Overview of snap lock standing seam roll forming machine
Snap lock standing seam roll forming machines are equipment used to produce standing seam metal roofing panels. They form the distinctive raised vertical seam along the panel edges which interlock to create a weathertight roof surface.
These versatile roll formers have become prevalent around the world due to benefits like:
- High strength and durability from interlocking seams
- Water tightness and weather resistance
- Aesthetic appeal of vertical seam architecture
- Lower installation time and labor
- Compatibility with many roof designs
- Customization of panel dimension and profiles
The working process involves feeding metal coil stock into a series of roller dies to bend and fold the sheet into panel profiles with raised seams. The locking process clinches the seams together tightly for stability.
Advanced computerized controls allow precision forming to exact specifications of length, width, thickness, contour, degree of arch etc.
Machine Type | Description | Typical Applications |
---|---|---|
Portable | Compact units mounted on wheel frame with own power source for site roll forming | Smaller roofs, remote sites, vessel hulls, truck rear panels |
Fixed | Stationary high capacity production lines with multiple forming stages | Large commercial and industrial roofing projects |
CNC Roll Former | Computer numerical control for precision custom profiles | Architectural facades, customized roofing, special panels |
Double Layer | Additional top roller to form double layer seams | High strength hurricane proof building roofs |
Automatic | Fully automated material feed and production for mass output | Roofing component manufacturing plants |
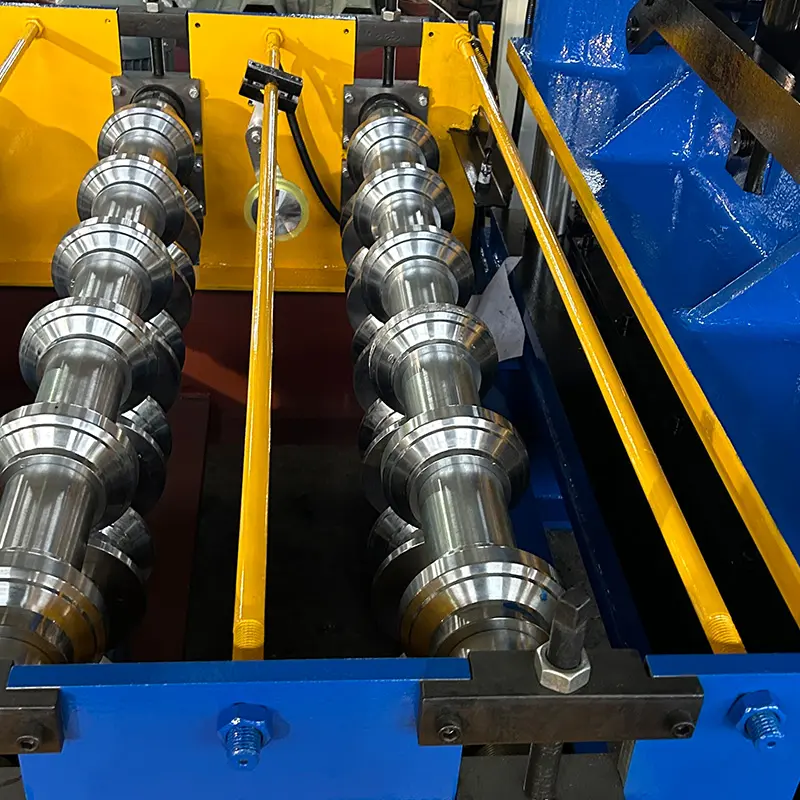
Working Process
The working principle involves passing metal coil feed stock through a series of roller stations in sequence to gradually turn the flat sheet into panel sections with raised vertical seams along the edges.
The process starts by loading a large coil of thin gauged metal sheet of material like steel, aluminum or copper onto an uncoiler. The sheet gets fed into a leveler machine to remove bends and warp. Next ink jets or printing rollers add color or patterns before punching stations cut ventilation holes.
The core snap lock forming section has top and bottom rollers engraved with the specified profile. As the sheet passes between alternating stations, it gets bent into the seam pattern piece by piece. Separate stations may form additional ridges, reinforcement ribs, or contours as per the design.
The snap lock rolling machine clinches the seams together to interlock panels edge to edge. The cutoff shear then slices formed panels to the set length as they are stacked for collection or loading for shipping.
Advanced computerized controls automate the length, speed, and alignment during the forming sequence for precision results.
Material Feeding
Feed Method | Description | Typical Applications |
---|---|---|
Batch | Manual loading of straight sheet sections | Low volume job sites |
Coil | Automated reel fed lines from bulk wound coils | High production manufacturing |
Welding | In-line joining of sheet coils for continuous high volume input | Component plants, building material suppliers |
Automatic | Programmable auto-loading from stack/pallet | CNC automated precision production |
Manual batch feed involves loading straight sheet segments into the intake area. This is generally used for custom small batches at construction sites using portable roll formers.
For large scale forming, automated lines unwind bulk coils of thin metal loaded on cylinders called decoilers. Welding machines then join each coil end to end for continuous high speed feeding into the roll stations.
Fully automatic computerized feed systems robotically pick sheet from pallets to constantly supply material to the snap lock roll forming equipment.
