परिचय
Understanding the Importance of Roll Forming Machines
Roll forming machines play a crucial role in the manufacturing industry, enabling the efficient production of various metal profiles and components. One such innovative machine is the double deck roll forming machine, which offers enhanced productivity and versatility. In this article, we will delve into the details of double deck roll forming machines, exploring their working principle, benefits, applications, maintenance tips, troubleshooting, and future trends.
What is a Double Deck Roll Forming Machine?
A double deck roll forming machine is a specialized equipment used to shape continuous metal coils into desired profiles with precision and consistency. It consists of two independent roll forming stations stacked vertically, allowing for the simultaneous production of two different profiles or panel configurations. This unique design increases production efficiency and flexibility, making the machine ideal for diverse manufacturing applications.
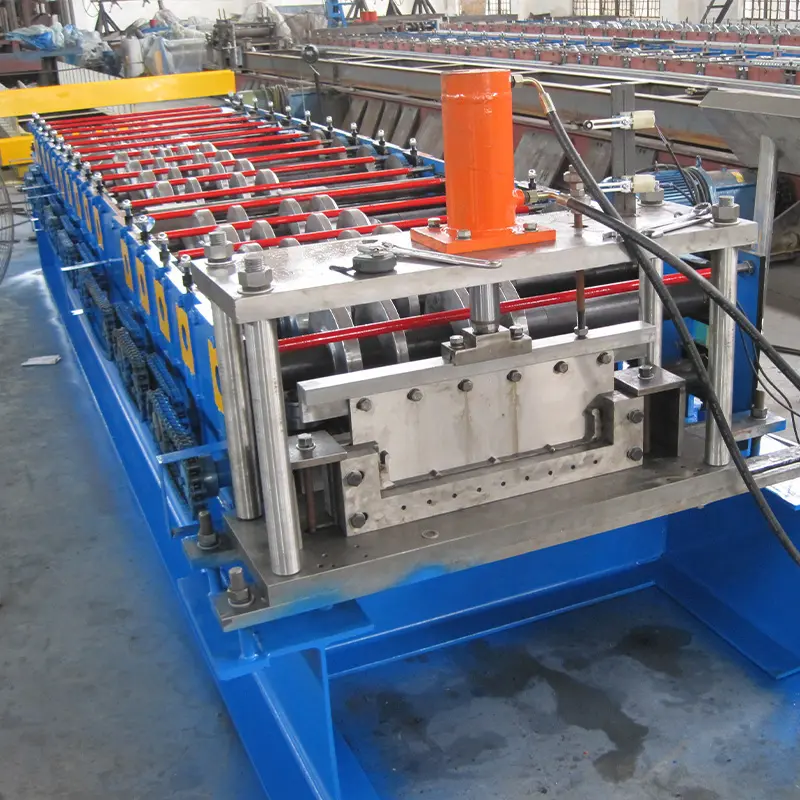
Working Principle of a Double Deck Roll Forming Machine
A double deck roll forming machine operates based on the principle of continuous bending and shaping of metal coils. Here is a step-by-step breakdown of its working process:
- Coil Unwinding: The process begins by unwinding the metal coil, which is loaded onto the machine’s entry section.
- Material Feeding: The metal strip is then fed into the first roll forming station, where a series of roller dies gradually shape the strip into the desired profile.
- First Deck Roll Forming: The first roll forming station utilizes a set of rolls and forming dies to progressively bend the metal strip into the desired shape. The precise adjustment of roller gaps and forming speeds ensures accurate and consistent results.
- Second Deck Roll Forming: Once the strip passes through the first station, it moves to the second roll forming station, located above the first one. The second station operates independently and can shape the strip into a different profile or panel configuration.
- Cutting and Stacking: After both decks complete the roll forming process, the machine cuts the profiles to the required length using a shearing mechanism. The cut profiles are then stacked or collected for further processing or assembly.
Benefits of Using a Double Deck Roll Forming Machine
Using a double deck roll forming machine offers several advantages for manufacturers:
- Increased Productivity: The simultaneous operation of two roll forming stations allows for higher production rates compared to single deck machines. This reduces manufacturing time and boosts overall productivity.
- Versatility: Double deck roll forming machines enable the production of two different profiles or panel configurations simultaneously. Manufacturers can switch between products quickly, accommodating diverse customer requirements.
- Cost Efficiency: The efficiency and speed of double deck roll forming machines contribute to cost savings in production. Faster turnaround times, reduced material waste, and improved output quality all lead to enhanced profitability.
