परिचय
When it comes to modern construction, efficiency, precision, and cost-effectiveness are paramount. The छत की दीवार पैनल रोल बनाने की मशीन is a remarkable piece of equipment that has transformed the way roofing and wall cladding elements are manufactured. In this article, we will explore the ins and outs of the roof wall panel roll forming machine, from its components and operation to its diverse applications in various industries.
Understanding Roof Wall Panel Roll Forming Machine
रोल बनाने की मशीन क्या है?
A roll forming machine is a specialized equipment used to shape metal sheets or coils into a desired cross-section profile. The process involves continuous bending of the material along a series of rollers, each performing a specific shaping function.
Roof Wall Panel Roll Forming Machine: An Overview
The roof wall panel roll forming machine is designed specifically for producing roof panels and wall cladding sheets with precision and consistency. It can handle a wide range of materials, including steel, aluminum, and copper, making it a versatile choice for various industries.
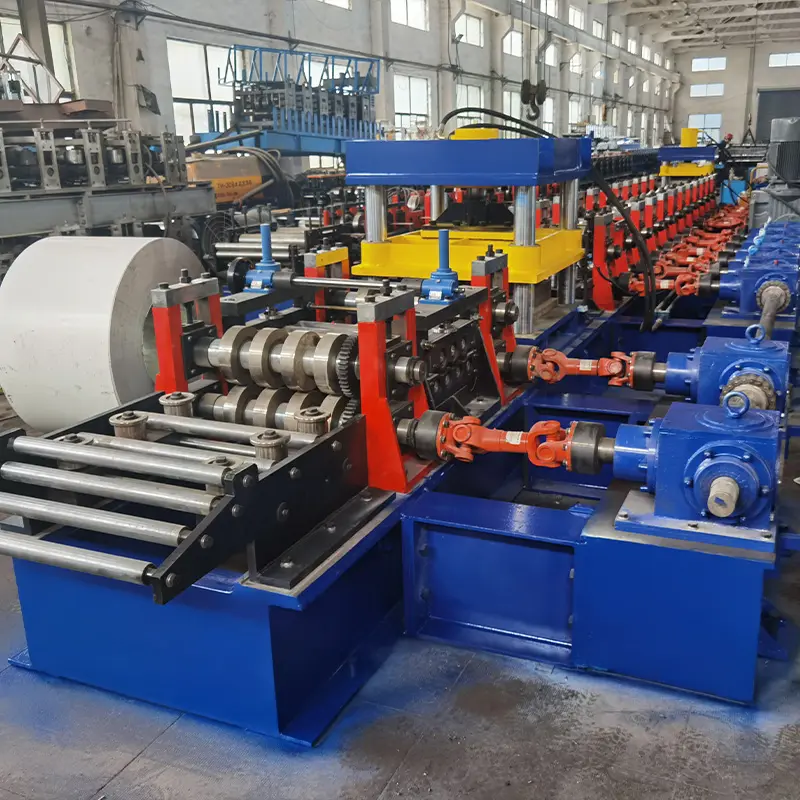
Key Components of a Roof Wall Panel Roll Forming Machine
The roof wall panel roll forming machine comprises several essential components that work together to deliver seamless production.
Entry Section
The entry section is where the raw material, typically a coil or sheet, is loaded into the machine. It sets the initial path for the material to pass through the roll forming process.
Roll Forming Section
The roll forming section consists of a series of rollers that gradually shape the material into the desired profile. Each roller performs a specific bending action, and the sequence is carefully engineered to achieve the final shape.
कटिंग सिस्टम
Once the material has been formed into the desired profile, the cutting system comes into play. It precisely cuts the continuous sheet into individual panels of specified lengths.
नियंत्रण प्रणाली
The control system is the brain of the roof wall panel roll forming machine. It monitors and regulates the entire process, ensuring accurate dimensions and minimizing material waste.
The Roll Forming Process Explained
The roll forming process is a systematic series of steps that transform a flat sheet of metal into a complex cross-sectional profile. Let’s take a closer look at each stage:
Coil Loading
The process begins with loading a coil of raw material onto the entry section of the machine. The coil is fed into the roll forming section, ready for shaping.
Feeding and Guiding
As the material enters the roll forming section, it is continuously fed and guided through a series of rollers. These rollers gradually shape the material as it progresses through the machine.
रोल बनाना
During roll forming, each roller exerts a specific force on the material, bending it into the desired shape. The cumulative effect of multiple rollers results in the complete profile.
