ক U profile forming machine is a type of roll forming machine used to produce U shaped metal profiles. U channels and profiles have a wide range of applications across industries like construction, infrastructure, automotive, appliances, and more. This guide covers key details about U profile forming machines.
Introduction to U Profile Forming Machines
U profile forming machines are a specialized type of রোল গঠনের মেশিন designed to transform flat metal sheets into U shaped channels or profiles. The roll forming process uses a series of rolling stations with contoured rolls to gradually shape the sheet into the desired profile through a series of bending and forming stands.
U profile rolling mills continuously form the sheet metal fed from a coil without the need for pre-cutting or pre-punching. This makes the process efficient, economical, and suitable for mass production applications. The flexible tooling allows fast changeovers to produce different sized U channels.
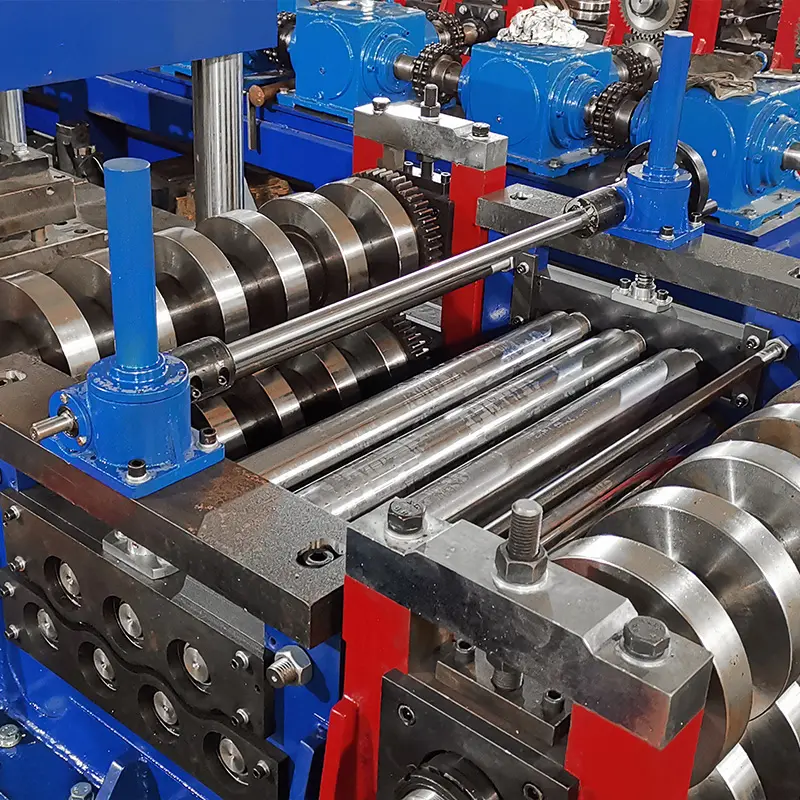
Types of U Profile Forming Machines
There are two main types of U profile forming equipment:
Type | Description |
---|---|
Manual | Basic machines for small production volumes. Require manual feeding and output of profiles. Cheaper option but labor intensive. |
Automatic | Advanced programmable machines with powered unwinding, feeding, forming, cutting. Higher outputs with less labor and monitoring needed. PLC controls allow fast profile changes. More expensive. |
Main Components of U Profile Rolling Mills
The major components of a U channel roll former include:
- Uncoiler/Decoiler: Feeds metal coil stock into the machine
- Feeding table: Transports sheet through machine
- Forming stands: Progressive stations that gradually shape the profile
- Finishing stands: Final sizing and calibration of U channel
- Cutoff device: Cuts formed profiles to desired length
- Stacking table: Collects cut U channels
Optional accessories like deburring, notching, hole punching stations can also be integrated.
Working Process of U Profile Rolling Machines
The forming process on U profile making machines follows fixed steps:
- Coil stock unrolled and fed into machine through powered or manual unwinding
- Sheet progresses through progressive rolling stations
- Contoured rolls bend metal through a series of stages
- Formed U shape profile calibrated and cut to length
- Finished U channels stacked at the exit
Advanced computerized controls precisely control each element of the rolling process.
Applications of U Profile Forming Equipment
U shaped sections produced on these machines find uses across industries:
- Construction: U strut framing, lintels, studs
- Infrastructure: Road signs, rail tracks, transmission towers
- Automotive: Chassis, trailers, hitches
- Shelving: Supermarkets, warehouses
- Appliances: Washing machines, refrigerators
- Heavy engineering: Truck bodies, crane booms
- Agriculture: Greenhouses, animal sheds
- Cabling: Channels for electrical conduits
- Solar: Mounting systems
- Furniture: Frames, legs, supports
The flexibility to produce varied geometries and sizes makes U profile forming lines ideal for prototyping and custom requirements.
