Common issues and solutions for C channel roll forming machines are a critical aspect of maintaining the efficiency and effectiveness of these machines. Despite their many benefits, C channel roll forming machines can encounter issues that can slow down production or compromise the quality of the finished product. Identifying these issues and finding solutions is crucial to ensuring optimal machine performance and preventing costly downtime.
In this article, we will explore some of the most common issues that can arise when using C channel roll forming machines and provide practical solutions to address them. By understanding these issues and implementing appropriate solutions, businesses can reduce the risk of production delays, minimize waste, and optimize the performance of their C channel roll forming machines.
Common issues of C Channel Roll Forming Machines
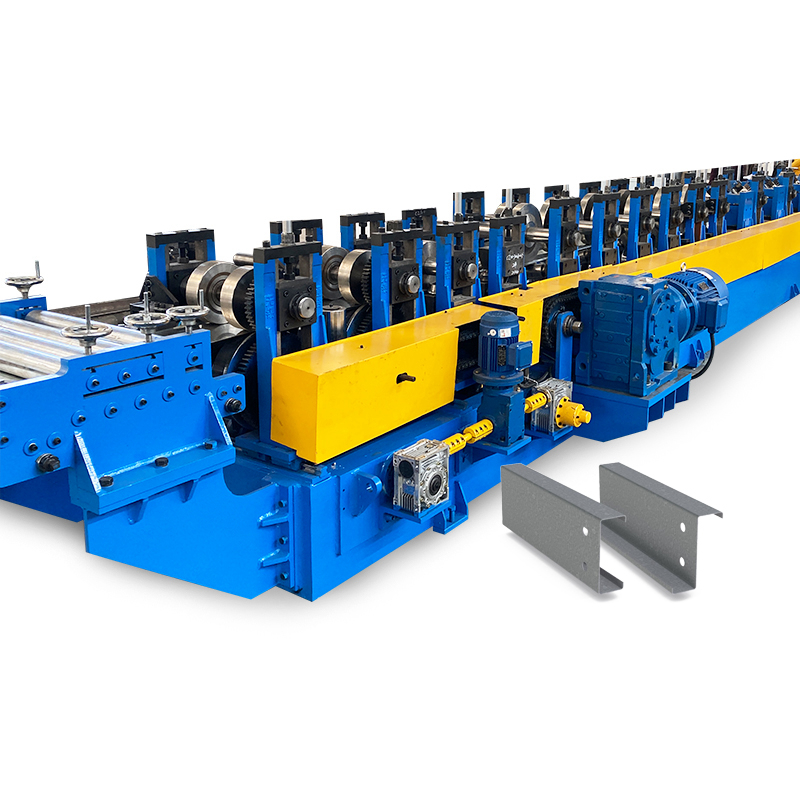
There are several common issues that can arise when using C channel roll forming machines, including:
- Material slippage: Material slippage can occur when the material being formed is not held securely in place during the forming process. This can result in uneven edges, incorrect dimensions, and wasted materials. The primary cause of material slippage is incorrect material handling or inadequate lubrication.
- Uneven edges: Uneven edges can occur when the material is not fed into the machine evenly, or when the rollers are not aligned correctly. This can lead to C channels with inconsistent widths and thicknesses, compromising the quality of the finished product.
- Machine jams: Machine jams can occur when the material being formed gets stuck in the machine. This can cause damage to the machine and result in production delays. Jams can be caused by several factors, including incorrect material handling, inadequate lubrication, or worn parts.
- Inaccurate dimensions: Inaccurate dimensions can occur when the machine is not set up correctly or when the material is not fed into the machine properly. This can result in C channels that are too short, too long, or have the wrong dimensions altogether.
These issues can have a significant impact on the production process, resulting in wasted materials, increased downtime, and decreased product quality. It is essential to identify the cause of each issue and implement appropriate solutions to prevent them from recurring in the future. In the next section, we will explore some solutions to these common issues.
Causes and solutions of C Channel Roll Forming Machines
Here are some potential causes and solutions for the common issues that can arise when using C channel roll forming machines:
- Material slippage: Material slippage can be caused by incorrect material handling or inadequate lubrication. To address this issue, businesses can implement better material handling processes, such as ensuring the material is held securely in place during the forming process. Additionally, businesses can increase the amount of lubricant used to reduce friction and prevent slippage.
- Uneven edges: Uneven edges can be caused by several factors, including incorrect material feeding and roller misalignment. To address this issue, businesses can ensure that the material is fed into the machine evenly and that the rollers are aligned correctly. Additionally, inspecting the machine regularly and replacing worn parts can prevent this issue from occurring.
- Machine jams: Machine jams can be caused by various factors, including incorrect material handling, inadequate lubrication, or worn parts. To address this issue, businesses can implement better material handling processes, increase the amount of lubricant used, and inspect the machine regularly to identify worn parts and replace them before they cause a jam.
