As the world races toward reducing carbon emissions and adopting renewable energy sources, wind power has become one of the fastest-growing energy sectors. At the heart of this transformation are wind turbines, specifically their towering structures that harness wind to generate clean energy. Manufacturing these towering giants requires precision, efficiency, and advanced technology, which is where Wind Turbine Tower Section Roll Forming Machines step in.
These machines are specialized industrial solutions designed to produce the high-strength, curved metal sections that form the structural components of wind turbine towers. With the global push for sustainable energy, these roll-forming machines are enabling manufacturers to meet the surging demand for turbine towers while maintaining quality and cost-effectiveness.
In this article, we’ll explore the applications, features, pricing, and environmental benefits of wind turbine tower section roll forming machines, along with insights into the latest technological advancements and market trends in 2025. We’ll also highlight why Wuxi Sunway Machinery is the go-to partner for roll-forming solutions in the renewable energy sector.
What are Wind Turbine Tower Section Roll Forming Machines?
Wind Turbine Tower Section Roll Forming Machines are highly specialized piece of equipment designed to manufacture the large, curved metal panels that make up the sections of wind turbine towers. These panels are typically made from high-strength steel and require a precise shape and curvature to ensure structural integrity and stability when assembled into the towering structures seen in wind farms.
Using a series of rollers, the machine bends and shapes flat metal sheets into the required cylindrical or conical profiles. The result is a durable, weather-resistant, and perfectly curved section ready for assembly into a wind turbine tower.
Applications of Wind Turbine Tower Section Roll Forming Machines
Wind turbine tower sections are essential components of renewable energy infrastructure. Below are the primary applications of Wind Turbine Tower Section Roll Forming Machines:
1. Onshore Wind Farms
- Use Case: Tower sections for wind turbines installed on land.
- Why It Matters: Onshore wind farms are the backbone of global wind energy initiatives, requiring durable and cost-effective tower sections.
2. Offshore Wind Farms
- Use Case: Tower sections for wind turbines installed in oceanic or coastal environments.
- Why It’s Crucial: Offshore turbines face harsher environmental conditions, requiring high-strength and corrosion-resistant tower sections.
3. Hybrid Wind-Solar Projects
- Use Case: Wind turbine towers integrated with solar panels for hybrid renewable energy projects.
- Why It’s Important: These towers maximize energy generation by combining wind and solar power.
4. Community Energy Projects
- Use Case: Smaller wind turbine towers for local energy cooperatives or microgrids.
- Why It’s Relevant: Roll-forming machines enable the production of customized sections for smaller-scale projects.
5. High-Altitude Wind Turbines
- Use Case: Taller turbine towers designed for high-altitude installations to harness stronger and more consistent winds.
- Why It’s Exciting: Roll-forming technology supports the production of extra-large sections that meet the structural demands of high-altitude turbines.
Key Features of Wuxi Sunway Wind Turbine Tower Section Roll Forming Machines
Wuxi Sunway Machinery is a global leader in roll-forming technology, offering machines specifically designed for manufacturing wind turbine tower sections. Here are the standout features of their machines:
1. High-Strength Material Processing
- What It Supports: Machines can process high-strength steel and other alloys used in wind turbine towers.
- Why It’s Important: Ensures the finished sections can withstand extreme wind loads and environmental conditions.
2. Large-Scale Profile Production
- What It Offers: Machines are capable of producing tower sections with diameters ranging from 2 meters to over 6 meters.
- Why It Matters: Supports the production of both onshore and offshore tower designs.
3. Precision Curvature Control
- What It Includes: Advanced roller systems ensure precise control over the curvature and dimensions of each section.
- Why It’s Crucial: Guarantees seamless assembly and structural stability of the tower.
4. High-Speed Production
- Performance: Machines can produce up to 10 meters of curved profiles per minute, depending on the material and design.
- Why It’s Relevant: Meets the high demand for wind turbine towers in large-scale renewable energy projects.
