Cable tray making machines are used to manufacture cable trays – an important component in electrical installations and industrial buildings for routing cables and wires safely. This comprehensive guide provides a detailed overview of cable tray making machine technology, working principles, types of machines available, manufacturing process, raw materials required, applications where used, cost considerations, tips for choosing suppliers, installation and maintenance procedures, and more.
What is a Cable Tray Making Machine?
A cable tray making machine, also known as a cable tray roll former, is an automated machine that forms metal coil strips into cable tray sections through a series of progressive dies and bending operations. The formed cable tray acts as a support system to safely carry electrical cables, wires, pneumatic tubing etc. in various indoor and outdoor structures.
Cable trays come in many sizes and designs – ladder type, ventilated channel type, solid channel type, wire mesh type etc. The cable tray making machine has customized dies and tooling that shape the metal coil into the desired tray configurations with great precision.
Type | Description |
---|---|
Ladder Type | Longitudinal side rails with transverse rungs resembling a ladder |
Ventilated Channel | U-shaped channel with ventilation slots/holes for heat dissipation |
Solid Channel | Enclosed U-shaped channel with no ventilation |
Wire Mesh | Trays made of wire mesh grids welded together |
Center Spine | Spine inside channel for extra support |
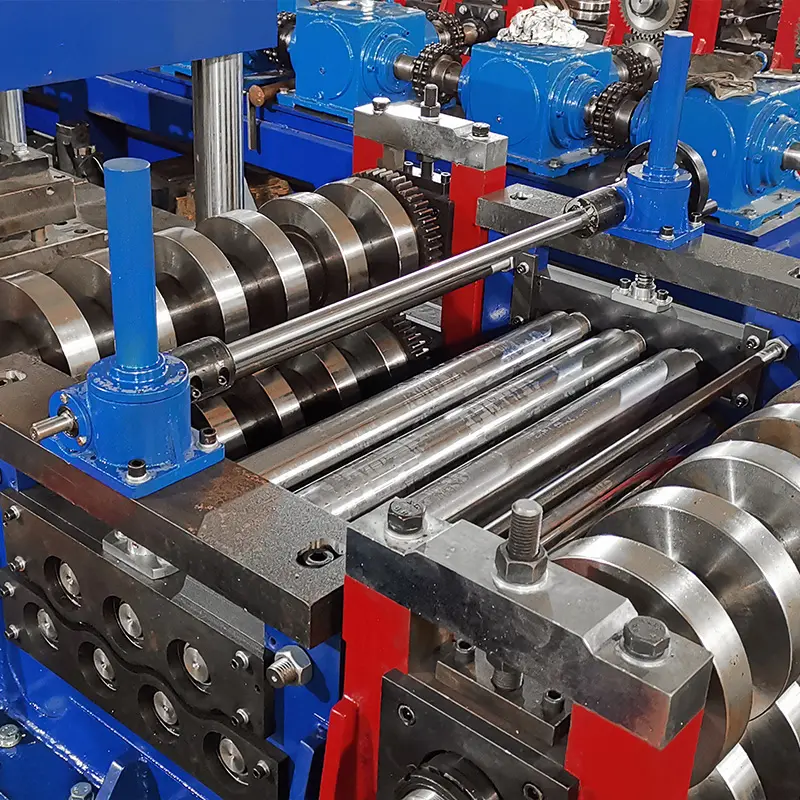
Working Principle of Cable Tray Making Machines
The working principle involves uncoiling the raw metal strip, guiding it through a series of progressing forming stations with rollers and dies to bend, cut and punch holes, finally cutting finished cable tray pieces to length.
Step | Operation Description |
---|---|
Feeding | Metal coil loaded, strip fed into machine through straightening rollers |
Forming | Forming rollers progressively bend metal into tray shape |
Punching | Dies punch ventilation holes if required |
Notching | Cutting rollers notch side rails to accept transverse rungs |
Welding | Rungs spot welded to notched side rails to complete ladder design |
Cutting | Finished cable tray cut to standard lengths |
Output | Formed cable tray pieces exit the machine |
The key components like forming stations, cutting dies, punching dies, welding electrodes etc. are customized to produce cable trays in different sizes and specifications. Advanced cable tray making machines have automated parts changing to switch manufacture different designs quick and easy.