- Inaccurate dimensions: Inaccurate dimensions can be caused by incorrect machine settings or incorrect material feeding. To address this issue, businesses can ensure that the machine is set up correctly, and that the material is fed into the machine correctly. Regular machine maintenance and inspection can also prevent this issue from occurring.
By identifying the causes of these common issues and implementing appropriate solutions, businesses can optimize the performance of their C channel roll forming machines and prevent costly production delays and waste. Regular machine maintenance, inspection, and employee training can also help businesses identify potential issues before they occur and prevent them from affecting the production process.
Maintenance of C channel roll forming machines
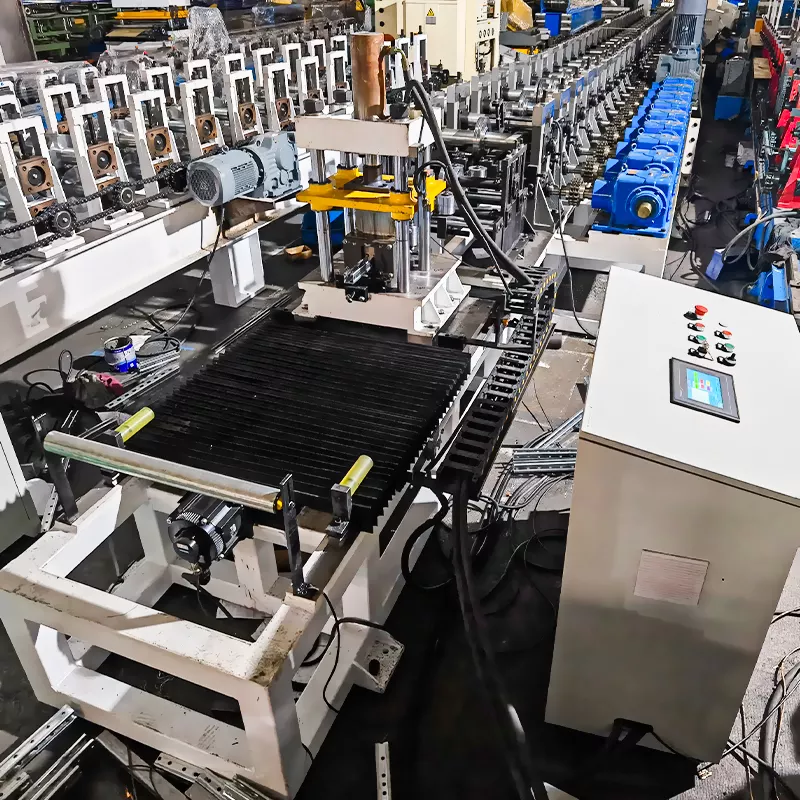
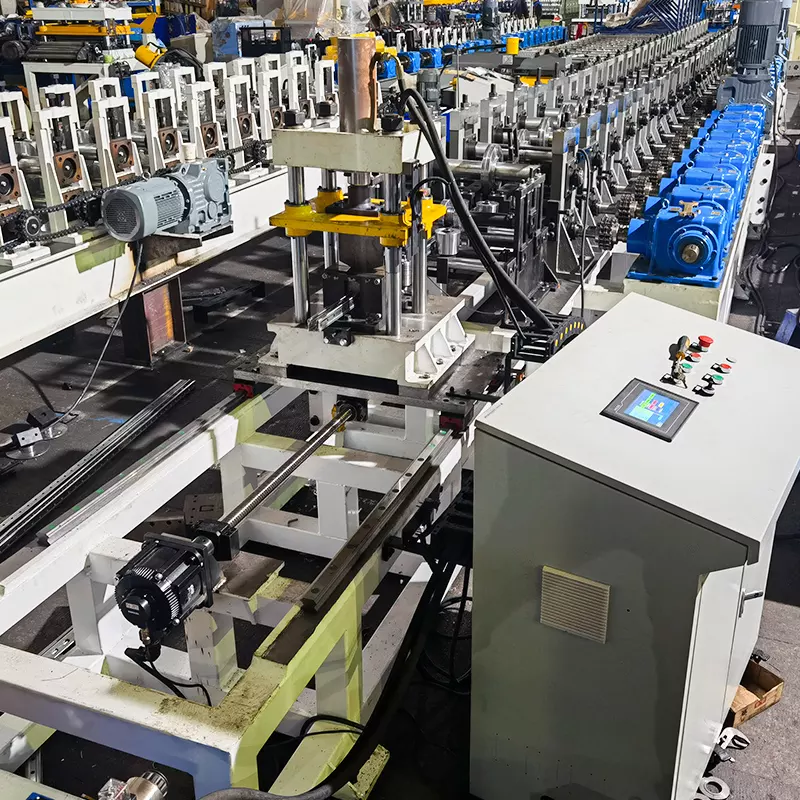
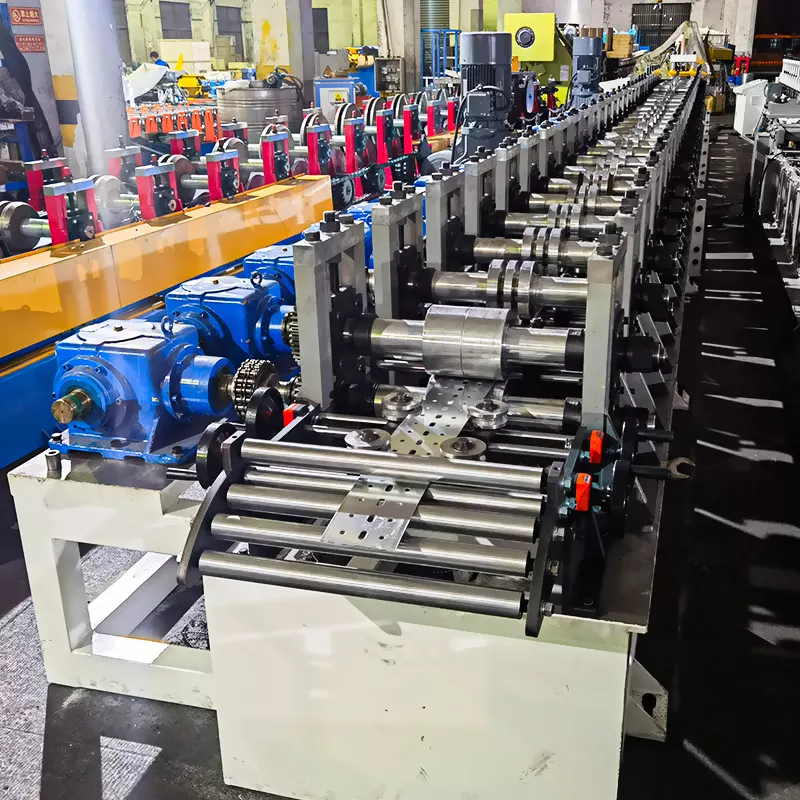
Regular maintenance is crucial in preventing common issues with C channel roll forming machines. Neglecting maintenance can lead to decreased machine performance, production delays, and increased downtime. Here are some tips for maintaining C channel roll forming machines:
- Check and replace worn parts: Over time, parts of the machine can wear out, leading to decreased performance and increased downtime. Regularly inspecting the machine and replacing worn parts can prevent this from happening. Additionally, using high-quality replacement parts can increase the lifespan of the machine and prevent issues from arising.
- Ensure proper alignment: Proper alignment is critical in ensuring that the machine produces high-quality C channels. Misaligned rollers can cause material slippage and uneven edges, compromising the quality of the finished product. Regularly checking and adjusting the alignment of the rollers can prevent this issue from occurring.
- Clean the machine regularly: Dust, debris, and other contaminants can accumulate on the machine, leading to decreased performance and increased downtime. Regularly cleaning the machine, including the rollers and other components, can prevent this from happening. Additionally, using appropriate lubricants can prevent contaminants from sticking to the machine and reduce the need for cleaning.
- Implement a preventative maintenance schedule: Establishing a preventative maintenance schedule can help businesses identify potential issues before they occur and prevent costly downtime. This can include regular inspections, lubrication, and replacing worn parts before they fail.
