Roll forming is a metal working process used to bend a long strip of sheet metal into custom profiles. A रोल बनाने की मशीन progressively forms the desired cross-section profile by passing the strip through a series of roll stations. Each roll station performs an incremental bending operation, gradually shaping the profile.
One common profile produced by roll forming is the C profile, which has a C-shaped cross section. C profiles, also known as C channels or C beams, are used extensively in the construction industry for purlins, girts, wall studs, roof trusses, and other structural framing members. They are valued for their optimal strength-to-weight ratio.
C profile roll forming machines have a unique arrangement of roll stations specifically designed to form the C shape. This article will examine the key functions and mechanisms of a C profile roll former.
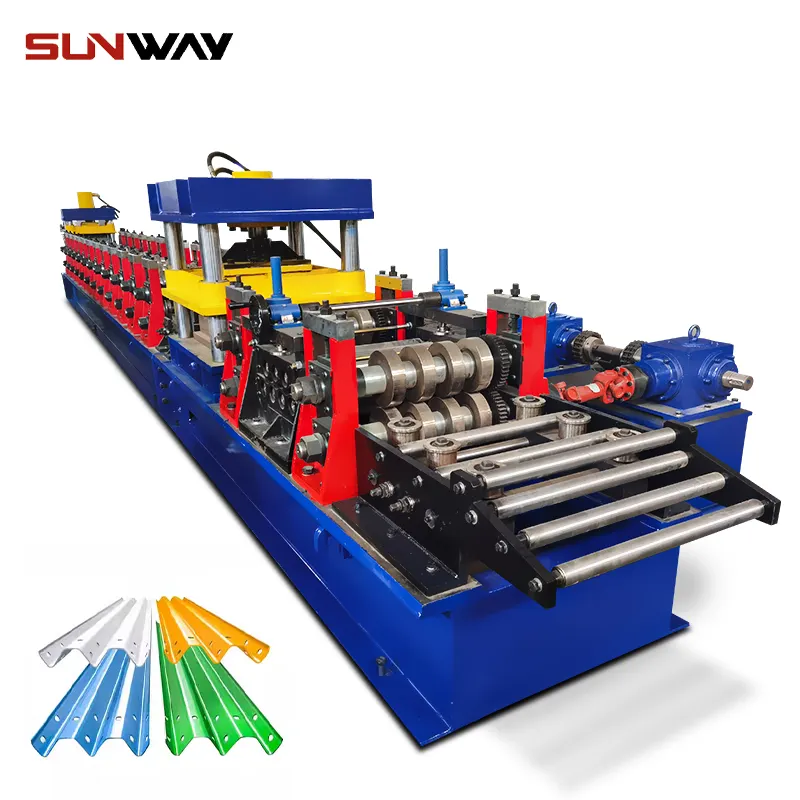
Overview of C Profile Roll Forming Process
Roll forming C profiles involves gradually bending the flat strip stock into the C-shape using a series of forming stands. Each stand has three rolls – two opposing horizontal rolls and one vertical roll positioned above.
The stock is fed through the roll former horizontally. As it passes each stand, the horizontal rolls induce curvature into the flanges while the vertical roll shapes the web. With each progressive stand, more bending occurs until the complete C profile is achieved.
Some key mechanisms in a C profile roll former include:
- Feeding – Feeds the strip stock into the roll former at a controlled speed
- Forming rolls – Progressively bend the material through precision contours
- Support rollers – Provide support and resist deflection between stands
- Shearing – Cuts profiles to length after roll forming
Now let’s look at the core functions within a C profile roll forming system.
Key Functions of a C Profile Roll Former
1. Strip Feeding
The feeding mechanism pulls the flat strip stock into the roll former at a fixed speed synchronized with the forming stands. Consistent material feed is critical for quality production.
Most C profile roll forming machines use a pinch roller feed. This consists of two motor-driven rollers that grip the strip stock and advance it forward into the forming section.
The feed rollers need adjustable pressure to accommodate various material thicknesses. They may also incorporate servo motors for precision speed control.
Some key requirements of the feeding system:
- Ability to handle a range of strip widths and thicknesses
- Consistent feeding speed without slippage or markng
- Easy width adjustment for rapid material changeovers
- Protection against backward pull from forming stands
2. Profile Forming
The heart of the roll former are the forming stands that incrementally shape the C profile. Each stand consists of two horizontal rolls and one vertical roll.
