china wall angle roll forming machines are used to continuously bend sheet metal into various shapes. This guide covers “China Wall” angle rollers specifically for producing wall panels and angle structural frames for buildings, solar panel mounts, and similar applications.
Overview of China Wall Angle Roll Forming Machine
China Wall angle rollers incorporate multiple box/pyramid type bending stations in-line to form complex cross-section panels and angles from strip steel coil. Key details:
- Forming Capacity: Up to 3mm thickness mild steel
- Product Types: Wall panels, solar mounting frames, angle frames, metal decking
- Forming Stations: Typically 4-12 various punch/bend stations
- Drives: Hydraulic or servo motor with PLC control
- Speed: 10-15 m/min
- Voltage: 380V, 50Hz (or customized)
Types of China Wall Angle Roll Forming Machines
There are a few design variations of China Wall angle rollers as summarized below:
Type | Description |
---|---|
Pyramid 12 Stations | For heavy wall panels. Around 12 pyramid stations. |
Pyramid 8 Stations | Lighter wall panels/decking. 8 stations. |
Step Roll Former | Angles and solar frames. Step punch and bend stations. |
Combined Pyramid + Step Stations | Hybrid design wall panels plus angles. |
The number and configuration of stations determines the complexity of forms producible. Machines with both pyramid and step-type tooling offer the most flexibility for factories.
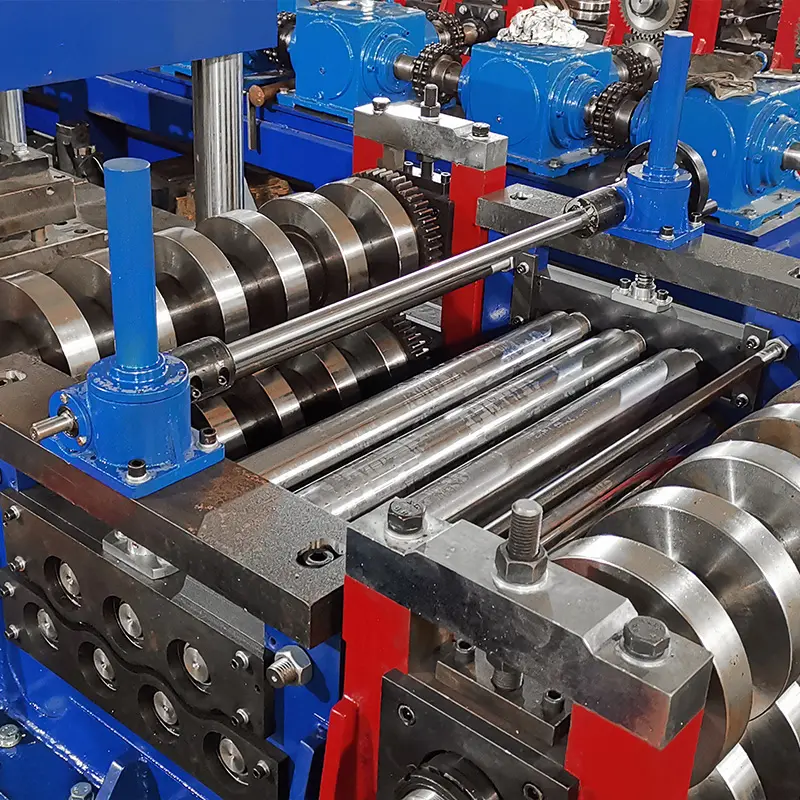
Working Process of Angle Roll Former
The working process involves unwinding coil stock, progressively punching and bending the strip through a series of pyramid and/or step stations to the desired profile, then cutting to length with a flying shear.
Adjustable upper and lower rollers guide the strip through the inline forming stations. The punch and die tooling bend and deform the metal incrementally at each station until the final angle, cavity, or channel shape is achieved.
Servo electric, hydraulic, or servo hydraulic motors drive the main rolling shafts as well as punch actuators. The punch frequency, material feed, and shear are synchronized by a PLC controller for automated operation.
Operators feed the sheet metal coil into the de-coiler and initiate the cycle through a touch screen panel. Formed product continuously exits the roll former where it can be manually cut or stack collected using a hydraulic shear.
The roll tooling is customized to produce the desired wall panel or angle cross-section. Complex shapes utilize more forming stations in sequence with deeper, asymmetric punches. Quick profile changes can be done by exchanging station cassettes.
Material Feeding, Roll Tooling, and Design
Details on the raw material requirements, roll forming process, and cross-sectional design flexibility are covered below:
Parameter | विवरण |
---|---|
Material Type | HR steel strip, DX51, Q235, galvanized, painted |
Material Thickness | 0.3-3 mm |
Material Width | 1000-1250 mm |
Coil I.D. | 508 mm |
Decoiler Capacity | 5 tons max |
Forming Stations | 4 to 12+ punch/bend boxes |
Punches and Dies | Quick change modular tooling. Custom profile. |
Roll Design Software | 3D modeling provided for tooling design |
Finished Profile | Channels, angles, ribs, panels. Symmetric and asymmetric. |
Hole Punching | Optional in-line hole punch units |
Profile Height | 50-320mm typical |
Curling Function | For panel edges. Optional. |
The modular tooling allows for easy design of cavities, channels, return lips, and complex asymmetric forms. The roll formed pieces can be perforated or punched inline. Special edge curling stations provide decorative edging.