By implementing these maintenance tips, businesses can ensure the optimal performance of their C channel roll forming machines and prevent common issues from arising. Additionally, regular maintenance can increase the lifespan of the machine and reduce the need for costly repairs or replacement.
Quality control of C channel roll forming machines
Quality control is essential in preventing common issues with C channel roll forming machines. Implementing quality control strategies can help businesses identify issues early and prevent them from affecting the production process. Here are some strategies for implementing quality control:
- Conduct regular inspections: Regular inspections can help identify potential issues with the machine or the production process. This can include checking for worn parts, misaligned rollers, or other issues that can affect the quality of the finished product.
- Implement quality control checkpoints: Quality control checkpoints can be used to ensure that each C channel produced meets the required quality standards. This can include conducting inspections at various stages of the production process to identify issues before they become more significant.
- Use statistical process control: Statistical process control is a method for monitoring the production process and identifying any trends or patterns that may indicate potential issues. By analyzing data from the production process, businesses can identify issues before they become significant and take corrective action.
- Train employees: Training employees on quality control standards and procedures can help ensure that the production process meets the required quality standards. This can include training on how to identify potential issues and how to implement corrective action.
By implementing these quality control strategies, businesses can prevent common issues with C channel roll forming machines and ensure that each C channel produced meets the required quality standards. Additionally, these strategies can help businesses identify potential issues early and take corrective action, reducing the risk of production delays and waste.
C channel roll forming machines are essential tools in various industries, but they can encounter common issues that can compromise the quality of the finished product and increase downtime. To prevent these issues, businesses must identify their causes and implement appropriate solutions, such as better material handling processes, regular machine maintenance, and implementing quality control strategies. Regular inspections, statistical process control, and employee training are also crucial in ensuring optimal machine performance and preventing issues from arising. By implementing these strategies, businesses can ensure the efficient and effective production of high-quality C channels.