ক Z purlin forming machine is an essential equipment used for roll forming metal sheets into Z-shaped purlins. Purlins are structural members used in metal buildings and roofing systems to support roof and wall panels. This guide provides a comprehensive overview of Z purlin forming machines, their working, types, components, suppliers, prices, operations, and more.
Overview of Z Purlin Forming Machines
Z purlin roll forming machines transform metal coil strips into Z-shaped structural building components through a series of progressive roll forming stations. The formed Z-purlins provide an efficient and economical option for metal roof and wall purlins.
They offer high production efficiency, consistency in quality, durability, and customizability as per application requirements. Automated Z purlin machines enable high volumes of structural metal roofing components to be manufactured quickly and precisely.
The versatile equipment can produce purlins from various materials like galvanized steel, alloy-coated steel, pre-painted steel, and aluminum. Special features like Punching Units allow in-line punching and slotting on the move for bolt holes, service holes, or lifting holes on the Z purins.
The fully automated equipment provides consistency in product quality and dimensions. They require minimal manual intervention with automated features like decoiler, feeding system, Punching Units, and exit tables. Overall, it is an efficient solution for high volume production of Z-purlins.
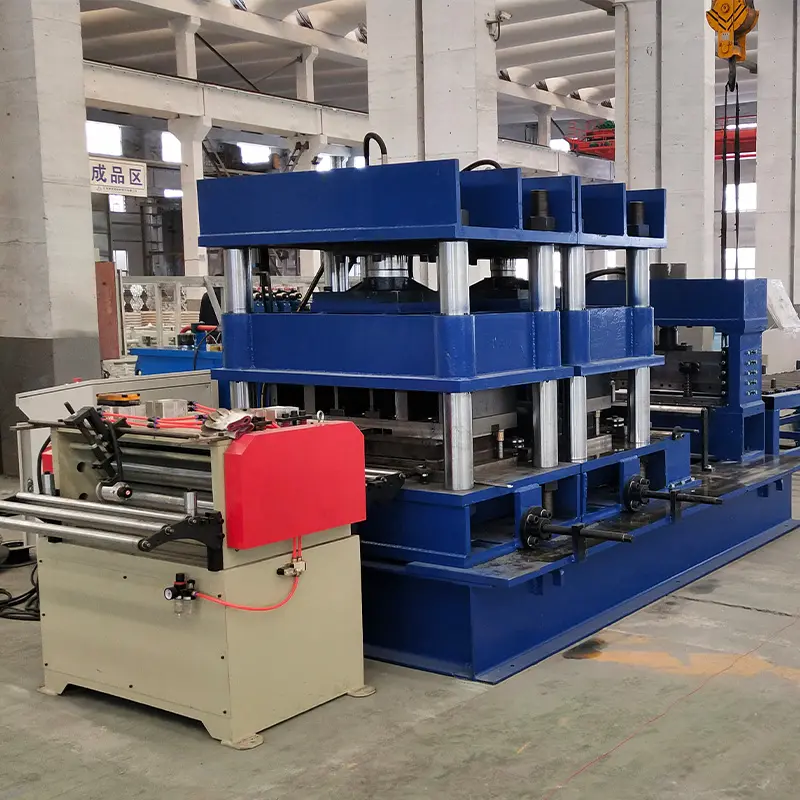
Working Process of Z Purlin Forming Machines
The working principle involves uncoiling metal strips, passing them through a series progressive roll forming stations to shape the strips into Z-sections, and cutting them to desired lengths.
The key processes are:
- Decoiling – Payoff reel equipment holds the metal coil and unroll it with an appropriate tension.
- Feeding – Feed rollers grip the strip and pull it through the different stations smoothly.
- Forming – Forming stations with custom upper/lower rolls progressively cold form the metal into Z-shape through each stand.
- Punching – Optional Punching Units with punch/die sets punch holes if needed.
- Shearing – Shearing blade slices the formed sections at preset length.
- Collection – Formed Z purlins discharged via exit tables for collection.
