Overview
Steel roll forming machines are the backbone of metal fabrication industries, offering precision and efficiency in shaping metal sheets into desired profiles. These machines are indispensable in various industries, from construction to automotive, thanks to their ability to produce consistent and complex shapes with high accuracy. This guide provides a comprehensive look at steel roll forming machines, their types, components, working processes, and how to choose the right one for your needs.
Steel Roll Forming Machine Guide
Roll forming is a continuous bending operation in which a long strip of sheet metal (typically coiled steel) is passed through sets of rolls mounted on consecutive stands, each set performing only an incremental part of the bend, until the desired cross-section profile is obtained. Roll forming is ideal for producing long lengths of metal profiles in large quantities.
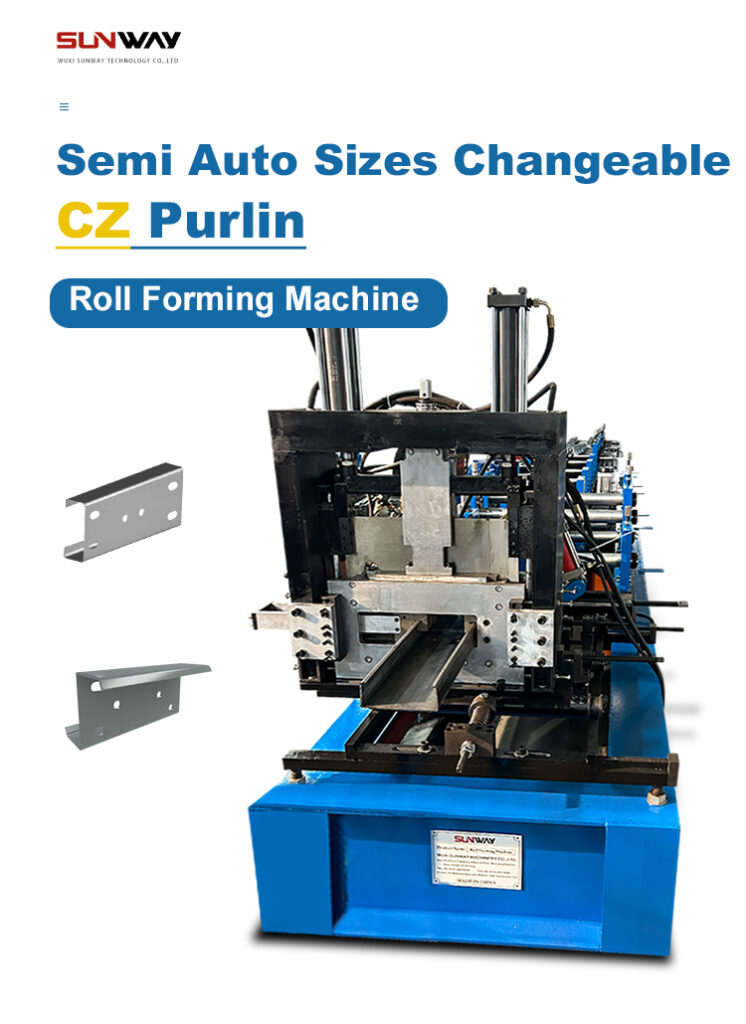
Precision Roll Forming Machine Types
Here are specific models of metal powder and their applications:
মডেল | Description |
---|---|
RSFM-100 | High-speed roll forming machine suitable for producing complex profiles at high precision. |
RSFM-200 | Versatile machine capable of forming a wide range of materials, including aluminum and stainless steel. |
RSFM-300 | Heavy-duty roll forming machine designed for thicker materials and heavy industrial applications. |
RSFM-400 | Compact roll forming machine ideal for small-scale operations and workshops. |
RSFM-500 | Advanced roll forming machine with automated control systems for enhanced efficiency. |
RSFM-600 | High-capacity machine designed for large-scale production with quick changeover capabilities. |
RSFM-700 | Customizable roll forming machine with modular design for specific profile requirements. |
RSFM-800 | Precision roll forming machine for producing intricate designs and high-quality finishes. |
RSFM-900 | Energy-efficient roll forming machine with low operational costs and high throughput. |
RSFM-1000 | High-speed roll forming machine with integrated cutting and punching systems for seamless production. |
Working Process of High-Speed Roll Forming Machine
The working process of a high-speed roll forming machine involves several stages, each critical for ensuring the final product meets the required specifications. Here’s a step-by-step guide to how these machines operate:
- Material Feeding: The process begins with feeding a metal coil into the machine. The coil is unwound and straightened to remove any curvature or imperfections.
