ক step beam forming machine is an efficient automated metal fabrication equipment used to bend metal sheets and plates into various step beam structural shapes. This guide provides a comprehensive overview of step beam forming machine technology, working, components, capabilities, suppliers, applications, installation and more.
What is a Step Beam Forming Machine?
A step beam forming machine, also known as a step structural beam line, is a customized automated machine press brake that cold forms metal coils and sheets into step beams and structural channel profiles used in the construction, infrastructure, logistics and other industries.
The machine progressively forms the sheet metal fed through automated roller tables into unique step shapes with multiple built-in returns/lips along the web and flanges. The specialized CNC press brake tooling consisting of male and female dies, punch and dies, is customized to produce specific step beam configurations continuously.
Key Features of Step Beam Forming Machines
- Automated roller tables for material feeding
- Programmable servo-electric/hydraulic press brakes
- Custom built-in tooling for forming steps
- Touchscreen HMI, PLC and other automated controls
- Modular designs for output flexibility
- High degree of forming accuracy and repeatability
- Low maintenance and operation costs
- Output range from 50 kg to 1000 kg per hour based on model
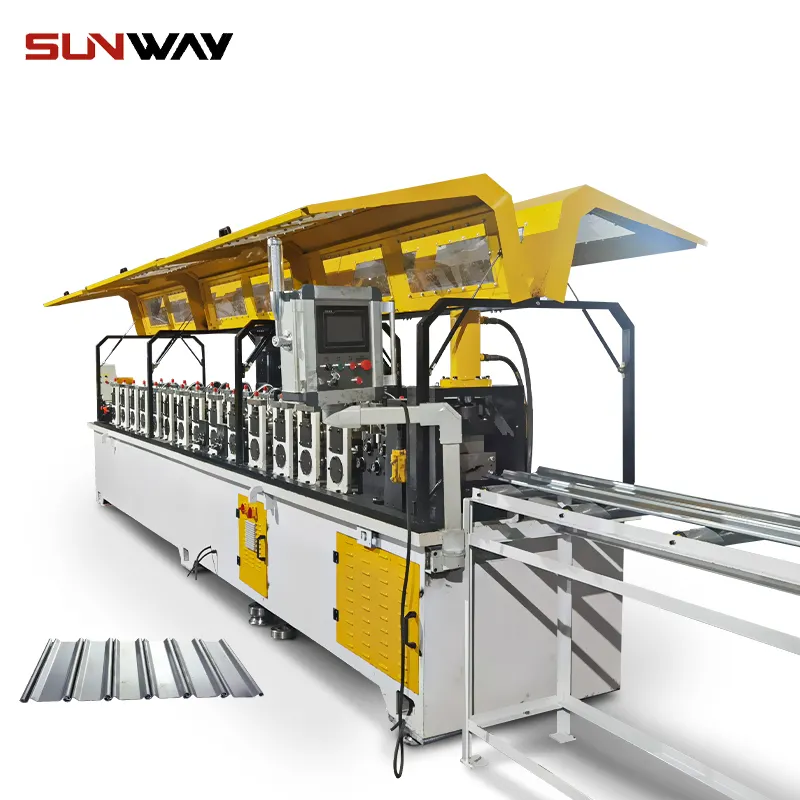
Components of a Step Beam Production Line
A typical step beam forming system consists of several important sub-systems working together:
Table: Components of a Step Beam Forming Machine
Component | Description |
---|---|
Uncoiler and Feeder | Automated units that unroll and feed metal coil/sheet at adjustable feed rates |
Guide Rollers | Straighten and guide sheets into the forming section |
Press Brake | Presses down on sheet using specialized upper/lower tooling to form unique step configurations continuously |
Controller | PLC/CNC control systems to automate and program entire forming process via HMI |
Conveyors | Roller tables to automatically transport formed step beams for next processes |
ডিকয়লার | Winds and recoils finished product |
Safety Enclosure | Full safety guards for operator protection |
The various components are synchronized via servo mechanisms to coordinate material feed, speed, bending and discharge automatically for continuous production.
Modern step beam lines also include self-diagnostic systems, quick die change capabilities and various material handling accessories. Custom engineered solutions can produce different step profiles by changing tooling modules.
Working Process of a Step Beam Forming Machine
The working concept involves continuously cold forming metal sheets into unique step beam shapes utilizing an automated forming section.
Table: Step by Step Process Flow in a Step Beam Production Line
Stage | Working Description |
---|---|
1. Material Loading | Metal coils or sheets loaded onto powered de-coiler |
2. Feeding | Automated feeder feeds sheet at preset feed rates into machine |
3. Shearing | Optional end cropping shear to cut sheets to length |
4 Straightening | Sheet passed through set of rollers to flatten/straighten it |
5. Forming | Sheet pressed between upper and lower specialized dies to gradually form steps |
6. Discharge | Formed step beam ejected onto exit roller tables |
7. Recoiling | Optional re-coiling of finished beams into rolls by powered recoiler |
The feeding, bending and discharge processes work continuously to produce high volumes of step beams per hour. Operators mainly load materials, monitor operations, inspect quality and replace tooling.
