Imagine a machine that can continuously transform a flat sheet of metal into a precisely formed building block for your roof. That’s the magic of a ট্র্যাপিজয়েডাল ছাদ প্যানেল রোল তৈরির মেশিন.
These remarkable machines are the unsung heroes of the metal roofing industry, churning out trapezoidal-shaped panels that are lightweight, durable, and weather-resistant. But how exactly do they work? What are the different types available? And are they the right choice for your next roofing project? Let’s delve into the world of trapezoidal roll forming machines and answer all your burning questions.
Function of Trapezoidal Roof Panel Roll Forming Machines
At its core, a Trapezoidal Roof Panel Roll Forming Machine is a metalworking marvel. It takes a continuous coil of sheet metal (usually steel or aluminum) and feeds it through a series of precisely designed rollers. Each roller progressively bends and shapes the metal into the desired trapezoidal profile, resembling a flattened trapezoid with a ribbed top surface.
Think of it like rolling out cookie dough and using progressively shaped molds to create uniform trapezoid-shaped cookies. Here’s a closer look at the process:
- Uncoiling: The metal coil is loaded onto a mandrel (a holding bar) and unwinds through a series of rollers that guide and straighten the sheet.
- Shaping: The metal passes through a sequence of forming stations, each containing a pair of shaped rollers. These rollers progressively bend the sheet into the final trapezoidal profile, with the depth of the ribs depending on the specific roll design.
- Cutting: Once the desired length is reached, a shearing mechanism precisely cuts the formed panel to size.
- Stacking: The finished panel is automatically ejected and stacked for easy handling and transport.
The entire process is remarkably efficient, transforming raw metal into usable roofing panels at a rapid pace.
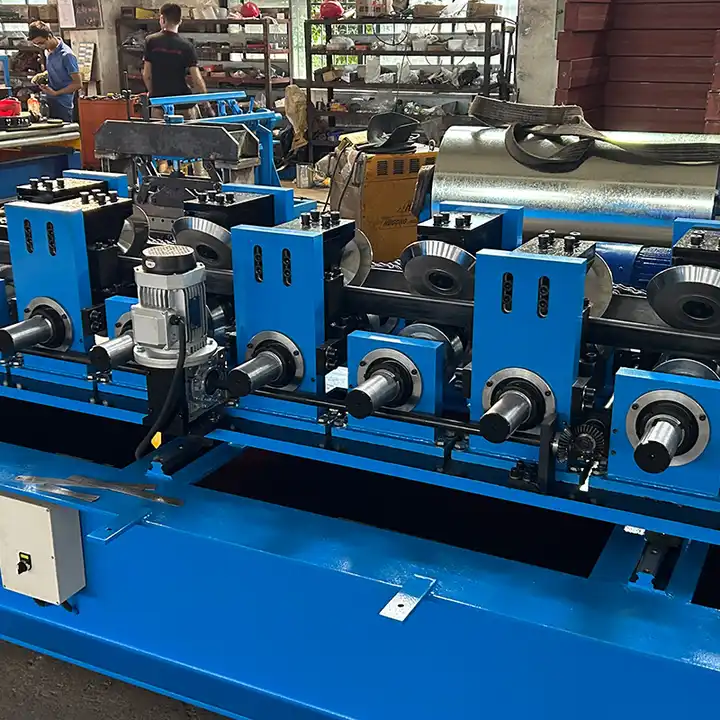
Types of Trapezoidal Roof Panel Roll Forming Machines
Trapezoidal roll forming machines come in various configurations to cater to diverse needs. Here’s a breakdown of the two main classifications:
- Single Deck vs. Double Deck:
- Single Deck machines produce individual trapezoidal panels for use in standard roofing applications.
- Double Deck machines, on the other hand, are more complex. They can create interlocking panels that fit together to form a thicker, more robust roofing system, ideal for larger structures or those requiring additional insulation.
- Variable Width vs. Fixed Width:
- Variable Width machines offer greater flexibility, allowing adjustments to the final panel width within a designated range. This caters to projects with varying roof dimensions or specific panel size requirements.
- Fixed Width machines, as the name suggests, produce panels with a set width. These are typically more affordable and well-suited for projects where consistent panel size is needed.