- Design Flexibility: The machine’s independent deck design allows manufacturers to create unique profiles or incorporate multiple functionalities in a single product. This promotes design flexibility and innovation.
- Improved Quality and Accuracy: Double deck roll forming machines offer precise control over the roll forming process, ensuring consistent quality across all produced profiles. The machine’s advanced control systems enable accurate dimensioning and high repeatability.
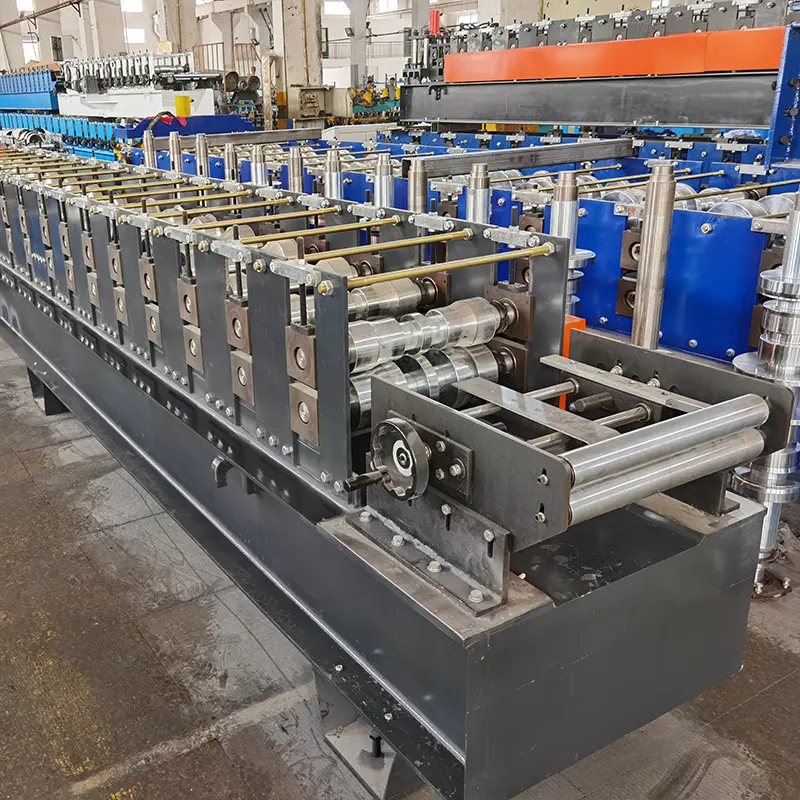
Applications of Double Deck Roll Forming Machines
Double deck roll forming machines find applications in various industries:
- Construction and Architecture: These machines are used to manufacture metal roofing panels, wall cladding, steel framing components, and other building elements.
- Automotive Industry: Double deck roll forming machines produce automotive body parts, such as door frames, roof rails, and structural components.
- HVAC Systems: The machines are employed to fabricate ductwork, ventilation components, and air conditioning system parts.
- Furniture and Shelving: Manufacturers utilize double deck roll forming machines to create metal furniture components, shelving systems, and storage racks.
- Solar Energy: The machines contribute to the production of solar panel frames and mounting structures.
- Electrical Enclosures: Double deck roll forming machines are utilized for manufacturing electrical cabinets, control panels, and enclosure systems.
- Other Industries: Additional applications include the production of garage doors, appliance components, agricultural equipment, and more.
Factors to Consider When Choosing a Double Deck Roll Forming Machine
When selecting a double deck roll forming machine for your manufacturing needs, consider the following factors:
- Profile Requirements: Determine the specific profiles you need to produce and ensure the machine can accommodate them. Consider the maximum width, thickness, and complexity of profiles the machine can handle.
- Material Compatibility: Check if the machine supports the type of material you work with, such as steel, aluminum, or other metals. Verify the material thickness range and its compatibility with the roll forming process.
- Production Capacity: Evaluate the desired production volume and choose a machine that meets your capacity requirements. Consider factors like roll forming speed, coil loading capacity, and stacking options.
- Machine Flexibility: Assess the machine’s capability to produce various profiles and configurations. Look for features like quick tooling changeover, adjustable roller gaps, and independent deck control.
- Automation and Control Systems: Consider the level of automation and control offered by the machine. Advanced features like touchscreen interfaces, PLC controls, and integrated safety systems can enhance efficiency and ease of operation.
