The फर्श डेक रोल बनाने की मशीन is an industrial equipment used to manufacture floor decks or metal deck panels by cold-forming thin gauge steel coils. These panels are widely employed in the construction industry for various applications like floor and roof systems, formwork, and concrete reinforcement. This comprehensive guide delves into the intricacies of floor deck roll forming machines, their working principles, components, and industrial applications.
Overview of Floor Deck Roll Forming Machines
A floor deck roll forming machine is a specialized equipment that progressively forms a continuous stream of metal coils into the desired floor deck profile through a series of synchronized roll stands. These machines are designed to produce floor decks with intricate shapes, embossments, and stiffening ribs, ensuring high structural integrity and load-bearing capacity.
The roll forming process involves feeding a flat metal coil (typically galvanized steel or aluminum) into the machine, where it undergoes a series of cold-forming operations through strategically arranged roll stands. Each roll stand progressively bends and shapes the metal strip, gradually transforming it into the desired floor deck profile.
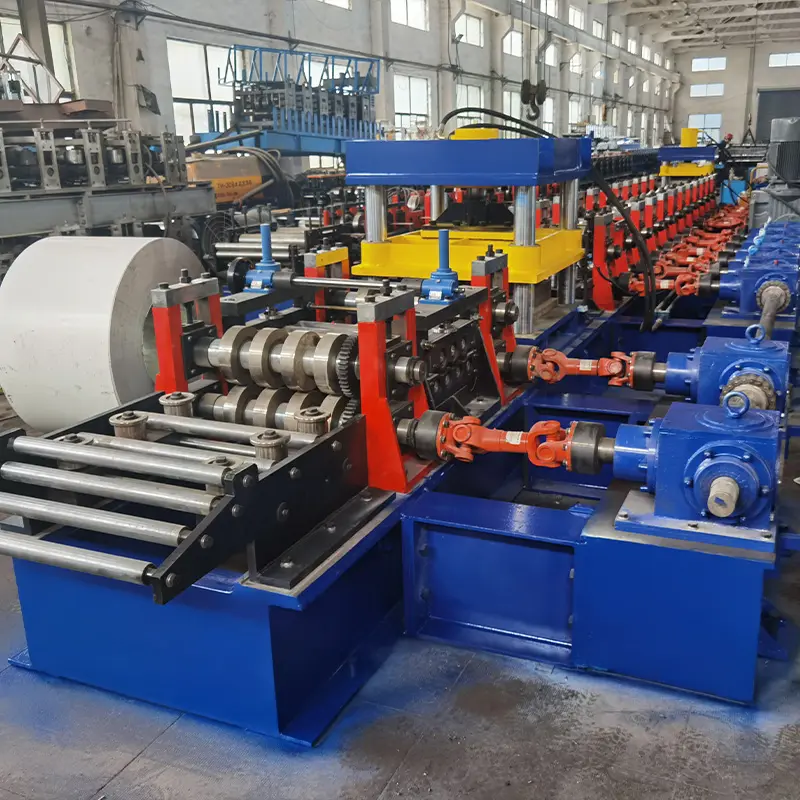
तल डेक रोल बनाने की मशीन Components
Floor deck roll forming machines comprise several essential components that work in harmony to produce high-quality floor decks efficiently. Here’s a breakdown of the key components:
Component | Description |
---|---|
डेकोइलर | Holds and feeds the metal coil into the roll forming line, ensuring a consistent supply of material. |
Entry Guide | Aligns and guides the metal strip into the first set of roll stands. |
Roll Stands | A series of roll stands, each with a specific configuration of rollers that progressively bend and shape the metal strip into the desired floor deck profile. |
Punch and Embossing Units | Integrated units that punch holes, create embossments, or add stiffening ribs to the formed floor deck. |
Cut-off Press | A hydraulic or mechanical press that cuts the formed floor deck to the desired length. |
Stacker or Collector Bed | Collects and stacks the finished floor deck panels for easy handling and transportation. |
नियंत्रण प्रणाली | A computerized control system that regulates the entire roll forming process, ensuring precise and consistent product quality. |
Floor Deck Roll Forming Process
The floor deck roll forming process can be broken down into the following steps:
- Material Feeding: The metal coil is loaded onto the decoiler, which feeds the metal strip into the roll forming line at a controlled speed.
- Forming: As the metal strip enters the roll forming line, it passes through a series of roll stands, each with a specific roller configuration. These rollers progressively bend and shape the metal strip, transforming it into the desired floor deck profile.
- Punching and Embossing: Depending on the design requirements, the formed floor deck may undergo additional operations like punching holes or creating embossments using integrated punch and embossing units.