-
দ্রাক্ষাক্ষেত্র পোস্ট রোল ফর্মিং মেশিন
-
স্বয়ংক্রিয় আকার পরিবর্তনযোগ্য সিগমা Purlin রোল ফর্মিং মেশিন
-
স্বয়ংক্রিয় আকার পরিবর্তনযোগ্য CZ Purlin রোল ফর্মিং মেশিন
-
স্বয়ংক্রিয় আকার পরিবর্তনযোগ্য Z Purlin রোল তৈরির মেশিন
-
Auto Size Changeable C U Purlin Roll Forming Machine
-
বৈদ্যুতিক মন্ত্রিসভা ফ্রেম রোল গঠনের মেশিন
-
দিন রেল রোল ফর্মিং মেশিন
-
তারের মই রোল ফর্মিং মেশিন
-
পিভি মাউন্টিং বন্ধনী সি শেপ প্রোফাইল রোল ফর্মিং মেশিন
Working Principles of U Channel Roll Forming
U profile rolling mills form flat strips into U shapes through a series of processes in successive stands:
Stripping
The sheet is longitudinally fed through preset intermeshing rollers which control the material flow during the bending process.
Forming
Progressive dies and bending rolls progressively form the sheet in stages into channel shape.
Calibration
Final forming guides accurately calibrate the profile to exact finished dimensions.
Cutoff
Mounted cutoff press shears or saws slice the end product to the desired length.
Stack delivery
Formed U channels are collected on an exit table.
Design Aspects of U Profile Machines
Key design elements influence the functioning:
Number of Rolling Stands: Typically 8 to 16. More stands allow gradual bending for stronger, uniform profiles.
Roll Pass Design: Determined by final U channel size and metal thickness. Complex profiles need more passes.
Roll Materials: Stainless or tool steel rolls with hardened wear-resistant surfaces.
Roll Diameter: Larger diameters impart higher bending forces. Typical size 75-250 mm.
Machine Rigidity: Robust steel frames minimize vibration for profile precision.
Drives: Independent AC drives for each motorized station.
Control: PLC/HMI controls for automatic parameterized operation.
Safety: Emergency stops, guards, sensors on all moving parts.
Noise: Acoustic enclosures for low operational noise.
Key Components of U Profile Making Lines
U profile rolling mills have different modules for each stage:
Component | Purpose |
---|---|
ডিকয়লার | Unwind metal coil stock |
Feeding unit | Push sheet into machine |
Right angle shearing unit | Square cut head of coil |
Straightening machine | Remove coil curl |
Pre-punching unit | Make holes in sheet |
Oil application unit | Lubricate sheet |
Forming stations | Gradually form U shape |
Sizing unit | Calibrate profile size |
Cutting unit | Cut U channel to length |
Stacking table | Collect finished pieces |
Working Process Stages in U Channel Rolling Lines
The step-by-step forming process on the machine is:
1. Feedstock Entry
Coiled steel sheet loaded and fed into the de-coiling unit.
2. Shearing
The strip head cut square in the right angle shear.
3. সোজা করা
Coil set removed by motorized rolls.
4. Holes and Notching
Additional features punched if needed.
5. Oil Application
Lubricants applied for smooth sheet flow.
6. Forming
Sheet pre-bent and gradually formed into U profile through multiple stands.
7. Sizing
Final stands calibrate shape to precise dimensions.
8. Cutting
End cutoff presses cut U channel to length.
9. Stack Delivery
Formed U lengths exited to collection tables.
Comparison of Manual vs Automatic U Profile Making Machines
Parameter | Manual U Profile Rolling Mill | Automatic U Profile Rolling Mill |
---|---|---|
Operation | Hand operated | Fully automatic PLC controlled |
Speed | Lower output | High production capacity |
Labor | Requires manual feeding and stacking | Less labor for supervision |
Size changes | Manual roll and die changeovers | Quick preset profile changes |
Cost | Cheaper price | Expensive, higher capabilities |
Maintenance | Basic | Intensive maintenance requirement |
Accuracy | Prone to size variations | Consistent and precise |
Defect prevention | Manual monitoring needed | Auto sensors to detect issues |
Add-ons | Limited capabilities | Integration of addons like punching, notching, etc. |
How to Choose U Profile Making Equipment Suppliers
Important aspects to consider when selecting U profile machine manufacturers:
Technical expertise: Look for extensive domain knowledge in roll forming process engineering.
