Urban infrastructure relies on efficient drainage systems to manage stormwater and prevent flooding. As cities grow, the demand for durable and cost-effective drainage products increases. Downpipe roll forming machines play a vital role in manufacturing the metal pipes and connectors that make up these critical drainage systems.
An Introduction to Downpipe Roll Forming Machines
A downpipe roll forming machine is a specialized machine used to manufacture downpipes, gutters, and other drainage products from coil metal. The roll forming process involves gradually bending and shaping sheet metal through a series of roller dies until the desired pipe or gutter profile is achieved.
Roll formed downpipes offer many advantages over other manufacturing processes:
- High Production Speeds – Modern downpipe roll forming machines can operate at speeds over 100 feet per minute. This allows for high volume production to meet market demand.
- Consistency – The roll forming process ensures each section has the exact same specifications and quality. This allows downpipes to join together neatly and function properly.
- Cost Effectiveness – Roll forming is an efficient metal shaping process requiring less raw material than other methods. The automated process also requires less labor.
- Flexibility – Roll forming machines can produce pipes and gutters of varying dimensions, thicknesses, and materials by changing the roller dies.
- Durability – Roll formed downpipes have a uniform shape and smooth surface that resists corrosion and enhances durability.
Downpipe roll forming creates pipes resistant to weathering, rust, and mechanical stress. This durability and longevity make roll formed products ideal for urban drainage infrastructure.
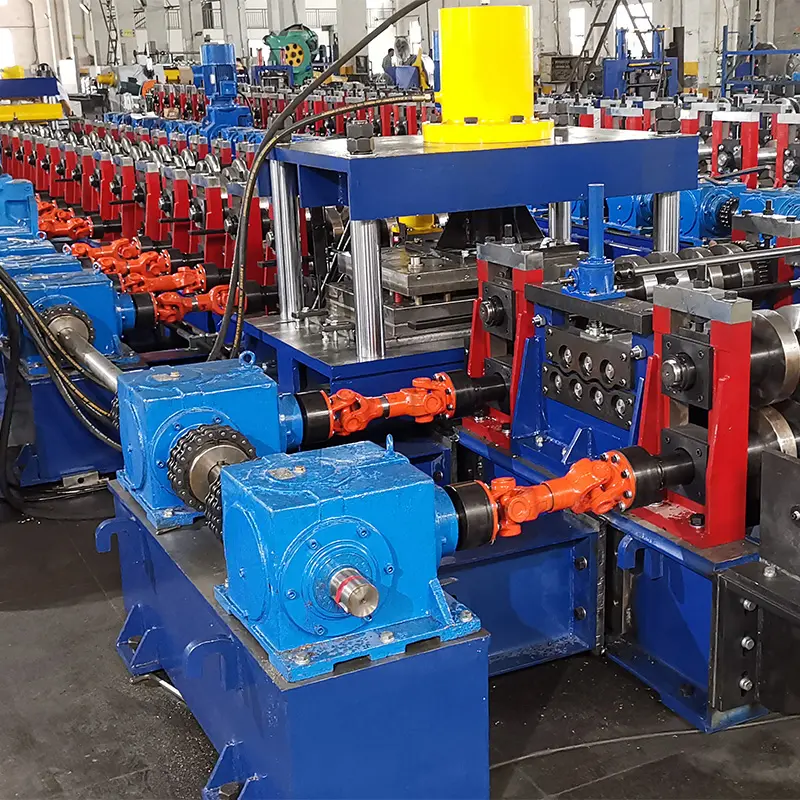
Downpipe Roll Forming Machines in Urban Drainage Systems
Urban population growth puts pressure on existing stormwater infrastructure. As more areas are paved over, increased stormwater runoff can exceed drain capacity and cause flooding. Proper drainage prevents waterlogging and damage during heavy rains. Complete drainage systems consisting of downpipes, gutters, and connectors are necessary to divert water safely away from buildings and streets.