- Maintenance and Support: Ensure the manufacturer provides reliable after-sales service, technical support, and maintenance documentation. Check for warranty coverage and availability of spare parts.
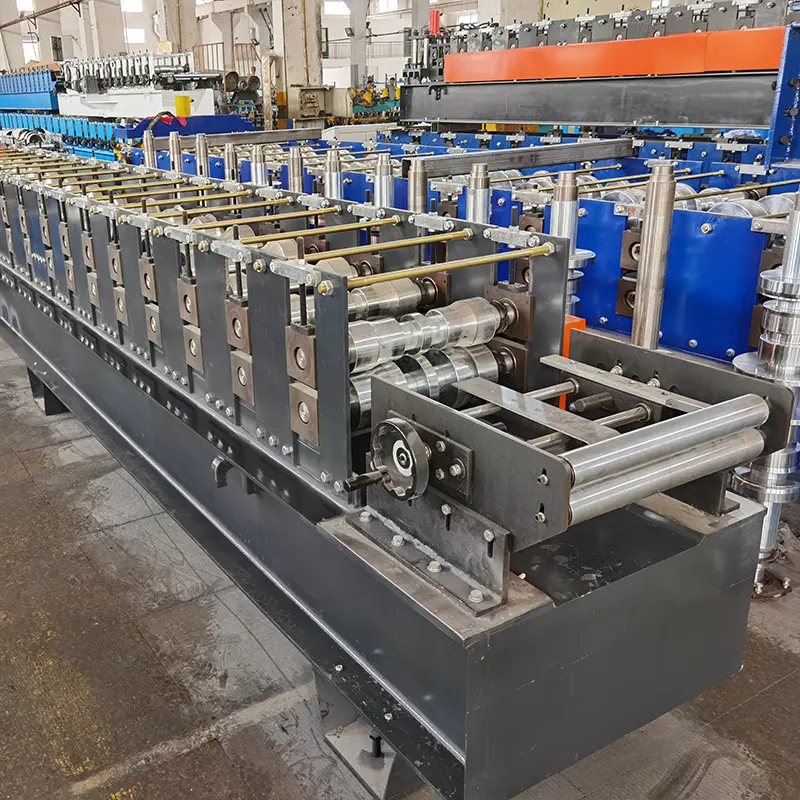
Maintenance and Safety Tips for Double Deck Roll Forming Machines
Proper maintenance and safety practices are crucial for the optimal performance and longevity of double deck roll forming machines. Here are some essential tips to follow:
- Regular Inspection: Conduct routine inspections to identify any signs of wear, damage, or misalignment in the machine’s components. Check for loose connections, lubrication levels, and the condition of belts, gears, and bearings.
- Lubrication: Follow the manufacturer’s guidelines for lubrication schedules and use the recommended lubricants. Regularly lubricate moving parts, rollers, and gears to reduce friction and prevent premature wear.
- Cleaning: Keep the machine clean and free from debris, dust, and metal shavings. Use appropriate cleaning methods and avoid abrasive materials that could damage the machine’s surfaces.
- Safety Measures: Implement comprehensive safety measures, including the use of personal protective equipment (PPE) for operators. Ensure emergency stop buttons, safety guards, and interlocking systems are in place and functioning properly.
- Operator Training: Provide thorough training to machine operators to ensure they understand the equipment’s operation, safety protocols, and maintenance procedures. Regularly update training programs to address any new features or technologies.
- Documentation: Maintain detailed records of maintenance activities, inspections, repairs, and any modifications made to the machine. This documentation will be useful for troubleshooting and future reference.
Troubleshooting Common Issues with Double Deck Roll Forming Machines
Even with regular maintenance, double deck roll forming machines may encounter occasional issues. Here are some common problems and their possible solutions:
- Uneven Profile Dimensions: Check for misaligned rolls, damaged forming dies, or improper adjustment of roller gaps. Ensure that all components are properly aligned and adjusted according to the specifications for the desired profile.
- Material Jamming: If the metal strip gets stuck or jams during the roll forming process, inspect the entry and exit guides for any obstructions. Clear out any debris or foreign objects that may be hindering the smooth movement of the material.
- Inconsistent Profile Shape: Verify that the material thickness is within the machine’s specified range. Inaccurate profile shaping can also occur due to worn-out or damaged forming rolls. Replace any worn components and ensure proper alignment to achieve consistent profile shapes.
- Excessive Noise or Vibration: Excessive noise or vibration during operation may indicate misaligned rolls, loose components, or damaged bearings. Conduct a thorough inspection of the machine’s mechanical parts and tighten any loose connections. Replace worn-out bearings or other damaged components.
