Chimney and ventilation systems are essential components in both residential and industrial setups, ensuring the safe and efficient expulsion of smoke, gases, and other emissions. With the rise of modular construction and stricter environmental regulations, the demand for precise, durable, and scalable chimney systems has surged. Enter the Chimney System Roll Forming Machine—a modern manufacturing marvel enabling the production of high-quality chimney system components at an industrial scale.
In this comprehensive guide, we’ll explore Chimney System Roll Forming Machines, their applications, key features, pricing, and why Wuxi Sunway Machinery stands out as an industry leader. Whether you’re a manufacturer, contractor, or supplier in the HVAC or construction sector, this guide will reveal how roll-forming technology is shaping the future of chimney system production.
What is a Chimney System Roll Forming Machine?
ক Chimney System Roll Forming Machine is a specialized industrial machine designed to produce a variety of chimney system components, such as flues, ducts, and connectors. These machines are designed to shape metal sheets into precise profiles through a continuous roll-forming process, ensuring structural integrity, dimensional accuracy, and high production efficiency.
These components are vital for chimney systems used in residential homes, commercial kitchens, industrial factories, and power plants. The roll-forming process allows manufacturers to meet the growing demand for energy-efficient and eco-friendly chimney systems while maintaining cost-effectiveness.
Applications of Chimney System Roll Forming Machines
The components produced by Chimney System Roll Forming Machines are essential to a wide array of industries and applications. Below is an overview of their primary use cases:
1. Residential Chimney Systems
- Use Case: Flue systems for wood-burning stoves, fireplaces, and heating systems in homes.
- Why It Matters: Roll-formed profiles ensure proper insulation, safety, and efficient smoke expulsion in residential setups.
2. Commercial Kitchens
- Use Case: Chimney ducts and exhaust systems for restaurants, cafeterias, and food courts.
- Why It Matters: Durable components withstand high heat and continuous operation in busy kitchens.
3. Industrial Ventilation Systems
- Use Case: Chimney systems for factories, warehouses, and manufacturing plants.
- Why It Matters: Corrosion-resistant materials ensure long-term performance and compliance with industrial safety standards.
4. Power Plants and Energy Facilities
- Use Case: Chimney flues for coal-fired, gas, or biomass power plants.
- Why It Matters: High-strength profiles can handle extreme temperatures and harsh environmental conditions, ensuring safe emission control.
5. Modular and Pre-Fabricated Construction
- Use Case: Pre-fabricated chimney systems for modular buildings and portable structures.
- Why It’s Crucial: Roll-forming machines enable rapid production of components, reducing construction timelines.
6. Retrofitting and Upgrades
- Use Case: Modernizing existing chimney systems to improve efficiency and meet updated standards.
- Why It Matters: Customizable profiles allow manufacturers to create components tailored for retrofitting projects.
Key Features of Wuxi Sunway Chimney System Roll Forming Machines
Wuxi Sunway Machinery is renowned for its precision-engineered roll-forming machines tailored to meet the specific requirements of chimney system manufacturing. Below are the features that set their machines apart:
1. Versatile Profile Production
- What It Offers: Machines can produce a variety of profiles, including round flues, rectangular ducts, and custom connectors.
- Why It’s Revolutionary: Supports the manufacturing of complete chimney systems in a single production line.
2. Material Compatibility
- Supported Materials:
- Stainless steel
- Galvanized steel
- Aluminum alloys
- Pre-coated and powder-coated metals
- Why It Matters: Enables manufacturers to produce components that are lightweight, corrosion-resistant, and durable.
3. High Precision and Tolerance
- What It Does: Produces profiles with tight tolerances, ensuring a perfect fit during installation.
- Why It’s Important: Guarantees leak-proof connections and optimal airflow in chimney systems.
4. Customizable Tooling Systems
- What It Includes: Interchangeable tooling systems for quick transitions between different profile designs.
- Why It Matters: Enhances flexibility for manufacturers catering to diverse industries and applications.
5. High-Speed Production
- Performance: Machines can produce up to 30 meters of profiles per minute, depending on the design.
- Why It Matters: Meets the high-volume demands of large-scale chimney system manufacturers.
6. Fully Automated Operations
- Features:
- PLC-controlled systems with a user-friendly interface.
- Real-time monitoring and error detection.
- Automated stacking and packaging systems.
