة يتم إنتاجها على نطاق واسع، مما يجعل البدائل متاحة بسهولة، مما يقلل من وقت التعطل. |
تطبيقات الصفيحة الفولاذية المدرفلة على البارد في ماكينة التشكيل على البارد
يمتد تأثير CRS إلى ما هو أبعد من الماكينة نفسها. فالمنتجات المشكّلة بالدلفنة من ألواح CRS تجد تطبيقات في مختلف الصناعات:
- البناء: تشكل CRS العمود الفقري لمكونات البناء مثل ألواح الأسقف والجدران وإطارات الأبواب والنوافذ والدعامات الهيكلية.
- السيارات: من إطارات السيارات وألواح الهيكل إلى قطع الزخارف ومكونات الهيكل السفلي، تلعب CRS دورًا حيويًا في تصنيع السيارات.
- تصنيع الأجهزة: تُستخدم CRS لإنشاء هياكل الأجهزة والرفوف والعناصر الهيكلية الأخرى.
- الأثاث: يمكن تشكيل جميع إطارات الكراسي وأرجل الطاولات والعناصر الزخرفية من CRS.
- أنظمة التدفئة والتهوية وتكييف الهواء: وغالباً ما تستخدم مجاري الهواء ومكونات التهوية أشكالاً من CRS الملفوفة.
استكشاف مشهد CRS: الموردون والتسعير
يعتمد توافر لوحات CRS وتكلفتها على عدة عوامل، بما في ذلك:
- السُمك: الألواح السميكة تتطلب بطبيعة الحال سعراً أعلى.
- العرض: تكون الألواح الأعرض أغلى ثمناً بشكل عام.
- النهاية: قد تترتب تكاليف إضافية على ألواح CRS المعالجة أو المغلفة بشكل خاص.
- الكمية: غالباً ما تجذب المشتريات بالجملة خصومات.
إليك لمحة عن مشهد الموردين:
- مراكز خدمة الصلب: تخزن هذه المنشآت مجموعة واسعة من منتجات CRS وتقدم خدمات ذات قيمة مضافة مثل القص والقطع بأبعاد محددة.
- مصانع الصلب: قد يقوم كبار منتجي الصلب بعرض CRS مباشرة، ولكن قد يكون الحد الأدنى لكميات الطلبات أعلى.
- بائعو التجزئة عبر الإنترنت: وهناك العديد من المنصات الإلكترونية التي تربط المشترين بموردي نظم الإبلاغ الموحد، مما يوفر خياراً مناسباً للمشاريع الصغيرة.
-
ماكينة تشكيل الطرفية الطرفية لحاجز الحماية على الطريق السريع
-
ماكينة تشكيل الأعمدة على الطريق السريع U/C
-
2 ماكينة تشكيل حواجز الحماية على الطرق السريعة ذات الموجات 2
-
3 ماكينات تشكيل حواجز الحماية للطرق السريعة ذات 3 موجات
-
آلة التشكيل بالدلفنة لكروم العنب
-
آلة تشكيل لفة Sigma Purlin قابلة للتغيير ذات الحجم الأوتوماتيكي
-
آلة التشكيل بالدلفنة لإطار الخزانة الكهربائية
-
آلة التشكيل بالدلفنة للسكك الحديدية Din
-
اثنين من موجات الطريق السريع الدرابزين آلة
فهم احتياجاتك: اختيار نظام إدارة علاقات العملاء المناسب
يتطلب اختيار نظام CRS الأمثل لتطبيق التشكيل بالدلفنة الخاص بك دراسة دقيقة لعدة عوامل:
- متطلبات الملف الشخصي: سيؤثر تعقيد المظهر الجانبي المطلوب على سُمك CRS المطلوب وقابلية التشكيل.
- متطلبات القوة: إن قدرة التحميل للمنتج المشكل بالدلفنة هي التي تحدد قوة التحميل المطلوبة من CRS.
- تفضيلات التشطيب: ضع في اعتبارك ما إذا كان الطلاء المطلي أو المجلفن أو المزيت ضرورياً من الناحية الجمالية أو لمقاومة التآكل.
- قيود الميزانية: وازن بين الميزات المرغوبة واعتبارات التكلفة عند اختيار نظام CRS.