5. Integrated Welding and Edge Preparation
- What It Enables: Machines can incorporate welding and edge preparation systems to streamline post-production processes.
- Why It’s Revolutionary: Reduces production time and ensures high-quality joints for assembled sections.
6. Modular Tooling Systems
- What It Offers: Interchangeable tooling for producing cylindrical, conical, and custom tower section profiles.
- Why It’s Important: Enhances flexibility for manufacturers catering to diverse project requirements.
7. IoT-Enabled Monitoring
- The Technology: Internet of Things (IoT) sensors collect data on machine performance, material usage, and output quality.
- Why It’s Essential:
- Enables predictive maintenance.
- Optimizes production efficiency.
- Integrates seamlessly into smart factory systems.
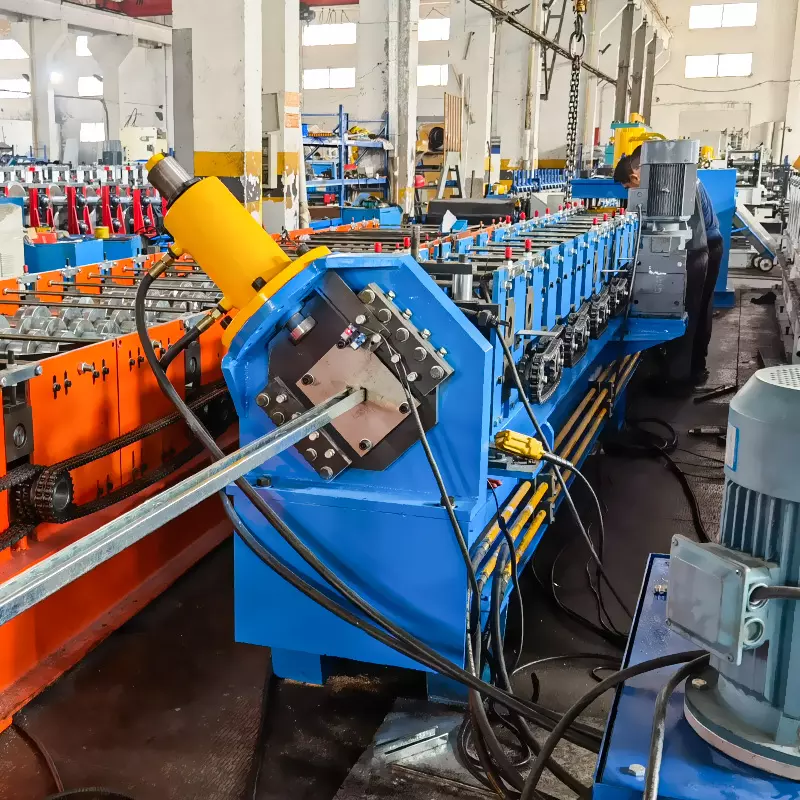
Production Workflow of Wind Turbine Tower Section Roll Forming Machines
The manufacturing process for wind turbine tower sections is designed for precision and efficiency. Here’s an overview of the workflow:
1. Material Feeding
- Raw steel sheets or coils are loaded onto the machine’s decoiler, which feeds the material into the rollers.
2. Leveling and Edge Trimming
- A leveling system ensures the material is flat and free from defects, while edge trimming prepares the sheet for welding.
3. Roll Forming
- The material passes through a series of rollers that gradually shape it into the desired cylindrical or conical profile.
4. Welding Preparation (Optional)
- Some machines include systems for preparing edges for welding or even performing initial welding operations.
5. Quality Inspection
- Each section is inspected for dimensional accuracy and surface finish to ensure compliance with design specifications.
6. Stacking and Transport
- Finished sections are stacked and prepared for transportation to the assembly site or wind farm.
