ভূমিকা
In the intricate world of automotive manufacturing, precision and efficiency are paramount. Car panel roll forming machines have emerged as a revolutionary technology, streamlining the process of creating vehicle panels with unparalleled accuracy and speed. This article delves into the nuances of car panel roll forming machines, exploring their benefits, components, selection criteria, manufacturing process, and the future they hold in the automotive industry.
Understanding Roll Forming in Car Panel Manufacturing
Roll forming is a manufacturing process that involves shaping metal sheets into desired cross-section profiles. In car panel production, this technique allows for consistent and uniform shaping of panels, ensuring a high level of quality across every piece. Unlike traditional fabrication methods, roll forming eliminates the need for extensive welding and machining, resulting in stronger, lighter, and more durable car panels.
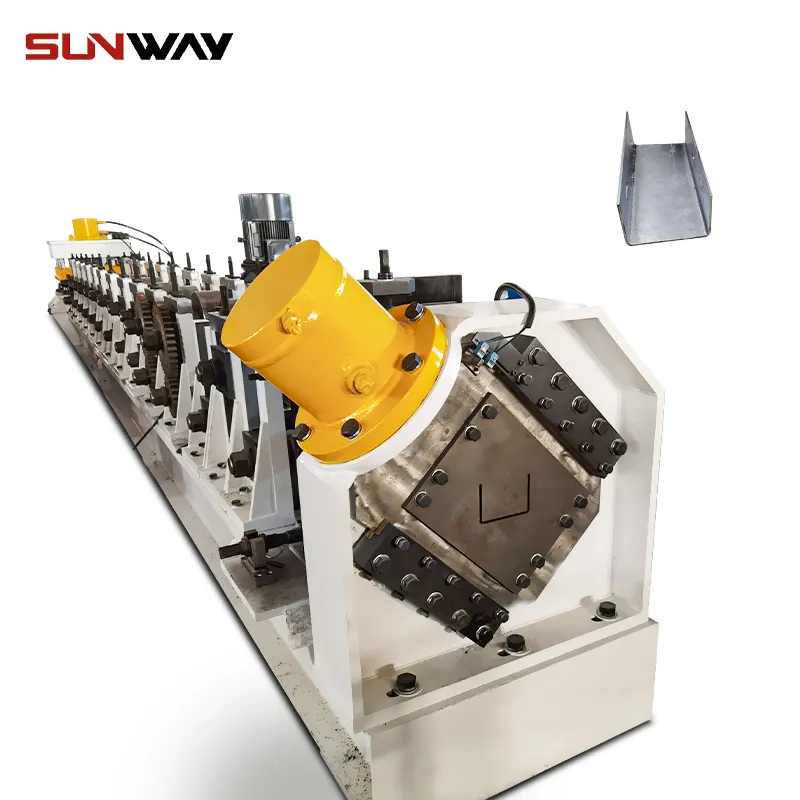
Advantages of Using Car Panel Roll Forming Machines
Car panel roll forming machines offer a range of advantages. They enable the production of intricate designs with complex geometries, ensuring a precise fit and finish. Additionally, the automation inherent in these machines reduces human error and increases production efficiency. The use of roll forming machines also leads to material savings and reduces post-processing requirements.
Key Components of a Car Panel Roll Forming Machine
A car panel roll forming machine comprises several essential components. These include uncoilers for feeding metal sheets, leveling units to ensure uniform material, the roll forming station itself, cutting tools for panel separation, and a control system that regulates the entire process.
Choosing the Right Car Panel Roll Forming Machine
Choosing the right car panel roll forming machine is a crucial decision that can impact the quality of your production, efficiency, and overall business success. Here are some important factors to consider when selecting a car panel roll forming machine:
- Type of Car Panels: Determine the specific types of car panels you’ll be manufacturing. Different roll forming machines are designed for various panel profiles, sizes, and thicknesses. Make sure the machine you choose can handle the panels you need to produce.
