Steel square pipe roll forming machines are efficient and cost-effective equipment used to produce various sizes of square steel pipes. This comprehensive guide covers everything you need to know about steel square pipe roll forming machines from types, key components, technical specifications, applications, installation, operations and maintenance.
Overview of Steel Square Pipe Roll Forming Machines
Steel square pipe roll forming machine is equipment designed to roll steel strips or steel coils into square steel pipes efficiently and continuously. Roll forming is a continuous bending operation in which sheet or strip metal is progressively formed through a series of contoured roll stands into structural shapes like squares, rectangles etc.
Compared to other pipe manufacturing processes like casting or welding, roll forming is a simple process with good dimensional accuracy and requires less raw material. The formed steel pipes have high strength and uniform wall thickness. Roll formed square steel pipes are lightweight and have clean edges without welding seams.
Key advantages of steel square pipe roll forming machines:
- Highly automated and efficient production of steel square pipes
- Ability to form various pipe sizes with good tolerance control
- Low operational costs and minimal raw material wastage
- Consistent quality with uniform wall thickness and high strength
- Lower investment costs compared to other pipe making processes
- Simple design allows ease of operation and maintenance
Square steel pipes produced find extensive structural applications in construction, infrastructure, industrial, transportation sectors for scaffoldings, greenhouses, trailers, fences, road signs etc.
Main Components of a Steel Square Pipe Roll Forming Machine
A typical steel square pipe roll forming system consists of the following components:
- Uncoiling unit – Feeds raw steel strip/coil into the roll forming line. Contains decoiler machine and straightening machine.
- Feeding unit – Controls feeding of the strip, sets required line speed electronically.
- Forming stations – Series of roll forming stands with contoured rolls that progressively cold form the strip into square tubing.
- Welding unit (optional) – Joins the formed edges by welding for pipes above certain diameters.
- Cutting equipment – Cuts pipes at required lengths as per production needs. Can be flying shear, rotary shear etc.
- Haul-off unit – Drives formed pipes forward, provides precise pulling and speed control. Connected to cutting machine.
- Hydraulic system – Provides power transmission to different moving parts. Consists of pumps, valves, cylinders etc.
- Electrical control system – Computerized controls to automate production, monitor parameters and ensure safety.
- Additional units like punching, notching, bending can also be integrated as per application needs.
Proper alignment and smooth functioning of all these components is critical for quality pipe production and optimum line efficiency.
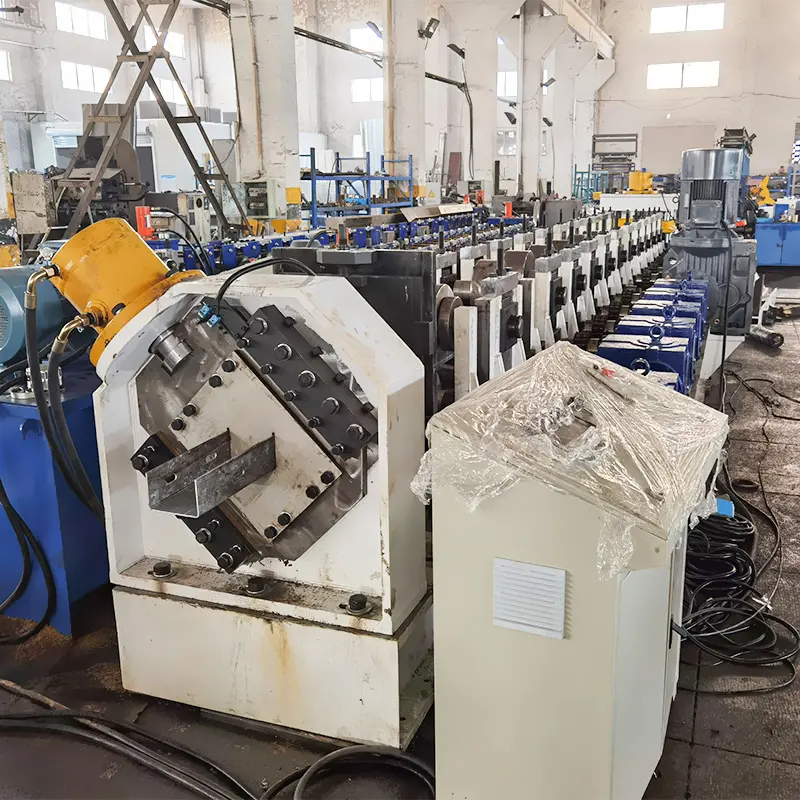
Types of Steel Square Pipe Roll Forming Machines
Steel square pipe roll forming machines can be categorized based on production speed, forming technology, automation level and customization scope:
Based on Production Speed
- Low Speed – Up to 10 m/min forming speed, manual controls, basic production up to 100-200 tons per month
- Medium Speed – 10 – 40 m/min speed, semi-automated operation, monthly capacity of 200-800 tons
- High Speed – Over 40 m/min, high degree of automation, capacity above 800 tons per month
Higher forming speeds increase production volumes and reduce per unit cost. But the machine cost is also higher.