- Roll Stands: The straightened metal strip passes through a series of roll stands. Each stand incrementally bends the metal, gradually forming the desired profile. This step ensures precision and consistency.
- Cutting and Punching: As the metal strip moves through the machine, integrated cutting and punching systems create holes, notches, or cut the strip to length. This step is crucial for applications requiring specific features or lengths.
- Forming: The final shape is achieved as the metal strip exits the last roll stand. Depending on the machine’s configuration, additional processes such as edge trimming or embossing may occur.
- Output: The finished product is collected, ready for further processing or assembly.
Key Components and Their Functions
Understanding the key components of a ইস্পাত রোল তৈরির মেশিন is essential for operating and maintaining the equipment effectively. Here are the main parts and their functions:
Component | Function |
---|---|
ডিকয়লার | Holds and feeds the metal coil into the machine. |
Roll Stands | Houses the rollers that bend the metal into the desired shape. |
কাটিং সিস্টেম | Cuts the metal strip to length and creates necessary features like holes or notches. |
Control Panel | Allows the operator to control and monitor the machine’s operations. |
Guiding System | Ensures the metal strip is properly aligned as it moves through the machine. |
Drive System | Powers the rollers and other moving parts of the machine. |
Hydraulic System | Provides the necessary pressure for cutting and punching operations. |
Output Table | Collects the finished product for easy handling and transport. |
Safety Guards | Protects operators from moving parts and ensures safe operation. |
-
Highway Guardrail End Terminal Forming Machine
-
Highway U/C Post Roll Forming Machine
-
2 Waves Highway Guardrail Roll Forming Machine
-
3 Waves Highway Guardrail Roll Forming Machine
-
দ্রাক্ষাক্ষেত্র পোস্ট রোল ফর্মিং মেশিন
-
স্বয়ংক্রিয় আকার পরিবর্তনযোগ্য সিগমা Purlin রোল ফর্মিং মেশিন
-
স্বয়ংক্রিয় আকার পরিবর্তনযোগ্য CZ Purlin রোল ফর্মিং মেশিন
-
স্বয়ংক্রিয় আকার পরিবর্তনযোগ্য Z Purlin রোল তৈরির মেশিন
-
Auto Size Changeable C U Purlin Roll Forming Machine
Machine Speed and Efficiency
The efficiency and speed of a roll forming machine are critical factors in determining its productivity. Here is a comparison of different models:
মডেল | Speed (meters/min) | Efficiency (units/hour) | Energy Consumption (kW) |
---|---|---|---|
RSFM-100 | 20 | 1200 | 10 |
RSFM-200 | 25 | 1500 | 12 |
RSFM-300 | 15 | 1000 | 8 |
RSFM-400 | 10 | 800 | 6 |
RSFM-500 | 30 | 1800 | 15 |
RSFM-600 | 35 | 2100 | 18 |
RSFM-700 | 20 | 1200 | 10 |
RSFM-800 | 40 | 2400 | 20 |
RSFM-900 | 22 | 1300 | 11 |
RSFM-1000 | 50 | 3000 | 25 |
Customized Mechanical Parameters
Roll forming machines can be customized to meet specific requirements. Here are some customizable parameters:
Parameter | Description |
---|---|
Roller Diameter | Customizable to accommodate different material thicknesses and profiles. |
Number of Roll Stands | Can be adjusted based on the complexity of the profile being formed. |
Material Width | The width of the metal strip can be customized to suit specific applications. |
Cutting Length | Adjustable to produce metal pieces of varying lengths. |
Punching Patterns | Customizable punching patterns to create specific hole shapes and sizes. |
গঠন গতি | Speed can be tailored to match production requirements and material characteristics. |
Automation Level | Machines can be equipped with various levels of automation for enhanced efficiency. |
Coil Weight Capacity | Can be designed to handle different coil weights depending on production needs. |
Drive System | Different drive systems (e.g., hydraulic, electric) can be chosen based on performance needs. |
Safety Features | Enhanced safety features can be added to meet regulatory standards and ensure operator safety. |
