Visión general
A máquina perfiladora de chapas para tejados is specialized equipment designed to produce metal roofing sheets in various profiles, such as corrugated, trapezoidal, and standing seam panels. These machines are extensively used in construction, industrial buildings, and residential projects due to their ability to produce high-quality, durable roofing sheets with minimal waste.
Características principales
✅ Producción a alta velocidad – Produces up to 30-50 meters per minute.
✅ Customizable profiles - Soportes corrugated, trapezoidal, and standing seam designs.
✅ Precision cutting system – Hydraulic or servo-driven cutting ensures accurate sheet lengths.
✅ Durable roller materials – Uses hardened tool steel or chrome-coated rollers.
✅ PLC & CNC automation – Advanced controls for error-free operation.
In this guide, we’ll cover:
✅ Types of roofing sheet roll forming machines
✅ Cómo funciona el proceso de perfilado
✅ Best materials for roofing sheets
✅ Cost analysis & pricing guide
✅ Top manufacturers & why Sunway Machine is a trusted choice
Let’s dive in!
Tipos
Different roofing sheet profiles requiere specific roll forming machines. Here are the most popular types:
1. Corrugated Roofing Sheet Roll Forming Machine
- Produce wavy or sinusoidal roofing sheets.
- Commonly used in industrial and agricultural buildings.
2. Trapezoidal Roofing Sheet Roll Forming Machine
- Crea box-like roofing sheets with deep ridges.
- Preferred for commercial and residential roofing due to its strength.
3. Standing Seam Roofing Sheet Roll Forming Machine
- Produce interlocking metal panels that eliminate screws.
- Ideal para modern architectural and waterproof roofing solutions.
4. Glazed Tile Roofing Sheet Roll Forming Machine
- Mimics traditional clay tiles but made from chapas metálicas.
- Popular for residential and decorative roofing applications.
Máquina Sunway ofrece customized roofing sheet roll forming machines for different profiles and materials.
How Roofing Sheet Roll Forming Works
los roll forming process involves transforming a flat metal coil into a profiled roofing sheet.
Step-by-Step Roofing Sheet Roll Forming Process
Paso | Descripción |
---|---|
1. Desaceitado | The metal coil is placed on the desbobinador for feeding. |
2. Leveling & Feeding | The sheet is straightened and guided into the forming stations. |
3. Perfilado | The metal passes through multiple roller stations, gradually forming the roofing profile. |
4. Cutting & Punching | A hydraulic or servo-driven cutter trims the sheet to the desired length. |
5. Stacking & Collection | Finished roofing sheets are automatically stacked for packaging. |
Consejo profesional: A PLC-controlled roll forming machine garantiza high precision and minimal material waste.
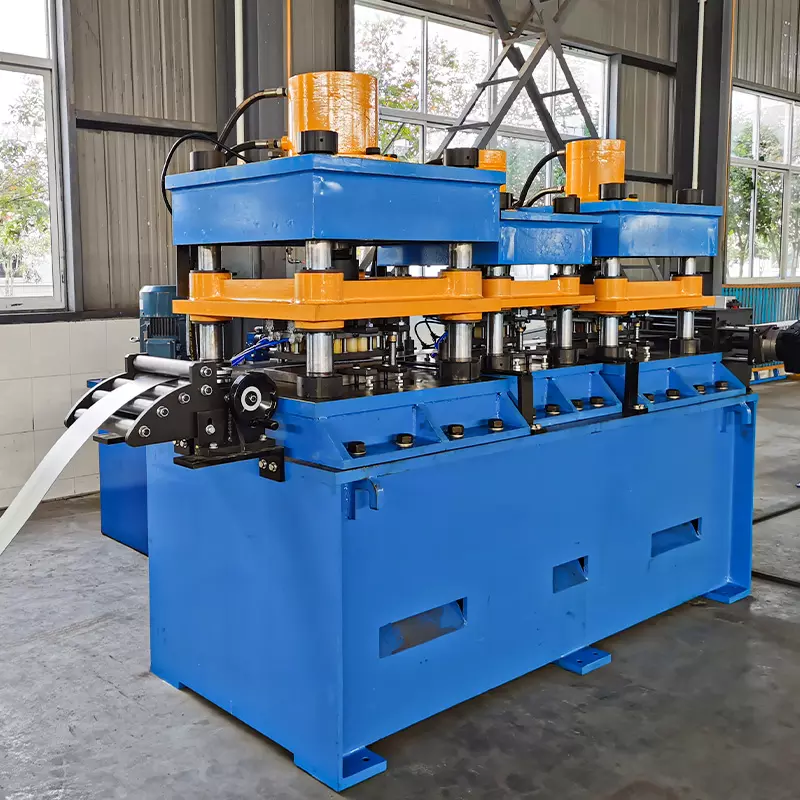
Best Materials for Roofing Sheets
Choosing the right material garantiza durability, corrosion resistance, and weatherproofing.
