Roll forming is a metal forming process used to form metal sheets, strips, coils or blanks into various profiles or shapes. Tishken is a leading manufacturer of high quality roll forming machines used for production of metal components with complex cross-sections. This guide provides a detailed overview of Tishken roll forming machines, their types, technical specifications, applications, advantages, installation and operation.
Overview of Tishken Roll Forming Machines
Tishken roll forming machines are engineered for efficient and precise forming of metal into custom profiles for various applications. Here is a quick look at key details:
- Product – Roll forming machine
- Manufacturer – Tishken, USA
- Main Components – Uncoiler, feeder, pre-cut station, rolling mill, cutoff press
- Drive Types – Mechanical, Servo, Hybrid
- Speed – Up to 400 feet/min
- Metal Thickness – 22 ga to 1 in
- Metal Type – Carbon steel, stainless steel, aluminum
- Profile Types – Simple C, Z, U, L profiles, complex profiles
- End Uses – Solar panel frames, door frames, roofing, cladding, racking, enclosures
Tishken uses advanced technology and robust construction to maximize productivity, efficiency, precision and flexibility for high volume roll forming production.
Roll Forming Technology by Tishken
Tishken rollers and tooling are engineered for superior performance and durability. Key technologies include:
- High speed precision planetary drives for smooth operation
- Helical gearing for reduced noise and vibration
- Hardened rollers with polished finish for reduced friction
- Quick change roller box design for fast roller changeovers
- Precision machinedComponents – No uncoiler, feeder, pre-cut station, rolling mill, cutoff press and other components
Construction and Design
Tishken roll formers feature all-welded steel construction and a modular frame design for strength and rigidity. Machines are designed for:
- Heavy duty industrial operation
- Quick and easy maintenance
- Operator safety
- Minimum downtime
They utilize robust mechanical drives and industrial electric motors to handle large material load. Control panels feature customer friendly touchscreen HMI for easy monitoring. Precisely engineered components allow tight tolerances and consistent output.
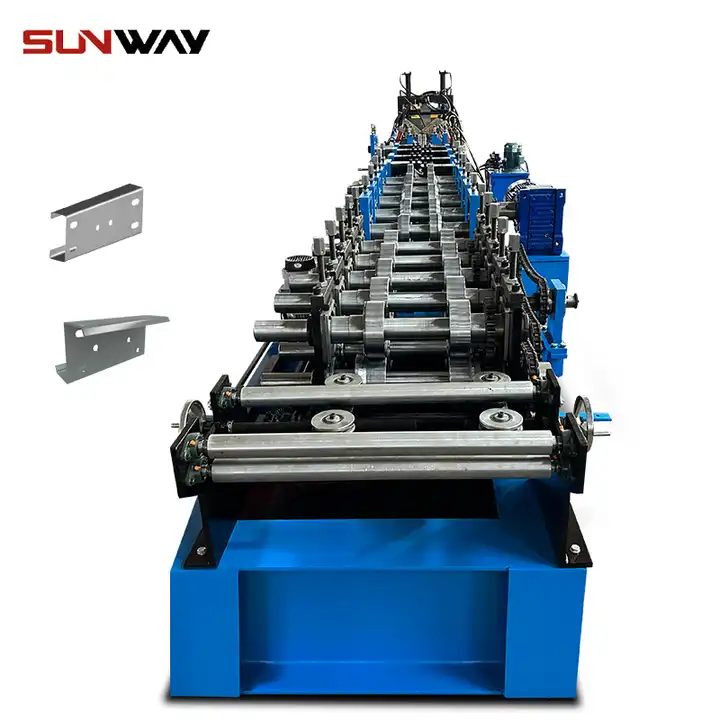
Types of Tishken Roll Forming Machines
Tishken offers a wide range of roll forming machines and customized configurations to suit specific production needs:
Roll Former Types by Drive
Roll Former Type | विवरण |
---|---|
Mechanical Drive | Geared AC motors and chain drives |
Servo Drive | Servo motors for each roller station |
Hybrid Drive | Servo motors for key stations, geared for others |
Roll Former Types by Configuration
Type | Description |
---|---|
Compact | Basic roll former with 10-12 stations |
High Speed | Higher speeds up to 400 ft/min |
Heavy Duty | For thick material up to 1 inch |
Double Head | Dual lanes for high volume |
Custom | Fully customized for special profiles |
Specialty Roll Forming Machines
Machine | Description |
---|---|
Folder | Folds profile edges |
Rotary Punch | Punches holes inline |
Hydraulic Press | Cutoff and end finishing |
Auto Stacker | Automatically stacks finished parts |
Tishken engineers analyze product design requirements and recommend the right equipment configuration for optimal productivity.