Based on Forming Technology
- Mechanical – Traditional roll forming method with a series of stands arranged in a line. Limited size variations.
- CNC Roll Forming – Forming stations have NC control for quick size changes. Flexible production.
- Spiral Rolling – Strip is rolled along a spiral path into square pipe. Only for small diameters.
- Hydrostatic Pipe Forming – Uses fluid pressure rather than rollers to form square tubing.
CNC roll forming lines offer more automation, precision and size flexibility compared to fixed mechanical lines.
Based on Automation Level
- Manual – Requires manual loading/unloading of coils, visual inspection and control adjustments by operator.
- Semi-automatic – Auto material feed and discharge, partial automated controls, may need some manual inputs.
- Fully Automatic – Minimal human intervention needed. Automated material flow, inspection and production control. Highest efficiency.
Higher automation improves productivity, quality and reduces labor cost. But machine cost increases.
Based on Customization
- Fixed – Produces pipes of fixed sizes and specs. No variation possible. Basic, low cost machines.
- Customized – Allows changes in product dimensions and features. Flexible production but higher machine cost.
Customized roll forming lines are reconfigurable and adaptable to new product requirements.
Specifications of Steel Square Pipe Roll Forming Machines
The main technical specifications to consider while selecting a steel square pipe roll forming machine include:
Forming Capability
- Pipe sizes – Min/max width & height possible
- Wall thickness range – Normal 0.5-3 mm
- Section sizes – 20mm x 20mm to 150mm x 150mm normal
- Edge types – UOE, Pittsburgh lock seam etc.
- Materials – Mild steel, stainless steel, aluminum etc.
Production Parameters
- Max line speed – Higher speeds increase production volumes
- Max yield strength of material
- Feeding accuracy
- Length accuracy and tolerance
- Cutting precision and efficiency
Machine Layout
- Number of roll stands – 8 to 16 typical for small to medium pipes
- Roll stand type – Vertical, horizontal, pyramid etc.
- Forming stations – Required punching, notching etc.
- Configuration – In-line, C-type, S-type, spiral etc.
Automation & Control
- Servo/hydraulic drives, motors, cylinders
- PLC/computerized control system
- Sensors for monitoring – encoder, laser, ultrasonic etc.
- Level of automation – manual, semi-auto, fully auto
Power Consumption
- Main motor capacity – 7.5kw to 22kw common
- Hydraulic power – 11kw to 45kw
- Power supply – 3 phase AC; optional generator
Machine Size & Weight
- Depends on production speed, pipe diameter range
- Medium speed – 8m x 1.2m x 1.8m, weight around 4 tons
Additional Features
- Decoilers, straighteners
- Punching, cutting, beading, notching
- Haul off systems, cooling systems
- Safety protections – light curtains, e-stops etc.
Correct selection of roll former specifications based on production needs is necessary to achieve the desired pipe sizes, volumes, quality, and line efficiency.
Applications and Uses of Square Steel Pipes
The unique square hollow structure of steel square pipes makes them suitable for the following applications across various industries:
Construction & Architecture
- Scaffolding structures
- Building and roofing frames
- Structural supports
- Temporary barriers and enclosures
Decorative Purposes
- Railing and fence infill
- External decor of buildings
- Furniture tubing
Automobile/Transportation
- Chassis and trailers
- Roll cages
- Roof racks, luggage carriers
- Side steps, running boards
Infrastructure
- Road signage and street furniture
- Guard rails
- Solar module mounting
Engineering Applications
- Conveyor systems
- Crane structures
- Agricultural equipment
- Greenhouse framing
Other Uses
- Waste/water management
- Shelving and storage racks
- Gym equipment
- Heat exchangers
- Shopping cart handles
The dimensional accuracy and high strength of roll formed square steel tubes make them suitable for heavy load bearing structures across above applications. Square profile also allows easy joining and welding.
