The world of metal fabrication is a symphony of machinery, each tool playing a crucial role in transforming raw materials into the building blocks of our lives. C profile making machines, also known as purlin roll forming machines, are vital instruments in this orchestra, responsible for shaping metal sheets into the distinctive C-shaped profiles that find applications in everything from construction to infrastructure.
But just like there’s a guitar for every genre, there’s a C profile making machine for every need. This guide delves into the different types of C profile machines available, their functionalities, and the applications they excel in, empowering you to make the perfect choice for your project.
Function, Applications, and Benefits
Imagine a metal channel with a flat web and two flanges jutting out at right angles – that’s the essence of a C profile. C profile making machines take sheets of metal, typically steel, and precisely bend them into this C-shaped form using a series of rollers. These rollers progressively shape the metal, ensuring consistent and accurate profiles throughout the production run.
C profiles boast a long list of applications. In construction, they serve as lightweight yet robust purlins, supporting roofs and wall cladding. Imagine the metal framework of a building – the C profiles act as the skeletal support system, holding everything together. They’re also instrumental in creating door and window frames, trusses, and even furniture components. Their versatility extends beyond construction, finding uses in automotive parts, agricultural equipment, and even solar panel mounting systems.
The benefits of using C profiles are numerous. They offer exceptional strength-to-weight ratio, meaning they’re incredibly sturdy for their weight. This translates to efficient use of materials and cost savings. Additionally, their C-shaped design provides excellent rigidity, making them perfect for applications requiring structural support. They’re also relatively easy to install and work with, further enhancing their appeal.
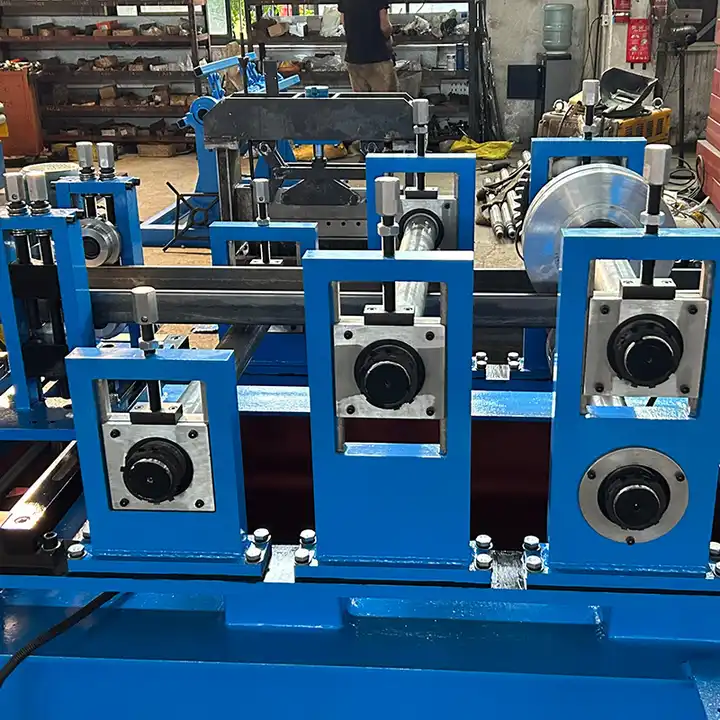
Common C Profile Making Machine Types
Now that we understand the C profile and its applications, let’s explore the different types of C profile making machines available:
- Roller Press C-Shaped Steel Forming Machine: This is the workhorse of the C profile world. It utilizes a series of rollers, each progressively shaping the metal sheet into the desired C-profile. These machines offer high production speeds, making them ideal for large-scale projects. They come in various configurations, allowing for the creation of C profiles in different sizes and thicknesses.
Advantages: High production speed, versatility in profile size and thickness.
Disadvantages: Can be complex to set up and require skilled operators.
- Hydraulic C-Shaped Steel Forming Machine: This type of machine uses hydraulic pressure to shape the metal sheet. Hydraulics offer precise control over the forming process, resulting in highly accurate C profiles. These machines are well-suited for intricate profiles or situations where tight tolerances are essential.
Advantages: Precise control, ideal for complex profiles and tight tolerances.