Cutting and Shearing
Once the material has been fully formed, the cutting system activates and accurately cuts the continuous sheet into individual panels of specified lengths.
Stacking and Unloading
After cutting, the finished panels are stacked and unloaded from the machine, ready for further processing or shipping.
Stay tuned for the second part of the article, where we’ll explore more about types of roof wall panel roll forming machines, their advantages, applications, and how to choose the right machine for your specific needs. The roof wall panel roll forming machine continues to be a game-changer in the construction industry, and understanding its intricacies is crucial for anyone involved in manufacturing roofing and wall cladding products.
Types of Roof Wall Panel Roll Forming Machines
Roll forming machines have evolved to meet the specific requirements of different industries and applications. Here are some common types of roof wall panel roll forming machines:
Single Roll Forming Machine
The single roll forming machine is a basic and cost-effective option for manufacturing simple roof and wall panel profiles. It is suitable for smaller-scale production with a limited range of product variations.
Double Layer Roll Forming Machine
A double layer roll forming machine is more versatile, allowing the production of two different profiles with a single machine. This option is ideal for manufacturers looking to expand their product offerings.
Continuous Roll Forming Machine
The continuous roll forming machine enables seamless and uninterrupted production, eliminating the need for stopping and starting between each panel. It is highly efficient for large-scale manufacturing.
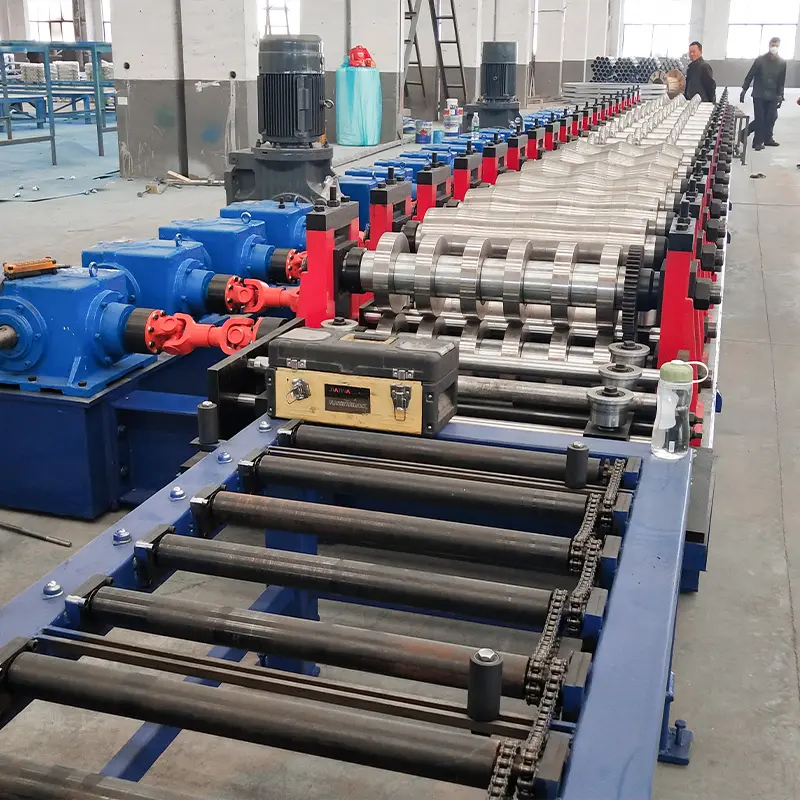
Advantages of Roof Wall Panel Roll Forming Machines
Efficiency and Productivity
Roof wall panel roll forming machines offer exceptional efficiency, allowing for rapid production of panels without compromising on quality. The continuous process and automated control systems contribute to enhanced productivity.
Versatility and Customization
With the ability to handle various materials and produce different profile designs, these machines offer unmatched versatility. Manufacturers can cater to specific customer demands and create custom-made panels.
Cost-Effectiveness
The reduced labor requirements and minimized material waste make roof wall panel roll forming machines a cost-effective solution for high-volume production.
Applications of Roof Wall Panel Roll Forming Machines
Construction Industry
In the construction sector, these machines are widely used to manufacture roof panels and wall cladding elements for residential, commercial, and industrial buildings. The precise shaping and consistent quality of the panels ensure they fit together seamlessly, providing excellent weather protection and aesthetic appeal to the structures.
