Introduction to Light Keel Roll Forming Machines
Roll forming is a metal working process where sheet metal is progressively bent until the desired cross-sectional profile is obtained. A light keel roll forming machine is designed specifically for roll forming light keel and small shaped steel. Compared to heavy keel and large structural roll forming machines, light keel roll forming machines are more compact in size and have relatively lower roll forming power.
Light keel generally refers to keels or beams with web height under 180 mm. The web thickness is typically between 1.5 mm to 3 mm. Light keel roll forming machine is ideal for forming such light gauge keels and small structural parts.
What is Light Keel?
Light keel is a type of metallic structural beam that has a C-shaped or U-shaped cross section. It consists of two flanges connected by a thin web. Light keels are used extensively in light steel construction in walls, floors, and roofs to provide support and stiffness.
The flange width of light keel is typically less than 80 mm. The web height or depth ranges from 50 mm to 180 mm for a light keel member. The material thickness is light gauge, usually between 1.5 mm to 3 mm. Popular materials used for light keel production include galvanized steel, cold rolled steel, and stainless steel.
Light keels are lighter in weight than traditional hot rolled I-beams. But the efficient cross-sectional shape and high strength-to-weight ratio of light keels allow them to span greater distances and carry reasonable load. Light keel members are easy to transport and require less structural support.
Advantages of Light Keels
Here are some of the main advantages and uses of light keel steel members:
- Lightweight construction – Light keels weigh less than I-beams, enabling light steel construction.
- Higher strength-to-weight ratio – Excellent strength despite low weight due to optimized cross-section.
- Easy transportation and handling – Can be moved manually due to light weight.
- Reduced structural support – Requires less heavy structural members due to light self-weight.
- Span longer distances – Ability to span longer spans while supporting loads.
- Faster installation – Quick and easy installation due to lightweight.
- Roof purlins – Light keels are ideal for roof systems as purlins.
- Wall studs – Used as load bearing wall studs in light steel framing.
- Floor joists – Provides stiff floor construction when used as floor joists.
Working Principle of Light Keel Roll Forming Machine
Light keel roll forming utilizes a series of consecutive sets of rolls to gradually bend the sheet metal into the required cross-sectional shape of the keel. Each roller imparts incremental bending to the material as it passes through the different roller stations in sequence.
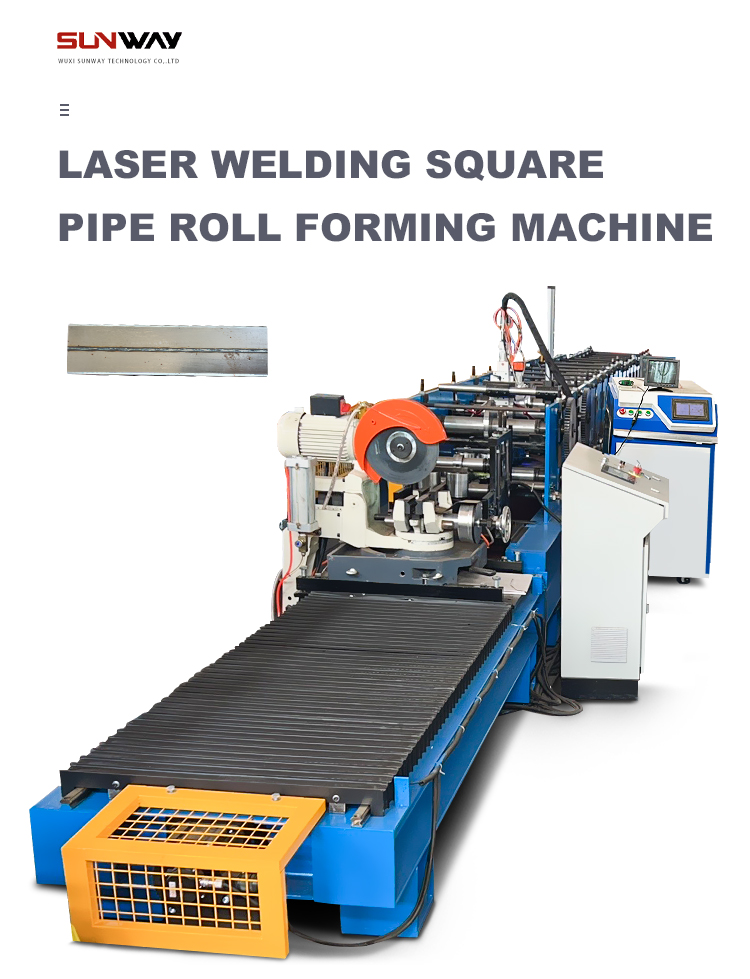
Roll Forming Process
The light keel roll forming process consists of three major steps:
- Feeding – Coiled sheet metal is placed on an uncoiler which feeds the strip of metal into the roll forming machine.