Disadvantages: Generally slower production speed compared to roller press machines, higher upfront cost.
- Composite C-Shaped Steel Forming Machine: This innovative machine combines the principles of roller forming and punching. It not only shapes the metal into a C profile but can also punch holes and cutouts simultaneously. This eliminates the need for a separate punching station, streamlining the production process and saving time.
Advantages: Streamlined production process, eliminates need for separate punching station.
Disadvantages: Higher initial cost compared to traditional roller press machines, may require specialized maintenance.
Key Considerations When Choosing a C Profile Making Machine:
Here are some crucial factors to weigh when selecting a C profile making machine:
- Production Volume: High-volume projects may benefit from the speed of a roller press machine, while lower-volume jobs might make a hydraulic machine a more cost-effective option.
- Profile Complexity: If you require intricate profiles with tight tolerances, a hydraulic machine might be necessary. For simpler profiles, a roller press machine would suffice.
- Budget: Roller press machines are generally the most budget-friendly option, while hydraulic and composite machines come with a higher initial investment.
- Skill Level of Operators: Roller press machines can be more complex to set up and operate compared to hydraulic machines.
Supplier & Pricing Considerations
Factor | Description |
---|---|
Supplier Selection | Identify a pool of qualified suppliers that meet your quality, capacity, and cost requirements. Research potential suppliers through online directories, industry publications, and recommendations. Request quotes from multiple suppliers to compare pricing and terms. |
Supplier Evaluation | Evaluate potential suppliers based on factors such as product quality, pricing, reliability, and customer service. Request samples to assess product quality. Check the supplier’s references and track record for on-time delivery and quality control. Evaluate the supplier’s customer service responsiveness and technical support capabilities. |
Negotiation & Contracting | Negotiate pricing, terms, and conditions with shortlisted suppliers. Clearly communicate your requirements and specifications. Aim to negotiate favorable payment terms, such as discounts for early payment or volume purchases. Review the contract carefully to ensure it outlines pricing, payment terms, delivery timelines, quality standards, and warranty information. |
Payment Terms | Establish clear payment terms, including payment methods, due dates, and discounts. Negotiate payment terms that align with your cash flow and optimize your working capital. Consider factors such as early payment discounts, credit card fees, and wire transfer costs when determining the payment method. |
Minimum Order Quantity (MOQ) | Determine the minimum order quantity (MOQ) required by the supplier. The MOQ is the smallest quantity of goods that a supplier is willing to sell in a single order. Understanding the MOQ is important for planning your inventory purchases and avoiding excess stock. In some cases, you may be able to negotiate a lower MOQ if you commit to a long-term supply agreement. |
Price Fluctuations | Consider potential price fluctuations due to market conditions, currency exchange rates, or raw material costs. Negotiate pricing models that account for potential price fluctuations, such as fixed pricing for a set period or index-based pricing that adjusts with market changes. You may also want to consider securing long-term contracts with suppliers to lock in pricing for a specific period. |
Lead Time | Understand the lead time required by the supplier to manufacture and deliver your products. Lead time refers to the time it takes between placing an order and receiving the goods. Factor in lead time when planning your inventory levels and production schedules. Reliable suppliers will be transparent about their lead times and work to meet your delivery requirements. |
Inventory Management | Develop an inventory management strategy to ensure you have sufficient stock to meet demand while minimizing holding costs. Effective inventory management involves forecasting demand, calculating reorder points, and optimizing stock levels. Consider implementing inventory management software to track stock levels and automate reorder processes. |
-
रोलिंग शटर स्लेट रोल बनाने की मशीन
-
Highway Guardrail End Terminal Forming Machine
-
Highway U/C Post Roll Forming Machine
-
2 Waves Highway Guardrail Roll Forming Machine
-
3 Waves Highway Guardrail Roll Forming Machine
-
विद्युत कैबिनेट फ्रेम रोल बनाने की मशीन
-
दीन रेल रोल बनाने की मशीन
-
दो लहरें राजमार्ग रेलिंग मशीन
-
तीन लहरें राजमार्ग रेलिंग मशीन
A Deeper Dive into C Profile Making Machine Features
Having explored the core types of C profile making machines, let’s delve deeper into the specific features that differentiate them and influence your choice:
- Roll Forming Stations: The number of roll forming stations directly impacts the complexity of the C profile a machine can produce. Simpler machines might have as few as six stations, while sophisticated models can boast upwards of twenty. More stations allow for intricate bends and shaping, ideal for profiles with flanges of varying angles or additional features like channels or grooves.