Production facilities: Company should have advanced machinery, testing infrastructure.
Customization capabilities: Supplier with in-house design, engineering resources preferred for range of requirements.
Installation support: Manufacturer should handle complete erection, commissioning of equipment.
প্রশিক্ষণ: Operator training on usage, maintenance should be provided.
Service infrastructure: After-sales service support across regions is vital for response times.
Certifications: Reputed companies have ISO and other certifications indicating standardization, quality focus.
Clientele: Check client lists and feedback to determine reliable vendors.
Pricing: Compare price quotes to filter economical options matching budget.
Brand reputation: Give preference to popular manufacturers with proven track record.
Pros and Cons of U Profile Forming Lines
Advantages
- Continuous and efficient roll forming
- High production volumes suiting mass production
- Dimensional accuracy and profile consistency
- Reduced material wastage
- Lower operating costs over long run
- Minimal need for secondary finishing processes
- Easy integration of addons like hole punching, notching
- Adaptable to produce varied U channel geometries
- Low maintenance if properly operated
- Better corrosion resistance than extruded U channels
- Safer with automated monitoring compared to manual handling
Limitations
- High initial capital investment
- Fixed tooling restricts extreme profile changes
- Regular roll and bearing replacement
- Dedicated floor space requirement
- Specialized skill requirement for machine operation
- Risk of edge cracking in channels if parameters not set correctly
Price Ranges of U Profile Making Machines
Production Output | Price Range |
---|---|
Low Volume up to 100 meters/min | $50,000 to $100,000 |
Medium Volume 100 – 200 meters/min | $100,000 to $250,000 |
High Volume 200+ meters/min | $250,000+ |
The production rate and level of automation greatly influence the machine price. Higher output automatic U profile rolling mills with addon capabilities will situate at the higher end of price spectrum.
Operational Aspects of U Channel Forming Lines
Effective functioning of U profile making systems depends on:
Parameter Settings: All electrical, mechanical, operational parameters need proper configuration as per profile design.
Speed Control: Roll speeds must synchronize correctly from the feeding unit to the cutoff end without fluctuations.
Tooling Maintenance: Roll pass design needs to match sheet thickness and final channel size to achieve uniform deformation. Regular roll grinding avoids marking defects.
Lubrication: Adequate and uniform lube application ensures frictionless sheet flow without scratching.
Coolants: Water soluble coolants prevent overheating during high speed operation.
Defect Monitoring: Inspection checks at each stage are needed to meet quality standards. Any belt wrinkling, twisting, edge cracking indicates improper adjustment.
Safety: Utmost care must be exercised when working around rotating tooling. All safeguarding mechanisms should function.
Maintenance Practices for U Profile Rolling Machines
Routine maintenance activities:
- Roll inspection: Check for scratches, wear. Replace damaged rolls.
- Bearing lubrication: Re-grease bearings at periodic intervals.
- Cleaning: Remove metal dust, scrap debris from assemblies.
- Belt tensioning: Inspect and adjust belt drives if loose.
- Bolt tightening: Check foundation, frame bolts, if loose tighten.
- Electrical wiring: Assess cabling, control wiring for fraying, cuts. Replace if damaged. Use dust and moisture resistant enclosures.
- Hydraulic inspection: Check cylinders, hoses for leakage. Refill levels if low.
- Sensor calibration: Recalibrate proximity switches, photoelectric sensors periodically.
Systematic maintenance essential for maximum working life and output quality.
U Profile Machine Manufacturers in China
Some leading Chinese U profile roll forming machine producers include:
প্রতিষ্ঠান | Location |
---|---|
Botou Xianfa | Hebei |
স্যামকো মেশিনারি | Zhejiang |
Jin De Rui | Shandong |
Ruifeng | Shandong |
Rifeng | Shandong |
SC Forming | Zhejiang |
Supermarch Forming | Jiangsu |
Forever Bend | Guangdong |
Sinospace | Hebei |
Lingheng | Guangdong |
The concentration of U channel making equipment manufacturers in eastern coastal Chinese provinces of Guangdong, Zhejiang, Jiangsu, Shandong and proximity to sheet metal supply chains allows competitive exports worldwide.