- Cut-off and Stacking: Once the floor deck reaches the desired length, the cut-off press severs the formed panel, and the finished product is collected and stacked on the stacker or collector bed.
- Quality Control: Throughout the process, various quality control measures are implemented to ensure dimensional accuracy, surface finish, and overall product quality.
Industrial Applications of Floor Deck Roll Forming Machines
Floor deck roll forming machines are essential in various industries and construction projects, including:
आवेदन | Description |
---|---|
Building Construction | Floor decks are widely used in commercial, residential, and industrial buildings, providing support for concrete slabs and serving as formwork. |
Infrastructure Projects | Floor decks are employed in the construction of bridges, overpasses, and other infrastructure projects, offering efficient and cost-effective solutions. |
Modular Construction | Prefabricated floor deck panels are utilized in modular construction techniques, enabling faster and more efficient building processes. |
Parking Garages | Floor decks are commonly used in the construction of multi-level parking garages, providing a durable and load-bearing surface. |
Retrofitting and Renovation | Roll-formed floor decks are often used in renovation projects, offering a lightweight and cost-effective solution for structural reinforcement. |
-
वाइनयार्ड पोस्ट रोल बनाने की मशीन
-
ऑटो आकार बदलने योग्य सिग्मा शहतीर रोल बनाने की मशीन
-
सी सेक्शन ब्रेसिंग ओमेगा स्टोरेज रैक अपराइट पोस्ट रोल बनाने की मशीन
-
स्टील बॉक्स प्लेट रोल बनाने की मशीन बनाना
-
शेल्फ कॉलम के लिए बॉक्स बीम स्टील रोल बनाने की मशीन
-
पैलेट रैकिंग स्टेप बीम पी बीम रोल बनाने की मशीन
-
गोदाम शेल्फ ईमानदार रोल बनाने की मशीन
-
विद्युत कैबिनेट फ्रेम रोल बनाने की मशीन
-
दीन रेल रोल बनाने की मशीन
Material Feeding and Forming Options
Floor deck roll forming machines can accommodate a wide range of materials and configurations, allowing for versatility in production. Here’s an overview of the material feeding and forming options:
Aspect | Options |
---|---|
Material Types | Galvanized Steel, Stainless Steel, Aluminum, Cold-Rolled Steel |
Coil Widths | Ranging from 12 inches to 36 inches (or wider, depending on the machine specifications) |
Coil Thicknesses | Typically ranging from 0.6 mm to 1.2 mm (or thicker, based on the application) |
Profile Types | Ribbed, Fluted, Trapezoidal, Dovetail, and various other custom profiles |
Forming Capabilities | Punching, Embossing, Slitting, Crimping, Perforating |
Suppliers and Price Range
Floor deck roll forming machines are available from various suppliers, ranging from local manufacturers to global industry leaders. The price range for these machines can vary significantly based on factors such as production capacity, level of automation, and customization options. Here’s a general overview of suppliers and price ranges:
Supplier | Price Range (USD) |
---|---|
Local/Regional Manufacturers | $50,000 – $250,000 |
National Manufacturers | $200,000 – $500,000 |
Global Industry Leaders | $500,000 – $1,500,000 |
It’s important to note that these price ranges are approximate and can vary depending on specific machine configurations, additional features, and customization requirements.
Installation, Operation, and Maintenance
Proper installation, operation, and maintenance are crucial for ensuring the longevity and optimal performance of floor deck roll forming machines. Here’s an overview of these aspects:
Aspect | Description |
---|---|
Installation | Roll forming machines require a dedicated production area with adequate space, proper flooring, and utilities (electricity, compressed air, etc.). Professional installation services are recommended for proper setup and calibration. |
Operation | Skilled operators are essential for running the roll forming machine safely and efficiently. Comprehensive training programs are often provided by the machine manufacturers. |
Maintenance | Regular maintenance, including lubrication, roll alignment, and component inspections, is necessary to prevent breakdowns and ensure consistent product quality. Preventive maintenance schedules should be followed strictly. |