Types of Cable Tray Making Machines
There are several types of cable tray manufacturing equipment that provide high productivity and flexibility –
1. Automatic Cable Tray Roll Forming Machine
Feature | Description |
---|---|
Operation | Fully automatic PLC-controlled machine |
Production Rate | Up to 15 meters per minute |
Roller Stations | 16-18 progressive forming stations |
Tooling | Quick changeable forming rollers and dies |
Designs Produced | All standard cable tray types and sizes |
These versatile CNC operated machines produce all types of cable trays like ladder type, solid/ventilated channel types, center spine designs etc. in one production line. Servo-electric puller feed system and rotary lateral shear provide high precision and efficiency.
2. Semi-Automatic Cable Tray Roll Former
Feature | Description |
---|---|
Operation | Semi-automatic with manual material feeding |
Production Rate | 8-10 meters per minute |
Roller Stations | 12-16 forming stations |
Tooling | Multi-profile tooling for size/design changes |
Designs Produced | Ladder type and channel type cable trays |
Economical solutions perfect for small scale production requirements. Simple mechanical controls and manual material handling reduce the overall cost. Standard forming rollers can make changes in output cable tray sizes.
3. Motorized Cable Tray Production Line
Feature | Description |
---|---|
Operation | Motorized stations but no automation |
Production Rate | 6-8 meters per minute |
Roller Stations | 10-12 forming stands |
Tooling | Fixed tooling for one tray type/size |
Designs Produced | One standardized cable tray design |
Basic roll forming lines with manual controls suitable for producing cable trays in large volumes without variety. Dedicated tooling allows high throughput of one specific design like 150mm wide solid channel etc.
4. Customized Cable Tray Manufacturing Machine
Feature | Description |
---|---|
Operation | Fully automatic customized features |
Production Rate | Up to 20 meters per minute |
Roller Stations | 20+ progressive bending stations |
Tooling | Customized for special tray designs |
Designs Produced | Non-standard and complex cable trays |
For manufacturers looking for special designs and cross-sections, customized cable tray making machines deliver unique profiles. Addition of specialized processes like center spine forming, embossing, automatic welding and cutting stations make them extremely versatile for innovative cable tray shapes. Computerized control panel allows precision repeatability for consistent quality and output. These flexible solutions have high upfront tooling investment but facilitate mass production of proprietary cable tray assortments.
-
रोलिंग शटर स्लेट रोल बनाने की मशीन
-
Highway Guardrail End Terminal Forming Machine
-
Highway U/C Post Roll Forming Machine
-
2 Waves Highway Guardrail Roll Forming Machine
-
3 Waves Highway Guardrail Roll Forming Machine
-
विद्युत कैबिनेट फ्रेम रोल बनाने की मशीन
-
दीन रेल रोल बनाने की मशीन
-
दो लहरें राजमार्ग रेलिंग मशीन
-
तीन लहरें राजमार्ग रेलिंग मशीन
Raw Material for Cable Tray Making
Cable trays are predominantly made from steel and stainless steel metal sheets and coils. Galvanized steel, aluminum sheets may also be formed into trays based on corrosion resistance required.
Material | विशेषताएँ | अनुप्रयोग |
---|---|---|
Mild Steel | Economical, strong | Indoor electrical uses |
Stainless Steel | Corrosion resistant | Outdoor/coastal areas |
Aluminum | Lightweight | Cable infrastructure |
Pre-galvanized Steel | Rustproof coating | Humid and wet areas |
The metal sheet coils need to undergo slit-edge/trimmed edge preparation for compatibility with the automated feeding mechanism of the cable tray manufacturing equipment. Coils are loaded on a de-coiler and fed into the machine for forming.
Applications of Cable Tray Systems
Cable tray systems find extensive use in industrial plants, buildings, infrastructure projects to route electrical cables and wires safely.