- Material Compatibility: Consider the type of materials you’ll be working with, such as steel, aluminum, or other alloys. Ensure that the machine is compatible with the materials you plan to use and can achieve the desired quality and accuracy.
- Production Volume: Evaluate your production needs in terms of the volume of car panels you plan to manufacture. Choose a machine that can handle your production volume without causing excessive downtime or inefficiency.
- Machine Size and Configuration: Consider the available space in your facility. Choose a roll forming machine that fits within your workspace while allowing sufficient room for material handling and operator movement.
- Complexity of Panel Profiles: Some car panel roll forming machines are more suitable for complex and intricate panel profiles, while others are better for simpler shapes. Consider the complexity of the panels you’ll be producing and choose a machine that can accurately create those profiles.
- Speed and Efficiency: Roll forming machines come with different production speeds. Balance the need for faster production with the quality and accuracy of the panels. A faster machine might be desirable, but not if it compromises the final product’s quality.
- Tooling and Changeover: Look into the ease of tooling setup and changeover between different panel profiles. Quick and efficient tooling changeovers can significantly reduce downtime and increase production flexibility.
- Automation and Technology: Consider whether the machine offers automation features such as computerized controls, touchscreens, and programmable settings. Modern technology can enhance efficiency, reduce errors, and streamline production processes.
- Quality and Accuracy: Assess the machine’s ability to consistently produce high-quality and accurately shaped car panels. Look for machines that have a reputation for precision and reliability.
- Supplier Reputation: Choose a reputable manufacturer or supplier with a track record of producing reliable and durable roll forming machines. Research reviews, testimonials, and case studies to gauge the supplier’s reputation.
- Support and Service: Consider the availability of technical support, training, and after-sales service. A supplier that offers comprehensive support can help you address issues and maintain the machine’s performance over time.
- Budget: Determine your budget for purchasing a roll forming machine. While it’s important to find a machine that meets your requirements, make sure it also fits within your financial constraints.
- Future Expansion: Think about your business’s potential for growth and expansion. Choose a roll forming machine that can accommodate increased production capacity if your business scales up in the future.
Before making a decision, thoroughly research different models, attend industry trade shows, and consult with experts in roll forming machinery. Consider reaching out to manufacturers or suppliers to discuss your specific needs and gather detailed information about the machines that align with your requirements.
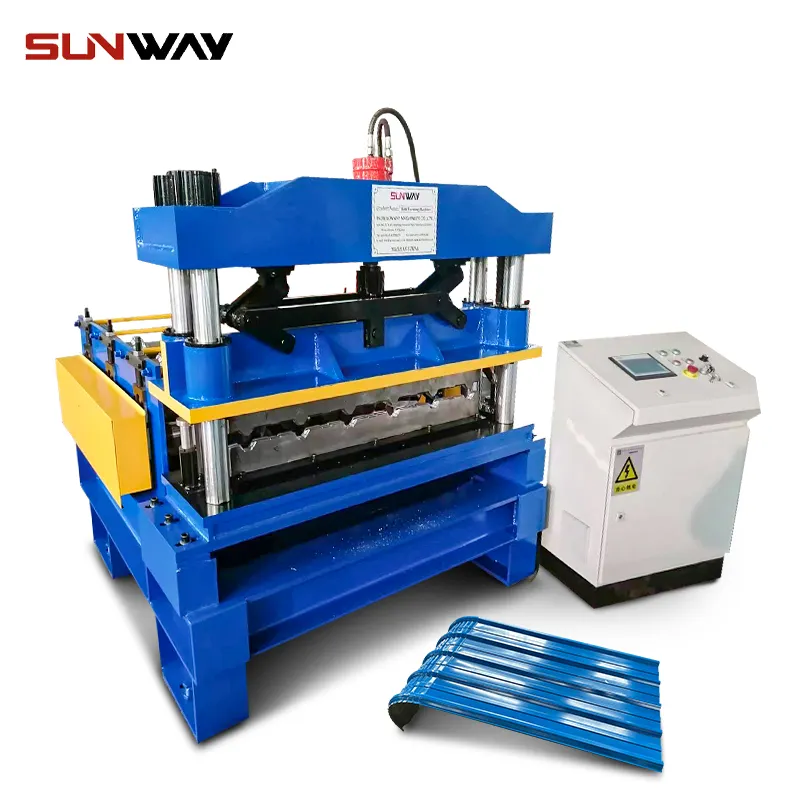
Factors to Consider When Selecting a Roll Forming Machine
When choosing a roll forming machine, various factors must be evaluated. These include the type of material being used (steel, aluminum, etc.), the thickness and width of the material, the required panel design, production speed, and the desired level of automation. Balancing these factors ensures optimal machine selection.