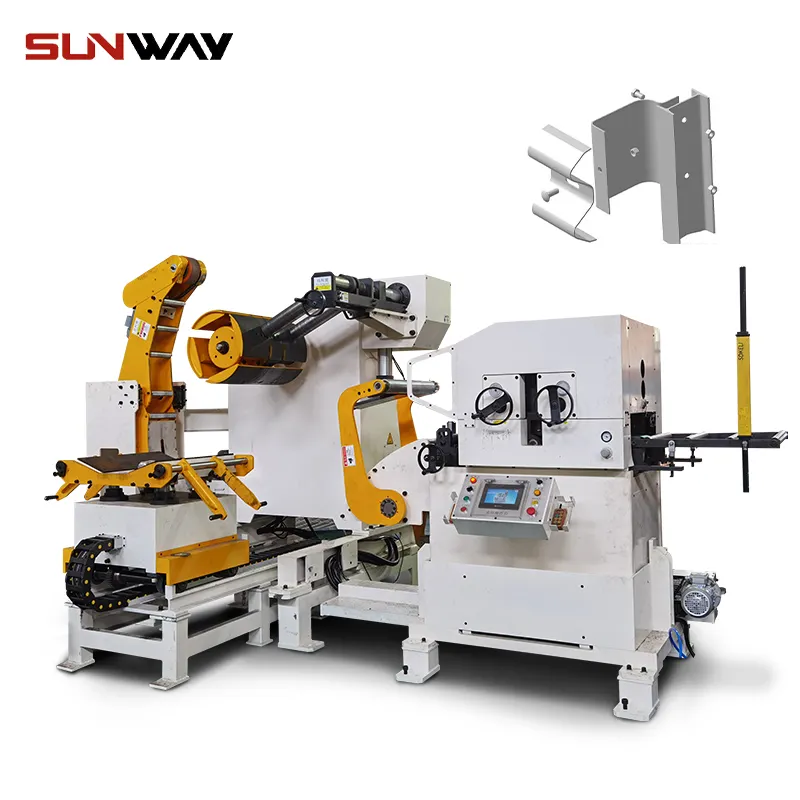
Choosing the Right Supplier
Selecting the right supplier for your floor deck roll forming machine is crucial to ensure optimal performance, quality, and support. Here are some key factors to consider when choosing a supplier:
Factor | Description |
---|---|
Reputation and Experience | Prioritize suppliers with a proven track record and extensive experience in the roll forming industry. |
Product Quality and Reliability | Evaluate the quality and reliability of the machines offered by different suppliers, ensuring they meet industry standards and your specific requirements. |
Customization Capabilities | Consider suppliers that offer comprehensive customization options to tailor the machine to your unique production needs. |
After-Sales Support | Assess the level of after-sales support, including training, maintenance services, and spare parts availability. |
Price and Value | While price is a consideration, it’s essential to evaluate the overall value proposition, including machine capabilities, quality, and long-term costs. |
Delivery and Lead Times | Evaluate the supplier’s ability to meet your project timelines and delivery requirements. |
Pros and Cons of Floor Deck Roll Forming Machines
Like any industrial equipment, floor deck roll forming machines have their advantages and limitations. Here’s a breakdown of the pros and cons:
Pros | Cons |
---|---|
High Production Efficiency | Initial Investment Cost |
Consistent Product Quality | Skilled Labor Required |
Design Flexibility and Customization | Maintenance and Downtime |
Cost-Effective Manufacturing | Limited Material Thickness Range |
Versatility in Material Types | Setup and Changeover Time |
Automated and Continuous Production | Space Requirements |
Advantages and Limitations
While floor deck roll forming machines offer several advantages, it’s important to understand their limitations as well. Here’s a more detailed look at the advantages and limitations:
Advantages:
- High Production Efficiency: Roll forming machines can produce floor decks continuously and at high speeds, resulting in increased production efficiency and output.
- Consistent Product Quality: With precise roll stand configurations and automated controls, roll forming machines ensure consistent dimensional accuracy and product quality.
- Design Flexibility and Customization: Roll forming machines can be customized to produce a wide range of floor deck profiles, accommodating unique design requirements.
- Cost-Effective Manufacturing: Compared to traditional manufacturing methods, roll forming is a cost-effective way to produce floor decks, resulting in lower material waste and labor costs.
- Versatility in Material Types: Roll forming machines can accommodate various materials, including galvanized steel, stainless steel, aluminum, and cold-rolled steel.
Limitations:
- Initial Investment Cost: Floor deck roll forming machines can be a significant investment, especially for high-end, fully automated systems.
- Skilled Labor Required: Operating and maintaining roll forming machines requires skilled labor, which may involve additional training and personnel costs.
- Maintenance and Downtime: Regular maintenance is necessary to ensure optimal performance and prevent breakdowns, which can lead to production downtime and associated costs.
- Limited Material Thickness Range: Roll forming machines have a limited material thickness range they can accommodate, typically ranging from 0.6 mm to 1.2 mm (or thicker, depending on the machine specifications).
- Setup and Changeover Time: Changing from one floor deck profile to another may require time-consuming adjustments and setup, potentially impacting production efficiency.
- Space Requirements: Roll forming machines, especially larger systems, require significant floor space for installation and operation, which may be a consideration for facilities with space constraints.
It’s essential to carefully evaluate your specific production requirements, budget, and operational constraints to determine if a floor deck roll forming machine is the right fit for your manufacturing needs.