Top China Wall Angle Roll Forming Machine Manufacturers
There are several major factories supplying pyramid and step roll formers made in China, including:
कंपनी | Location | संपर्क करना |
---|---|---|
BOD Machinery | Jiangsu | [email protected] |
Elite Machinery | Shanghai | [email protected] |
YSD Roll Former | Hebei | [email protected] |
CF YJ Industry | Shandong | [email protected] |
These companies offer ISO certified construction with CE marked electrical components. The machine frames are constructed from steel plate, with hardened wear-resistant components at punch/die stations. Pricing ranges from 30,000 USD up to 150,000+ USD depending on configuration. Delivery time averages 3-4 months.
-
रोलिंग शटर स्लेट रोल बनाने की मशीन
-
विद्युत कैबिनेट फ्रेम रोल बनाने की मशीन
-
दीन रेल रोल बनाने की मशीन
-
केबल सीढ़ी रोल बनाने की मशीन
-
पीवी माउंटिंग ब्रैकेट सी शेप प्रोफाइल रोल बनाने की मशीन
-
केबल ट्रे रोल बनाने की मशीन
-
स्टील का तार लंबाई लाइन मशीन में कटौती
-
स्टील का तार लंबाई लाइन मशीन में कटौती
-
स्टील का तार लंबाई लाइन मशीन में कटौती
Installing China Wall Angle Roll Former
Proper installation is key for smooth operation of the angle roll forming system:
- Foundation should be level concrete able to bear 15 tons weight
- Leave 1000mm clearance around machine for coil loading and servicing
- Electrical supply should be grounded 380V 50Hz 35+ kW depending on size
- Air and water connections made to panel for hydraulics cooling
- Test run initially with plastic/wood before metal sheet
- Adjust punch actuators, rollers for 0.2mm clearance to stock
- Control panel accessible within 6 meters of operation side
Take care when moving machine sections into place. Recheck anchor bolt locations and shim configuration. Tighten all station bolts/nuts before operation. Confirm electrical phases wired correctly before applying power.
Operation of China Wall Angle Roll Former
The angle roll forming machine is operated through an integrated control panel:
- Touchscreen for selecting profiles, speed, punches
- Buttons for Start, Stop, Emergency stop
- Status indicators for drives, stations
- Alarm history log and troubleshooting guides
- Convenient USB port for tooling design files
- Wireless connectivity optional for mobile monitoring
Loading procedures:
- Open decoiler safety gate and thread coil through guides onto mandrel
- Clamp tail end of coil strip into feed section
- Select profile on HMI recipe screen corresponding to tooling
- Press Start for automatic operation
- First pieces may be deformed until all stations activate
- Monitor strip feed, shear, and exit of formed pieces
- Stop machine to clear jams if necessary
The PLC automatically synchronizes the punch frequency, feed rate, shear and other components once running stable to produce formed pieces continuously. farming efficiency is up to 25 pieces per minute depending on profile complexity.
Maintenance of China Wall Angle Roll Former
Regular maintenance activities include:
Task | Frequency | Procedure |
---|---|---|
Check oil level | Daily | Top up hydraulic tank as needed |
Clean filter | Monthly | Drain filter housing; replace elements |
Inspect chain/belt | Monthly | Tension/align if wearing unevenly |
Inspect wiring | 6 months | Check terminals tight; insulate wears |
Lubricate gears | 6 months | Apply grease to enclosure seals |
Calibrate sensors | Yearly | Reset clearance sensors; check analog signals |
Check foundation | Yearly | Re-grout mounting pads as required |
Station punches and dies should be examined for cracking or uneven wear monthly. Lubricate punch actuators and guides. Sharpen/replace excessively worn inserts.
Keep machine clean by removing metal chips, oil buildup. Back up PLC recipes and HMI settings regularly. Schedule preventative maintenance during production breaks to minimize downtime.
How to Select a China Wall Angle Roll Forming Machine Factory
When researching manufacturers, here are key selection criteria:
Consideration | विवरण |
---|---|
Product Quality | Reliable operation for 2 shifts minimum daily |
Forming Accuracy | Within 0.5mm tolerance for web height, angles |
Roll Tooling | Quick change stations; hardened inserts |
Production Speed | 10+ meters/minute feed rate |
Safety | CE marked; 2-hand operation; E-stop |
Programming | Simple profile loading; customization |
Commissioning Support | Virtual and on-site debugging |
Maintenance | Parts inventory and upgrade kits |
Pricing | Competitive pricing 20-40% below European brands |
Lead Time | Under 20 weeks preferred |
Payment Terms | 30% deposit; 70% before shipment |
Request 2-3 references from prior customers shipping similar products to validate performance claims. Compare warranty terms between suppliers as well. Opt for manufacturers able to deliver reliable, heavy-duty equipment rather than lowest bidders.