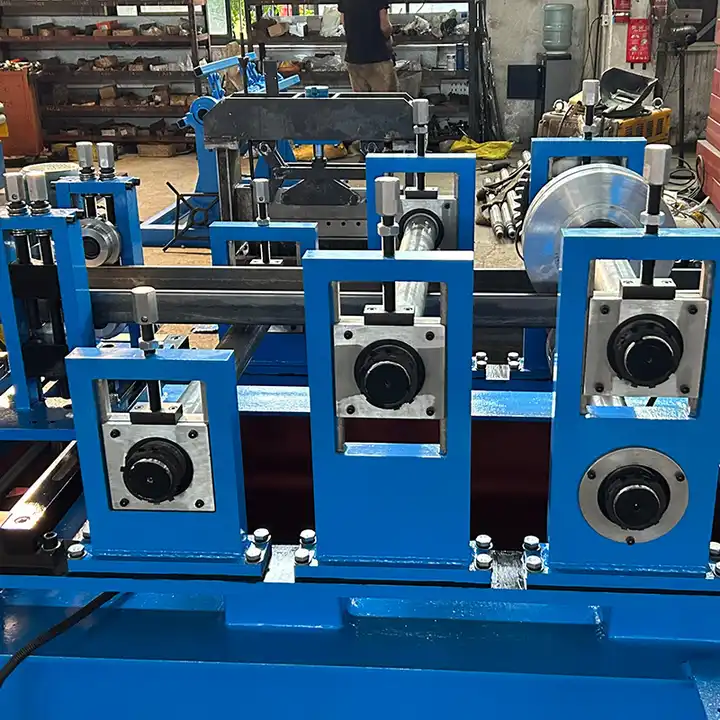
Design, Standards and Codes for Steel Square Pipes
The design of steel square pipes and roll forming lines must conform to relevant manufacturing standards and product specifications.
Key standards for reference:
- ASTM A500 – Standard specification for cold-formed welded and seamless steel square pipe
- EN 10219 – Cold formed steel square and rectangular hollow sections
- JIS G3466 – Carbon steel square and rectangular tubes for general structrual purposes
- AS/NZS 1163 – Structural square and rectangular steel hollow sections
Design considerations:
- Product dimensions – width, height, wall thickness, length
- Edge/seam type – UOE, HF welded etc.
- Steel grade and properties – yield strength, hardness etc.
- Tolerances – on dimensions, ovality, camber etc.
- Testing – pressure, bend, flattening, macrographic etc.
- Surface quality – Galvanizing, epoxy coatings etc.
Structural design factors:
- Loading – static, dynamic, wind loads etc.
- Joining methods – welding, bolting, riveting etc.
- Support conditions – column, beam, cantilever etc.
- Safety and stability – against buckling, fire, fatigue etc.
- Applicable building codes and pipe load capacity standards
The machine and tooling design must match the product design needs as per relevant standards.
Roll Forming Machine Operations
Effective and safe functioning of a steel square pipe roll forming machine requires standardized operating protocols.
Pre-Production Inspection and Checks
- Check raw material quality – surface, dimensions, properties of steel coil
- Ensure no obstacle in material flow path
- Confirm tightness of forming rollers
- Verify calibration of sensors and controls
- Apply lubrication on rotating parts
- Examine hydraulic, pneumatic systems for leaks
- Review emergency stop circuits and safety guards
- Program machine settings and parameters
Roll Forming Production Steps
- Load Steel Coil on Decoiler
- Feed strip through straightening machine
- Auto feeding of strip into first forming stand
- Cold rolling through successive stands to gradually shape strip
- Joining at welding station (if needed)
- Cutting at required length by shear
- Removing cut square pipe section
- Repeating steps 3-7 continuously
Quality Control During Production
- Monitor pipe dimensions using gauges and laser scanner
- Check surface defects and weld seam quality
- Measure geometric tolerances with laser micrometer
- Verify length accuracy as per standards
- Test wall thickness at regular intervals
- Periodic tensile and pressure testing of pipes
- Calibrate sensors and control components
Post-Production Activities
- Organize and store finished pipes
- Properly shut down machine; relieve pressure
- Clean the line and lubricate parts
- Inspect for any abnormal wear and tear
- Analyze production data for improvements
- Plan maintenance activities as scheduled
Following SOPs for roll former operation reduces safety risks and improves quality and productivity.