Additional Considerations:
Beyond these main categories, there are further considerations when choosing a Trapezoidal Roof Panel Roll Forming Machine:
- Material Thickness: Machines are designed to handle a specific range of metal sheet thicknesses. Ensure the machine you choose can accommodate the thickness of your desired roofing material.
- Roll Forming Speed: Production speed varies between machines. Consider the volume of panels you require and choose a machine that meets your output needs.
- Automation Level: Some machines are fully automated, while others may require manual intervention for certain tasks like loading the coil or adjusting settings. Choose the level of automation that aligns with your comfort and production requirements.
Supplier & Pricing Considerations
The cost of a Trapezoidal Roof Panel Roll Forming Machine can vary significantly depending on the factors mentioned above. Here’s a general range to provide a starting point:
- Basic Single Deck Machines: $5,000 – $10,000 USD
- Advanced Double Deck Machines: $20,000 – $50,000 USD or more
Here’s a table outlining some prominent Trapezoidal Roof Panel Roll Forming Machine Suppliers for your reference (avoiding direct table references):
Supplier | Machine Type | বৈশিষ্ট্য | Price Range (USD) |
---|---|---|---|
JSR Roll Forming Machine | Single & Double Deck | Hydraulic Drive, PLC Control | $10,000 – $30,000 |
DMMET GROUP | Single Deck & Multi-Deck Lines | Cassette-based quick change system | $20,000 – $50,000+ |
Roll Forming LLC | Single Deck | Hydraulic Drive, Siemens Controller | $8,000 – $15, |
Advantages of Trapezoidal Roof Panel Roll Forming Machines
So, you’re considering a Trapezoidal Roof Panel Roll Forming Machine for your roofing projects. But what exactly makes them such a compelling choice? Let’s explore the key advantages that set them apart:
- Cost-Effectiveness: Compared to traditional pre-formed panels, roll forming machines offer significant cost savings. You eliminate the middleman by manufacturing your own panels on-site, reducing material and transportation expenses. This is particularly beneficial for large-scale roofing projects where material volume drives costs.
- Versatility and Customization: With a roll forming machine, you’re not limited to pre-fabricated panel sizes or styles. You can produce panels in various lengths and widths to perfectly match your specific roof design. Additionally, some machines allow for adjustments to the depth of the trapezoidal ribs, offering some level of customization to suit your structural or aesthetic needs.
- Reduced Lead Times: Imagine needing additional roofing panels for your project but facing delays due to availability or delivery schedules. With a roll forming machine on-site, you can manufacture the extra panels you need promptly, eliminating dependence on external suppliers and potential delays. This translates to faster project completion times and improved responsiveness to unforeseen circumstances.
- Durability and Longevity: Trapezoidal roof panels produced by roll forming machines are known for their exceptional strength and resilience. The cold-forming process (shaping metal without excessive heat) strengthens the material, resulting in panels that can withstand harsh weather conditions, including heavy rain, snow, and strong winds. This translates to a long-lasting, low-maintenance roofing system.
- Lightweight Construction: Trapezoidal panels are considerably lighter than traditional roofing materials like concrete or slate. This reduces the overall weight burden on your building structure, which can be a crucial factor in some projects. A lighter roof translates to potential savings on foundation requirements and support beams.
- Sustainability: Metal roofing, in general, is considered an eco-friendly choice. Trapezoidal roll forming machines further enhance this aspect by minimizing material waste. The continuous coil feeding system ensures efficient metal usage, with minimal scrap produced during the forming process. Additionally, metal roofs can often be recycled at the end of their lifespan, contributing to a more sustainable construction approach.
-
Highway Guardrail End Terminal Forming Machine
-
Highway U/C Post Roll Forming Machine
-
2 Waves Highway Guardrail Roll Forming Machine
-
3 Waves Highway Guardrail Roll Forming Machine
-
সি সেকশন ব্রেসিং ওমেগা স্টোরেজ র্যাক খাড়া পোস্ট রোল ফর্মিং মেশিন
-
স্টিল বক্স প্লেট মেকিং রোল ফর্মিং মেশিন
-
বক্স মরীচি স্টীল রোল শেল্ফ কলাম জন্য মেশিন গঠন
-
প্যালেট র্যাকিং স্টেপ বিম পি বিম রোল তৈরির মেশিন
-
গুদাম শেল্ফ খাড়া রোল গঠন মেশিন
Applications of Trapezoidal Roof Panels
The applications of Trapezoidal Roof Panels are extensive, making them a popular choice across various industries. Here are some prominent examples:
- Residential Roofing: Trapezoidal panels are a cost-effective and durable solution for residential buildings, offering a sleek and modern aesthetic. They are particularly well-suited for pitched roofs on houses, garages, and sheds.