- रोल बनाना – The sheet passes through consecutive roller stations to gradually form the keel shape.
- Cutting – After achieving the profile, the continuously formed keel is cut into desired lengths by rotary shears.
The roll forming action involves two types of metal deformation – bending and flattening. The sheet metal is subjected to sequential bending and flattening as it passes through different roller stations to eventually form the keel profile.
Roller Stations
The main working parts of the light keel machine are the roller stations. Each roller station consists of an upper roller and lower roller that are positioned closed to each other. The clearance between the rollers is kept just slightly more than the thickness of the metal sheet.
As the strip passes between the rotating upper and lower roller pair, it gets gradually bent. By passing through multiple such roller stations in sequence, the complete keel profile is incrementally formed step-by-step.
The rollers have machined grooves or contours in their circumference to bend the sheet to the desired shape. The rollers must be machined precisely to high tolerance and hardness to withstand the metal forming forces.
Components of Light Keel Roll Forming Machine
Light keel roll forming machine consists of several modular components and sections that work together to continuously form the desired light keel sections.
Feeding Section
This is the starting section where the sheet coil is mounted on an uncoiler and gradually released into the roll forming section. It consists of:
- डेकोइलर – Holds the sheet coil and rotates to unroll the sheet. Braking is provided to prevent overrunning.
- Feeding rolls – Pulls the sheet strip from the decoiler and feeds into the roll forming section.
- Straightening rolls – Removes coil curvature and straightens the sheet before roll forming.
Forming Section
This section has the roller stations that gradually form the web and flanges of the keel profile. The main components are:
- Forming rollers – Different contour rollers that bend the sheet in stages to create the keel shape.
- Forming shafts – Housings that hold the forming rollers at precise positions.
- Guide rolls – Rolls that maintain sheet alignment during bending.
- Support roll stands – Structural frames to mount the roller stations.
Cutting Section
Once the desired keel profile is achieved by the forming section, the continuously formed keel is cut into lengths as per requirement in the cutting section. It has:
- Rotary shears – Cuts the formed keels into pieces by a rotating blade.
- Length measuring system – Measures the linear length of the formed keel and triggers the shears.
- Discharge tables – Roller tables to collect the cut keel pieces.
नियंत्रण प्रणाली
Sophisticated automation and control equipment to synchronize and operate the machine includes:
- PLC – Controls all machine operation sequences through automation programs.
- HMI – Human Machine Interface with a display to view and control settings.
- Servo motors – Provide precise positioning of forming rollers.
- Sensors – Various sensors to detect and monitor sheet position.
- Safety modules – Emergency stops, safety guards for operator protection.
Structural Frame and Housing
The roll forming machinery is housed in a rugged structural frame built from structural steel sections like channels, I-beams, square tubes etc. Logical machine layout and ergonomic positioning of components allows easy operation and maintenance access.
Housings and enclosures are used to enclose the working parts for safety. Guards prevent contact with moving parts. Openings are provided for entry, exit and observation of the sheet metal.
For a light keel roll former, a C-type frame design is commonly adopted. This consists of two side frames connected by horizontal frame sections. The roll forming machinery is laid out within this rigid C-frame structure. Sheet metal guards on the sides and top cover the machine.