Automotive Sector
The automotive industry also benefits from roof wall panel roll forming machines. These machines are utilized in the production of vehicle body components, such as roof rails and door panels. The ability to work with different metals and create complex shapes makes them valuable assets for automotive manufacturers.
Appliance Manufacturing
In the appliance manufacturing sector, roof wall panel roll forming machines play a crucial role in creating various housing components for appliances like refrigerators, washing machines, and air conditioners. The precise and efficient production process helps appliance manufacturers meet consumer demands and maintain competitive prices.
Furniture Production
Roof wall panel roll forming machines find application in the furniture industry as well. They are used to produce metal parts for furniture items like cabinets, drawers, and shelves. The customization options enable furniture manufacturers to create unique designs to suit their customers’ preferences.
Choosing the Right Roof Wall Panel Roll Forming Machine
Selecting the appropriate roof wall panel roll forming machine is essential to ensure optimal performance and efficiency. Here are some key factors to consider when making this decision:
Production Capacity
The production capacity of the machine should align with your manufacturing requirements. Evaluate the number of panels you need to produce per day or month and choose a machine that can meet or exceed that demand.
Material Compatibility
Consider the types of materials you plan to work with, such as steel, aluminum, or copper. Ensure that the machine you choose is capable of handling these materials without causing damage or compromising product quality.
Machine Size and Space Requirements
Evaluate the available space in your production facility and choose a machine that fits comfortably within that space. Additionally, consider the ease of installation and maintenance of the machine.
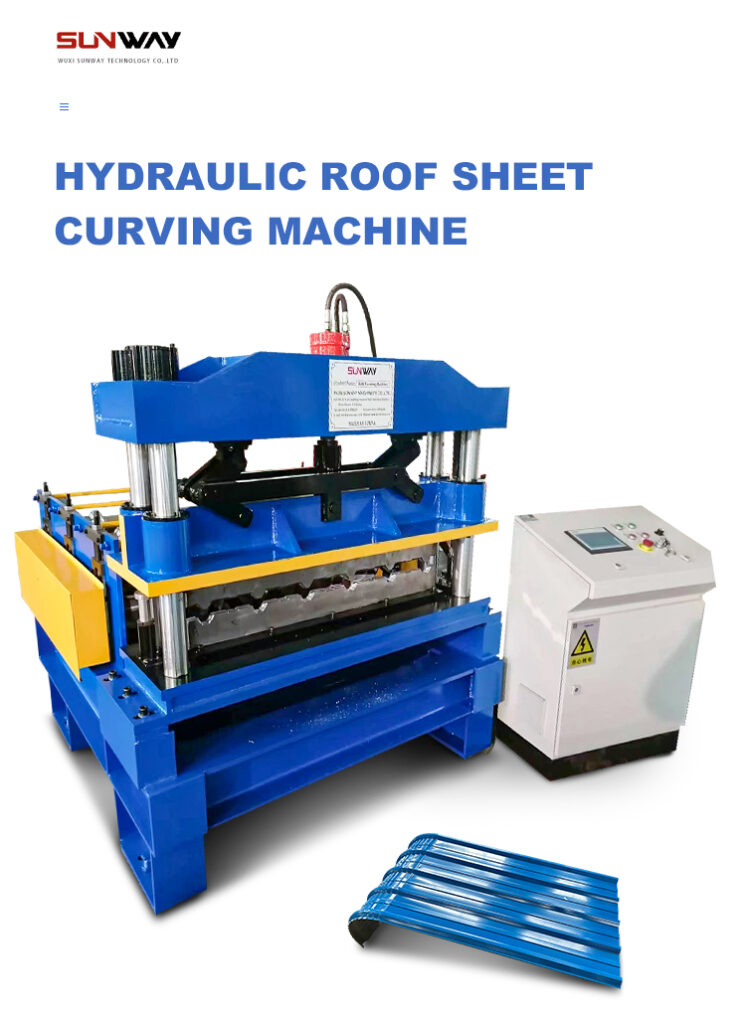
Maintenance and Safety Tips
Maintaining a roof wall panel roll forming machine is crucial to ensure its longevity and consistent performance. Here are some maintenance and safety tips to follow:
Regular Maintenance
Schedule regular maintenance checks to inspect and lubricate moving parts, tighten screws and bolts, and address any signs of wear or damage promptly. Keeping the machine in top condition reduces downtime and enhances productivity.
Safety Precautions
Train operators on proper machine operation and safety protocols. Ensure they wear appropriate personal protective equipment (PPE) and follow safety guidelines while working with the machine.