Roll Forming Machine Specifications
Tishken roll forming machines are available in different specifications based on speed, size, material thickness, drive type and other parameters as highlighted below:
Size and Speed
Spec | विवरण |
---|---|
Production Speed | Up to 400 feet/min |
Roller Size | 6 in to 26 in diameter |
Forming Length | 10 ft to 60 ft |
Material Width | 18 in to 80 in |
Material Thickness Capacity
मोटाई | Description |
---|---|
22 gauge to 16 gauge | Typical for flashing and panels |
16 gauge to 7 gauge | Standard for door frames, racks |
7 gauge to 1 inch | Heavy duty range |
Driveline Components
Component | विवरण |
---|---|
Motors | 5 HP to 20 HP AC motors |
Gearbox | Helical or planetary type |
Chains | ANSI roller chain drives |
Bearings | Heavy duty tapered or spherical roller |
Electrical Specifications
Feature | Description |
---|---|
Control Voltage | 24 VDC for servo/VFD drives |
System Bus | Ethernet/IP or DeviceNET |
Motor Control | VFD or servo drives |
Safety Features | E-stop, guarding, alarms |
Customized configurations outside standard specs are available. Engineering team analyzes requirements and recommends optimal machine design.
Applications of Tishken Roll Forming Machines
Tishken roll forming machines are versatile and can produce components for wide range of applications:
By Industry
Industry | Typical Applications |
---|---|
Solar | Solar panel frames, mounting structures |
Construction | Roofing, siding, door frames |
Automotive | Racks, brackets, chassis parts |
Appliances | Washing machine tubs, housings |
Aerospace | Aircraft interiors, enclosures |
Agriculture | Greenhouse frames, livestock equipment |
By Product
उत्पादों | Description |
---|---|
Door frames | Roll formed door jambs |
Roofing | Standing seam panels |
Cladding | Insulated metal panels |
Racking | Pallet rack uprights |
Enclosure | Electrical or equipment housings |
From simple profiles like angles and rails to complex custom shapes, Tishken roll formers can produce components for virtually any application.
Roll Forming Process Basics
Understanding the roll forming process helps appreciate machine design and productivity parameters:
- Coiled metal sheet or strip is fed into the roll former
- The strip passes through consecutive rolling stations
- Each station progressively forms the material through a series of rolling dies
- Stations can perform processes like punching, notching, cutting
- The fully formed profile is cut off at the end
- Material is formed gradually without extremes of stress/strain
Benefits of roll forming:
- Highly productive continuous process
- Consistent quality and tolerance
- Efficient material utilization with low waste
- Flexibility to change profiles with quick roll change
- Allows complex custom shapes
A key metric is feet of material produced per minute. Robust machine design by Tishken allows maximizing production speeds.