- Coil Alignment Issues: Improper coil alignment can lead to feeding problems and affect the quality of the formed profiles. Check the coil loading system for proper alignment and tension control. Adjust the guides and ensure that the material is properly centered and aligned during the feeding process.
- Electrical or Control Malfunctions: If the machine experiences electrical or control issues, inspect the wiring, connections, and control systems. Check for loose connections, damaged cables, or faulty sensors. Consult the machine’s manual or contact the manufacturer for assistance in diagnosing and resolving electrical problems.
- Insufficient Lubrication: Inadequate lubrication can cause increased friction, premature wear, and suboptimal performance. Follow the manufacturer’s recommended lubrication schedule and use the appropriate lubricants for each part of the machine. Regularly check and refill lubrication reservoirs as needed.
If troubleshooting the issues becomes challenging or requires expertise, it is advisable to contact the machine manufacturer or seek assistance from a professional technician.
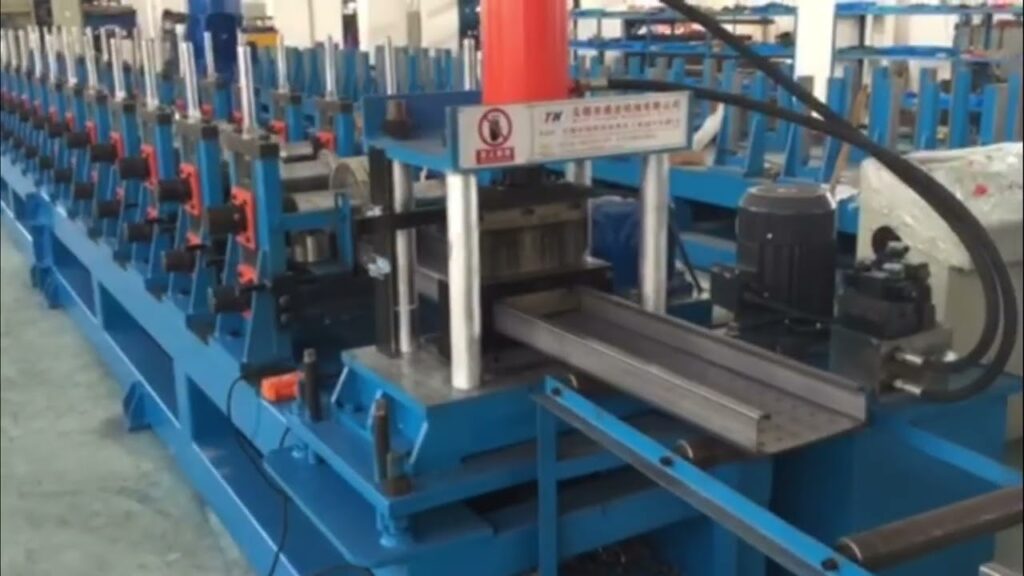
Future Trends in Double Deck Roll Forming Technology
Double deck roll forming technology continues to evolve, incorporating innovative features and advancements. Here are some future trends to watch for:
- Integrated Automation: Automation plays a significant role in improving efficiency and reducing human error. Future double deck roll forming machines are expected to integrate advanced automation technologies such as robotic material handling, automatic tooling changeover, and real-time production monitoring.
- Enhanced Control Systems: Advanced control systems will offer improved user interfaces, intuitive programming, and data analytics capabilities. These features will enable manufacturers to optimize production, monitor performance, and make data-driven decisions.
- Lightweight Material Applications: With the growing demand for lightweight materials in various industries, double deck roll forming machines will adapt to process materials like advanced high-strength steels, aluminum alloys, and composite materials. This will cater to industries seeking weight reduction and improved fuel efficiency.
- Customization and Design Flexibility: Manufacturers will benefit from increased design flexibility and customization options. Future machines may incorporate modular tooling systems and advanced software for quick product changeovers and rapid prototyping.
- Energy Efficiency: The focus on sustainability and energy efficiency will drive the development of more energy-efficient double deck roll forming machines. Optimized motor systems, energy recovery mechanisms, and smart power management will contribute to reduced energy consumption during operation.
- Integration of Inline Quality Inspection: Inline quality inspection systems will be integrated into double deck roll forming machines, allowing for real-time quality control and defect detection. Vision systems, sensors, and machine learning algorithms will ensure consistent and high-quality production.