Application Area | विवरण |
---|---|
Power Plants | Cable routing for control wiring, instrumentation, switchgear |
Chemical Industry | Hessian wrapped cables for corrosion resistance |
Oil & Gas | Double wall trays as flame barriers |
Commercial Buildings | Service channel raceways in false ceilings |
Data Centers | Overhead racks for network cabling |
Substations | Seismic certified trays |
Cable trays provide neat accessible routing solutions for cable management critical for optimized performance and safety. Customized design and production via cable tray making machines cater to unique application needs.
How to Choose A Reliable Cable Tray Making Machine Supplier?
Choosing an established machinery manufacturer ensures a cable tray production line designed to maximize efficiency, safety and ROI.
Parameter | What to Evaluate |
---|---|
Product Portfolio | Diverse equipment range indicating advanced capabilities |
Industry Experience | Long track record of successful machine installations |
Production Facilities | Company-owned infrastructure for quality assurance |
Customization Skills | Design talent and machining versatility |
Certifications | ISO accreditations for standardized process implementation |
Service Support | Responsiveness for technical queries, maintenance etc. |
Clientele | Reputed companies already using their machinery |
Prioritize suppliers who offer customized features in standard machines and even engineer special solutions from scratch based on unique specifications. Choose manufacturers open to imparting training to operate equipment as well as modify in-house later. Long-term partnerships facilitate scaling production optimally.
Installation and Working of Cable Tray Making Machine
Proper installation by technicians ensures smooth functioning of the cable tray manufacturing line.
Site Preparation
Task | विवरण |
---|---|
Space | Allocate flat hard flooring of suitable load rating |
शक्ति | Three phase electrical connection |
Lighting | Adequate illumination for safe working |
Access | Unloading provision for machines/coils |
Machine Assembly
Task | विवरण |
---|---|
Positioning | Fix machine stands firmly |
Levelling | Use spirit levels for uniformity |
Links | Connect elementary sections |
Alignment | Precision adjust forming levels |
Trial Run | Check functioning minus load |
The supplier’s commissioning engineer will complete the installation process before handling over for production operations.
Working of the Cable Tray Making Machine
Operating the machine step-by-step:
Stage | Working Pattern | Control Mode |
---|---|---|
Loading | Position metal coil on de-coiler | Manual |
Feeding | Adjust feeder limit switches | Semi-auto |
Forming | Monitor dimensional accuracy | Automatic |
Punching | Actuate pneumatic piercing | Automatic |
Notching | Adjust depth electronic stops | Automatic |
Welding | Set weld timer/temperature | Manual inputs |
Cutting | Use shear limit switches | Semi-auto |
Collecting | Manually unload finished pieces | Manual |
The machine has manual, semi-automatic and fully automatic configured stations. Operators would initialize the process by setting parameters, loading raw material, troubleshoot errors by responding to the PLC alerts after which automated processes like forming, punching, notching, welding take over for high productivity with minimal manual intervention.
Maintenance of Cable Tray Manufacturing Equipment
Scheduled preventive maintenance enhances longevity and performance.
Activity | Frequency | Methodology |
---|---|---|
Inspection | Daily | Check for leaks, wear, damage |
Cleaning | Weekly | Blow dust, wipe visible parts |
Lubrication | Monthly | Apply grease through nipples |
Adjustment | Quarterly | Realign forming stations, hydraulics |
Overhaul | Yearly | Replace worn parts – belts, gears |
In addition to regular upkeep, qualified technicians must troubleshoot and repair issues considering equipment safety standards. Document equipment parameters during maintenance for analyzing performance.