Maintenance of Steel Square Pipe Roll Forming Machines
A good maintenance program is essential for any roll forming system to maximize its lifetime, production efficiency and product quality.
Types of Maintenance
- Preventive – Regular cleaning, inspections, lubrication, adjustments to prevent breakdowns.
- Breakdown – Repair or replacement of components that have failed unexpectedly.
- Condition monitoring – Advanced methods like vibration analysis, oil analysis etc. to evaluate machine health.
Maintenance Activities
Daily
- Clean machine, especially around moving components
- Check hydraulic fluid level, fill if needed
- Examine all bearings, gears for abnormal temperature or noises
- Verify pneumatic system air pressure and leaks
- Inspect safety devices like pull cords, light curtains etc.
- Lubricate moving joints, applies grease if needed
Weekly
- Thorough cleaning of roll forming stands
- Tighten any loose fasteners, hardware
- Verify alignment of rolls using gauges
- Check wear on drive belts, chains; adjust tension
- Examine electrical wiring for fraying or damage
- Confirm calibration of sensors and gauges
Monthly
- Inspect machine structure for cracks or damage
- Lubricate bearings and gearboxes
- Check hydraulic filters and fluid; change if needed
- Verify proper functioning of cylinders, valves, pumps
- Check machine leveling, re-level if out of alignment
- Review emergency stops, circuits, buttons
Yearly
- Complete check of alignment, drives, and calibration
- Flush and replace hydraulic fluid, filters
- Replace worn-out rollers and bearings
- Repaint machine to prevent rusting
- Update machine lubrication chart
- Schedule major overhauls if needed
Following scheduled preventive maintenance activities minimizes unplanned downtime and improves operational safety.
Choosing the Right Steel Square Pipe Roll Forming Machine Manufacturer
Selecting a reliable and experienced roll forming machine manufacturer is key to get equipment that matches the production needs and offers maximum efficiency.
Here are important factors to consider when selecting a steel square pipe roll forming machine supplier:
Technical Expertise & Experience
- Years of experience in roll forming machines
- Expertise with steel square pipe production
- In-house design, engineering, manufacturing capabilities
- Membership of reputed industry associations
Machine Quality & Capabilities
- Use of quality materials, components
- Precision and durability of construction
- Production capacity, line speed range
- Automation, control systems, and flexibility offered
- Additional features – decoiler, cutter, bender etc.
Range of Products Offered
- Ability to supply different types of roll forming machines
- Size and profile variations possible
- Option for customized solutions besides standard machines
After-sales Service Quality
- Installation and operator training provided
- Maintenance and technical support services
- Inventory of spare parts and consumables
- Upgrades, reconditioning services offered
Pricing
- Initial purchase costs and running costs
- Cost competitiveness against competitors
- Payment terms and lead time
Compliance with Standards
- Product safety certifications
- Quality management system certification – ISO 9001
- Environmental management system – ISO 14001
Choosing a manufacturer with proven production technology, extensive experience, good service record and competitive pricing ensures acquiring an efficient and reliable steel square pipe roll forming system meeting cost targets.
Cost Analysis of Steel Square Pipe Roll Forming Machines
The price of steel square pipe roll forming equipment depends on various factors:
Specifications
- Maximum line speed and output
- Level of automation and controls
- Size range and features
- Additional accessory equipment
- Customization extent
Higher the capacity, automation level and features, higher the cost.
Construction
- Quality of components like motors, pumps, bearings
- Use of domestic or imported parts
- Machine finish and paint coatings
Production Scale
- Small scale, manual machines – $15,000 to $50,000
- Medium scale, semi-auto – $50,000 to $150,000
- Large scale, high speed lines – $150,000 to $500,000
Additional Costs
- Design, engineering charges
- Power and installation costs
- Freight and taxes
- Spare parts inventory
Supplier Type
- Reputed international brand – Higher cost
- Local or Chinese manufacturer – Lower cost
Used or Refurbished
Can save 30-50% compared to new machine cost
By opting for suitable production capacity, automation level and features, an optimum value and feature set roll forming machine can be obtained at reasonable price.