Comparison of Roofing Sheet Materials
Material | Propiedades | Lo mejor para |
---|---|---|
Galvanized Steel (GI) | Corrosion-resistant, affordable | Industrial & residential roofing |
Galvalume Steel (GL) | Better corrosion resistance than GI | Coastal & high-humidity regions |
Aluminio | Lightweight, rust-proof | Modern architectural projects |
Cobre | Premium, long-lasting | High-end roofing, decorative applications |
Acero inoxidable | Extremely durable & corrosion-resistant | Condiciones meteorológicas extremas |
Máquina Sunway manufactures roll forming machines compatible with all major roofing materials.
Price Guide
El coste de un máquina perfiladora de chapas para tejados depends on factors like automation level, production speed, and profile complexity.
Estimated Price Ranges
Tipo de máquina | Gama de precios (USD) | Características |
---|---|---|
Basic Manual Machine | 10,000–10,000 – 10,000–30,000 | Manual adjustments, low-speed production |
Máquina semiautomática | 30,000–30,000 – 30,000–80,000 | PLC-controlled, requires manual profile adjustments |
Máquina totalmente automática | 80,000–80,000 – 80,000–150,000 | CNC and servo motor control, high-speed production |
High-Speed Machine | 150,000–150,000 – 150,000–300,000 | 50+ meters per minute, ideal for mass production |
Looking for a custom quotation? Póngase en contacto con Sunway Machine hoy mismo.
Top Roofing Sheet Roll Forming Machine Manufacturers
Selecting a reliable manufacturer ensures high-quality machines, long-term support, and global service.
Comparison of Leading Roofing Sheet Roll Forming Machine Manufacturers
Fabricante | País | Especialización | Características principales |
---|---|---|---|
WUXI SUNWAY MACHINERY CO., LTD | China | Roofing sheet roll forming machines | Custom solutions, high-speed automation, IoT-enabled machines |
Dreistern GmbH | Alemania | High-precision metal forming | CNC-controlled machines, strong R&D |
Maquinaria Samco | Canadá | Roll forming for construction | Custom engineering, automation |
Grupo Bradbury | EE.UU. | Heavy-duty roll forming systems | Robust machines, automation-focused |
Veredicto: If you’re looking for custom, high-speed, and cost-effective roofing sheet roll forming machines, Máquina Sunway es un top choice for global buyers.
Common Problems & Solutions in Roofing Sheet Roll Forming Machines
Even with high-quality roofing sheet roll forming machines, some operational challenges may occur due to material inconsistencies, misalignment, or maintenance issues. Understanding these problems and their solutions can help improve efficiency and minimize downtime.
Troubleshooting Guide for Roofing Sheet Roll Forming Machines
Edición | Possible Cause | Solución |
---|---|---|
Sheet Warping or Distortion | Misaligned rollers or improper pressure settings | Adjust roller stations and check pressure distribution |
Inconsistent Sheet Length | Faulty hydraulic or servo cutting system | Inspect and recalibrate cutting mechanism |
Material Slippage During Forming | Loose feeder rollers or incorrect tension settings | Tighten feeder rollers and adjust material tension |
Excessive Machine Vibration | Loose bolts, unstable foundation | Secure machine components and ensure a stable installation |
Uneven Coating on Galvanized Steel Sheets | Incorrect roller pressure or feeding speed | Adjust roller settings and optimize speed |
Consejo profesional: Regular roller realignment y servo-driven adjustments improve profile accuracy by 30%.
Future Trends in Roofing Sheet Roll Forming Machines
Con Industria 4.0 and rapid advancements in manufacturing automation, roofing sheet roll forming machines are integrating advanced technology para better efficiency, precision, and cost-effectiveness.
Top Innovations in Roofing Sheet Roll Forming for 2025
1. AI-Based Quality Inspection
- Sensores con IA detect defects in real-time, reducing waste.
- Mejora product accuracy and reduces rejection rates.
2. IoT & Smart Factory Integration
- Machines are now cloud-connectedpermitiendo remote monitoring and predictive maintenance.
- Mejora production tracking and troubleshooting.
3. High-Speed Servo-Driven Systems
- Servo-controlled motors oferta better speed control and energy efficiency.
- Reduce wear and tear on moving components.
4. Automated Profile Changeovers
- Traditional machines require manual adjustments when switching profiles.
- Newer systems use CNC-driven auto-adjustments, reducing downtime.
Upgrading to AI-powered roll forming machines can increase production efficiency by up to 50%!
Roll Forming vs. Metal Stamping for Roofing Sheets
When considering roofing sheet manufacturing, businesses often compare roll forming and metal stamping.
Comparison Between Roll Forming and Metal Stamping
Característica | Perfilado | Estampación de metales |
---|---|---|
Process Type | Continuous shaping | Individual sheet punching |
Velocidad de producción | Faster for long, continuous profiles | Slower for custom single-sheet designs |
Residuos materiales | Minimal waste | Higher material usage per sheet |
Costes de utillaje | Higher initial investment, lower long-term cost | Lower upfront cost, higher per-unit cost |
Lo mejor para | High-volume production, industrial applications | Custom, low-volume roofing designs |
Veredicto: If you require continuous, high-speed roofing sheet production with minimal waste, roll forming is the better choice.