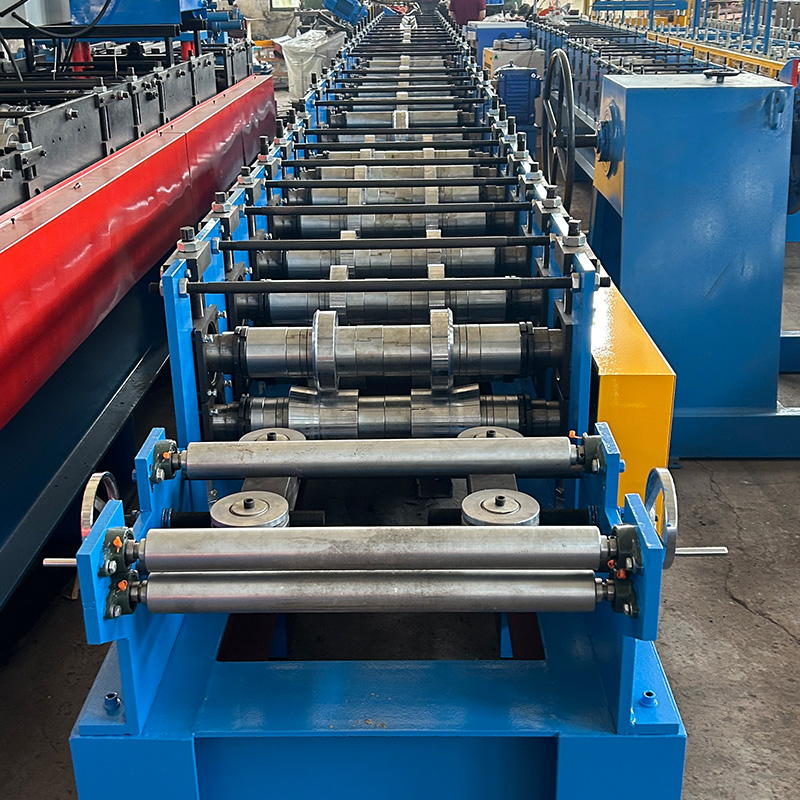
الأسئلة الشائعة
سؤال: ما هي مزايا استخدام ألواح CRS في آلات تشكيل اللف مقارنة بالمواد الأخرى؟
ج: يوفر نظام الإبلاغ الموحد مزيجاً مقنعاً من المزايا:
- لمسة نهائية فائقة: إن الحصول على مظهر سلس ومصقول على المنتج النهائي أسهل مع CRS نظرًا لجودة سطحه المتأصلة. ويمكن أن يكون هذا الأمر مهمًا بشكل خاص للتطبيقات التي يكون فيها المظهر الجمالي مهمًا، مثل الألواح المعمارية أو مكونات الأجهزة.
- دقة الأبعاد: التفاوتات الضيقة والسماكة المتسقة ضرورية للتشكيل الدقيق. تتفوق CRS في هذه الجوانب، مما يقلل من حالات رفض الإنتاج ويضمن جودة المنتج المتسقة.
- قابلية التشكيل: تعمل عملية الشغل على البارد على تعزيز قدرة CRS على الانحناء والتوافق مع الأشكال المعقدة دون تشقق أو انقسام. وتسمح هذه المزايا المتعددة بإنشاء مقاطع جانبية معقدة.
- نسبة القوة إلى الوزن: توفر CRS توازنًا جيدًا بين القوة والوزن. وهذا يُترجم إلى منتجات قوية مشكلة بالدلفنة بدون وزن زائد، وهو ما يمكن أن يكون مصدر قلق في بعض التطبيقات مثل مكونات السيارات.
- الفعالية من حيث التكلفة: وبالمقارنة مع بعض المعادن المتخصصة، فإن CRS مادة معقولة التكلفة نسبياً. وهذا يجعله خياراً جذاباً لعمليات الإنتاج بكميات كبيرة.