Technical Specifications
Light keel roll forming machines are available in a range of sizes and production speeds to produce small to mid-size keels and open beams. Here are some typical specifications of these machines:
- Metal thickness capacity: 0.5 mm to 3 mm
- Keel web height: 50 mm to 180 mm
- Flange width: Up to 80 mm
- Forming speed: 8 to 15 m/min
- Drive power: 3 kW to 7.5 kW
- Production rates vary from 10 to 30 pieces per minute depending on the keel size. The machine size is relatively compact compared to larger roll formers. Weight ranges from 3000 Kg to 8000 Kg based on capacity.
How to Choose a Light Keel Roll Forming Machine
Here are some important factors to consider when selecting a light keel roll forming machine:
- Keel sizes – Dimensions like web height, flange width, thickness should be within machine capacity.
- Production volume – Match the machine speed and output rate to your required production.
- Power type – Electric or hydraulic power based on production rate.
- Level of automation – Manual to fully automatic models are available.
- Coil parameters – Coil ID, outer diameter, weight should fit the decoiler.
- Roller materials – Special steels for heavy duty or stainless steel applications.
- Machine rigidity – Heavier frames for reduced vibration and better profile quality.
- Expandability – Ability to add more roller stations or modifying tooling for more profiles.
- Software controls – Ease of programming PLC for flexibility.
- Safety – Integrated safety as per mandatory industrial norms.
- Service – Installation, commissioning, operator training should be provided.
- Budget – Higher production machines typically cost more.
Consider present and future production requirements and choose the appropriate light keel roll former model.
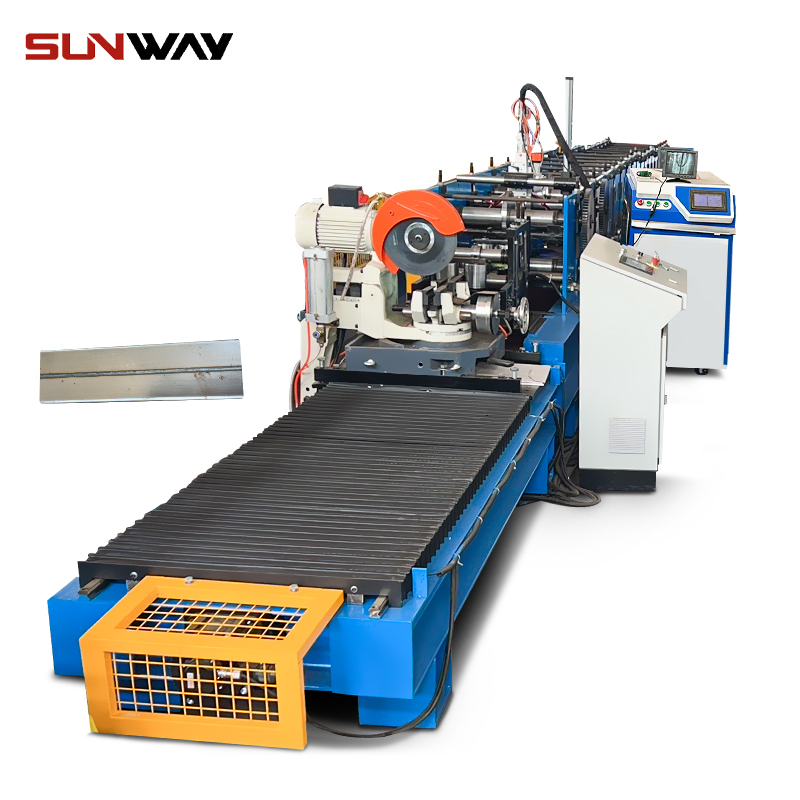
Manufacturers of Light Keel Roll Forming Machines
Some leading manufacturers of light keel roll forming machines are:
- ZITAI (China)
- Formtek (Taiwan)
- Fundametal (Taiwan)
- Samco Machinery (Taiwan)
- Joton Rollforming (Taiwan)
- Metform (Turkey)
- CNCRollforming (China)
- Gasparini (Italy)
- DREISTERN (Germany)
Many Chinese manufacturers also offer light keel roll formers at economical prices. Choose a reputable manufacturer and evaluate machine quality, capabilities and service support.