Pricing of Wind Turbine Tower Section Roll Forming Machines
The cost of Wind Turbine Tower Section Roll Forming Machines varie based on its features, production capacity, and customization options. Below is a general pricing guide for 2025:
Machine Type | Capabilities | Price Range (USD) |
---|---|---|
Standard Machines | Basic tower section production | $500,000–$800,000 |
Advanced Machines | High-speed and multi-profile output | $800,000–$1,200,000 |
Fully Customizable Machines | Including welding and IoT-enabled systems | $1,200,000–$2,000,000 |
For detailed pricing and tailored solutions, reach out to Wuxi Sunway Machinery.
Environmental Benefits of Wind Turbine Tower Section Roll Forming Machines
These machines play a crucial role in advancing sustainable manufacturing practices in the renewable energy sector:
1. Material Efficiency
- How It Works: The roll-forming process minimizes waste by using nearly 100% of the raw material.
- Impact:
- Conserves valuable resources.
- Reduces scrap and landfill waste.
- Lowers production costs.
2. Use of Recyclable Materials
- What It Supports: Machines process steel and alloys that are fully recyclable.
- Why It Matters:
- Promotes a circular economy.
- Reduces the environmental impact of end-of-life turbines.
- Aligns with sustainability goals.
3. Energy-Efficient Operations
- The Innovation: Modern machines consume less energy while maintaining high throughput.
- Why It’s Crucial:
- Lowers operational carbon footprint.
- Supports green manufacturing initiatives.
- Improves cost efficiency.
FAQs About Wind Turbine Tower Section Roll Forming Machines
Question | Answer |
---|---|
Can the machine produce conical sections? | Yes, modular tooling allows for the production of both cylindrical and conical sections. |
What is the average production speed? | Machines can produce up to 10 meters of profiles per minute, depending on design requirements. |
Does Wuxi Sunway provide operator training? | Absolutely! Comprehensive training for operators and technicians is included with every purchase. |
What is the expected lifespan of the machine? | With proper maintenance, these machines can last 15–20 years or more. |
Are financing options available? | Yes, flexible financing solutions are available for qualified buyers. |
What industries benefit from this machine? | Industries include renewable energy, construction, and heavy industrial manufacturing. |
Latest Innovations in Wind Turbine Tower Section Roll Forming Machines
The wind energy sector is constantly evolving, and so are the machines that make it possible. Here are some of the key innovations shaping the future of Wind Turbine Tower Section Roll Forming Machines:
1. Adaptive Roller Technology
- What It Does: This technology allows rollers to automatically adjust to varying material thicknesses and section shapes without manual intervention.
- Benefits:
- Reduces downtime during production transitions.
- Increases machine versatility for producing multiple tower designs.
- Ensures consistent quality across all sections.
2. Advanced Edge Welding Integration
- The Feature: Machines now incorporate automatic edge welding systems that prepare tower sections for seamless assembly.
- Why It’s Revolutionary:
- Eliminates the need for separate welding processes.
- Improves structural integrity and reduces production time.
- Enhances the durability of tower sections, especially for offshore applications.
3. AI-Driven Process Optimization
- How It Works: Artificial intelligence monitors production parameters in real time and makes adjustments to maximize efficiency.
- Advantages:
- Reduces material waste by detecting and correcting defects immediately.
- Optimizes machine performance to meet specific project requirements.
- Ensures consistent output quality, even during long production cycles.
4. High-Strength Material Compatibility
- What It Supports: Machines can now process advanced alloys and ultra-high-strength steels used in modern wind turbines.
- Why It’s Important:
- Enables the production of taller, more robust towers for high-capacity wind turbines.
- Meets the structural demands of extreme weather conditions in offshore installations.
5. Modular Machine Configurations
- The Customization: Modular designs allow manufacturers to add or remove components, such as edge trimming or welding units, based on project needs.
- Why It’s Exciting:
- Reduces initial investment costs for smaller manufacturers.
- Provides scalability as production demands grow.
- Offers flexibility for handling unique project specifications.