Pros vs Cons of Steel Square Pipe Roll Forming Machines
Advantages:
- High production efficiency and speeds
- Low operating costs due to automation
- Good dimensional accuracy and pipe quality
- Minimal raw material wastage
- Easy design customization possible
- Simple operation and maintenance
- Lower investment cost than alternatives
- Flexibility to change pipe sizes quickly
- Safer working than other pipe making processes
Limitations:
- High initial purchase and installation cost
- Regular maintenance and skilled labor needed
- Size range limitations depending on machine
- Not ideal for small batch or prototype production
- Larger footprint than other processes
- Frequent roll and blade changes needed for different sizes
- Noise and safety issues if not designed properly
Overall, benefits of using roll formed square steel pipes outweigh limitations for manufacturers focused on medium to high volume production.
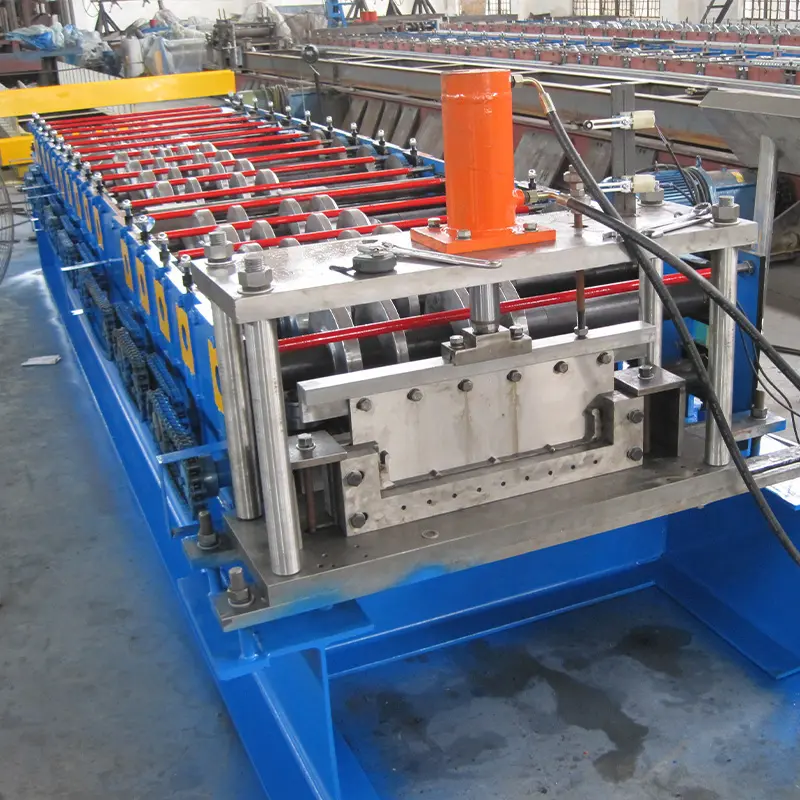
सामान्य प्रश्न
Q: What are the different edge types possible with steel square pipes?
A: Common edge types for steel square pipes are – Plain square (unfinished), UOE, Pittsburgh lock seam, welded, swaged seam, and interlocked seam. The appropriate edge finish depends on pipe size, usage of pipes and production method.
Q: What materials can be used to make square pipes besides steel?
A: Square tubes can also be produced in aluminum, copper, stainless steel, nickel alloys etc. besides carbon steel and mild steel which are most common. Each material requires specific tooling design and machine settings.
Q: What are the key factors affecting quality of roll formed square pipes?
A: Critical quality factors are steel strip quality, forming roller design, number of stands, weld seam integrity, line speed, pipe wall thickness, accuracy of shearing, and dimensional control. Proper monitoring and control of these parameters is must.
Q: How to calculate power consumption of a pipe roll forming machine?
A: Power needs depend on forming capacity, line speed, material yield strength, number of roll stands, size range and features like welding, punching etc. Approximate connected load is ~10 kW for a medium speed roll former producing small to medium steel square pipes.
Q: How to increase productivity and efficiency of a roll forming system?
A: Steps like optimizing line layout, upgrading to servo drives, automating size changeover, advanced process and machine monitoring, preventive maintenance, operator training help improve overall productivity and efficiency.