- Why It’s Revolutionary: Reduces labor requirements while ensuring consistent quality and increased output.
7. Eco-Friendly Operation
- What It Offers: Energy-efficient motors and waste-reducing technologies.
- Why It Matters: Aligns with sustainability goals and reduces operational costs.
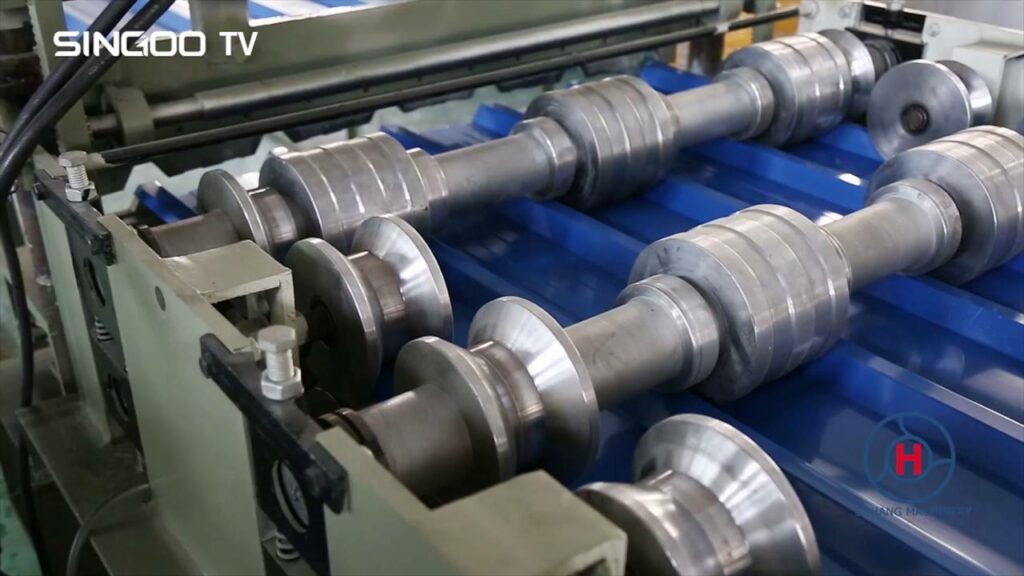
Production Workflow of a Chimney System Roll Forming Machine
The production process for chimney system components is designed for maximum efficiency and precision. Below is an overview of the workflow:
1. Decoiling
- Raw metal coils are loaded onto the decoiler, which feeds the material into the machine.
2. Leveling
- A leveling system ensures the material is flat and free from warping or defects before entering the roll-forming section.
3. Roll Forming
- The material passes through a series of rollers that gradually shape it into the desired profile, such as a flue or duct.
4. Cutting and Punching
- Integrated cutting units trim profiles to the required lengths, while punching systems create holes or slots for modular connections.
5. Surface Finishing (Optional)
- Additional treatments, such as powder coating or anti-corrosion finishes, can be applied to enhance durability and aesthetics.
6. Stacking and Packaging
- Finished profiles are automatically stacked and packaged for easy transportation and assembly.
Pricing of Chimney System Roll Forming Machines
The cost of a Chimney System Roll Forming Machine depends on its features, production capacity, and customization options. Below is a general pricing guide for 2025:
Machine Type | Capabilities | Price Range (USD) |
---|---|---|
Standard Machines | Basic profile production | $200,000–$400,000 |
High-Precision Machines | Advanced tolerances and multi-profile output | $400,000–$600,000 |
Fully Customizable Machines | Multi-material compatibility and custom features | $600,000–$1,000,000 |
For tailored pricing and financing options, contact Wuxi Sunway Machinery.
Advantages of Using Chimney System Roll Forming Machines
Investing in a Chimney System Roll Forming Machine offers substantial benefits for manufacturers:
1. Enhanced Efficiency
- High-speed operation reduces lead times and increases overall production output.
2. Precision and Consistency
- Ensures uniform quality across all components, minimizing installation errors.
3. Material Versatility
- Supports a wide range of materials, including corrosion-resistant and lightweight alloys.
4. Cost Savings
- Reduces material waste and labor costs, improving overall profitability.
5. Scalability
- Suitable for both small-scale manufacturers and large-scale production lines.