Downpipe roll forming machines enable high production of standard and custom drainage components necessary for efficient drainage networks across cities.
Downpipes
Downpipes, also known as rainwater pipes or drainpipes, carry rainwater from rooftops and gutters down to the ground or drainage system. Roll formed downpipes are widely used due to their snap-fit modular design. Standard 10 ft sections featuring smooth surfaces and uniform diameters join together to form complete downpipe systems. Custom bent sections are also produced to fit site requirements.
Made from galvanized steel, aluminum, or stainless steel, roll formed downpipes offer superior corrosion resistance and strength to plastic alternatives. The lasting durability of metal downpipes reduces the need for replacement and maintenance.
Gutters
Gutters collect and channel rainwater runoff from rooftops into downpipes. Roll formed gutters available in various styles, sizes, and metal finishes seamlessly integrate with downpipe systems.Specialized gutter roll forming machines produce strong gutter profiles resistant to leakage, rust, and debris buildup. This ensures proper water flow into downpipes.
Elbows, Couplers, and Accessories
Roll formed downpipe systems require additional accessories to guide water flow around corners and join pipe sections. Elbows, couplers, end caps, brackets, and hanger straps can all be manufacturered by roll forming machines. Standardized accessories and seamless integration with downpipes and gutters facilitate efficient installation.
Benefits of Roll Formed Drainage Products for Urban Areas
Downpipe roll forming machines enable durable and modular drainage components that offer multiple advantages for managing stormwater in urban environments:
- ** Flood Prevention** – Downpipe systems prevent overflow and localized flooding by efficiently diverting roof and surface runoff.
- Storm Resilience – Durable metal downpipes are able to withstand heavy rain, high wind speeds, and debris during extreme weather.
- Low Maintenance – Corrosion and rust resistant downpipes retain smooth water flow for decades without cleaning or repairs.
- Noise Reduction – Roll formed downpipes absorb and reduce rainfall noise versus plastic drain pipes. This helps maintain peaceful urban soundscapes.
- Aesthetics – Downpipes and gutters come in various finishes to complement building exteriors and general streetscapes.
- Scalability – Standardized roll-formed components can expand existing drainage networks as urban areas grow.
- Sustainability – Recyclable metal downpipes have lower embodied energy than plastic alternatives to support green building practices.
Proper stormwater management is crucial for urban livability and resilience. Roll formed downpipes and gutters provide long-lasting and adaptable drainage essential for future-proofing cities.
Technical Specifications of Downpipe Roll Forming Machines
Downpipe roll forming relies on precision machinery to produce consistent and accurate drainage components. The process involves uncoiling sheet metal and running it through a motorized forming station containing a series of roller dies that gradually shape the material. The formed downpipe is then cut into standard lengths by an automated cutting machine.
Key specifications of downpipe roll forming machines include:
- फॉर्मिंग स्टेशन – Contains 10-18 roller dies in a sequential arrangement that progressively bend/form the material into the downpipe profile.
- Roller Dies – Made of hardened steel and precisely engineered for durability. Various die sets available for manufacturing different pipe sizes and styles.
- Die Box – Houses the roller dies and provides structural support for high-pressure metal forming.
- Feeding System – Sets of powered rollers that continuously pull and guide the sheet metal through the forming station.
- Hydraulic System – Provides power to the rolling dies for uniform pressure along the entire forming length.
- Cutting Device – Automated circular or guillotine-style blade that cuts formed pipes into set lengths for easy shipping and installation.
- Control Panel – Computerized control panel allows operators to adjust machine settings and parameters.
- चौखटा – Rigid steel frame absorbs vibration and keeps components securely aligned during operation.
- Conveyors – Carry finished downpipe pieces away from the machine for inspection and packaging.
Advanced downpipe roll forming machines can produce over 300 ft of pipe per minute with tolerances within 0.5mm for high precision drainage components.