The line is fully automated using a centralized PLC-control panel for setting parameters, tracking production, and monitoring operations. Advanced features like servo motor driven decoiler, encoder based length control, and touchscreen HMI improve performance.
Table 2. Details of Working Process Steps
Process | Description | Control Method |
---|---|---|
Decoiling | Payoff reel holds coil, feeds strip at set tension | Servo motor or brake motor |
Feeding | Feed rollers grip and pull the strip | Servo motor driven |
Forming | Custom upper/lower rolls form Z shape through stands | Precision roll design |
Punching | Optional process to punch holes in purlins | CNC positioning |
Shearing | Cuts formed sections at preset length | Encoder or length sensor |
Collection | Exit tables to safely collect formed Z purlins | Exit roller conveyor |
Types of Z Purlin Forming Equipment
Z purlin roll forming lines are available in standard and customizable configurations:
1. Standard Z Purlin Lines
- Pre-engineered models with fixed speed and output
- Cost-effective for regular Z purlins in standard sizes
- Limited customization possible
2. Customized Z Purlin Lines
- Custom-built as per required sizes and features
- Highly configurable for parameters
- Advanced automated features for high precision
Table 3. Comparison between Standard and Customized Z Purlin Machines
Parameter | Standard Lines | Customized Lines |
---|---|---|
গঠন গতি | Fixed standard speed | Customizable/Higher speed |
Output range | Up to 18,000 pieces/shift | Higher capacity possible |
Control features | Basic controls | Advanced automation (PLC/servo) |
Customization scope | Limited | Highly customizable |
Special features | Not available | Possible (ex: Punching Unit) |
Price | Economic | Higher cost |
Leading manufacturers offer both standard as well as engineered solutions to meet demands in terms of speed, accuracy, and flexibility. Customized lines allow incorporating additional processes like hole punching or embossing if required.
Both kinds of Z purlin roll formers provide quality, efficiency and reliability. Choice depends on production needs, budget, customization needs, and expansion scope.
Main Components of Z Purlin Forming Machines
Z purlin lines comprise various modules functioning collaboratively for the roll forming process. The key components are:
1. Decoiler
- Also called as payoff reel
- Holds metal coil and supplies strip to feeder
- Types: Manual, Hydraulic, Servo Motor, etc.
2. Feeder
- Grips and feeds metal strip into the forming sections
- Ensures smooth feeding without slippage
- Types: servo motor or geared motor
3. Forming Stands
- Progressive stands with custom roll sets
- Each stand forms the strip further into Z shape
- Number of stands based on final shape
4. Punching Unit
- Optional CNC powered punch and die sets
- For punching holes as per profiles
5. Shearing Unit
- Cuts formed metal Z profiles at set length
- Types: Hydraulic, Servo Electric, etc.
6. Control System
- Automates line parameters, tracking and operation
- Uses PLC, HMI touchscreen, sensors, servo drives
7. Supporting Tools
- Entry guides, brackets, exit tables, etc.
- For safe functioning of metal strips
Table 4. Technical Details of Key Components
Component | Functions | Types | Control |
---|---|---|---|
ডিকয়লার | Uncoils metal coil | Manual, Hydraulic, Servo | Motor drive |
Feeder | Feeds metal strip | Geared, Servo motor | Motor drive |
Forming Stands | Progressively forms Z shape | Custom roll sets | Precision rolls |
Punching Unit | Punches holes if needed | Hydraulic, Servo Electric | CNC positioning |
Shearing Unit | Cuts at pre-defined length | Hydraulic, Servo Electric | Encoder, PLC logic |
নিয়ন্ত্রণ ব্যবস্থা | Automates and monitors process | PLC + HMI + Drives | Program logic |
These components offer flexibility to design customized lines as per specific production needs in terms of speed, hole punching, and other parameters.