Step-by-Step Process of Car Panel Roll Forming
The roll forming process involves several stages. First, the metal coil is fed into the machine, where it undergoes leveling and pre-cutting. Then, it moves through the roll forming stations, where rollers gradually shape the material into the desired panel profile. Finally, cutting tools trim the formed panels to the required lengths.
Ensuring Quality and Precision in Roll Formed Car Panels
Quality control is a pivotal aspect of car panel roll forming. Advanced machines incorporate sensors and gauges to monitor parameters such as panel dimensions and material thickness. Regular maintenance and calibration are essential to ensure that the machine consistently produces panels that meet industry standards.
Maintenance and Care of Car Panel Roll Forming Machines
Maintenance and care of car panel roll forming machines are crucial to ensure their optimal performance, longevity, and safety. Regular maintenance can prevent breakdowns, reduce downtime, and extend the lifespan of the equipment. Here are some guidelines for maintaining and caring for car panel roll forming machines:
- Read the Manual: Familiarize yourself with the manufacturer’s manual for your specific roll forming machine. It will provide detailed instructions for assembly, operation, maintenance, and troubleshooting.
- Regular Cleaning:
- Keep the machine and its surrounding area clean to prevent dust, debris, and dirt buildup.
- Regularly clean the rollers, guides, and other moving parts. Use a mild detergent and a soft cloth to avoid damaging the machine’s surfaces.
- Lubrication:
- Proper lubrication is essential for smooth operation. Follow the manufacturer’s recommendations for the type and frequency of lubrication.
- Apply lubricants to bearings, gears, chains, and other moving parts as specified. Avoid over-lubrication, as excess lubricant can attract dust and debris.
- Inspect for Wear and Tear:
- Regularly inspect all components for signs of wear, such as worn-out rollers, misaligned guides, loose bolts, and damaged belts.
- Replace any worn or damaged parts promptly to prevent further damage and maintain machine accuracy.
- Alignment and Calibration:
- Ensure that the machine is properly aligned and calibrated according to the manufacturer’s specifications.
- Regularly check the alignment of rollers, guides, and other critical components to prevent production issues.
- Electrical Components:
- Regularly inspect electrical connections, wires, and control panels for any signs of damage or corrosion.
- Ensure that emergency stop buttons and safety interlocks are functioning properly.
- Safety Measures:
- Prioritize safety by following all safety protocols and guidelines provided by the manufacturer.
- Train operators on safe operation practices and ensure they use appropriate personal protective equipment (PPE).
- Scheduled Maintenance:
- Create a maintenance schedule based on the manufacturer’s recommendations and the machine’s usage. Schedule regular inspections, cleaning, and lubrication.
- Keep records of maintenance tasks, repairs, and replacements.
- Professional Maintenance:
- For more complex maintenance tasks and repairs, rely on experienced technicians or professionals who are familiar with the specific machine model.
- Consider scheduling periodic maintenance checks from the manufacturer’s service team or authorized service centers.
- Storage and Environment:
- If the machine is not in use for an extended period, store it in a clean and dry environment to prevent rust and damage.
- Avoid exposing the machine to extreme temperatures, humidity, or corrosive substances.
Remember that the specific maintenance requirements may vary based on the make and model of the roll forming machine. Following the manufacturer’s guidelines and best practices is crucial to ensure the machine’s optimal performance and longevity.