- Material Thickness Capacity: C profile making machines are designed to handle metal sheets within a specific thickness range. Typical machines can handle steel sheets from 0.5mm to 3.0mm, though some heavy-duty models can manage thicker materials. Choosing a machine that accommodates your desired profile thickness is crucial.
- Roll Material: The material of the rolls themselves plays a vital role. High-quality hardened steel rolls are the industry standard, offering durability and resistance to wear and tear. Some machines might utilize chrome-plated rolls for additional longevity, particularly when working with abrasive materials.
- Feeding and Take-Off Systems: The feeding system efficiently guides the metal sheet into the machine, while the take-off system removes the finished C profile. Automated feeding and take-off systems improve production efficiency and minimize manual handling. Look for features like adjustable feeding speeds and stacker units for longer profiles.
- Control Systems: Modern C profile making machines are equipped with sophisticated control systems. These systems allow for precise control over the forming process, including parameters like roll speed, pressure, and profile dimensions. Some advanced machines offer computer-aided design (CAD) integration, enabling the creation of complex profiles with ease.
The Importance of Branding and Customer Service
While technical specifications are essential, don’t underestimate the importance of brand reputation and customer service when choosing a C profile making machine. Established brands with a proven track record are more likely to offer reliable machines, readily available spare parts, and comprehensive after-sales support. Look for companies that provide training for your operators and have a responsive customer service team to address any technical issues that might arise.
Examples of Leading C Profile Making Machine Manufacturers:
Here’s a glimpse into some of the leading manufacturers of C profile making machines:
- Piranha Engineering: Renowned for their high-speed, user-friendly roller press machines.
- Dahlih Machinery: Offers a comprehensive range of C profile making machines, including hydraulic and composite options.
- Amada Machinery: A trusted brand known for their innovative and technologically advanced machines.
Remember, conducting thorough research on different manufacturers and requesting quotes is crucial before making a final decision.
Selecting the Right C Profile Making Machine
Choosing the right C profile making machine requires careful consideration of your specific needs and project requirements. Here’s a breakdown to guide you through the selection process:
- Identify Your Profile Needs: Determine the size, thickness, and complexity of the C profile you intend to produce. Sketching out the desired profile beforehand can be helpful.
- Evaluate Production Volume: Consider the volume of C profiles you need to produce. High-volume projects necessitate machines capable of fast production speeds.
- Budget Constraints: Be realistic about your budget and determine how much you’re comfortable investing in the machine.
- Operator Expertise: Assess the skill level of your operators. Complex machines might require more experienced personnel.
- After-Sales Support: Prioritize brands with excellent after-sales support and readily available spare parts.
Remember, the ideal C profile making machine is an investment that streamlines your production process, ensures quality output, and delivers a healthy return on investment.
Additional Considerations for C Profile Production
While the machine is undoubtedly the centerpiece, successful C profile production encompasses several other crucial aspects:
- High-Quality Metal Coils: The quality of the metal sheet you use directly impacts the final C profile. Opt for reputable steel suppliers who provide coils with consistent thickness and properties.
- Lubrication: Proper lubrication of the rolls is essential for smooth operation, minimizing friction and wear. Use lubricants specifically formulated for metal forming applications.
- Maintenance: Regular maintenance is paramount to ensure the machine’s longevity and optimal performance. Follow the manufacturer’s recommended maintenance schedule for cleaning, lubrication, and adjustments.
- Safety Measures: C profile making machines can pose safety hazards. Ensure your operators are properly trained on safety protocols and wear appropriate personal protective equipment (PPE) such as gloves, safety glasses, and hearing protection.