-
দ্রাক্ষাক্ষেত্র পোস্ট রোল ফর্মিং মেশিন
-
স্বয়ংক্রিয় আকার পরিবর্তনযোগ্য সিগমা Purlin রোল ফর্মিং মেশিন
-
স্বয়ংক্রিয় আকার পরিবর্তনযোগ্য CZ Purlin রোল ফর্মিং মেশিন
-
স্বয়ংক্রিয় আকার পরিবর্তনযোগ্য Z Purlin রোল তৈরির মেশিন
-
Auto Size Changeable C U Purlin Roll Forming Machine
-
সি সেকশন ব্রেসিং ওমেগা স্টোরেজ র্যাক খাড়া পোস্ট রোল ফর্মিং মেশিন
-
স্টিল বক্স প্লেট মেকিং রোল ফর্মিং মেশিন
-
বক্স মরীচি স্টীল রোল শেল্ফ কলাম জন্য মেশিন গঠন
-
প্যালেট র্যাকিং স্টেপ বিম পি বিম রোল তৈরির মেশিন
Working Principle and Process Flow
The working principle of Z purlin roll forming machines involves continuously transforming metal strips into Z profiles through a series of stands with configured rolls.
The forming process flow is:
- Decoiler holds coil of steel/aluminum strip
- Strip fed into first forming stand via feeder
- First stand initiates bend on the strip
- At each subsequent stand, bend increased progressively
- Final few stands complete Z shape purlin profile
- Punching Unit punches holes if specified
- Shearing Unit cuts purins at fixed length
- Formed Z purlins discharged via exit tables
During the process, parameters like forming angles, feed speed, cut length, hole patterns are precisely controlled via the automation system and drives. Advanced features like servo motor controlled recoiler and quick changeover roll sets make the process efficient. The lines can operate continuously with minimum downtime for high productivity.
Industrial Applications of Z Purlins
Table 5. Major Application Areas of Z Purlins (Cont.)
Segment | Specific Applications |
---|---|
Building Construction | – Warehouses – Factories – Commercial buildings – Residential roofing |
Infrastructure | – Steel plants – Power plants – Metro rail shed roofing |
Agriculture | – Grain storage sheds – Farm equipment roofing |
The light weight yet high strength Z purlins are valued across construction industry for longevity and safety. Galvanized or color-coated Z purlins provide corrosion resistance and aesthetics demanded in metal buildings. They significantly reduce building costs and construction schedules versus traditional methods.
Being customizable sections, Z purlins suit diverse structural and load requirements in factories, warehouses, plant buildings, retail spaces, shelters, etc. Special roll formed shapes with lips/cleats provide additional load bearing capacity. Their easy integration with roof sheets, rafters etc. makes installation faster.
Hence automated Z purlin roll forming lines enable mass production of these structural building components to meet rising infrastructure needs cost-effectively.
Design Aspects of Z Purlin Sections
The design of Z purlin sections and dies is specialized work based on:
1. Loading needs
- Dead and live loads as per building norms
- Wind uplift loads based on roof area/geography
- Seismic load considerations in earthquake zones
2. Structural mechanics
- Static structural analysis
- Beam stress distributions
- Load span capacities
- Deflection limits
- Column buckling checks
3. Manufacturing feasibility
- Metal sheet type and grades
- Cold roll forming method constraints
- Process lubrication needs
- Mill capability for tensioning etc.
4. Construction needs
- Roofing integration requirements
- Bracing provisions with rafters
- Compatibility with sheeting profiles
The profile geometry, dimensions (height, flange width, lip size) and thicknesses (gauge) are finalized based on these factors. Custom roll dies are engineered to form the exact shape through computerized simulations. Correct die design ensures uniform material flow into the Z configuration.
Table 6. Typical Design Factors for Z Purlin Sections
Parameter | Typical Range |
---|---|
Height | 50 – 300 mm |
Flange width | 30 – 80 mm |
পুরুত্ব | 1.5 – 3 mm |
উত্পাদন শক্তি | 300 – 550 MPa |
Cleat/Lip length | 5 – 15 mm |
The forming process imparts strength and rigidity to the roll formed sections. Taller or heavier Z purlins may require additional reinforcement using internal stiffeners. Embossing the surfaces provide added structural rigidity.
Overall an optimal design balances strength, stability, weight, and cost economics specific to building needs.