Applications and Uses
Steel roll forming machines are used in various industries due to their versatility and efficiency. Here are some common applications:
Industry | আবেদন |
---|---|
Construction | Production of roofing panels, wall claddings, and structural components. |
Automotive | Manufacturing of automotive body parts, chassis, and interior components. |
Aerospace | Creation of lightweight and durable components for aircraft. |
Furniture | Production of metal frames, shelving units, and other furniture parts. |
HVAC | Manufacturing of ductwork, vents, and other heating, ventilation, and air conditioning parts. |
Appliances | Creation of metal casings, panels, and structural parts for household appliances. |
Storage | Production of shelving units, storage racks, and containers. |
Electrical | Manufacturing of cable trays, electrical enclosures, and other components. |
Railway | Creation of railway track components and structural parts. |
Agriculture | Production of metal structures and components for agricultural machinery and equipment. |
Installation, Operation, and Maintenance
Proper installation, operation, and maintenance are crucial for the efficient functioning of steel roll forming machines. Here are some guidelines:
Aspect | Description |
---|---|
Installation | Ensure a stable and level foundation, proper alignment of components, and secure electrical connections. |
Operation | Follow manufacturer’s guidelines, ensure proper material feeding, and monitor machine parameters regularly. |
Maintenance | Regularly check and lubricate moving parts, inspect for wear and tear, and replace damaged components promptly. |
Suppliers and Price Range Details
Choosing the right supplier and understanding the price range is essential for making an informed purchase. Here are some details:
Supplier | Price Range (USD) |
---|---|
ABC Machinery | $20,000 – $50,000 |
XYZ Equipment | $25,000 – $60,000 |
Roll Form Tech | $30,000 – $70,000 |
Forming Solutions | $40,000 – $80,000 |
Industrial Roll Form | $35,000 – $75,000 |
Metal Master | $50,000 – $100,000 |
Steel Tech | $45,000 – $90,000 |
Precision Roll | $55,000 – $110,000 |
Advanced Machinery | $60,000 – $120,000 |
Ultimate Forming | $65,000 – $130,000 |
How to Choose a Supplier
Selecting the right supplier for a steel roll forming machine is crucial for ensuring quality and reliability. Here are some factors to consider:
Factor | Description |
---|---|
Reputation | Look for suppliers with a solid reputation in the industry and positive customer reviews. |
অভিজ্ঞতা | Choose suppliers with extensive experience in manufacturing roll forming machines. |
Technical Support | Ensure the supplier offers robust technical support and after-sales service. |
Customization Options | Check if the supplier can customize machines to meet specific requirements. |
Price | Compare prices from different suppliers to find the best value for your investment. |
Warranty | Look for suppliers that offer comprehensive warranties on their products. |
Delivery Time | Consider the delivery time and ensure it aligns with your project timeline. |
গুণ নিশ্চিত করা | Ensure the supplier follows strict quality assurance processes and standards. |
Training and Documentation | Check if the supplier provides training and detailed documentation for operating the machine. |
Advantages and Limitations
Steel roll forming machines offer several advantages but also come with some limitations. Here’s a comparison:
Advantages | Limitations |
---|---|
High Precision | Initial setup cost can be high |
Consistent Quality | Requires skilled operators for optimal performance |
Efficient Production | Limited to specific profile shapes |
Versatility | Maintenance can be complex and time-consuming |
Reduced Waste | Not suitable for low-volume production |