FAQs About Chimney System Roll Forming Machines
Question | Answer |
---|---|
Can the machine handle stainless steel? | Yes, the machine is optimized for stainless steel and other durable materials. |
What is the production speed? | Machines can produce up to 30 meters of profiles per minute, depending on the design. |
Does Sunway provide operator training? | Absolutely! Wuxi Sunway offers comprehensive training for operators and technicians. |
Are financing options available? | Yes, flexible financing options are offered to qualified buyers. |
Can the machine produce custom profiles? | Yes, it supports multi-profile capabilities for customized chimney system designs. |
What is the typical maintenance schedule? | Routine maintenance includes lubrication, inspection of rollers, and tooling calibration. |
Global Trends Driving the Adoption of Chimney System Roll Forming Machines
The growing demand for advanced chimney systems is fueled by global trends in construction, energy efficiency, and regulatory compliance. Let’s explore the key drivers of this demand:
1. Stricter Emission Regulations
- The Shift: Governments worldwide are implementing stricter regulations to reduce air pollution and greenhouse gas emissions.
- Impact on Chimney Systems: Manufacturers must produce flue systems that meet stringent emission control standards, ensuring the safe and efficient expulsion of smoke and gases.
- Why It Matters: Roll-forming machines enable the precision manufacturing of components that comply with these regulations, such as double-walled insulated flues and airtight connectors.
2. Rise in Modular and Prefabricated Construction
- The Trend: Prefabricated construction is on the rise, offering faster project completion and reduced costs.
- Impact on Chimney Systems: Modular chimney components are in high demand for quick installation in prefabricated residential and commercial projects.
- Why It’s Crucial: Roll-forming machines provide the scalability needed to mass-produce modular chimney components with consistent quality.
3. Growth in Renewable Energy Facilities
- The Opportunity: Biomass power plants, a key player in renewable energy, require advanced chimney systems to manage emissions.
- Impact on Chimney Systems: These facilities need corrosion-resistant and high-temperature-resistant flue systems.
- Why It’s Relevant: Roll-forming machines can produce specialized profiles tailored for renewable energy applications.
4. Urbanization and High-Density Living
- The Numbers: By 2030, nearly 60% of the global population will live in urban areas, driving the demand for high-rise residential and commercial buildings.
- Impact on Chimney Systems: Efficient and compact chimney systems are crucial for urban construction projects.
- Why It’s Important: Roll-forming machines can produce precise, space-saving components ideal for urban environments.
5. Focus on Energy Efficiency
- The Push: Energy-efficient systems are becoming mandatory in new construction projects to reduce energy consumption and costs.
- Impact on Chimney Systems: Advanced flue designs with insulation and airtight sealing improve the efficiency of heating systems.
- Why It’s Exciting: Roll-forming technology supports the production of energy-efficient chimney components.
6. Retrofitting and Modernization
- The Challenge: Aging chimney systems in older buildings need to be upgraded to meet modern safety and efficiency standards.
- Impact on Chimney Systems: Customizable profiles are required for retrofitting projects.
- Why It’s Important: Roll-forming machines allow manufacturers to produce bespoke components for seamless integration into existing systems.
Technological Advancements in Chimney System Roll Forming Machines
Technological innovation is driving the evolution of Chimney System Roll Forming Machines, making them faster, smarter, and more versatile. Let’s explore the cutting-edge advancements shaping the industry in 2025:
1. AI-Powered Quality Control
- What It Does: Artificial intelligence monitors production parameters, detects defects, and automatically adjusts settings to optimize output.
- Benefits:
- Guarantees consistent quality across all profiles.
- Reduces material waste by identifying issues early.
- Enhances overall production efficiency.
2. IoT Integration for Smart Manufacturing
- How It Works: IoT sensors collect real-time data on machine performance, material usage, and output quality.
- Advantages:
- Enables remote monitoring and predictive maintenance.
- Reduces downtime caused by equipment failures.
- Supports integration into Industry 4.0 smart factories.
3. Advanced Material Processing
- The Innovation: Modern machines can process a wider range of materials, including pre-coated metals, stainless steel, and aluminum alloys.
- Why It’s Revolutionary:
- Expands the range of chimney system applications.
- Supports lightweight yet durable component production.
- Meets the demands of diverse industries, from residential to industrial.
4. Servo-Controlled Precision
- The Technology: High-precision servo motors control rollers, cutters, and punching units.
- Why It’s Crucial:
- Ensures flawless dimensions and smooth finishes.