Customization and Special Features
Z purlin production lines offer standardization as well flexibility through customizable features:
1. Size Customization
- Height, width, thickness, length changes
- New die sets engineered easily
2. Feature Addition
- Hole punching unit integration
- Special embossing
- Length cutting or slotting
3. Process Automation
- Advanced controls for precision
- Data logging, analytics features
- Remote monitoring provisions
4. Secondary Operations
- Integration with galvanizing kettle
- Weathering/powder coating line
5. Accessory Equipment
- Infeed or outfeed tables
- Stacking arms for finished products
- Conveyor systems for automation
Such flexible equipment enables manufacturers to stay competitive through rapid product innovations, quality enhancement, or productivity improvements.
Suppliers and Price Range
Z purlin roll forming equipment is available from:
1. OEM manufacturers
- Specialized in manufacturing the machines
- Offer complete system guarantee
- Provide support for maintenance
2. Authorized dealers
- Sell on behalf of OEMs
- Interface for ordering and coordination
- Assist in installation and training
There are reputed manufacturers in China, India, Turkey, Europe and USA. Choice depends on relationship, price value, and local presence.
Table 7. Indicative Price Range of Z Purlin Making Lines
Speed (pieces/hr) | Price range |
---|---|
Up to 2000 | $40,000 – $60,000 |
2000 – 4000 | $60,000 – $150,000 |
4000 – 7000 | $150,000 – $250,000 |
Above 7000 | $250,000 – $500,000 |
Higher automation and customization increase costs. Large players offer financing options. Overall excellent return on investment is achievable through higher efficiency and consistency.
Installation and Commissioning
Installing Z purlin roll forming systems requires:
Table 8. Installation Procedure for Z Purlin Forming Machines
Stage | Activities |
---|---|
Site Preparation | – Level concrete foundation – Working platform for operators – Electrical supply line readied |
Unloading | – Use forklifts/cranes to unload parts safely |
Positioning | – Assemble machine as per drawings – Align forming stands perfectly |
Connections | – Make hydraulic, electrical, pneumatic connections |
Trial Runs | – Feed dummy strips to test operations – Ensure smooth strip flow without issues |
Manufacturer’s engineers commission the line by configuring the control system, drives, and relevant parameters as per product needs. They demonstrate full functioning and train the operators. Proper installation and commissioning ensures long working life for the machine.
Operations and Working
Smooth functioning of Z purlin roll forming lines requires:
1. Operator training
- Control panel operations
- Safety procedures
- Coil loading/unloading
2. Parameter setting
- Forming angles station-wise
- Feed rate, cutoff length
- Hole punching patterns if applicable
3. Roll pass maintenance
- Cleaning roll surfaces
- Applying lubricants
4. Schedule maintenance
- Inspecting bearings, cylinders
- Hydraulic system checks
Table 9. Typical Production Operation Steps
Step | Operation | Control |
---|---|---|
1 | Load metal coil on decoiler | Set tension/alignment |
2 | Thread strip through stations | Jog switches |
3 | Start cycle as per settings | PLC automated |
4 | Monitor strip flow | Visual checks |
5 | Unload panels via exit table | – |
The forming process is clean and quiet. Daily production logs help optimize configurations. Proper working methods and upkeep result in maximum machine availability.
Maintenance Aspects
The maintenance checklist covers:
1. Forming rolls
- Surface wear inspection
- Lubrication application
- Alignment checks
2. Hydraulic system
- Checking leaks
- Topping up oil levels
- Hose and valve inspection
3. Electrical system
- Control panel cleaning
- Wire/cable checks
- Sensor/drive functioning
4. Structural frame
- Tightening loose nuts/bolts
- Greasing bearings
- Wear checks in moving parts
Table 10. Recommended Maintenance Schedule
Item | Frequency | Method |
---|---|---|
Forming rolls | Monthly | Cleaning and lubricating |
Hydraulic oil | 15 days | Checking level + topping up |
Wear parts | Quarterly | Inspection and replacement |
Drives | Half yearly | Testing and tuning |
Structural frame | Yearly | Cleaning and tightening |
Preventive maintenance as per schedule is vital for maximizing working life and minimizing downtimes.