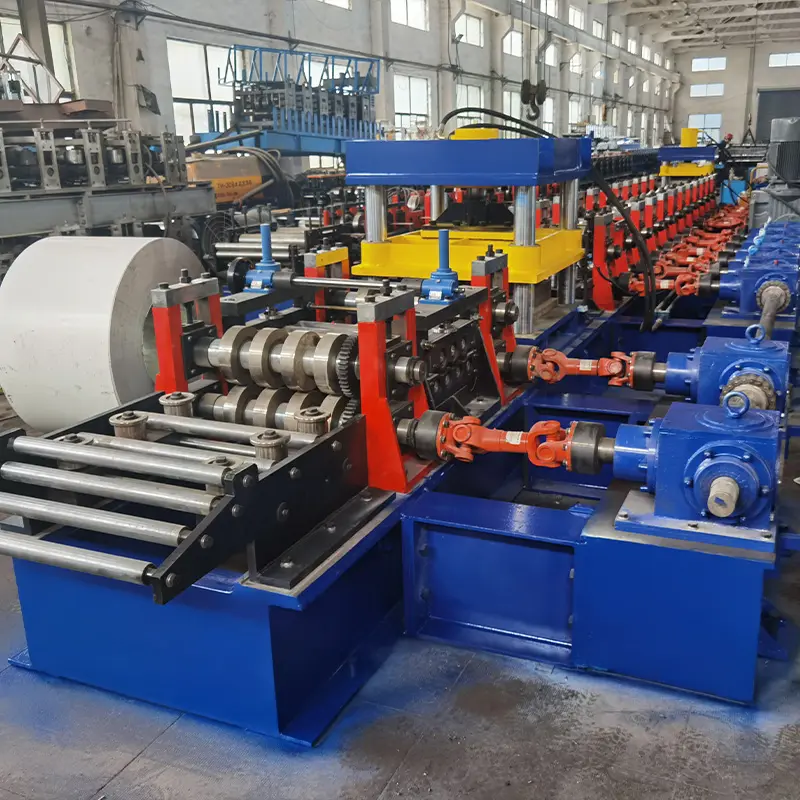
The Pipe Manufacturing Process
The full downpipe production process consists of multiple stages:
1. Design
Engineers draft the pipe design in 3D CAD software based on project specifications. The CAD files are used to engineer the custom roller dies needed to form each unique pipe profile.
2. Raw Material Preparation
Metal coils of the required gauge and width are loaded onto the unwinding reel of the roll forming machine. Common materials include galvanized steel, aluminum, and stainless steel.
3. Roll Forming
The coil sheet enters the roll forming machine and passes through the sequential roller dies to be gradually formed into a downpipe shape. The hydraulic system applies consistent pressure for uniform bending.
4. Cutting
The finished downpipe is cut to length by the automated cutting machine. Lengths are usually in 10 ft segments for easy handling and joining.
5. Hole Punching
Some downpipe sections have holes punched at set intervals to allow for brackets or cable ties to mount the pipes. This takes place after cutting.
6. Packaging
Formed downpipe pieces are manually inspected then packed into bundles for shipping. Custom packaging protects the finished products from damage.
7. Inventory & Distribution
Packed downpipe material is sent to warehouses and distribution centers to await purchase and delivery. Inventory management coordinates production with market demand.
Applications Across Urban Infrastructure Projects
Downpipe roll forming machines support drainage system installation for diverse building and infrastructure projects across urban areas:
Commercial Buildings
Schools, hospitals, offices, shopping malls, and other commercial sites rely on integrated gutter and downpipe systems to control runoff from vast roof surfaces.
Residential Buildings
Condo complexes and housing projects utilize downpipe systems to prevent water damage and moisture accumulation within densely packed homes.
Transportation Infrastructure
Bridges, overpasses, tunnels, and transport stations require drainage pipes to redirect water away from critical infrastructure.
Storm Drains
Downpipe machines produce the metal pipe fittings that connect street-level storm drain inlets to underground collection pipes.
Sports Arenas
Stadium seating and expansive arena roofs demand high capacity drainage to handle heavy rainfall.