6. Real-Time Data Analytics and Reporting
- What It Includes: Machines are equipped with IoT sensors and software that generate detailed production reports.
- Benefits:
- Provides actionable insights for improving efficiency and reducing costs.
- Tracks key performance indicators (KPIs) such as material usage, energy consumption, and output quality.
- Simplifies compliance with industry standards and certification requirements.
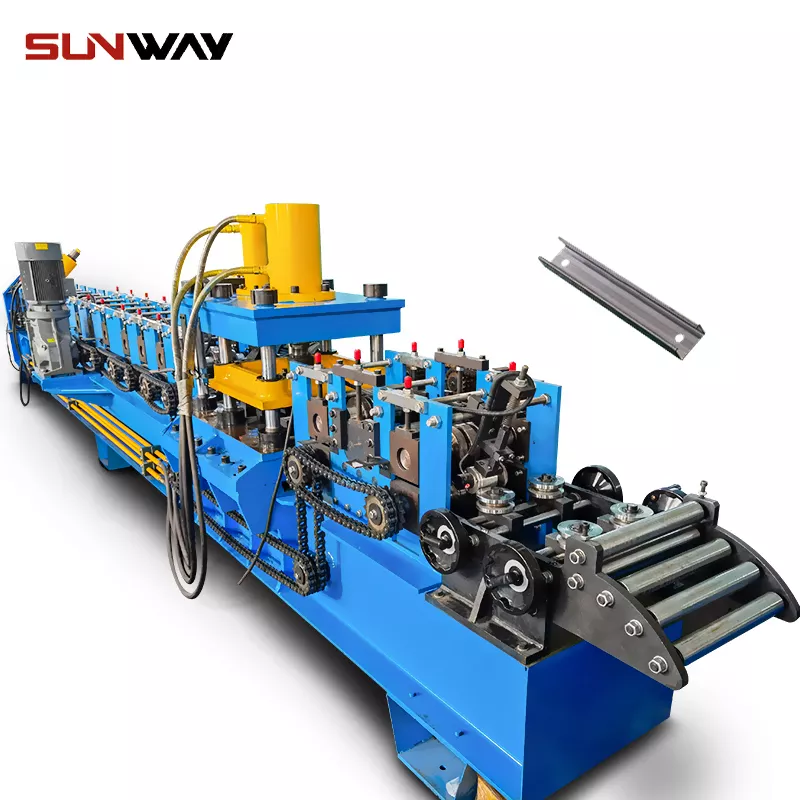
Market Growth and Trends for Wind Turbine Tower Manufacturing
The global wind energy market is experiencing unprecedented growth, driven by government initiatives, technological advancements, and increasing awareness of renewable energy’s importance. Here’s how these factors are shaping the demand for Wind Turbine Tower Section Roll Forming Machines:
1. Global Wind Energy Expansion
- The Numbers: According to the Global Wind Energy Council (GWEC), wind energy capacity is expected to grow by more than 60% by 2030, with significant investments in both onshore and offshore projects.
- Impact on Roll Forming Machines:
- Higher demand for tower sections to support new turbine installations.
- Increased need for machines capable of producing large-diameter sections for offshore turbines.
2. Offshore Wind Growth
- The Opportunity: Offshore wind farms are projected to account for over 25% of global wind energy capacity by 2030.
- Why It’s Relevant:
- Offshore turbines require taller towers and more durable materials, increasing the demand for advanced roll-forming machines.
- Manufacturers need machines that can handle the unique challenges of offshore tower production, such as corrosion resistance and extreme load-bearing capacity.
3. Transition to Taller Turbines
- The Trend: Modern wind turbines are reaching heights of over 150 meters, requiring larger and stronger tower sections.
- Impact on Roll Forming Machines:
- Demand for machines with the capability to produce larger-diameter and thicker tower profiles.
- Increased focus on precision and consistency to ensure the structural integrity of taller towers.