The top and bottom rolls bend the flanges while the middle roll forms the web. The rolls have precision machined contours that control the material bending.
The number of stands can vary based on the profile size and material thickness – typically 10 to 16 stands for a C channel. More stands allow for greater control over the material deformation.
Important aspects of the forming section:
- Roll contours engineered for desired profile geometry
- Sufficient forming stations for gradual bending
- Rolls specially surfaced for low friction and mark-free forming
- Quick roll change design for profile variations
- Stand adjustment for rapid size changeovers
3. Strip Support and Guiding
As the strip stock passes through the forming stands, it can tend to deflect sideways or twist. This can lead to distortion in the final profile shape.
To counteract this, support rollers are positioned between the stands. These rollers make light contact underneath the profile to provide continual support as it forms.
Another function is strip guiding to keep the material centered as it progresses through the machine. Guide rollers located along the sides maintain the strip position and prevent meandering.
Key features for support and guiding:
- Strategic support roller placement for maximum backing
- Height adjustment on support rolls for various profiles
- Quality guide rollers to minimize friction and scratches
- Quick set-up of support and guides for new profiles
4. Profile Cutoff
The final step is cutting the continuously formed profile into set lengths. A cutoff press with rotating shear blades slices through the profile at predetermined points.
For accurate cuts, the shear blades must be properly timed with the line speed. Precise cutoff controls are essential for mass production of C profiles.
Some key factors for the cutoff mechanism:
- Sharp shear blades for clean, burr-free cuts
- Synchronized with feed speed for correct cut lengths
- Programmable for variable profile lengths
- Scrap removal and stacking
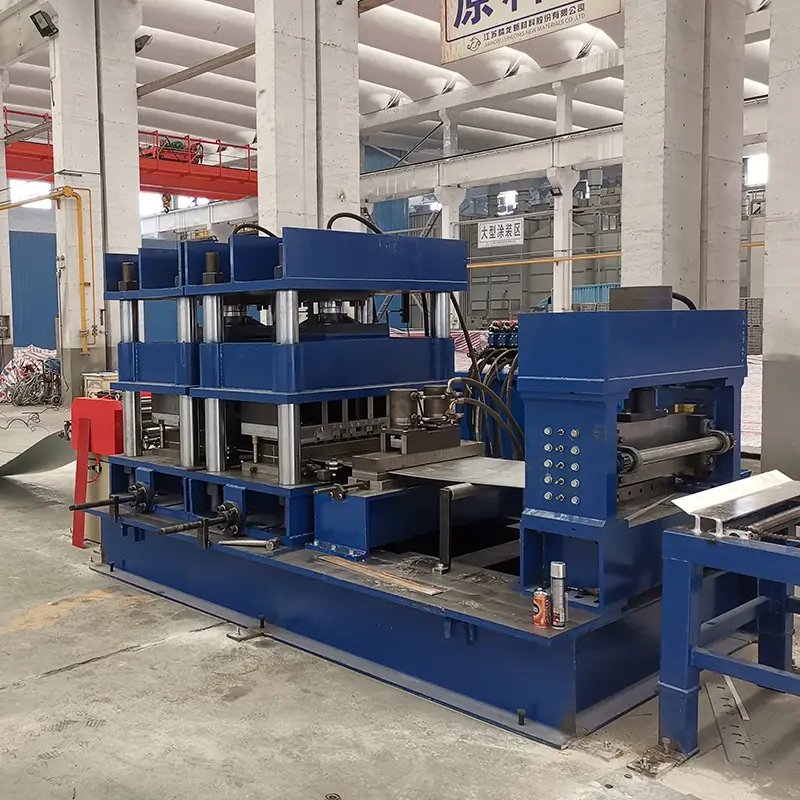
Additional Functions
Beyond the core roll forming and cutoff functions, C profile roll forming machines can incorporate additional processes:
- Decoiling – Unwinds strip coil stock and feeds into roll former
- Pre-punching – Punches holes prior to roll forming
- Heat treating – Special stands for in-line heat treatment
- Cambering – Creates arched profile for roofs and curved walls
- Hot dipped galvanizing – Applies protective zinc coating
Typical Specifications
C profile roll forming machine technical specifications can include:
- Profile width – 50 to 300 mm range
- Material thickness – 0.5 to 3 mm steel and aluminum
- Roll forming speed – 10 to 40 m/min
- Drive type – Electric, hydraulic, or servo motor
- Cut length – Programmable up to 10 m
- Installed power – 15 to 50 kW
Machines may be fully automated with controls like a PLC, HMI, and servo drives. Robust machine frames prevent deformation under high rolling forces.