Urban Flood Control
Flood barrier walls, levees, pumping stations, and drainage networks incorporate large-scale downpipe systems for storm resilience.
In addition to standard drainage functions, creative downpipe implementations take on unique roles across urban communities:
- Community art murals and sculptures
- Rain harvesting systems
- Charging stations for electric vehicles
- Integration with solar panels
- Heat exchange systems
Downpipe Roll Forming Machine Manufacturers
Leading downpipe roll forming machine manufacturers include:
Best engineers
Best Engineers is an Indian manufacturer of high quality roll forming machines used to produce roofing, wall paneling, solar mounting systems, and drainage products. Their downpipe and gutter roll forming machines incorporate European engineering for optimal efficiency and precision pipe forming.
Botou Xianfa Roll Forming Machine Factory
With over 19 years of experience, this Chinese company produces affordable downpipe roll forming machines with extensive customization options. They offer equipment specifically designed for drainage system production.
Zeman Bauelemente GmbH
Based in Austria, Zeman supplies innovative downpipe roll forming lines engineered for high-volume drainage component manufacturing. Advanced 3D scanning technology ensures their machines produce pipes with tight tolerances.
फॉर्मटेक ग्रुप
The Formtek Group provides technologically advanced downpipe roll forming equipment that integrates inline punching and cutting after forming. Based in Taiwan, they are a leading Asia supplier with global export experience.
Finform Group SRL
Finform Group is an Italian roll forming machine manufacturer with expertise in designing high-output downpipe and gutter production lines. Their flexible equipment can rapidly switch between multiple profile shapes and sizes.
Kingsland Engineering Ltd
Kingsland produces a comprehensive range of roll forming machines for roofing and cladding, including the KD288 model built specifically for downpipe manufacturing. The UK-based company provides machines to over 75 countries worldwide.
Cost Considerations
Downpipe roll forming machine prices vary based on:
- Production Output – Higher capacity machines for mass production cost more.
- Automation Features – Programmable control systems and instrumentation increase costs.
- Advanced Tooling – More complex die sets, punching, and cutting raise the price.
- Raw Material Capability – Stainless steel compatible machines cost more than low carbon steel only models.
- Brand Reputation – Leading international brands commands higher pricing. Low-cost Chinese manufacturers offer cheaper alternatives.
Other factors like customization, shipping expenses, training, and installation costs can impact total machine expenditures. Typically, prices range from:
- Manual Downpipe Machine – $8,000 to $15,000
- Semi-automatic Machine – $15,000 to $35,000
- Fully Automatic High Output Machine – $50,000 to $120,000
Purchasing used machinery can lower startup costs for small businesses. However, productivity and consistency may be reduced compared to new machines.
Benefits of Investing in Downpipe Roll Forming Equipment
- Meet Market Demand – Efficiently produce high quality downpipes to capture a share of the growing market.
- Consistent Quality – Automated process provides reliable and uniform output.
- Low Operating Costs – Requires less raw material, labor, and energy than traditional fabrication.
- High Production Rates – Output several hundred feet per minute for large volume capabilities.
- Product Diversification – Ability to manufacture multiple pipe and gutter styles by changing roller dies.
- Custom Capabilities – Roll form specialized downpipe designs for unique architectural projects.
- Reduced Labor Requirements – Automated equipment increases throughput while reducing manual work.
Investing in capable downpipe roll forming machines positions businesses to capitalize on private and public sector drainage infrastructure projects.