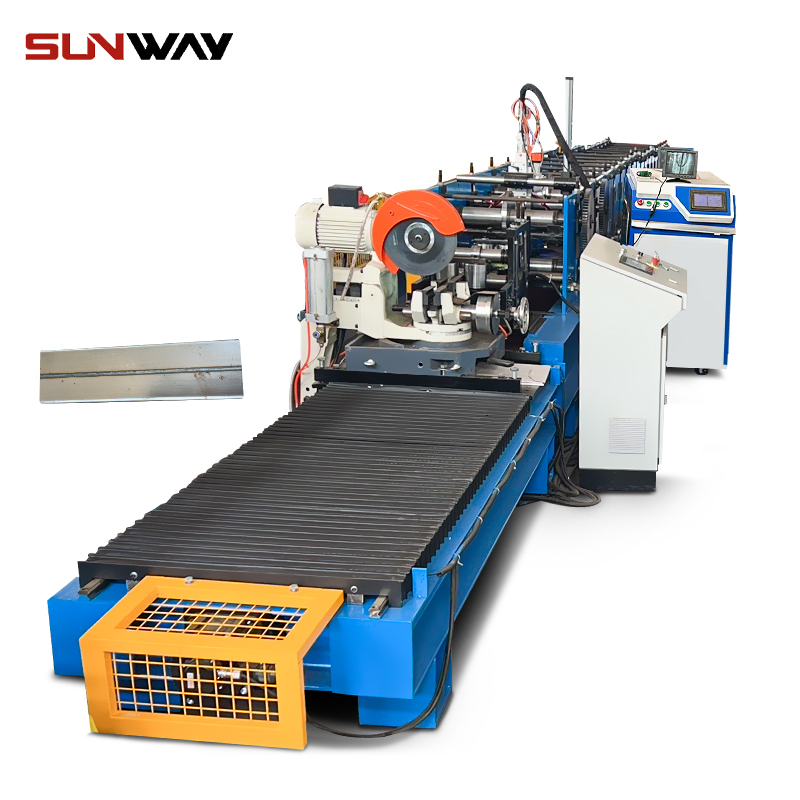
Key Parameters and Considerations
When evaluating and selecting a floor deck roll forming machine, several key parameters and considerations should be taken into account. Here’s an overview of some critical factors:
Parameter | Description |
---|---|
Production Capacity | Assess your desired output rates and ensure the machine can meet your production requirements. |
Material Compatibility | Verify that the machine can accommodate the types and thicknesses of materials you plan to use. |
Profile Versatility | Consider the range of floor deck profiles the machine can produce and its ability to accommodate future design changes. |
Automation Level | Determine the level of automation required, factoring in factors like labor costs, production volumes, and efficiency goals. |
Floor Space and Layout | Ensure that your facility has sufficient space and an appropriate layout to accommodate the roll forming machine and associated equipment. |
Integration Capabilities | Evaluate the machine’s ability to integrate with existing systems, such as CAD/CAM software or automated material handling systems. |
Energy Efficiency | Consider the machine’s energy consumption and potential energy-saving features to minimize operating costs. |
Noise and Vibration Levels | Assess the machine’s noise and vibration levels, as these factors can impact the working environment and potentially require additional sound insulation measures. |
Safety Features | Prioritize machines with robust safety features, such as emergency stop systems, guarding, and operator protection measures. |
Supplier Support | Evaluate the supplier’s track record, after-sales support, and availability of spare parts and maintenance services. |
By carefully considering these parameters and weighing them against your specific requirements, you can make an informed decision and select a floor deck roll forming machine that aligns with your production needs, budget, and operational objectives.
FAQs
Question | Answer |
---|---|
What is the typical production speed of a floor deck roll forming machine? | The production speed can vary based on the machine’s specifications and configuration, but most modern floor deck roll forming machines can achieve speeds ranging from 30 to 120 feet per minute (9 to 36 meters per minute). |
Can floor deck roll forming machines handle different material thicknesses? | Yes, most floor deck roll forming machines are designed to accommodate a range of material thicknesses, typically from 0.6 mm to 1.2 mm (or thicker, depending on the machine specifications and application requirements). |
How long does it take to change the roll stand configuration for a different floor deck profile? | The changeover time can vary depending on the machine’s design and the complexity of the profile change. It can range from a few hours to a full day, depending on the level of automation and the skill of the operators. |
What maintenance is required for floor deck roll forming machines? | Regular maintenance is essential, including lubrication, roll alignment checks, tooling inspections, and component replacements as needed. Preventive maintenance schedules should be followed strictly to ensure optimal performance and minimize downtime. |