When it comes to construction and industrial projects, galvanized steel panels are often the unsung heroes. Their strength, durability, and corrosion resistance make them indispensable for various applications, from roofing and siding to structural components in buildings and infrastructure. In this article, we’ll take a deep dive into galvanized steel panels, discussing everything from their types and working process to their applications and how to choose the right supplier.
Overview
Galvanized steel panels are coated with a layer of zinc to protect them from rust and corrosion. The galvanization process significantly extends the life of the steel, making it more durable for outdoor and harsh environments. Whether you’re working on a small DIY project or a large commercial build, galvanized steel offers a high-performance material at a relatively low cost. But what exactly makes galvanized steel so versatile?
It all boils down to the zinc coating. This coating acts as a sacrificial layer, meaning it will corrode first before the steel underneath does. In essence, it buys you time and saves you money on repairs and replacements, which is why it’s so popular in construction, especially for roofing, walls, and industrial applications. Let’s dive deeper into what makes galvanized steel panels tick and how they can fit into your next project.
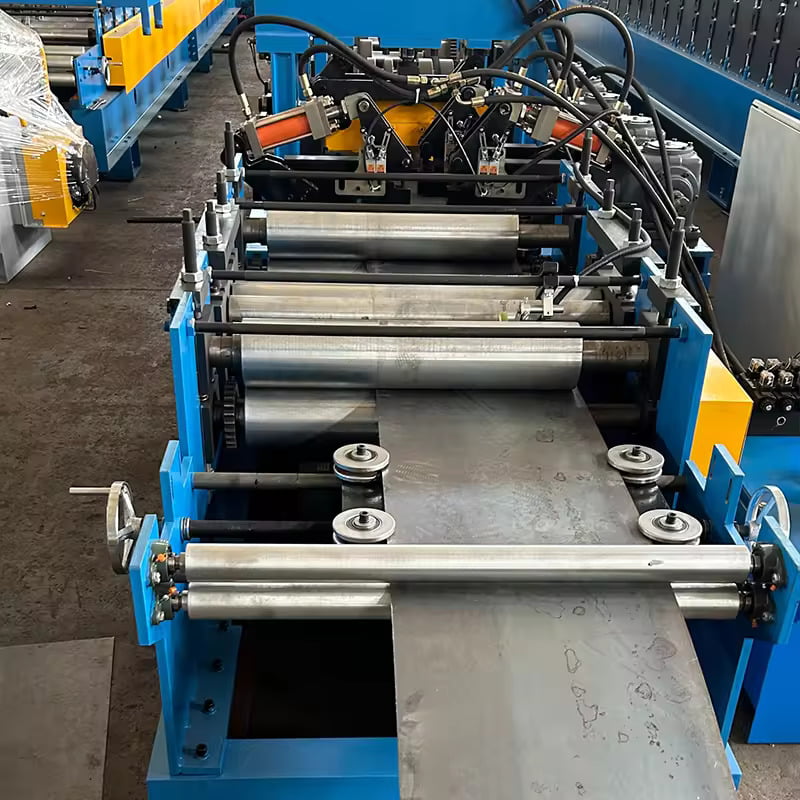
Corrugated Iron Sheets Guide
Before we delve into the intricacies of galvanized steel, it’s worth mentioning corrugated iron sheets. These sheets, often confused with galvanized steel, are made using similar processes but are typically used for different purposes. Corrugated sheets are made from a variety of metals, including steel and aluminum, and have distinct wave-like patterns, which enhance their strength-to-weight ratio.
When comparing corrugated iron sheets to galvanized steel panels, corrugated options are commonly used in roofing due to their lightweight nature. Meanwhile, galvanized panels are used in structural applications where greater durability is required. The key takeaway? Both materials offer durability, but corrugated sheets are better suited for lightweight, less load-bearing applications, while galvanized steel excels in heavy-duty environments.
Types of Galvanized Steel Panels
Choosing the right type of galvanized steel panel for your project can be tricky due to the wide range of options. Below is a detailed breakdown of some of the most common types, categorized by their coating, thickness, and intended application.