U Profile Forming Machine Manufacturers in India
Prominent Indian manufacturers and exporters of U profile roll forming lines include:
প্রতিষ্ঠান | Location |
---|---|
SURYA | Gujarat |
Spirol International | Punjab |
Kiran Hydraulics | Maharashtra |
Sree Engineering | Andhra Pradesh |
Metro Engineers | Maharashtra |
Sunbeam Equipments | Delhi |
Samrat Machine Tools | Gujarat |
Brakes India | Tamil Nadu |
Friends Engineering | Maharashtra |
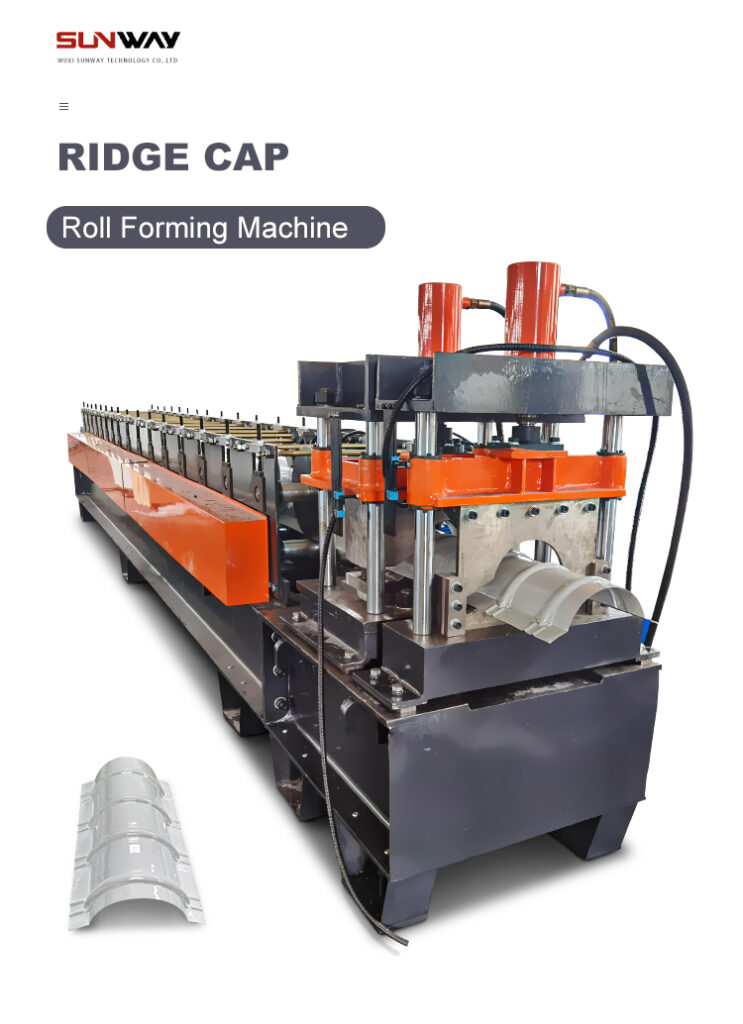
FAQ
Q: What materials can be formed into U profiles?
A: Commonly rolled materials are mild steel, stainless steel, aluminum and copper. Other roll-formable metals include brass, titanium, nickel alloys depending on machine capabilities.
Q: What is the thickness range of metals that can be formed into U channel?
A: U profile rolling mills can typically process metal thickness from 0.3 mm to 8 mm thickness sheets. Custom machines exist for thicker plates.
Q: What maintenance is required on U profile making lines?
A: Regular roll inspection and replacement, lubrication of bearings, cleaning of scrap debris, electrical, hydraulic and sensor checks constitute routine maintenance.
Q: What are common defects in roll formed U channels?
A: Defects like twisting, flaring, bowing, wrinkling, scratching, edge cracking indicate issues with machine settings, roll design or lubrication adjustment.
Q: What safety aspects are important on U profile rolling mills?
A: Mechanical guards, emergency stop buttons, two hand operated consoles, overload protection should cover all risk areas according to industrial safety norms to prevent accidents.
Q: What is the lifespan of U profile forming machines?
A: Correctly installed and meticulously maintained U profile makers deliver over 15 years of service. Preventive maintenance maximizes longevity.
Q: What is the delivery time for these machines?
A: Readymade U channel rolling mills can ship within 30 days of order. Custom built machines can take 60-90 days for design, manufacturing and factory acceptance testing before dispatch.
Q: What certifications are held by reputed U profile making machine brands?
A: Leading international roll forming equipment manufacturers comply with quality standards ISO 9001 and safety certifications like CE, UL, CSA, ISI.