Price Range
Light keel roll forming machines are available in a wide price range depending on the production capacity, level of automation and optional features. Here is a rough price estimate:
- Entry-level – $8,000 to $15,000
- Medium-capacity – $15,000 to $35,000
- High-production – $35,000 to $65,000
- Heavy-duty – Above $65,000
Bigger machines with faster production rates and more automation typically cost more. Imported European or Taiwan made machines are costlier but offer better quality and performance.
How to Operate a Light Keel Roll Forming Machine
Operating a light keel roll forming machine requires basic technical skill. Proper training must be provided by the machine manufacturer. Here is a summary of the main steps:
1. Safety Checks
- Ensure all guards are in place
- Confirm emergency stops are working
- Check electrical and hydraulic systems
- Use safety shoes, helmets, glasses
2. Material Loading
- Mount sheet coil on decoiler using overhead crane
- Feed sheet into rollers and align
3. Set up Parameters
- Enter material thickness, keel height, etc.
- Set forming speed, cut length, other settings
4. Initiate Operation
- Start motors and allow machine to reach speed
- Gradually feed sheet into forming section
5. Finished Product
- Quality check formed keels visually
- Offload finished pieces using lift truck
6. Regular Maintenance
- Lubricate bearings, inspect components
- Change wear items like shear blades
The machine operator must monitor the process and make any necessary adjustments to ensure proper keel profile and quality. Modern light keel roll forming machines are designed for quick set up and easy operation.
Advantages and Disadvantages
Advantages
- High productivity and faster production rates.
- Consistent and uniform profile quality.
- Capability to form complex and asymmetric shapes.
- Low tooling cost compared to other processes.
- Flexible adjusting parameters through controls.
- Greater dimensional accuracy of products.
- Minimal material wastage and scrap.
Disadvantages
- High initial machine investment cost.
- Regular maintenance and skilled labor required.
- Setting up tooling and changeovers take time.
- Limited size range for a given machine.
- Noise and safety issues require precautions.
Light Keel Roll Forming Machine Maintenance
Regular preventive maintenance is essential for trouble-free operation and longevity of the roll forming machine. Here are some important maintenance aspects:
- Clean the machine daily and inspect for oil leaks.
- Lubricate all bearings and sliding surfaces regularly.
- Check alignment and clearances of rollers. Adjust if needed.
- Examine all electrical connections and hydraulic hoses.
- Confirm all safety devices are functioning properly.
- Check chain and belt drives for proper tension.
- Replace worn out components like blades, sprockets, guards etc.
- Keep roller shafts clean and grease thread screws.
- Examine machine frame for any cracks or loose joints.
- Verify that all warning labels and signs are legible. Replace if needed.
Proper maintenance according to supplier’s guidelines will minimize unplanned downtime and help achieve maximum productivity.
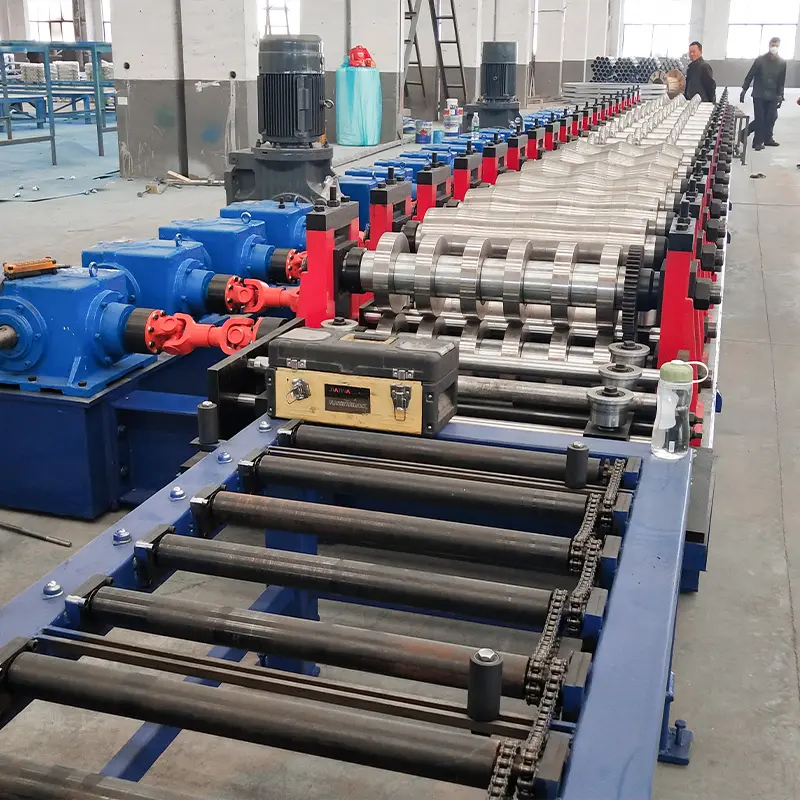
Troubleshooting Common Problems
Some common issues that may occur with light keel roll forming machines are:
Problem – Metal sheet jamming and clogging
Solution – Check alignment of rolls, reduce feeding speed, ensure adequate lubrication
Problem – Excessive flange or web deformation
Solution – Adjust roll gaps, check roller contours and spacing