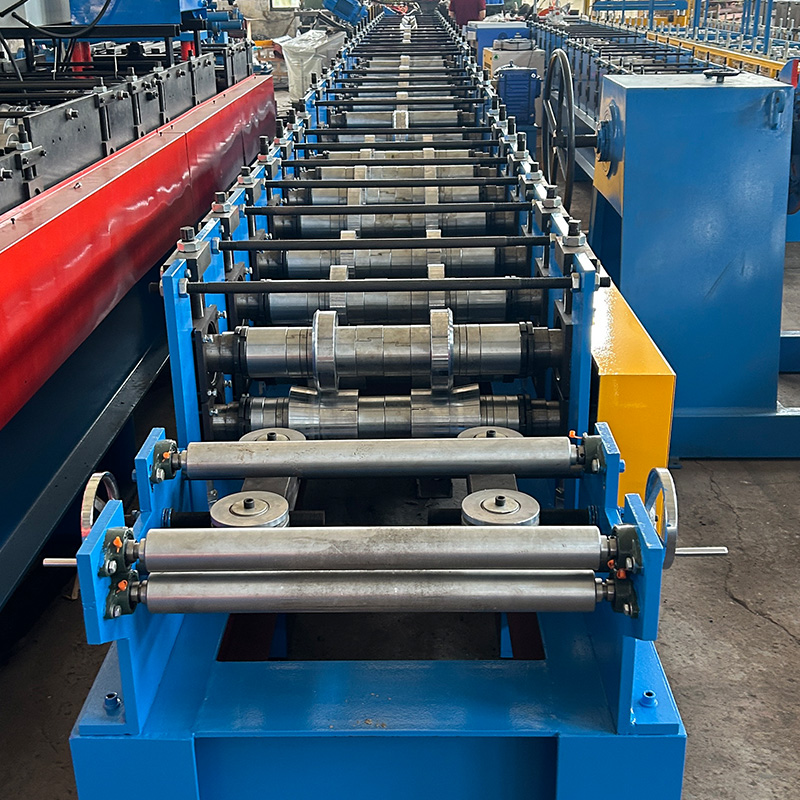
सामान्य प्रश्न
Here are some of the most frequently asked questions regarding C profile making machines, presented in a clear and informative question-and-answer format:
Q: What are the typical sizes of C profiles that can be produced by these machines?
A: The size capabilities of C profile making machines vary depending on the model. Generally, machines can produce profiles with web heights ranging from 50mm to 300mm and flange widths from 20mm to 100mm. However, some heavy-duty machines can handle profiles with larger dimensions. It’s crucial to consult the technical specifications of the specific machine you’re considering.
Q: Can these machines produce C profiles from other materials besides steel?
A: While steel is the most common material used for C profiles, some machines can handle other metals like aluminum or even high-strength steel alloys. The suitability of a machine for a particular material depends on its forming capabilities and the material’s properties. Always check the manufacturer’s recommendations for compatible materials.
Q: How much maintenance do these machines require?
A: The maintenance requirements for C profile making machines vary depending on the complexity of the machine and the frequency of use. Generally, regular cleaning, lubrication, and adjustments are necessary. Most manufacturers provide detailed maintenance schedules in their user manuals. Following these guidelines is crucial to ensure the machine’s longevity and optimal performance.
Q: What safety precautions should be taken when operating a C profile making machine?
A: C profile making machines can pose safety hazards if not operated correctly. Here are some essential safety precautions to follow:
- Proper training: Ensure all operators are thoroughly trained on the safe operation of the machine, including emergency shutdown procedures.
- Personal protective equipment (PPE): Operators must wear appropriate PPE such as gloves, safety glasses, and hearing protection.
- Loose clothing and jewelry: Loose clothing and jewelry should be avoided to prevent entanglement in the machine.
- Guarding: Always keep safety guards in place and ensure they function properly.
- Regular inspections: Conduct regular inspections of the machine for any signs of damage or wear and tear.
Q: Where can I find more information about C profile making machines?
A: Several resources can provide more information about C profile making machines:
- Manufacturer websites: Most reputable C profile making machine manufacturers have comprehensive websites with detailed information about their products, including technical specifications, brochures, and user manuals.
- Metal fabrication industry publications: Trade publications and online resources catering to the metal fabrication industry often feature articles and reviews on C profile making machines.
- Industry associations: Organizations like the American Metal Stamping Association (AMSA) or the Sheet Metal and Air Conditioning Contractors’ National Association (SMACNA) can offer valuable resources and insights.