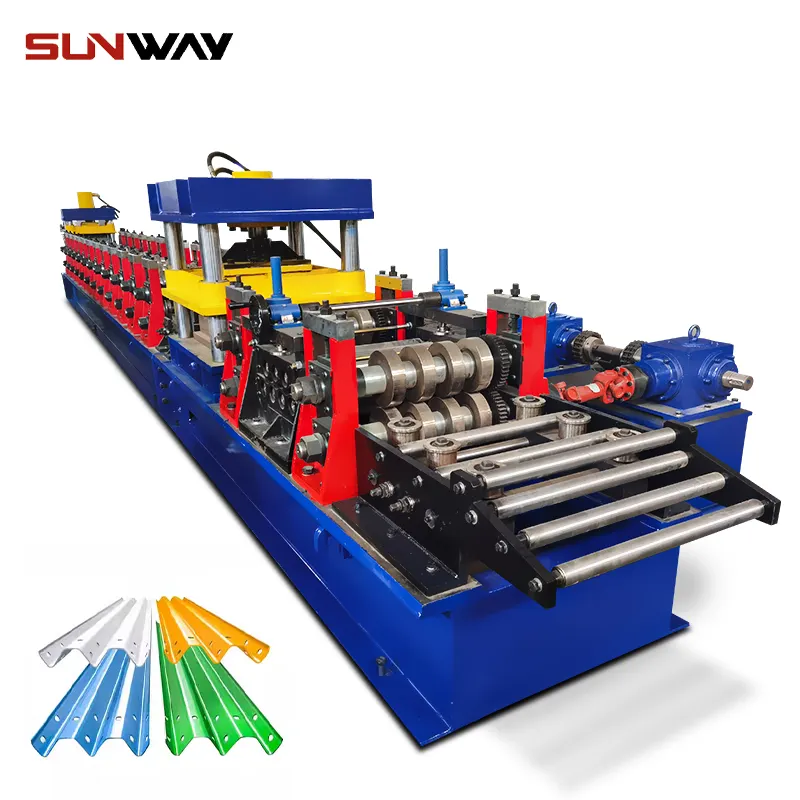
Future Outlook
Urban development will continue to drive demand for durable and high-capacity drainage products worldwide. Construction activity forecasts predict steady growth in both residential and commercial building sectors, along with increased infrastructure investment. This bodes well for increased adoption of efficient downpipe roll forming technology.
At the same time, rising focus on environmental sustainability is expected to further boost use of steel and aluminum over plastic components. Roll formed metal provides outstanding durability and recyclability to support green building.
Advanced in-line part manipulation, automation, and quality control will enable new generations of high-precision downpipe roll forming equipment. Integration of the internet of things and industry 4.0 practices will also assist efficiency and production flexibility improvements.
Overall, downpipe roll forming machines represent a sound investment opportunity given the essential and growing role of drainage infrastructure across expanding urban landscapes worldwide. Superior quality, performance, and longevity will cement roll formed downpipes as a fixture within sustainable and climate resilient cities.
सामान्य प्रश्न
What materials can you use on a downpipe roll forming machine?
The most common materials are galvanized steel, stainless steel, and aluminum. Some machines also support titanium, copper, and alloy metals provided they can withstand the high pressures.
What thickness of metal sheet is normally used?
Standard sheet metal thickness for drainage pipes ranges from 0.4mm to 1mm. Higher end machines can form up to 2mm thickness for heavy duty applications.
What is the difference between manual vs automatic downpipe machines?
Manual machines require operators to feed in the coil stock and transfer finished pipes. Automatic machines handle coil loading, forming, cutting, and offloading automatically for complete start-to-finish automation.
How easy is it to adjust a machine to form different pipe sizes?
One of the key advantages of roll forming is easy size adjustment. Different style roller dies are simply swapped out within the die box to produce different profiles. The process takes as little as 10-15 minutes.
What is the typical production rate?
Basic manual machines produce around 70-100 ft of downpipe per minute. High end automated machines with optimized hydraulics can achieve over 300 ft/min production rates.
What factors affect downpipe machine prices?
Major factors include production speed, automation level, durability, raw material capabilities, brand reputation, and customization extent. Advanced features and higher build quality increase costs.
Can downpipe machines be used to make other products?
Yes, with a change of roller dies, the machines can produce various profiles like roofing panels, wall panels, open channels, solar frame components etc. Some machines can alternate between multiple products.