Pros and Cons of China Wall Angle Roll Forming Machines
Like any industrial equipment, China angle roll formers have tradeoffs versus alternatives:
Pros | Cons |
---|---|
Cost effective forming solution | Not as precise as pressed angles |
Flexible profile customization | More maintenance than press brakes |
Small footprint for production | Expensive quick die change upgrade |
High outputs up to 1000 kg/hr | Seasoning required for max uptime |
Proven technology | Training needed to program profiles |
Add curling, punching easily | Not suited for short production runs |
The automated roll forming approach is ideal for long production runs where the same profile is made for years. Operators with press brake experience may find the programming learning curve steep initially. Allow for seasoning time when commissioning.
Pyramid type rollers offer deepest draw heights around 300 mmm versus step or combo machines limited to under 200 mm typically. Evaluate serviceability – are common wear items standardized and modular? Curling and hole punching may seem unnecessary options upfront but prove useful for expanding product range down the road.
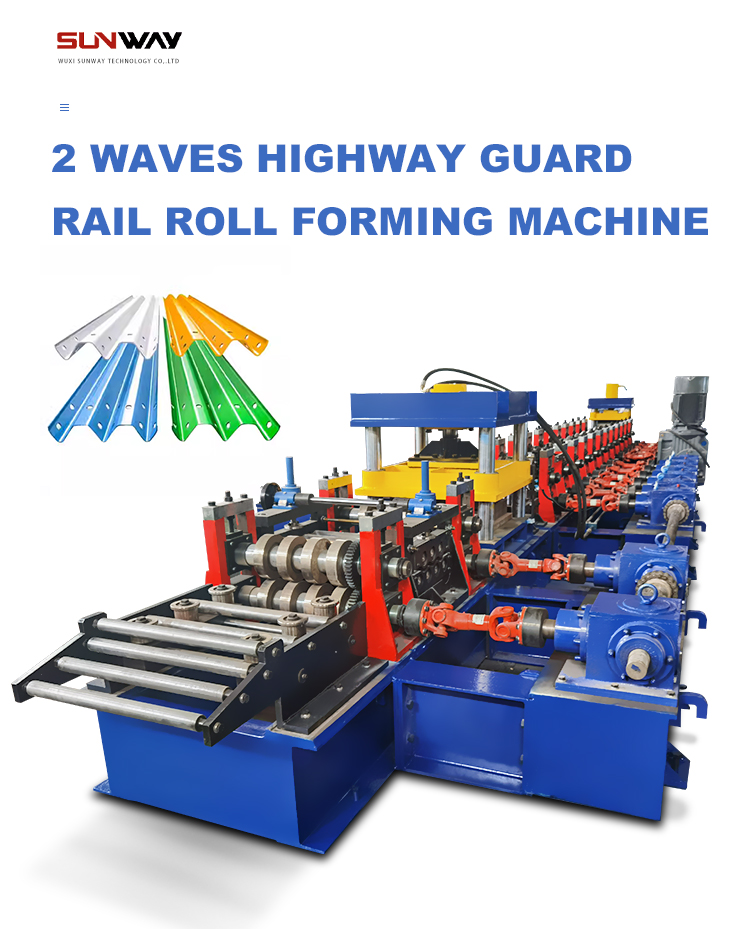
सामान्य प्रश्न
Q: What thickness of mild steel can China angle rollers form?
A: Up to 3 mm thickness SPCC/DX51/SGCC grade steel is rated for most pyramid 12 station rollers. More powerful 25 ton servo hydraulic machines can do 5mm plate.
Q: Can I make equal or unequal leg angles?
A: Both equal leg and unequal leg angles are possible by adjusting the upper/lower roll dies inward or outward.
Q: What is the max angle length produced?
A: Around 5 meters max linear length. Restricted by exit roller tables.
Q: Can the same machine make different types of sections?
A: Yes – just swap out the modular tooling cassette at each station to produce different profiles.
Q: What accuracy can I expect for formed angles and channels?
A: Within +/- 0.5mm is standard for web dimensions on properly seasoned machines. Precision to 0.2mm possible for select high end manufacturers. Depends on steel thickness and complexity of profile as well.
Q: How long does it take to changeover profile tooling?
A: Around 35-90 minutes for experienced technicians. Quick change systems can reduce this to under 15 minutes.
Q: What is the standard power supply?
A: 380V, 50 Hz, 35 kW is typical. 480V 60Hz available as well for North America. Consult your electrician.
Q: Can 1 machine make both wall panel and solar mounting profiles?
A: Yes. Some China Wall angle rollers feature both pyramid and step stations to produce panels plus angular components.
Q: How much area does the angle roll former require?
A: Around 6×4 meters. Allow 3 feet workspace around for safe operation and maintenance access.