س: هل هناك أي قيود على استخدام CRS في التشكيل بالدرفلة؟
ج: على الرغم من أن CRS مادة متعددة الاستخدامات، إلا أن لها بعض القيود التي يجب مراعاتها:
- قيود القوة: بالنسبة للتطبيقات ذات القوة العالية بشكل استثنائي، قد لا يكون الفولاذ المقاوم للصدأ CRS كافيًا. وفي هذه الحالات، قد يكون الفولاذ المدلفن على الساخن أو حتى الفولاذ عالي القوة خيارًا أفضل.
- قيود القابلية للتشكيل: في حين توفر CRS قابلية تشكيل جيدة، قد تتطلب بعض الأشكال المعقدة للغاية مواد أكثر مرونة مثل الألومنيوم أو الفولاذ المغلف مسبقًا.
- مقاومة التآكل: تكون حوامل CRS القياسية عرضة للصدأ. إذا كانت مقاومة التآكل هي الشغل الشاغل، فينبغي استكشاف خيارات CRS المجلفنة أو المطلية مسبقًا.
س: ما مدى سماكة ألواح CRS المستخدمة في ماكينات التشكيل بالدلفنة؟
ج: تقع سماكة ألواح CRS المناسبة لماكينات التشكيل بالدلفنة عادةً في نطاق يتراوح بين 0.4 ملليمتر (0.015 بوصة) إلى 6.35 ملليمتر (0.25 بوصة). تعتمد السماكة المثالية على المظهر الجانبي المحدد الذي يتم تشكيله. تعتبر الألواح السميكة أكثر ملاءمة لإنشاء مكونات هيكلية قوية، بينما توفر الألواح الرقيقة مرونة أكبر للأشكال المعقدة.
س: كم تبلغ تكلفة لوحات CRS عادةً؟
ج: تتقلب تكلفة لوحات CRS بناءً على عدة عوامل، بما في ذلك:
- ظروف السوق: يمكن أن تؤثر الأسعار العالمية للصلب على تكلفة CRS.
- المورد: قد يكون لدى الموردين المختلفين هياكل تسعير مختلفة.
- الكمية: غالباً ما تجتذب المشتريات بالجملة خصومات على الحجم.
- المواصفات: تؤثر السماكة والعرض واللمسات النهائية على السعر.
ومع ذلك، فإن هذا مجرد رقم تقريبي، ومن المهم الحصول على عروض أسعار من الموردين المحتملين بناءً على متطلباتك المحددة.
س: أين يمكنني العثور على موردي ألواح CRS لعملية التشكيل بالدلفنة الخاصة بي؟
توجد عدة طرق للحصول على لوحات CRS:
- مراكز خدمة الصلب: تقوم هذه الشركات المحلية بتخزين مجموعة كبيرة ومتنوعة من منتجات CRS وتقدم خدمات المعالجة مثل القص والتقطيع حسب الأبعاد التي تريدها. ويمكن أن تكون متجراً شاملاً مناسباً للكميات الصغيرة.
- مصانع الصلب: قد يقوم كبار منتجي الصلب ببيع CRS مباشرة، ولكن قد يكون الحد الأدنى لكميات الطلبات أعلى. وقد يكون هذا الخيار مناسباً لعمليات الإنتاج بكميات كبيرة.
- بائعو التجزئة عبر الإنترنت: وهناك العديد من المنصات الإلكترونية التي تربط المشترين بموردي خدمات الحفارات على الإنترنت في جميع أنحاء البلاد. يمكن أن يكون هذا خياراً جيداً للعثور على أسعار تنافسية، خاصة بالنسبة للمشاريع الصغيرة.
تذكّر عند اختيار المورد، ضع في اعتبارك عوامل مثل التسعير والمهل الزمنية والحد الأدنى لكميات الطلبات والخدمات ذات القيمة المضافة المقدمة.
الخاتمة
تلعب ألواح الفولاذ المدرفلة على البارد دورًا لا غنى عنه في عالم ماكينات التشكيل على البارد. إن مزيجها الفريد من القوة وقابلية التشكيل والقدرة على تحمل التكاليف وتوافرها على نطاق واسع يجعلها المادة المفضلة لمجموعة كبيرة من التطبيقات. من خلال فهم خصائص ألواح الصلب المدلفن على البارد وكيفية اختيار النوع المناسب لاحتياجاتك، يمكنك ضمان التشغيل السلس لماكينة التشكيل على البارد وإنشاء منتجات عالية الجودة.