4. Localization of Manufacturing
- The Shift: Governments are encouraging local production of wind turbine components to reduce costs and boost regional economies.
- Why It Matters:
- Roll-forming machines enable manufacturers to set up localized production facilities, reducing transportation costs and emissions.
- Supports the creation of jobs and enhances supply chain reliability.
5. Sustainability and Recycling
- The Goal: Wind energy projects are prioritizing sustainability, from production to decommissioning.
- How Roll Forming Machines Help:
- Machines are designed to process recyclable materials, contributing to a circular economy.
- Energy-efficient designs reduce the carbon footprint of manufacturing processes.
Business Advantages of Investing in Wind Turbine Tower Section Roll Forming Machines
For manufacturers, investing in a high-quality Wind Turbine Tower Section Roll Forming Machine offers numerous benefits:
1. Cost Savings
- How It Helps:
- Reduces material waste through precise forming processes.
- Minimizes labor costs with automated operations.
- Lowers energy consumption with advanced motor systems.
2. Scalability
- What It Enables:
- Supports small-scale manufacturers entering the wind energy market.
- Provides flexibility to scale production as demand increases.
- Accommodates diverse project requirements, from onshore to offshore installations.
3. Competitive Advantage
- Why It Matters:
- High-quality tower sections improve the reliability and lifespan of wind turbines.
- Faster production times help manufacturers meet tight project deadlines.
- Advanced features like welding integration and real-time monitoring set manufacturers apart from competitors.
4. Alignment with Sustainability Goals
- The Impact:
- Eco-friendly operations enhance a company’s reputation in the renewable energy sector.
- Compliance with green building certifications and industry standards attracts more clients.
- Reduced carbon footprint contributes to global sustainability initiatives.
Additional FAQs About Wind Turbine Tower Section Roll Forming Machines
Question | Answer |
---|---|
Can the machine handle different material grades? | Yes, machines are designed to process various grades of steel and alloys, including high-strength materials. |
What is the maximum diameter of tower sections? | Machines can produce sections with diameters ranging from 2 meters to over 6 meters. |
Does Wuxi Sunway offer maintenance services? | Absolutely! Wuxi Sunway provides comprehensive maintenance and support to ensure optimal machine performance. |
Are custom configurations available? | Yes, machines can be customized to meet specific project and production requirements. |
What is the typical delivery time for a new machine? | Delivery times vary but typically range from 3 to 6 months, depending on customization needs. |
What industries can benefit from these machines? | Industries include renewable energy, heavy industrial manufacturing, and infrastructure development. |
Why Choose Wuxi Sunway Machinery for Wind Turbine Tower Section Roll Forming Machines?
Wuxi Sunway Machinery has established itself as a leader in roll-forming technology, offering unparalleled expertise and innovation. Here’s why they’re the preferred choice for wind turbine tower manufacturers:
- Global Expertise: Decades of experience in providing roll-forming solutions for renewable energy projects worldwide.
- Custom Solutions: Machines tailored to the unique demands of wind turbine tower production.
- Sustainability Focus: Eco-friendly designs that minimize waste and energy consumption.
- Comprehensive Support: From installation to training and maintenance, Wuxi Sunway ensures seamless operations.
- Proven Track Record: Trusted by clients across Asia, Europe, the Americas, and beyond.
- Cutting-Edge Technology: Features like IoT integration, AI-driven optimization, and modular configurations.
Conclusion: Powering Renewable Energy with Roll Forming Excellence
দ্য Wind Turbine Tower Section Roll Forming Machine is a cornerstone of the renewable energy revolution, enabling the efficient and sustainable production of wind turbine towers. By investing in these advanced machines, manufacturers can not only meet the growing demand for wind energy but also contribute to a cleaner, greener future.
Ready to lead the renewable energy charge? Contact Wuxi Sunway Machinery today to explore their state-of-the-art roll-forming solutions. Together, let’s power the world with precision and sustainability—one tower section at a time!