Automation in Roofing Sheet Roll Forming Machines
Automation is revolutionizing roofing sheet roll forming machines, making them smarter, faster, and more efficient.
Key Benefits of Automated Roofing Sheet Roll Forming Machines
Característica | Beneficio |
---|---|
PLC & CNC Control Systems | Ensures precise measurements and eliminates human error |
AI-Based Defect Detection | Identifies issues in real-time, reducing material waste |
IoT & Remote Monitoring | Allows operators to track machine performance from anywhere |
Automated Profile Changeover | Reduces downtime when switching between profiles |
Energy-Efficient Servo Motors | Lowers operational costs and improves sustainability |
Fully automated roofing sheet roll forming machines from Máquina Sunway improve production efficiency by up to 40%!
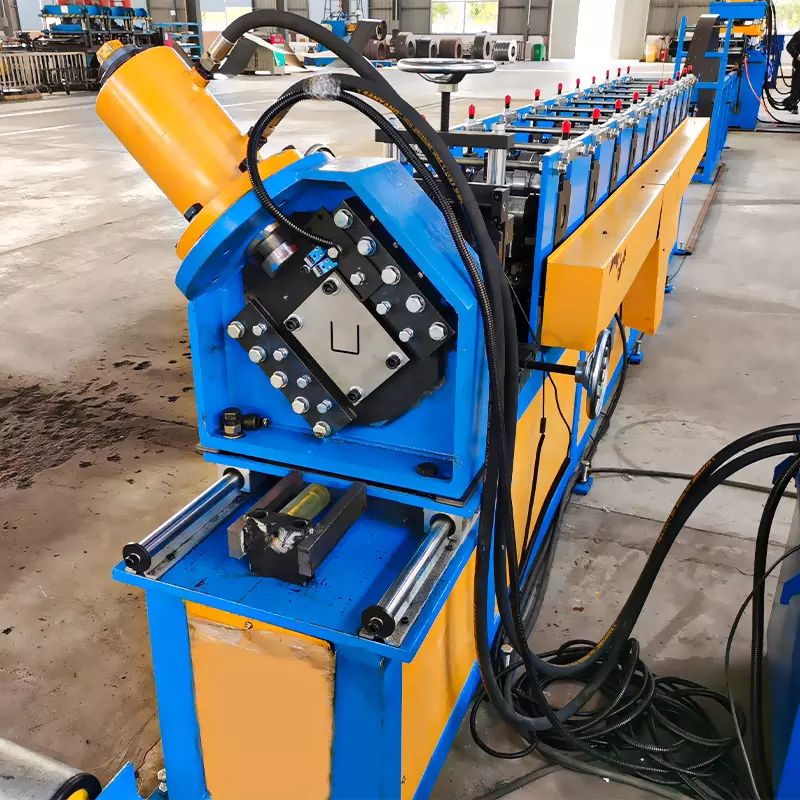
Essential Maintenance Tips for Roofing Sheet Roll Forming Machines
To ensure longer machine lifespan and uninterrupted production, regular maintenance is critical.
Maintenance Checklist for Roofing Sheet Roll Forming Machines
Tarea | Frecuencia | Propósito |
---|---|---|
Lubricate Rollers & Bearings | Semanal | Prevents wear and tear |
Check Roller Alignment | Mensualmente | Ensures accurate profile production |
Inspect Cutting Mechanism | Trimestral | Prevents defective cuts and misalignment |
Clean Machine Components | Diario | Removes dust and debris that can affect performance |
Update Software & Calibration | Semi-Annually | Keeps automation functions optimized |
Consejo profesional: Scheduled maintenance can extend machine lifespan by 50% y reduce failures by 70%.
FAQ: Roofing Sheet Roll Forming Machines
1. How fast can a roofing sheet roll forming machine produce sheets?
High-speed models can produce up to 50 meters per minuteen función del perfil.
2. What roofing sheet profiles can be produced?
Common profiles include corrugated, trapezoidal, standing seam, and glazed tile roofing sheets.
3. How much does a roofing sheet roll forming machine cost?
The price ranges from 10,000forbasicmodels∗∗to∗∗10,000 for basic models** to **10,000forbasicmodels∗∗to∗∗300,000 for fully automated high-speed systems.
4. What materials can be used in roofing sheet roll forming machines?
Los materiales más comunes son galvanized steel, galvalume, aluminum, copper, and stainless steel.
5. Where can I buy a high-quality roofing sheet roll forming machine?
Para custom-built, high-speed roofing sheet roll forming machines, visit WUXI SUNWAY MACHINERY CO., LTD.
Reflexiones finales
Invertir en un máquina perfiladora de chapas para tejados is essential for efficient, high-quality metal roofing production. Whether you need a standard or fully automated system, choosing a trusted manufacturer garantiza long-term reliability and profitability.
WUXI SUNWAY MACHINERY CO., LTD es un fabricante líder mundial de custom-built roofing sheet roll forming machines, ofreciendo advanced technology, expert support, and competitive pricing.
Want a custom roofing sheet roll forming machine? Contact us today!