Automated Operation | High energy consumption in some models |
Customization Options | Heavy and requires significant space |
Cost-Effective for High Volumes | Initial learning curve for operators |
Durability and Longevity | Potential for wear and tear on rollers |
Energy Efficient Models Available | Higher initial investment compared to manual or simpler forming methods |
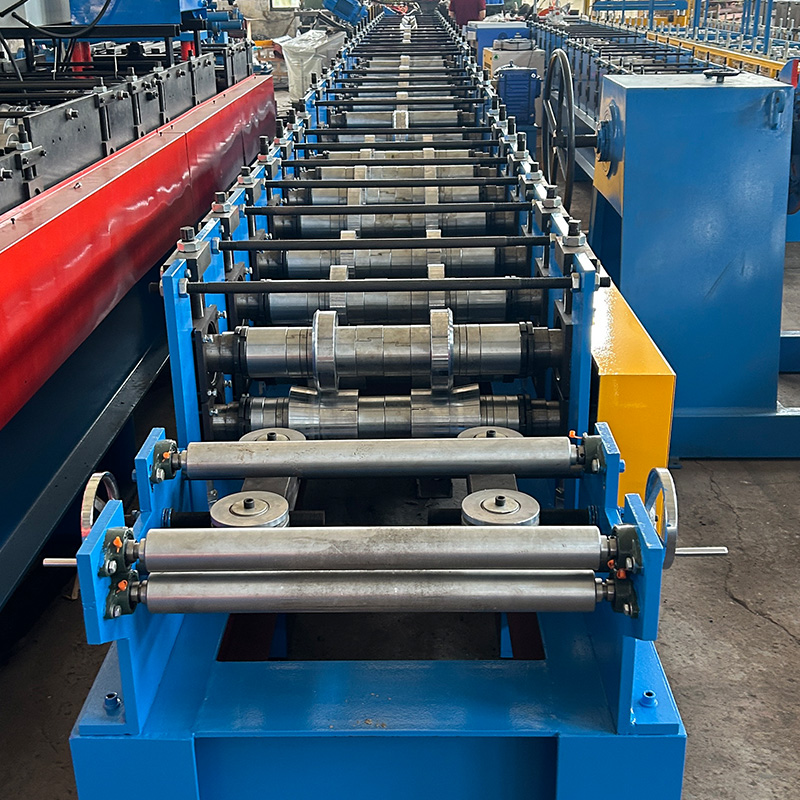
FAQ
Q1: What materials can be used with a steel roll forming machine?
Answer: Steel roll forming machines can work with a variety of materials including steel, aluminum, copper, and stainless steel. The choice of material depends on the specific application and desired properties of the final product.
Q2: How do I maintain my roll forming machine?
Answer: Regular maintenance includes lubricating moving parts, inspecting for wear and tear, replacing damaged components, and ensuring proper alignment of rollers. Following the manufacturer’s maintenance schedule is crucial for optimal performance.
Q3: Can roll forming machines be customized?
Answer: Yes, roll forming machines can be customized to meet specific requirements such as different profile shapes, material thicknesses, and additional features like punching or cutting systems.
Q4: What is the typical production speed of a roll forming machine?
Answer: Production speed varies by model, but high-speed roll forming machines can achieve speeds of up to 50 meters per minute, depending on the complexity of the profile and material type.
Q5: Are there energy-efficient roll forming machines available?
Answer: Yes, many modern roll forming machines are designed to be energy-efficient, reducing operational costs while maintaining high production rates.
Q6: How do I choose the right roll forming machine for my needs?
Answer: Consider factors such as the type of profiles you need to produce, material specifications, production volume, customization options, and budget. Consulting with experienced suppliers can help you make an informed decision.
Q7: What are the common applications of roll-formed products?
Answer: Roll-formed products are commonly used in construction (roofing panels, wall claddings), automotive (body parts, chassis), aerospace (components), furniture (frames, shelving), HVAC (ductwork, vents), and many other industries.
Q8: How long does it take to set up a roll forming machine?
Answer: Setup time varies based on the complexity of the machine and the specific requirements of the production run. It can range from a few hours to a couple of days.
Q9: What safety measures should be taken when operating a roll forming machine?
Answer: Ensure proper training for operators, use safety guards, follow operating procedures, and conduct regular safety inspections to prevent accidents and injuries.
Q10: What is the lifespan of a roll forming machine?
Answer: With proper maintenance and care, a roll forming machine can last several decades, making it a worthwhile investment for long-term production needs.
উপসংহার
Steel roll forming machines are essential tools in the metal fabrication industry, offering precision, efficiency, and versatility. By understanding the different types, components, working processes, and how to choose the right machine and supplier, businesses can optimize their production processes and achieve high-quality results. Whether you are in construction, automotive, aerospace, or any other industry requiring metal profiles, a well-chosen roll forming machine can significantly enhance your operations.
Remember, the key to getting the most out of your roll forming machine lies in proper maintenance, understanding its capabilities, and working with a reputable supplier. So, dive into the world of roll forming with confidence, armed with the knowledge and insights from this comprehensive guide!