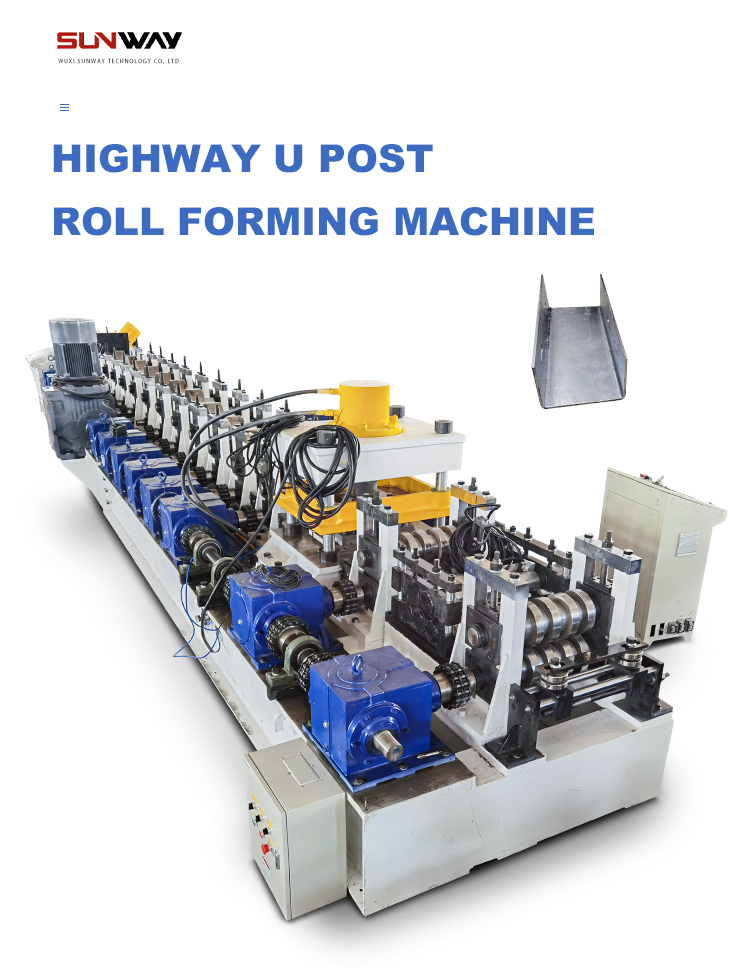
Benefits of Tishken Roll Forming Machines
Tishken roll forming equipment offers significant benefits to profile manufacturers:
Maximized Productivity
- High speed production up to 400 feet/min
- Quick roll changes in 45 minutes
- Easy operator control through touchscreen HMI
- Low maintenance due to quality components
- Minimum downtime for changeovers or maintenance
Superior Part Quality
- Advanced roller box design for precision forming
- Consistent tolerances within +/- 0.005 in
- Excellent surface finish
- Uniform mechanical properties by gradual forming
- No scratches or defects from material handling
Flexible and Versatile
- Produce simple or complex custom profiles
- Easy programming of different profiles through HMI
- Various configurations from 10 ft to 60 ft long
- Handles 22 ga to 1 in material thickness
- Suit different production volumes
Cost Effective Solution
- Compact footprint saves factory space
- Energy efficient drives reduce operating costs
- Streamlined material utilization with low waste
- High productivity lowers cost per piece
- Made in USA quality with total support
When choosing a roll forming machine, Tishken offers productivity, quality, flexibility and cost effectiveness all in one robust, reliable system.
How to Choose a Roll Forming Machine Supplier?
Choosing the right roll forming machine supplier is critical for production efficiency and end product quality. Here are key factors to consider:
Company Overview
- Many years of roll forming experience
- Full in-house manufacturing capabilities
- Strong reputation in metal forming industry
- Financially stable long-term partner
Machine Design and Construction
- Rugged all-welded steel frame construction
- Brand name industrial components
- Precision engineered for quality and tolerance
- Designed for high productivity
- Safety integrated into design
Range of Equipment Offered
- Standard and custom roll formers
- Specialty machines like folder, punch, etc.
- Line integration capabilities
- Entry level to heavy duty machines
Technical Expertise
- In-house engineering department
- Assist with tooling design
- Experience with various profiles and metals
- Provide design and product development support
Customer Service and Support
- Responsive sales and service team
- Programming support and training
- Timely technical support and maintenance
- Readily available spare parts
- Installation and start-up assistance
As an industry leader, Tishken excels in all above parameters providing a complete production solution.
Comparing Tishken with Competitors
Tishken faces competition from other established roll forming manufacturers along with some smaller regional players. Here is how Tishken compares on key criteria:
Criteria | Tishken | Competitor A | Competitor B |
---|---|---|---|
Years in Business | 60+ | 40+ | 25+ |
Manufacturing Facility | 130,000 sq ft | 100,000 sq ft | 60,000 sq ft |
Product Range | Standard + Custom | Mainly Standard | Only Standard |
Max Speed | 400 ft/min | 300 ft/min | 250 ft/min |
Max Thickness | 1 inch | 0.5 inch | 0.75 inch |
Construction | All-welded steel | Some fabricated | Mostly fabricated |
Driveline | Helical gearing | Some chain drives | Chain drives |
Design Experience | All profiles | Mainly standard shapes | Standard shapes |
Technical Support | Full engineering team | Limited | Limited |
Spare Parts | Large inventory | Average inventory | Long lead times |
Tishken clearly leads competitors on parameters like speed, thickness capacity, construction quality, design experience and customer support. Tishken’s all-welded heavy duty construction also ensures longer equipment life versus fabricated machines.