Type of Galvanized Steel Panel | Description | Coating Thickness (in µm) | आवेदन |
---|---|---|---|
G90 Galvanized Steel | Standard coating used for heavy-duty projects | 20-30 µm | Roofing, siding, outdoor structures |
G60 Galvanized Steel | Moderate coating suitable for less aggressive environments | 15-25 µm | Residential construction, HVAC |
G40 Galvanized Steel | Light coating, primarily for indoor use | 8-15 µm | Indoor framing, light structures |
Pre-painted Galvanized Steel | Galvanized steel with an additional color coating | 10-30 µm (zinc) + Paint | Decorative facades, custom signage |
Galvalume Steel | Combines zinc and aluminum coating for increased corrosion resistance | 15-30 µm | Coastal and industrial environments |
Aluzinc Steel | Zinc and aluminum alloy coating | 25-35 µm | Extreme weather conditions |
Hot-Dip Galvanized Steel | Submerged in molten zinc for a thicker coating | 40-60 µm | Bridges, pipelines, industrial equipment |
Electro-Galvanized Steel | Uses electrical current to apply zinc coating | 5-10 µm | Automotive parts, indoor applications |
Cold-Rolled Galvanized Steel | Steel is cold-rolled before galvanization for additional strength | 20-40 µm | High-strength structural applications |
Zinc-Iron Alloy Coated Steel | Added iron in the coating for increased hardness | 15-20 µm | Heavy-duty industrial equipment |
Each type has its pros and cons, so it’s essential to consider factors like the environment (coastal vs inland), application (structural vs decorative), and desired lifespan when choosing the best one for your project.
How Galvanized Steel Panels Are Made
The process of creating galvanized steel panels is fascinating, blending both chemistry and physics to produce one of the most durable construction materials on the market. Here’s a step-by-step breakdown:
- Preparation of Steel: Raw steel is first cleaned to remove any impurities such as oil, dirt, or rust. This is typically done by bathing the steel in an acid solution, a process known as “pickling.”
- Fluxing: After cleaning, the steel is dipped into a flux solution. This helps the zinc to adhere to the steel more effectively during the galvanizing process.
- Galvanizing: The prepared steel is then dipped into molten zinc at around 450°C (840°F). The zinc forms a metallurgical bond with the steel, creating a protective layer.
- Cooling and Inspection: Once the zinc has coated the steel, the panels are cooled down and inspected for any imperfections or uneven coating.
- Passivation: Some galvanized steel panels undergo an additional passivation treatment, which further enhances corrosion resistance by creating a thin film on top of the zinc coating.
This process not only makes the steel resistant to corrosion but also adds a layer of physical protection, which is why galvanized steel is a top choice for demanding environments.
Key Components and Their Functions in Galvanized Steel Panels
Every component involved in the galvanization process plays a vital role in ensuring the steel’s durability and efficiency. Here’s a breakdown of the key components:
Component | Function |
---|---|
Zinc Coating | Provides corrosion protection by acting as a sacrificial layer |
Steel Core | Offers structural integrity and strength |
Flux Solution | Ensures that the zinc adheres evenly to the steel |
Passivation Layer | Adds additional corrosion resistance for high-exposure environments |
The effectiveness of galvanized steel comes down to how well these components interact. The zinc coating not only protects but also preserves the steel core underneath, making it a highly effective barrier against the elements.
-
Highway Guardrail End Terminal Forming Machine
-
Highway U/C Post Roll Forming Machine
-
2 Waves Highway Guardrail Roll Forming Machine
-
3 Waves Highway Guardrail Roll Forming Machine
-
वाइनयार्ड पोस्ट रोल बनाने की मशीन
-
ऑटो आकार बदलने योग्य सिग्मा शहतीर रोल बनाने की मशीन
-
सी सेक्शन ब्रेसिंग ओमेगा स्टोरेज रैक अपराइट पोस्ट रोल बनाने की मशीन
-
स्टील बॉक्स प्लेट रोल बनाने की मशीन बनाना
-
शेल्फ कॉलम के लिए बॉक्स बीम स्टील रोल बनाने की मशीन
Machine Speed and Efficiency in Galvanized Steel Production
The speed and efficiency of machinery involved in producing galvanized steel panels are crucial for both quality and cost-effectiveness. Here’s a look at typical machine speeds and how they affect production.