- Enhances the structural integrity of chimney components.
- Reduces energy consumption, aligning with sustainability goals.
5. Modular Tooling Systems
- What It Offers: Interchangeable tooling systems allow for quick transitions between different profile designs.
- Why It’s Important:
- Simplifies the production of custom chimney components.
- Reduces downtime during tooling changes.
- Enhances flexibility for manufacturers serving multiple markets.
6. Automated Stacking and Packaging
- What It Includes: Machines are equipped with automated systems for stacking and packaging finished components.
- Why It Matters:
- Streamlines post-production processes.
- Reduces the need for manual labor.
- Improves overall operational efficiency.
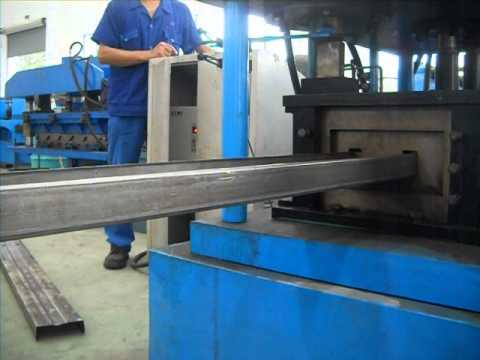
Environmental Impact of Chimney System Roll Forming Machines
Sustainability is a critical focus across industries, and Chimney System Roll Forming Machines align with eco-friendly manufacturing practices. Here’s how these machines contribute to greener production:
1. Reduced Material Waste
- How It Works: Roll-forming machines shape metal with high precision, minimizing scrap and offcuts.
- Impact: Conserves raw materials, reduces environmental impact, and lowers production costs.
2. Use of Recyclable Materials
- What It Supports: Machines can process recyclable materials like aluminum and galvanized steel.
- Why It Matters: Promotes a circular economy by enabling material reuse and reducing landfill waste.
3. Energy-Efficient Operation
- The Innovation: Advanced machines consume less energy while maintaining high production speeds.
- Why It’s Crucial: Helps manufacturers reduce their carbon footprint and operational costs.
4. Localization of Production
- What It Enables: Manufacturers can produce chimney components locally, reducing the need for long-distance transportation.
- Outcome: Cuts down on emissions associated with shipping and enhances supply chain reliability.
Additional FAQs About Chimney System Roll Forming Machines
Question | Answer |
---|---|
Can the machine handle pre-coated materials? | Yes, it is designed to process pre-coated and pre-painted metals with precision. |
What is the typical production speed? | Machines can produce up to 30 meters of profiles per minute, depending on the design. |
Does Wuxi Sunway provide after-sales support? | Absolutely! Comprehensive after-sales support, including maintenance and troubleshooting, is provided. |
Are financing options available? | Yes, flexible financing options are offered to qualified buyers. |
What industries use these machines? | Industries include residential construction, commercial kitchens, industrial ventilation, and power plants. |
What is the machine’s expected lifespan? | With proper maintenance, these machines can last 10–15 years or more. |
Why Choose Wuxi Sunway Machinery for Chimney System Roll Forming Machines?
Here’s why Wuxi Sunway Machinery is the preferred choice for chimney system manufacturers worldwide:
- Decades of Expertise: Deep experience in designing innovative roll-forming solutions for HVAC and chimney systems.
- Global Reputation: Trusted by clients across Asia, Europe, the Americas, and beyond.
- Customization Excellence: Machines tailored to meet specific chimney system designs and material requirements.
- Sustainability Leadership: Eco-friendly designs that minimize material waste and reduce energy consumption.
- Cutting-Edge Technology: Features like IoT integration, AI-powered quality control, and energy-efficient systems.
- Comprehensive Support: From installation to training and maintenance, Sunway ensures seamless operations and customer satisfaction.
Conclusion: Shaping the Future of Ventilation Systems
দ্য Chimney System Roll Forming Machine is revolutionizing how chimney systems are designed and manufactured, enabling precision, scalability, and sustainability. Whether you’re producing components for residential, commercial, or industrial applications, these machines provide the innovation and efficiency needed to excel in 2025 and beyond.
Ready to elevate your manufacturing operations? Contact Wuxi Sunway Machinery today to explore their advanced roll-forming solutions. Together, let’s redefine the future of chimney system manufacturing—one profile at a time.