While Competitor A also has good capability, their max thickness capacity is lower at 0.5 inches only. Competitor B has lower maximum speed of 250 ft/min and limited design experience beyond standard profiles.
Roll Forming Machine Pricing
Cost of a roll forming machine depends on its size, configuration, speed, material capacity and other features. Here is an overview of price range:
Standard Roll Forming Machines
Machine Type | Price Range |
---|---|
Compact Mechanical | $75,000 to $150,000 |
Servo Hybrid | $150,000 to $250,000 |
Heavy Duty | $200,000 to $400,000 |
Custom Roll Forming Machines
- Prices start from $250,000
- Can exceed $500,000 for large custom machines
- Geometric complexity, size, material thickness, speed determine price
- Per piece price reduces with higher production volume
- Return on investment from productivity and operational savings
Additional Equipment
Item | Price Range |
---|---|
Tooling | $10,000 to $50,000 |
Hydraulic Press | $30,000 to $100,000 |
डेकोइलर | $10,000 to $50,000 |
Stacker | $5,000 to $15,000 |
Key Price Factors
- Type of drive: Servo > Mechanical
- Size: Line length, roller diameter
- Speed: 300+ fpm costs more
- Material thickness capacity
- Complexity of profile shape
- Additional secondary operations
Tishken provides customized quotations based on client production needs and budget. Their team analyzes the application and recommends the optimal equipment specification.
How to Install a Roll Forming Machine
Proper installation is vital for smooth operation and maximum production. Here are key steps:
Site Preparation
- Prepare suitable foundation – concrete or steel structure
- Allow clearance around machine for material and maintenance access
- Have electric power supply available per machine requirements
- Set up proper grounding, separate from welding machines
- Ensure sufficient compressed air supply and piping
Receiving and Handling
- Unload components carefully using forklifts, cranes etc.
- Place machine components as per installation drawings
- Use appropriate chains, straps, lifting eyes for handling
Assembly
- Bolt machine frame, stands, and bases as marked
- Install drive motors, gearboxes, and chain drives
- Mount forming rollers and roller boxes
- Install electrical cabinets and wire system
- Connect hydraulics, air supply and other utilities
Commissioning
- Check all anchors, mounts and clearances
- Verify electrical, controls and drives
- Test run empty to confirm smooth operation
- Load initial tooling and material
- Debug any issues before production run
Taking time to properly install the roll former as per guidelines pays off through years of reliable production.
How to Operate a Roll Forming Machine
Operating a roll forming machine requires proper training and adherence to protocols for efficient, safe production. Key steps:
Safety Checks
- Ensure all guards and doors are in place
- Confirm E-stop, pull cords and other safety devices function
- Check electrical panel has no loose wires or issues
- Ensure no oil leaks
- Verify pneumatic pressure and air lines
- Inspect material feeding path for obstructions
- Use lockout procedures during maintenance
Startup
- Turn on main power and control power
- Set line speed through HMI panel
- Jog machine to verify correct rotation
- Set hydraulic pressure for cutoff
- Thread material through machine
Running Production
- Monitor strip feeding and tracking
- Listen for any abnormal sounds
- Watch formed profile for defects
- Periodically check roller wear
- Ensure smooth material flow to downstream processes
Changeovers
- Save existing production parameters
- Remove existing tooling safely
- Install new tooling for profile per drawings
- Adjust machine settings like speed, feed length etc.
- Run machine empty then re-thread material
- Verify first pieces meet specifications
Shutdown
- Stop feeding material into machine
- Allow running material to clear out
- Turn off main power and control power
- Clean machine and clear off cut pieces
- Close and lock electrical panel and doors
Proper operation procedures maximize output while minimizing safety risks, defects and downtime.