Machine Speed (in m/min) | Efficiency (%) | Production Application |
---|---|---|
100 m/min | 85% | High-volume production lines |
70 m/min | 90% | Moderate volume with focus on quality |
50 m/min | 95% | Precision applications requiring high-quality finishes |
30 m/min | 98% | Custom or specialized panel production |
The faster the machine speed, the more panels you can produce, but sometimes this comes at the cost of precision. Slower speeds tend to produce more consistent, higher-quality panels but at a higher cost.
Customizing Mechanical Parameters for Galvanized Steel Panels
Depending on your project, you may require customized mechanical parameters for your galvanized steel panels. This could involve tweaking thickness, strength, or other mechanical properties. Here’s a quick guide to what can be customized.
Parameter | Description | Adjustable Range |
---|---|---|
Panel Thickness | Thickness of the steel core | 0.2 mm – 2.5 mm |
Coating Thickness | Zinc layer thickness | 5 µm – 60 µm |
Tensile Strength | Steel strength | 250 MPa – 550 MPa |
Width | Panel width | 500 mm – 1500 mm |
Length | Panel length (custom cuts) | Variable |
Customizing these parameters allows you to get the exact specifications needed for your project, whether it’s for structural durability or aesthetic appeal.
Applications and Uses of Galvanized Steel Panels
One of the best things about galvanized steel panels is their versatility. They can be used in a wide range of applications, both indoors and outdoors, in commercial, residential, and industrial settings. Here are some of the most common uses:
आवेदन | विवरण |
---|---|
Roofing and Siding | Durable against weather conditions, ideal for residential and commercial buildings |
Bridges and Infrastructure | High corrosion resistance makes it perfect for outdoor structures like bridges |
Automotive Parts | Often used in car frames and body panels due to its rust-resistant properties |
Agricultural Buildings | Ideal for barns, silos, and other agricultural storage due to its durability |
Fencing | Galvanized steel fencing lasts longer than traditional wooden fences |
Industrial Equipment | Used in manufacturing machinery and equipment that operates in corrosive environments |
Each of these applications benefits from galvanized steel’s core strength and rust resistance, ensuring that structures last longer and require less maintenance over time.
Installation, Operation, and Maintenance of Galvanized Steel Panels
While galvanized steel panels are relatively easy to work with, proper installation, operation, and maintenance are essential to maximize their lifespan and performance. Here’s what you need to know:
Step | विवरण |
---|---|
Installation | Ensure that panels are properly aligned and secured to avoid stress points that could lead to cracks or warping. Use galvanized fasteners to prevent rust. |
Operation | Monitor for any early signs of corrosion, especially in high-moisture environments. |
Maintenance | Regularly inspect for any damages or rust spots, especially at cut edges or where panels meet other materials. Cleaning the surface periodically will prevent build-up of debris and moisture. |
Following these steps will ensure that your galvanized steel panels perform at their best, giving you years of durable service with minimal maintenance.
How to Choose the Right Supplier for Galvanized Steel Panels
Choosing a supplier for galvanized steel panels is critical to ensuring you get high-quality materials at a reasonable price. Here’s what to look for when selecting a supplier:
Factor | विवरण |
---|---|
Reputation | Look for suppliers with a track record of delivering quality products. Check reviews and ask for recommendations. |
Price Range | Compare prices from multiple suppliers. While cheaper may seem better, always consider the quality. Expect prices between $600 to $1,000 per ton, depending on the type. |
Customization Options | Choose a supplier that offers customization to meet the specific needs of your project. |
Certifications | Ensure the supplier is certified by industry standards like ASTM or ISO to guarantee the quality of the product. |
Partnering with the right supplier will not only ensure that you get the best materials for your project but also that you receive excellent customer service and support throughout the process.