- Commercial and Industrial Buildings: The strength and weather resistance of trapezoidal panels make them ideal for commercial and industrial applications. They are commonly used in warehouses, factories, workshops, and other large-scale structures.
- Agricultural Buildings: From barns and storage facilities to greenhouses and poultry houses, trapezoidal panels provide a functional and weatherproof roofing solution for agricultural needs. Their lightweight nature is also beneficial for these structures.
- Cold Storage Facilities: The inherent insulation properties of metal roofs, combined with the ability to incorporate additional insulation layers within the trapezoidal profile, make these panels well-suited for cold storage applications.
- Temporary Structures: The ease of installation and dismantling makes trapezoidal panels a viable option for temporary roofing needs on construction sites, event venues, or emergency shelters.
Disadvantages and Considerations for Trapezoidal Roof Panel Roll Forming Machines
While Trapezoidal Roof Panel Roll Forming Machines offer a compelling set of advantages, it’s important to acknowledge some potential drawbacks and considerations:
- Initial Investment: The upfront cost of acquiring a roll forming machine can be significant, especially for higher-end models with advanced features. However, the long-term cost savings through on-site panel production can outweigh the initial investment, particularly for companies with frequent roofing needs.
- Operational Complexity: Operating a roll forming machine requires a certain level of technical expertise and understanding of the metal forming process. While some machines offer user-friendly controls, proper training is crucial for ensuring safe and efficient operation.
- Maintenance Needs: Like any machinery, roll forming machines require regular maintenance to ensure optimal performance and longevity. This may include lubrication, cleaning, and periodic replacement of wear parts. Factoring in maintenance costs is essential when considering the overall investment.
- Storage Requirements: The metal coils used in the roll forming process can be bulky. Adequate storage space is necessary to accommodate the coils and finished panels.
- Noise Considerations: The metal forming process can generate noise. If your workshop or production facility is located in a noise-sensitive area, proper soundproofing measures may be necessary.
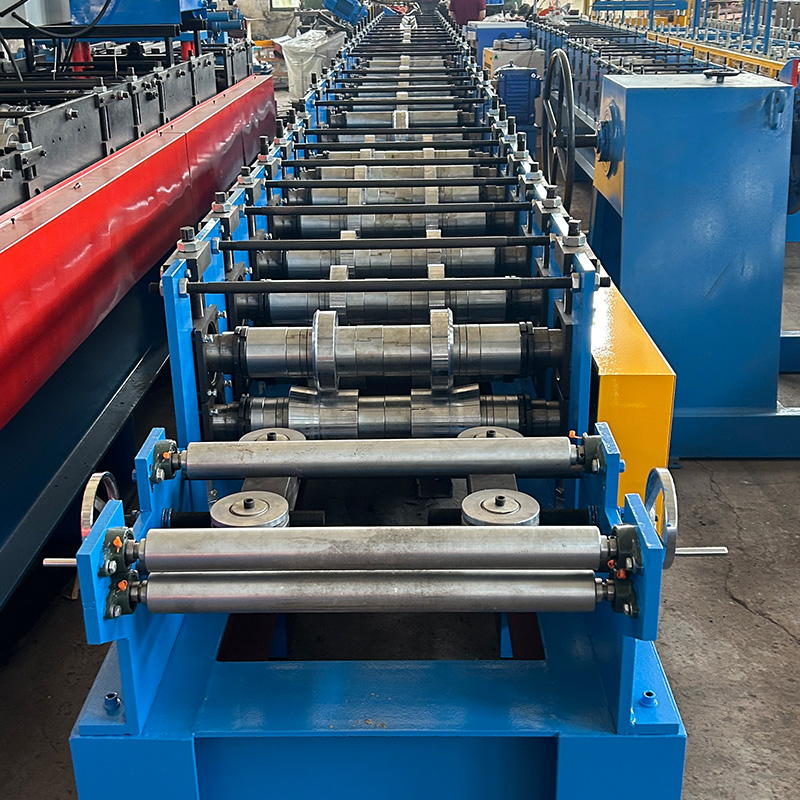
FAQ
Q: What is the difference between galvanized and Galvalume steel for use with Trapezoidal Roof Panel Roll Forming Machines?