Safety is also important – machines have interlocked guards, E-stops, and overload protection.
Applications of C Profile Roll Forming
Thanks to their optimal strength, C profiles produced by these machines have become prevalent in metal building construction:
- Purlins – Horizontal roof supports
- Girts – Vertical wall supports
- Studs – Vertical framing members
- Truss chords – Upper and lower parts of a truss
- Joists – Horizontal floor supports
- Rafters – Angled roof supports
- Soffits – Horizontal underside of overhangs
C profiles are also used for shelving, racking, conveyors, platforms, trailer sides, and more.
Benefits of C Profile Roll Forming
Compared to other C profile manufacturing methods, roll forming offers significant advantages:
- High speeds – Up to 10x faster than extrusion
- Lower cost – Reduced material waste versus bending or press braking
- Flexibility – Fast changeovers between sizes and profiles
- Strength – Cold working improves material properties
- Quality – Consistent dimension and finish
- Automation – Can be integrated into automated production
Thanks to these benefits, roll formed C profiles are ideal for cost-effective, high volume production.
C Profile Roll Former Manufacturers
Many companies offer specialized C profile roll forming equipment and technology, including:
- Rollvis (Italy)
- Samco Machinery (UK)
- Metform International (US)
- Botou Xianfa Roll Forming Machine (China)
- Gasparini SpA (Italy)
- Formtek Canada
- Dallan SpA (Italy)
When selecting a C profile roll former, consider the manufacturer’s experience, production speeds, quality standards, and service support. High precision European and American machines tend to offer the best performance and reliability.
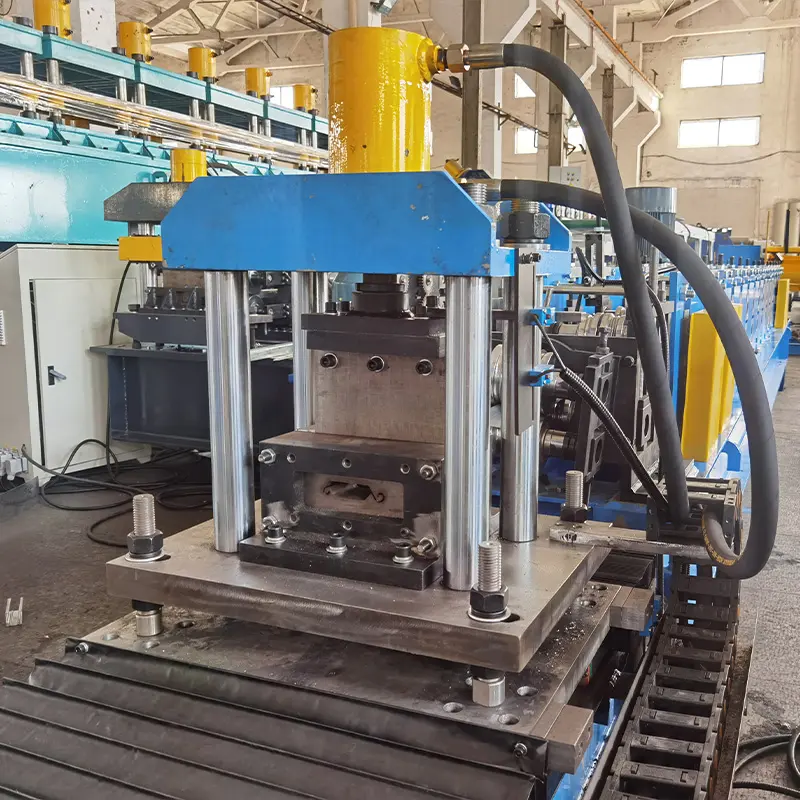
निष्कर्ष
With its ability to efficiently mass produce structural C profiles, the C profile roll forming machine provides important capabilities for the construction industry and other metal fabrication sectors.