Future Trends in Roll Forming Technology
As technology continues to advance, the roll forming industry is expected to undergo significant developments. Here are some future trends to watch out for:
Automation and Robotics
The integration of automation and robotics into roof wall panel roll forming machines will further enhance production efficiency and reduce human intervention. Automated processes will lead to faster production cycles and higher precision.
Advanced Materials and Coatings
Advancements in material science will introduce new lightweight and durable materials for roll forming applications. Additionally, innovative coatings will enhance the panels’ performance in terms of corrosion resistance and aesthetics.
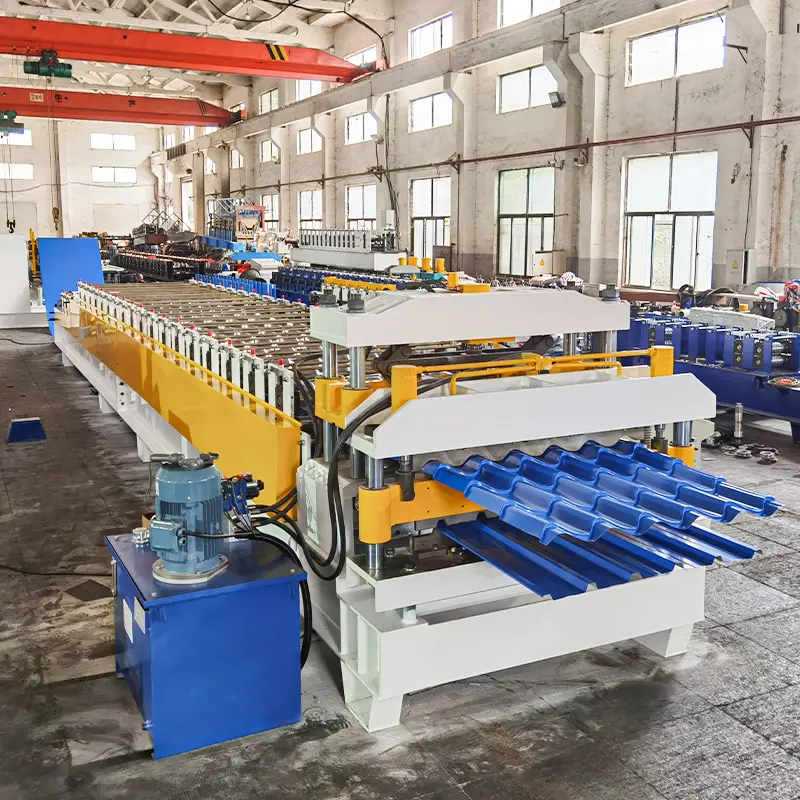
निष्कर्ष
The roof wall panel roll forming machine has revolutionized the construction industry by providing an efficient, cost-effective, and customizable solution for producing roof panels and wall cladding elements. Its applications span across various industries, including construction, automotive, appliances, and furniture. By understanding the different types of roll forming machines and considering essential factors in their selection and maintenance, manufacturers can ensure a seamless and productive production process.
As the roll forming technology continues to evolve, we can anticipate even more advancements, including increased automation and the adoption of new materials and coatings. Embracing these future trends will further elevate the capabilities and potential of roof wall panel roll forming machines in the coming years.
FAQs
1. Are roof wall panel roll forming machines suitable for small-scale manufacturing?
Yes, roof wall panel roll forming machines come in various sizes and configurations, making them suitable for both small-scale and large-scale manufacturing. Manufacturers can choose a machine that aligns with their production requirements.
2. Can roof wall panel roll forming machines work with non-metallic materials?
While roof wall panel roll forming machines are primarily designed for metal materials like steel and aluminum, there are specialized machines available for roll forming non-metallic materials like PVC and polycarbonate.
3. What are the typical maintenance intervals for a roof wall panel roll forming machine?
Maintenance intervals can vary based on the machine’s usage and operating conditions. However, a general rule of thumb is to perform regular maintenance checks every three to six months.
4. Can roof wall panel roll forming machines produce custom-designed panels?
Yes, one of the key advantages of roof wall panel roll forming machines is their ability to create custom-designed panels. Manufacturers can adjust the machine’s settings and tooling to produce panels with specific dimensions and profiles.
5. How does the roll forming process compare to other manufacturing methods?
The roll forming process offers several advantages over traditional manufacturing methods, such as stamping or press braking. It provides higher precision, faster production cycles, and better material utilization, resulting in cost-effective and consistent production.