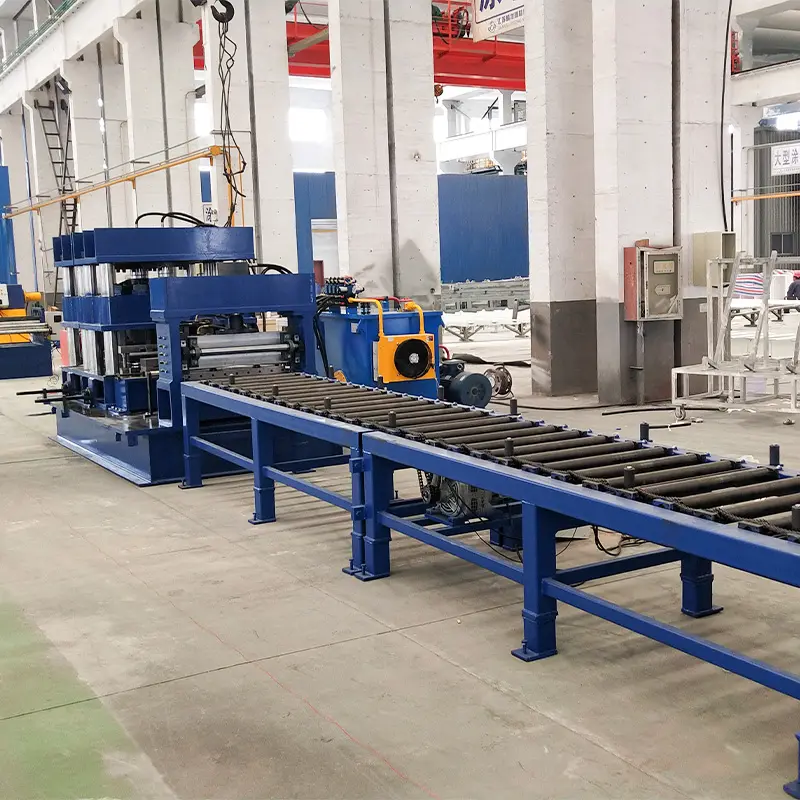
The Future of Car Panel Manufacturing
As technology continues to evolve, so does car panel manufacturing. Innovations in roll forming technology are driving the industry toward more sustainable practices and enhanced efficiency. Customization options, improved energy efficiency, and integration with digital manufacturing platforms are shaping the future landscape.
Innovations and Trends in Roll Forming Technology
The roll forming sector is witnessing transformative innovations. Adaptive control systems that optimize parameters in real-time, the integration of AI for predictive maintenance, and the exploration of lightweight and eco-friendly materials are among the notable trends.
Sustainability in Car Panel Production
Sustainability is a growing concern in manufacturing. Roll forming contributes to sustainability by minimizing material wastage, enabling energy-efficient production, and creating durable, longer-lasting panels. This aligns with the automotive industry’s push for greener practices.

উপসংহার
Car panel roll forming machines have revolutionized the way car panels are manufactured, paving the way for enhanced precision, efficiency, and sustainability. As the automotive industry continues to evolve, embracing these technologies will be key to meeting the demands of modern car production.
FAQs
- Q: Are roll-formed car panels as strong as traditionally welded panels? A: Yes, roll-formed panels are equally strong while being lighter and more precise due to the uniform shaping process.
- Q: Can roll forming machines create panels with complex designs? A: Absolutely, roll forming machines can produce panels with intricate geometries and complex designs.
- Q: What materials can be used with car panel roll forming machines? A: Roll forming machines can work with a variety of materials, including steel, aluminum, and more.
- Q: How can I ensure the quality of roll-formed panels? A: Regular maintenance, calibration, and incorporating quality control measures in the process are crucial for panel quality.
- Q: What role does automation play in car panel roll forming? A: Automation in roll forming machines reduces human error, increases efficiency, and ensures consistent panel quality.