Pros and Cons: Galvanized Steel Panels vs. Other Materials
Let’s compare galvanized steel panels against other common building materials like aluminum, wood, and stainless steel to see where they stand in terms of advantages and limitations.
Material | Advantages | Limitations |
---|---|---|
Galvanized Steel Panels | Highly durable, corrosion-resistant, cost-effective | Can rust at cut edges, heavier than alternatives |
Aluminum | Lightweight, corrosion-resistant | Less strong than steel, more expensive |
Wood | Aesthetic appeal, easily customizable | Susceptible to rot, requires frequent maintenance |
Stainless Steel | Extremely corrosion-resistant, strong | Expensive, heavy |
When durability and cost-effectiveness are your top priorities, galvanized steel is often the best choice. However, for projects where weight or appearance are more important, materials like aluminum or wood might be a better fit.
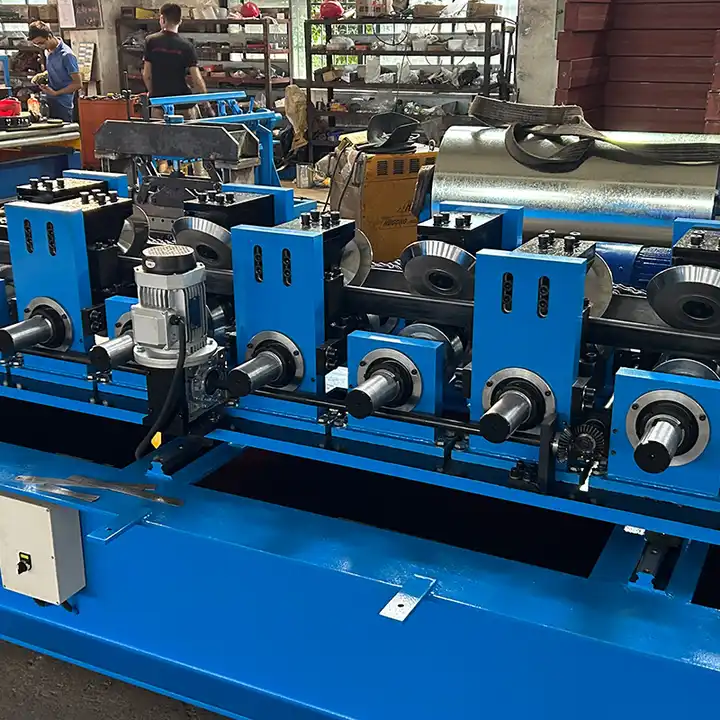
FAQs
Question | Answer |
---|---|
What is galvanized steel used for? | Galvanized steel is used in a variety of applications, including roofing, fencing, automotive parts, and bridges. Its rust-resistant properties make it ideal for outdoor and industrial environments. |
How long do galvanized steel panels last? | With proper maintenance, galvanized steel panels can last anywhere from 20 to 50 years, depending on the environment and the thickness of the zinc coating. |
Is galvanized steel better than stainless steel? | It depends on the application. Galvanized steel is more cost-effective and lighter, while stainless steel offers superior corrosion resistance and strength but at a higher cost. |
Can galvanized steel panels be painted? | Yes, galvanized steel can be painted, but it requires a special primer to ensure the paint adheres properly. Pre-painted options are also available. |
Are galvanized steel panels eco-friendly? | Yes, galvanized steel is recyclable, and the zinc coating reduces the need for frequent replacements, making it a more sustainable option over time. |
In conclusion, galvanized steel panels offer an excellent balance of strength, durability, and affordability, making them a top choice for a wide range of applications. Whether you’re building a new roof, reinforcing a bridge, or fabricating industrial equipment, the right type of galvanized steel can make all the difference.