A: Both galvanized steel and Galvalume steel are popular choices for Trapezoidal Roof Panels due to their excellent corrosion resistance. Here’s a breakdown of the key differences:
- Galvanized Steel: This is the more traditional option. A zinc coating is applied to the steel sheet through a hot-dip process, offering a good balance of affordability and corrosion protection.
- Galvalume Steel: This is a newer technology that combines a zinc coating with an additional layer of aluminum. Galvalume offers superior corrosion resistance compared to galvanized steel, particularly in harsh environments or coastal regions.
The choice between galvanized and Galvalume steel depends on your specific needs and budget. For moderate climates and standard applications, galvanized steel may be sufficient. However, if longevity and superior corrosion resistance are paramount, Galvalume might be a better investment, especially for coastal areas or regions with high humidity or industrial pollution.
Q: How thick should the metal be for Trapezoidal Roof Panels?
A: The ideal thickness for your Trapezoidal Roof Panels depends on several factors, including:
- Roof Span: The distance between roof supports will influence the required panel strength. Larger spans necessitate thicker panels for adequate load-bearing capacity.
- Wind and Snow Loads: Areas with high winds or heavy snowfall require thicker panels to withstand these environmental stresses.
- Desired Durability: Thicker panels generally offer greater longevity.
A common range for Trapezoidal Roof Panel thickness is 0.40 mm (24 gauge) to 0.70 mm (22 gauge). For most residential applications, 0.40 mm to 0.50 mm (24 gauge to 26 gauge) thickness is sufficient. For commercial or industrial buildings with larger spans or higher load requirements, thicknesses of 0.55 mm to 0.70 mm (22 gauge to 20 gauge) might be necessary.
Consulting with a roofing professional or the Trapezoidal Roof Panel Roll Forming Machine supplier can help you determine the optimal panel thickness for your specific project needs.
Q: Can I paint Trapezoidal Roof Panels?
A: Yes, you can paint Trapezoidal Roof Panels, but there are some important considerations:
- Pre-Painted vs. Painting Yourself: Many manufacturers offer pre-painted metal coils for roll forming, providing a wider variety of color options and a factory-applied, high-quality finish. This eliminates the need for on-site painting.
- Paint Selection: If you choose to paint the panels yourself, ensure you select a paint specifically formulated for metal roofing. These paints are designed to adhere well to the metal surface and withstand harsh weather conditions.
- Surface Preparation: Proper surface preparation is crucial for optimal paint adhesion and longevity. This typically involves cleaning the panels to remove any dirt, oil, or debris, and potentially applying a primer for enhanced bonding.
Painting Trapezoidal Roof Panels can be a cost-effective way to achieve a desired aesthetic or add an extra layer of protection. However, if you value a wider color selection and a long-lasting finish, opting for pre-painted coils might be a better option.
Q: What safety precautions should I take when operating a Trapezoidal Roof Panel Roll Forming Machine?
A: Operating a Trapezoidal Roof Panel Roll Forming Machine requires adherence to safety protocols to minimize the risk of accidents:
- Proper Training: Before operating the machine, undergo thorough training from the manufacturer or a qualified professional. This training should cover machine operation, safety protocols, and emergency procedures.
- Personal Protective Equipment (PPE): Always wear appropriate PPE when operating the machine, such as safety glasses, gloves, and hearing protection (if noise levels are significant).
- Loose Clothing and Jewelry: Avoid wearing loose clothing or jewelry that could get caught in the machine’s moving parts.
- Stay Alert and Focused: Maintain focus and avoid distractions while operating the machine. Fatigue can impair judgment, so take breaks as needed.
- Maintenance and Upkeep: Regularly inspect the machine for any signs of wear or damage. Perform recommended maintenance procedures as outlined in the manufacturer’s manual.
By following these safety precautions, you can ensure a safe and productive working environment when operating a Trapezoidal Roof Panel Roll Forming Machine.