Modern computerized models allow easy programming of parameters like feed rates, stroke depth, punches per minute via the touchscreen HMI panel resulting in quick size/profile changes.
Key Specifications
Major parameters that define step beam line technical specifications:
Table: Technical Specifications of Step Beam Forming Machines
Parameter | Typical Range |
---|---|
Roller Table Length | 5m – 12m or more |
Material Thickness | 2mm – 10mm |
Material Type | Mild Steel, Stainless Steel |
Sheet Width | 1000mm – 2500mm |
Bending Force | 25 Ton to 100 Ton |
Step Height | 50mm – 300mm |
Production Speed | 10m to 30m per min |
Production Capacity | 50 kg to 1000 kg per hour |
পাওয়ার সাপ্লাই | 220V/380V AC , 15-50kW+ |
Custom step beam plants can be supplied to suit specific dimensional and output requirements.
-
রোলিং শাটার স্ল্যাট রোল ফর্মিং মেশিন
-
Highway Guardrail End Terminal Forming Machine
-
Highway U/C Post Roll Forming Machine
-
2 Waves Highway Guardrail Roll Forming Machine
-
3 Waves Highway Guardrail Roll Forming Machine
-
বৈদ্যুতিক মন্ত্রিসভা ফ্রেম রোল গঠনের মেশিন
-
দিন রেল রোল ফর্মিং মেশিন
-
দুই তরঙ্গ হাইওয়ে গার্ডেল মেশিন
-
থ্রি ওয়েভ হাইওয়ে গার্ডেল মেশিন
Types of Step Beam Profiles Produced
Common standard and custom step beam profiles that can be formed by these machines include:
Table: Step Beam Shapes that can be Produced
Profile Shape | Description | আবেদন |
---|---|---|
C Channel Steps | C sections with multiple lipped returns | Column beams, supports |
U Channel Steps | U channels with formed lips | Heavy load bearing |
Uneven Steps | Varying step depths in one web | Decorative and structural |
Equal Steps | Uniform steps along full web | Modular structures |
Z Section | Z shape with steps on flanges | Special architectural shapes |
Tapered Steps | Progressively decreasing steps | Visual appeal |
Advanced tooling designs allow forming channels, tapers, unequal flanges and almost any step beam shape on demand.
Raw Material for Step Beams
Commonly used materials for step beam profiles:
- Mild steel sheets and coils
- Galvanized iron coils
- Stainless steel sheets
- Aluminum sheets up to 4mm thickness
The uncoiler and feeding mechanism is equipped with dedicated roller tables for smooth loading and handling of steel, stainless steel and aluminum coils without damage.
Structural Step Beam Applications
Step beams provide excellent load bearing capacity similar to standard I beams but with decorative shapes. Common applications include:
Industry
- Warehouses
- Factory structures
- Steel plants
- Commercial buildings
Infrastructure
- Metro stations
- Bridges
- Railways
- Platform roofs
Transportation
- Container chassis
- Tipper trailers
- Truck chassis
Agricultural
- Greenhouses
- Farm equipment
Logistics
- Racking systems
- Mezzanine floors
- Shelving
Marine
- Ships
- Offshore platforms
Defense
- Military vehicles
- Remote installations
The automated process allows mass production of step beams in standard and custom sizes as per application requirements.
Step Beam Tooling Modules
The male and female tooling dies utilize complex tool piece modules that collectively form each step. Common tooling elements include:
Table: Tooling Modules in a Step Beam Machine Press Brake
Module Type | Description |
---|---|
Guiders | Guide sheet into forming zone |
Locators | Align sheet precisely |
Grippers | Firmly grip sheet |
Formers | Female dies to create basic step shape |
Punches | Male dies to press sheet into female dies |
Goosenecks | Form lipped returns |
Directors | Guide formed profile out |
These special tool pieces combine to produce continuous stepped channels via synchronized sequential movements. The open architecture allows replacing only certain modules like punches and dies to alter step configurations.
Buying Factors – Choose Right Step Beam Making Machine
Key considerations for selecting a step beam production line:
Table: Checklist to Select Best Step Beam Making Machine
Parameter | Description |
---|---|
Production Output | Match speed, thickness and width to output rates needed |
Profile Variants | Tool flexibility for standard and custom shapes |
Material Type | Compatibility for steel, aluminum, stainless steel |
Length Range | Roller tables, shear to suit beam lengths |
Control Type | Ease of programming via PLC/CNC |
Die Type | Quick change modular tooling preferred |
Safety | Must have full operator protection guards |
Automation Level | Auto material feed, discharge and other functions |
Post-sales Service | Installation support, maintenance and warranty |
Machine Finish | Robust all-welded frame structure |
Budget | Compare model price versus production capacity |
Reputed manufacturers provide customizable step beam forming equipment built to specifications.