Maintenance of Roll Forming Machines
Regular preventive maintenance is key for trouble-free operation of a roll forming machine. Standard activities include:
Daily Maintenance
- Quick visual inspection of machine
- Check oil levels
- Verify pneumatic pressure
- Test emergency stop
- Ensure guides and stripper plates are tight
- Remove metal debris and dirt
- Lubricate chains, bearings and gears
Weekly Maintenance
- Thorough cleaning of machine
- Inspect electrical wiring and connections
- Check chain/gearbox alignment
- Verify drive key tightness
- Test coolant flow on gearboxes and motors
Monthly Maintenance
- Check roller wear and refinish contacting surfaces
- Inspect gear teeth for wear or cracks
- Verify alignment of shafts, sprockets and gears
- Grease bearings and sliding surfaces
- Check fluid quality and change if required
Annual Maintenance
- Disassemble gearboxes for inspection and re-lubrication
- Inspect and replace worn sprockets or chains
- Recondition or hard-chrome worn rollers
- Review safety devices, guards, E-stops
- Calibrate sensors, encoders and instrumentation
Proper maintenance improves safety, reduces downtime, and increases productivity. Tishken provides detailed preventive maintenance schedules for all equipment.
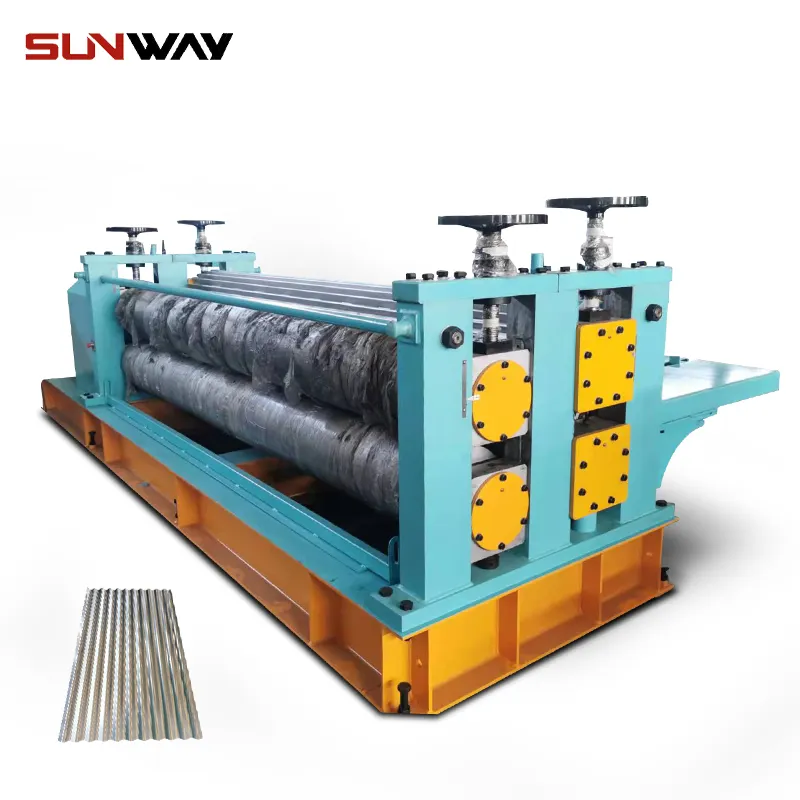
Roll Forming Troubleshooting Guide
Some common issues that can arise with roll forming machines include:
Issue | Possible Causes | Fixes |
---|---|---|
Material tracking off | Misaligned rolls, stripper plates | Realign/adjust guides, plates |
Scratched material | Dirty/scratched rolls | Clean or refinish rollers |
Roller marking | Worn rollers, roller overlap | Refinish or replace rollers |
Flared profile | Improper roll alignment | Realign forming rolls |
Dimensional deviation | Worn tooling, loose components | Replace worn tooling, tighten |
Uneven material flow | Feed speed mismatch | Adjust feed vs line speed |
Motor overload | Line jam, speed mismatch | Clear jam, align speeds |
Hydraulic oil overheating | Low oil level, leaking valve | Top up oil, replace valve |
Electrical fault | Loose connection, blown fuse | Check wiring, replace fuse |
Tishken field technicians are available for troubleshooting and repairs to minimize production downtime.
सामान्य प्रश्न
Q: How long does it take to change roller tooling on a roll former?
A: On a Tishken quick-change roll former, complete tooling changeovers can be accomplished in 30-45 minutes due to the easy access design.
Q: Can a roll forming machine make complex custom profiles?
A: Yes, an experienced supplier like Tishken can engineer roll formers to produce complex cross-sections based on customer product designs.
Q: What precision can be held on a roll formed part?
A: Tishken machines can routinely hold tolerances of +/- 0.005 in on critical dimensions through robust construction and precision components.