The unique arrangement of forming rolls, feed systems, and cutoff mechanisms allow complete control over the C channel shape, dimensions, and lengths.
Continued technology advancements will further improve the productivity, precision, and capabilities of C profile roll forming equipment.
सामान्य प्रश्न
What materials can be roll formed into C profiles?
The most common materials are mild steel, stainless steel, and aluminum. With the proper roll sets, galvanized steel, brass, copper, and titanium can also be formed into C sections.
What thickness range can a C profile roll former handle?
A typical machine can process material from 0.5 mm up to 3 mm thickness. Special heavy duty roll formers are available that can form steel over 5 mm thick.
How are different C profile sizes set up on the machine?
Most roll formers use a quick change cassette system. Preset cassettes with the properly contoured rolls can be swapped out to rapidly change over between common profile sizes.
How accurate is a C profile roll formed part?
With advanced machines, dimensional tolerances of +/- 0.5 mm on critical dimensions can be achieved. The accuracy depends on precision components, a rigid frame, and proper machine calibration.
Can a C profile be strengthened with in-line heat treatment?
Yes, some roll formers have a heat treat station built into the line. As the profile exits the final forming stand, it passes through an induction heating system to improve its strength through controlled heating and cooling.
Are there safety concerns with a C profile roll forming machine?
All moving and rotating parts must be properly guarded for operator protection. Other safety features include emergency stop circuits, interlocks, and overload/fault monitoring. Proper training and protective equipment are also essential.
How fast can a C profile roll former operate?
Standard production speeds are around 10 to 15 meters per minute. High speed machines can achieve up to 40 m/min, while slower precision roll formers may operate at 5 m/min. The maximum speed depends on the profile size, material thickness, and required tolerance.
What expertise is needed to program and operate a C profile roll former?
The machine is programmed by experienced technicians based on the profile specifications. General operators then simply select the preset profile recipe. PC-based controls with touch screens make the machines user-friendly.
निष्कर्ष
In summary, C profile roll forming machines are specialized equipment engineered specifically to form structural C channel profiles. Their core functions include precision feeding, incremental forming, support and guiding, and cutoff. When all mechanisms work together, the roll former can produce C sections in high volumes with accuracy and repeatability. With speed, flexibility, and quality advantages over other processes, these versatile machines will continue enabling cost-effective production of C profiles across numerous industries.
Links provided by Claude may not always be valid or up to date. We appreciate your patience as we work to improve link accuracy.Copy
continue the part of FAQ
L
Here is more content continuing the FAQ section:
How should C profile roll formed parts be handled and stored?
Care should be taken to avoid scratches, dents, and deformation during handling. Use lifting straps instead of chains or hooks. Store profiles on wooden racks and avoid letting them rest on hard surfaces. Use protective inserts between stacked profiles.
What causes defects like twisting or flairing in roll formed C profiles?
This can be caused by issues like worn forming rolls, inadequate support rollers, poor stock alignment, or excessive feed speeds. It’s critical to monitor and inspect for defects and make any necessary forming adjustments.
How are complex variations of C profiles produced?
More complex shapes may require 3D forming rolls, additional forming stations, support tooling within the profile, post-forming operations like punching or notching, or secondary value-added processes.
How should roll formed C profiles be joined for assemblies?
Self-tapping screws inserted into pre-punched holes is a common joining method. Other options include welding, riveting, clinching, or using hardware like bolts, gussets, and brackets.
What factors determine the machine size and number of roll stations?
Larger profile dimensions and thicker material generally require a bigger frame size, higher tonnage, and more roll stations to handle the forces and bending increments.
How should tooling life and profile quality be monitored?
Regular inspection of roll wear, profile dimensions, cut quality, and surface finish should be done. This ensures problems are caught early before quality deteriorates.
What safety precautions are important for maintenance and setup?
Lockout/tagout procedures must be followed. Only skilled technicians should perform tasks like roll changes, machining, and electrical work. Use proper lifting equipment and follow safety procedures.
How is advanced data collection used on modern C profile roll formers?
PLC data monitoring, HMI diagnostics screens, and IoT sensors can provide production analytics. This helps identify areas for optimization and predictive maintenance.
What expertise is required for proper machine operation?
Operators should have training in machine safety, startup and shutdown, troubleshooting, quality checks, and basic maintenance. Experience with similar metalworking equipment is preferred.