List of Step Beam Machine Manufacturers and Models
Table: Leading Step Beam Making Machine Brands and Models
ব্র্যান্ড | Model Range | Location |
---|---|---|
Anhui Yuding | YD WM/WMS | China |
Jurmex | JBC/JBM | Taiwan |
Sahinler | Beam Line | Turkey |
IMC | Megaform | ভারত |
Techno Designs | TDS | ভারত |
Durma | AD-R/RX | Turkey |
Pricing Estimate
Typical price range for new step beam production lines based on capabilities:
Table: Price Range Estimate for Step Beam Making Machines
Capacity | Price Range |
---|---|
50-100 kg/hour | $30,000 to $60,000 |
100-250 kg/hour | $60,000 to $150,000 |
250-500 kg/hour | $150,000 to $300,000 |
500-1000 kg/hour | $300,000 to $500,000 |
Higher output custom engineered solutions with more features, automation and accessories will be priced higher. Getting quotations from shortlisted suppliers is advised.
Installation and Operation
- Step beam plants require about 200-250 sqft of covered shop floor space for setup.
- Dedicated material loading and forming sections needed with minimum 5-6m length.
- Power requirement is generally 25kW to 50kW based on press brake motor capacity.
- Machines are shipped pre-assembled in containers for quick installation using cranes, forklifts before commissioning.
- Supplier technicians commission the line and provide training on working procedures.
- 1-2 semi-skilled technicians can operate the line by monitoring process parameters on HMI panel and via control switches.
Routine maintenance involves cleaning of tooling, oil levels check and observing performance. Production planning is entering coil dimensions and required beam sizes.
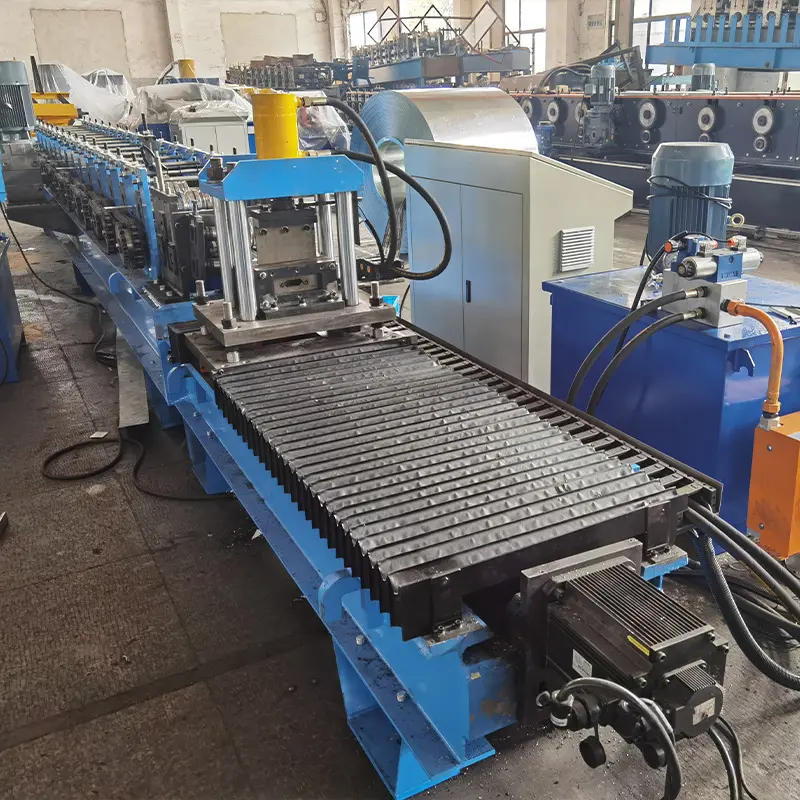
Maintenance Best Practices
Proper maintenance is key for maximum uptime. Steps to follow:
- Clean dies, punches and other tooling regularly
- Lubricate presses and slider guides
- Check belt tensions, motors
- Monitor hydraulic systems
- Replace faulty automation modules
- Keep a stock of common wear parts
- Record machine hours
- Comply with maintenance schedule prescribed
Qualified mechanics from manufacturer provide support for breakdown repairs or overhauling aging machines.
FAQs
Q: What expertise is needed to operate a step beam line?
A: Semi-skilled technicians can run step beam plants after proper training. The automated operation via PLC reduces direct manual work.
Q: Can we get trial samples before order?
A: Reputed suppliers have test facilities to produce sample beams for approval using sheets/profiles provided.
Q: What after sales service is provided?
A: Manufacturers include 1 year machine warranty. AMCS and spare parts supply for 5-7 years along with mechanic support for repairs/maintenance.