Cost Analysis for Cable Tray Manufacturing Business
Here is an overview of the economics involved in cable tray production using roll forming machinery:
Expense Items | Indicative Cost |
---|---|
Automatic Cable Tray Machine | $35000 to $55000 |
Manual Cable Tray Machine | $15000 to $25000 |
Raw Material Coils | $2.5 to $4 per kg |
Skilled Machine Operators | $500 per month x 3 shift operators |
Maintenance Costs | $2000 per year approx. |
Factory Rental + Utilities | $1500 per month approx. |
Total Investment | $100000 to $150000 |
Cable Tray Selling Prices
Cable Tray Type | Price per meter |
---|---|
Ladder Type Cable Tray | $10 to $25 |
Ventilated Channel Cable Tray | $15 to $30 |
Solid Bottom Cable Tray | $12 to $20 |
Profit Estimation
Production Details | Indicators |
---|---|
30 days per month x 1 shift of 8 hours | 240 production hours monthly |
Output 10 meters tray/minute | 2400 meters output monthly |
Selling Price $15 per meter | $36000 sales revenue |
Raw Material Cost 20% | $7200 |
Gross Monthly Profit | $28800 |
By maximizing production volumes across shifts, strategic tray sizes and optimal pricing – cable tray making business promises good returns on investment.
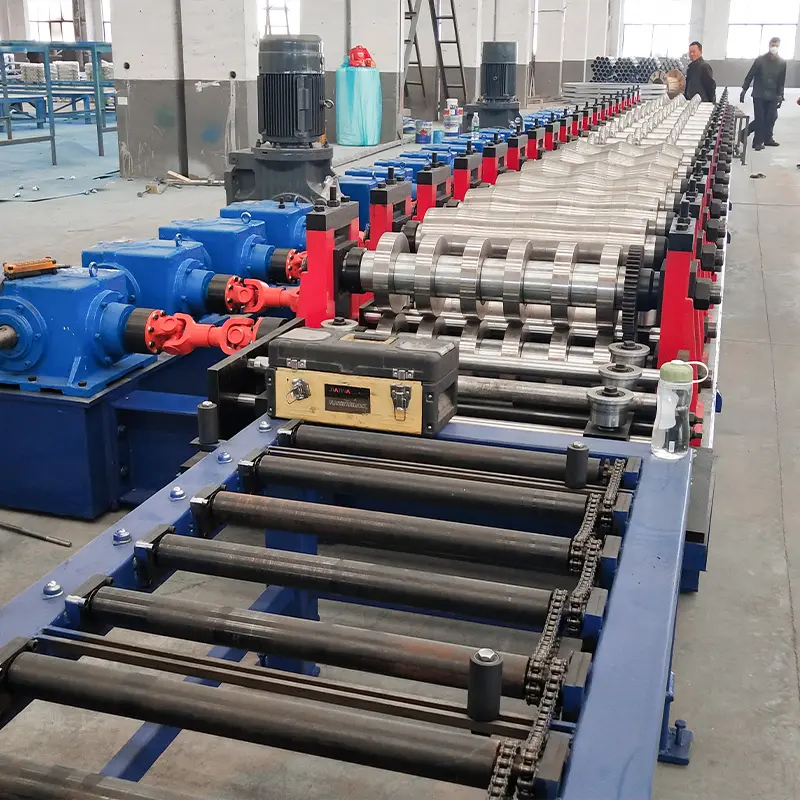
FAQs
Q: What thickness of sheets used for making cable trays?
Cable trays are commonly produced from 1-2.5mm thick HR steel sheets or stainless-steel coils. Thicker gauges provide higher load bearing strength. Choose appropriate thickness based on cable weights.
Q: What standards are cable trays manufactured to?
Cable trays conform to NEMA Ve-1 and IEC 61537 specifications covering mechanical performance, load ratings, bend radius, corrosion testing amongst other parameters. CE marking demonstrates conformity with EU directives for quality and safety.
Q: Can cable trays be bolted together for extension?
Yes, sections of cable trays can be joined together on-site using splice plates. Many manufacturers also offer hinged distribution boxes for connecting ladder type cable trays.
Q: How to determine the load capacity of cable trays?
Load capacity primarily depends on the cross-section, material thickness and supporting span length. Manufacturer test certificates detail permissible uniformly distributed load ratings that cable tray installations must follow.
Q: What accessories are used in cable tray installations?
Commonly used accessories include horizontal and vertical elbows, T and X connectors, reducers, covers, drops, risers, hinges, end caps, earth bonds, and fixation components like trapeze hangers, brackets, clamps and side rails.
Q: Can cable trays be grounded for safety?
Yes, earth continuity must be provided in cable tray systems using ): testing enables certification of integrity.