Choosing the Right Z Purlin Machine Supplier
Selection of Z purlin roll forming line supplier based on:
1. Product quality
- Material quality certificates
- Tested structural properties
2. Design and engineering competence
- Use of CAD and simulations
- Roll pass expertise
3. Production capability
- Installed capacity for demand
- Inventory of key bought-outs
4. Commissioning support
- Installation service
- Operator training efficiency
5. Responsiveness and availability
- Turnaround on inquiries
- Lead time and delivery track
6. Upgrades and maintenance
- Ease of upgrades/retrofits
- Maintenance team responsiveness
A supplier well-rated on these aspects inspires long term confidence for partnership. Site visits to existing customers help assess competencies. Support relationship matters especially for custom engineered products.
Pros and Cons of Z Purlin Roll Forming
Table 11. Advantages of Z Purlin Roll Forming
Benefits | বিস্তারিত |
---|---|
High productivity | – Automated forming at high speeds – Mass production ability |
Material savings | – Up to 20% savings versus hot rolling |
Flexible sections | – Custom profiles as per design needs |
Consistent quality | – Precision forming every time |
Value engineering | – Integral stiffeners possible – Weight optimization |
Versatile usage | – Roofing, walling, structures |
Ease of construction | – Light sections for faster fitting |
Table 12. Limitations of Z Purlin Roll Forming
Constraints | বিস্তারিত |
---|---|
High tooling cost | – Die set for each new profile |
Size limitations | – Width limited by coil size |
Limited strength | – May need stiffeners for stability |
Skill dependence | – Section design expertise crucial |
Roll formed Z purlins score heavily on material and building cost economies. Automation results in reliable output. However the process requires significant initial investments. Overall, choosing automated lines helps construction industry enhance quality and competitiveness.
Price Range from Different Z Purlin Machine Manufacturers
Top manufacturers of Z purlin machines offer price economical solutions:
Table 13. Indicative Pricing of Z Purlin Lines from Major Manufacturers
প্রতিষ্ঠান | Price Range |
---|---|
Company 1 | $50,000 – $100,000 |
Company 2 | $80,000 – $250,000 |
Company 3 | $100,000 – $300,000 |
Company 4 | $150,000 – $400,000 |
Pricing depends on factors like:
- Production speed and output needs
- Level of automation
- Type of raw material coils
- Addition of accessories
- Customization of features
- Quality and precision requirements
Top tier manufacturers provide configurable pricing options to balance capability and affordability. Their modular equipment allows upgrading in future. Additional discounting may be offered for large orders.
How to Choose the Suitable Z Purlin Roll Forming Machine
Choosing the optimal Z purlin production line involves:
1. Production Objective
- Required output per hour
- Operating hours per day
- Annual volume estimate
2. Product Mix
- Range of purlin sizes
- Material specifications – thickness/grades
- Feature needs – holes, stiffeners etc.
3. Budget
- Capital investment affordability
- Consider current and future needs
4. Supplier Selection
- Reviews of product quality
- Service capability
- Upgradation flexibility
5. Process Plan
- Space planning for line installation
- Manpower and operation process
The machine’s capability should match both current and upcoming manufacturing targets. A value-for-money equipment offering reliability, flexibility and support ensures success.
Future Trends in Z Purlin Roll Forming Equipment
Latest technological trends shaping Z purlin lines include:
1. Servo motor drives
- For speed, feed and automation precision
2. IoT connectivity
- For smart data capture and analysis
3. Touchscreen controls
- For efficient HMI and visual aids
4. Laser cut/punch Integration
- For high speed hole forming
5. Robotic stacking arms
- Automated sorting and stacking
6. Conveyor integration
- For movement of feedstock and finished goods
7. Modular expandable frames
- Allowing capacity extensions when needed
With relentless innovation focus, manufacturers are offering connected, data-driven, and agile Z purlin forming solutions to maximize productivity and quality.