Problem – Sheared parts have burrs and are out of square
Solution – Replace worn shear blades, check blade gaps, reduce cutting speed
Problem – Keel profile distortion
Solution – Improve material surface finish, check alignment of guiding rolls
Problem – Motor overload tripping
Solution – Check if metal thickness exceeds capacity, inspect gearbox and chain condition
Problem – Hydraulic power unit overheating
Solution – Check oil level, clean oil filters, inspect pump and valves
Safety Tips
Some important safety tips when operating light keel roll forming machines:
- Keep hands away from roller areas during operation.
- Do not make any adjustments until machine has fully stopped.
- Wear cut resistant gloves when handling sheet metal.
- Use proper lifting methods for transporting coils and finished products.
- Ensure sufficient lighting in the work area.
- Keep the area clean and dry to avoid slipping/tripping hazards.
- Turn machine OFF and follow lockout procedures before maintenance.
- Make sure all safety guards are in place during operation.
- Use ear protection as the noise levels can be high.
- Follow standard industry protocols and safety procedures.
सामान्य प्रश्न
Q: What materials can be roll formed into light keels?
A: Commonly used materials are low carbon steel, galvanized steel, and stainless steel sheets with thickness up to 3 mm. Aluminum alloys can also be roll formed.
Q: What is the difference between light keel and normal keel profiles?
A: Light keels have a web height of less than 180 mm and thickness up to 3 mm. Normal keels are larger in cross-section and thicker.
Q: What length of keels can be produced?
A: Common lengths range from 2 m to 12 m. Custom or infinite lengths can also be produced.
Q: How to design the roller contours for a new keel profile?
A: Roller contours are designed by analysis of the bending sequence and stages required to gradually form the keel shape. Engineering software can aid the design.
Q: Is heat treatment required after roll forming keels?
A: No, the cold roll forming process work hardens and strengthens the formed keels. Post heat treatment is typically not required.
Q: What is the production rate of light keel roll forming machines?
A: Production rate depends on keel size, metal thickness, and machine speed. Typical output is 10 to 30 pieces per minute.
Q: How should I maintain the roll tooling?
A: Keep the rollers clean by removing metal dust and particles. Lubricate the bearings. Resurface or hard chrome eroded segments.
Q: Is automated keel packing available?
A: Yes, some machines integrate conveying and stacking units to automatically stack the finished keel pieces.
निष्कर्ष
Light keel roll forming is an efficient process to mass produce small to medium sized keels and beams with a C or U shaped profile. The roll forming machine gradually forms the web and flanges by passing the sheet strip through a series of roller stations.
Compared to heavy steel structural profiles, light keels up to 180 mm height and 3 mm thickness can be efficiently mass produced using light keel roll forming machines. These compact and versatile machines enable small to mid-size metal building product manufacturers to automate production.
Careful selection of the appropriate machine capacity, features and options is necessary based on current and future production needs and budget. Leading Taiwanese and European manufacturers offer high quality light keel roll forming machines. With proper operation and maintenance, the roll forming machine can deliver consistent quality and low cost production.