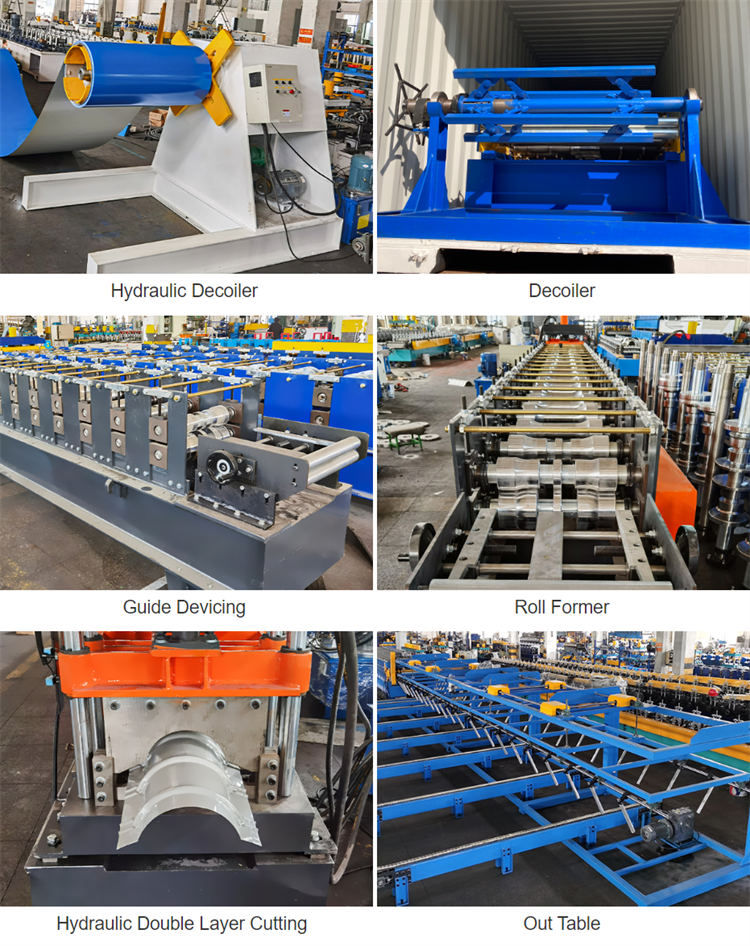
निष्कर्ष
Double deck roll forming machines are versatile and efficient equipment used in the manufacturing industry for shaping metal coils into precise profiles. They offer numerous benefits, including increased productivity, versatility, cost efficiency, design flexibility, and improved quality. These machines find applications in various industries such as construction, automotive, HVAC, furniture, solar energy, and more. Choosing the right machine involves considering factors like profile requirements, material compatibility, production capacity, machine flexibility, automation, and support. Proper maintenance and adherence to safety guidelines are essential for optimal performance and longevity. Troubleshooting common issues and staying updated on future trends in double deck roll forming technology can further enhance productivity and competitiveness in the manufacturing sector.
FAQs
1. What is the difference between a single deck and a double deck roll forming machine? A single deck roll forming machine has only one roll forming station, whereas a double deck roll forming machine has two independent stations stacked vertically. The double deck design allows for simultaneous production of two different profiles or panel configurations, resulting in increased productivity and versatility.
2. Can double deck roll forming machines handle different types of metals? Yes, double deck roll forming machines can process various types of metals such as steel, aluminum, and others. However, it is essential to check the machine’s specifications and ensure its compatibility with the specific metal and thickness required for the desired profiles.
3. Are double deck roll forming machines suitable for small-scale production? Double deck roll forming machines are commonly used in both small-scale and large-scale production environments. Their versatility, design flexibility, and quick product changeover capabilities make them suitable for a wide range of manufacturing needs.
4. How often should a double deck roll forming machine undergo maintenance? Regular maintenance is crucial to ensure the optimal performance and longevity of a double deck roll forming machine. The frequency of maintenance depends on factors such as machine usage, operating conditions, and manufacturer recommendations. It is advisable to follow the manufacturer’s maintenance schedule and conduct routine inspections to identify and address any issues promptly.
5. Can double deck roll forming machines be customized to specific production requirements? Yes, double deck roll forming machines can be customized to meet specific production requirements. Manufacturers often offer options for modular tooling systems, adjustable roller gaps, and programmable control systems, allowing for flexibility in creating unique profiles or accommodating specific customer needs. It is advisable to consult with the machine manufacturer to discuss customization options.