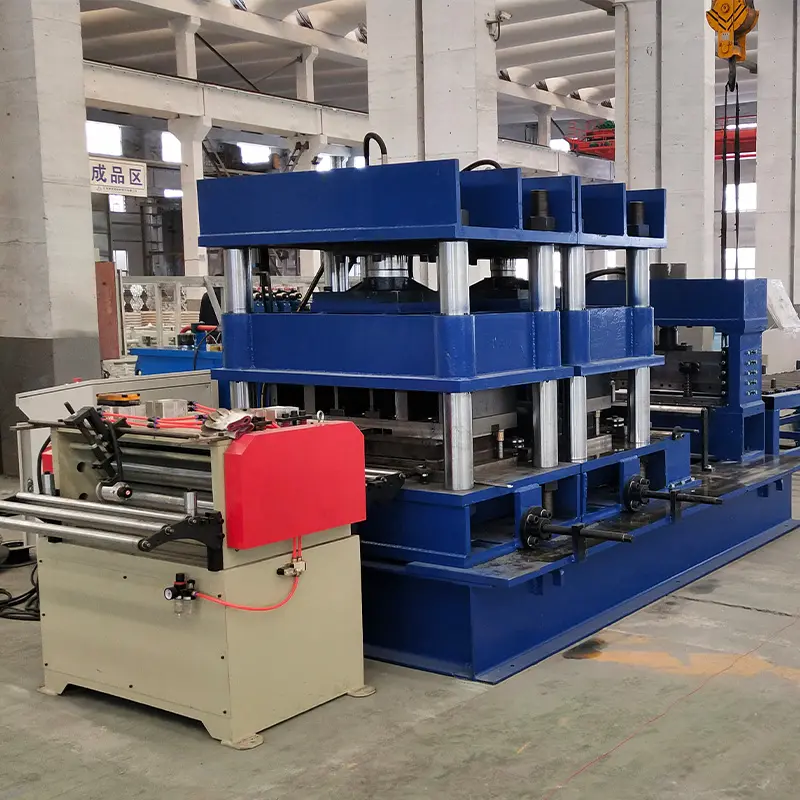
FAQ
Q1. What materials can be formed into Z purlins?
Z purlin roll forming machines can handle galvanized steel, pre-painted steel, alloy-coated steel, and aluminum coils. Hardened rolls allow extended production runs.
Q2. What is the production speed and output capacity?
Standard Z purlin lines offer upto 100 meters per minute speed with annual volumes between 1 – 3 million meters depending on hours of operation. Customized lines provide higher throughputs.
Q3. What are the regular maintenance needs?
Regular roll cleaning, lubrication, inspection of wearing parts like bearings and hydraulics, and overall machine tightening is vital for smooth production. Periodic preventive maintenance improves equipment lifetime.
Q4. What level of operator skill is needed?
Basic computer literacy helps in understanding the touchscreen machine controls for daily operation. No special skill is required as suppliers provide comprehensive training for machine working, troubleshooting and maintenance.
Q5. What factors affect the price of Z purlin roll forming equipment?
Speed, automation level, accessories, customization needs, and production volumes influence pricing. Highly automated lines above 100 m/min with special features cost higher. Large order quantities attract discount from manufacturers.
Q6. How to increase efficiency of the Z purlin forming process?
Optimizing roll pass design, usage of automated servo controls, and integrating conveyor and robotic systems improves process efficiency. Real-time data analytics also helps identify productivity areas. Overall system competence of supplier is vital.
Q7. What are the latest innovations in Z purlin roll forming equipment?
Suppliers are offering breakthrough innovations in AutoCAD roll pass design, IoT-enabled predictive maintenance, flexible manufacturing systems, and additive roll tooling for greater speed, accuracy and responsiveness to market demands.
Q8. How to minimize operational costs in Z purlin production?
Right equipment selection matching output needs, quality spare parts sourcing, preventive maintenance routines, and operator best practices helps optimize overall operating costs and maximize profitability from the Z purlin making business.