Profile Forming
Snap lock machines utilize a series of top and bottom roller dies to gradually turn flat metal sheet into panel sections with raised vertical side seams.
Common panel profiles formed are illustrated here:
Standard Seam
The standard interlocking seam has a simple vertical ridge shape. Installation involves toggles, cleats and clips to secure panels.
Double Lock Seam
The double seam has two parallel indentations with a bridge in between. The double ridge provides extra strong weather-tight fitting.
Triple Lock Seam
Three ridges give maximum seam strength and rigidity. The triple lock is inherently stable needing fewer mounting clips.
In addition to the seam shape, the entire panel can be profiled as corrugated, box ribbed, or tapered. Special architectural forming can emboss custom decorative shapes.
Advanced CNC snap lock roll forming machinery can produce complex profiles with steps and contours for specialized applications like rainscreen facades, canopy roofs, equipment housings etc.
-
Standing Seam Roof Panel Curving Machine
-
ব্যারেল ঢেউতোলা রোল ফর্মিং মেশিন
-
Stand Seaming Roof Panel Roll Forming Machine
-
ডাউনস্পাউট পাইপ রোল তৈরির মেশিন
-
গটার রোল তৈরির মেশিন
-
Trapezoidal Panel Roll Forming Machine
-
রিজ ক্যাপ রোল ফর্মিং মেশিন
-
ডাবল লেয়ার প্যানেল রোল তৈরির মেশিন
-
ছাদের টাইল প্যানেল রোল তৈরির মেশিন
Custom Panel Design
Today’s computer-controlled lines offer flexible specification of all critical panel measurements:
Feature | Description | Typical Range |
---|---|---|
Width | Formed section width | 300 mm to 1000 mm |
পুরুত্ব | Metal sheet gauge | 0.4 mm to 2 mm |
Length | Cutoff panel length | 300 mm to 10000 mm |
Contour | Profile shape – tapered, angled, curved etc. | Various geometric designs |
Seam Height | Vertical interlock projection | 16 mm to 65 mm |
Material | Steel, aluminum, copper alloys | Grade 304, 5052, 110 etc. |
Coating | Color coatings, insulation layers | PE, PVDF, stone coat |
Pattern | Graphics – dots, lines, logos | Digital printing options |
Perforation | Hole shapes – round, square | Various spacing, sizes |
Reinforcement | Ribs, ridges for strength | As needed |
Advanced 3D modeling software allows architects and building contractors to digitally design one-off panels to exacting specifications.
The CAD files get directly imported into the CNC snap panel roll forming machine control which then replicates the complex profile in the physical world by precision metal forming.
Such flexibility enables creation of distinctive building envelopes from standard snap lock wall panel modules.
Cutting & Slicing
Formed panel sections coming out the exit end of the machine need trimming to final size. This is done by cutoff shear blades mounted just past the seaming assembly.
Cutting Method | Descripton | অ্যাপ্লিকেশন |
---|---|---|
Shearing | Sharp blades slice sheets | Most universal, lower cost |
Punching | Hydraulic press cutouts | High tonnage only |
Laser | CNC laser burns edges | Precise, no distortion |
Waterjet | High pressure jet cuts seams | Delicate, detailed shapes |
As individual panels get sliced off the continuously forming sheet, they can be manually moved or automatically stacked. Programmable logic controllers stage panels elegantly for easy lifting.
Many snap lock roll formers allow adding custom components like insulation, membranes, wiring channels or mounting hardware between stations before final cutoff. This facilitates integrated production of finished roofing or wall assemblies.
Supplier Landscape
China is the global hub manufacturing snap lock roll forming equipment at both value and premium quality levels:
প্রতিষ্ঠান | Location | Product Grade | Price Range |
---|---|---|---|
Botou Xianfa | Hebei | Value | $1500 – $8000 |
Jiangyin Hydraulic | Jiangsu | Value | $2000 – $15000 |
Kuangtai | Shandong | Premium | $5000 – $30000 |
JinDeXin | Shanghai | Premium | $10000 – $50000 |
In addition to complete machines, most suppliers offer roll forming component kits or sections allowing customized layouts. Taiwan, India, Turkey, Europe also have manufacturers of standing seam rolling mills.
Buying through Alibaba allows accessing small scale equipment at economical pricing or fully loaded automated lines for panel plants at premium investment.
Pricing Trends
Costs depend on:
- Production Throughput: Sheet width & line speed
- Level of Automation: Manual to fully automated CNC
- Build Quality: Component durability & precision
- Feature Set: Forming flexibility, controls intelligence
Fig.3 – Approximate Snap Lock Standing Seam Roll Former Cost by Capability
As capability, durability, precision, and automation increases, so does the capital cost of these roll forming machines on a progressive curve. High volume efficient systems with advanced software functionality, large production throughputs, and heavy duty construction represent premium investments likely north of $100,000.
Value range basic manually operated machines producing simple seam profiles at slower speeds can cost between $2000 to $15000.
Installation & Operation
Snap lock roll forming equipment requires stable foundations for smooth high speed running:
Parameter | বিস্তারিত |
---|---|
Site | Level surface, away from vibrations |
শক্তি | Dedicated line, voltage stabilizer |
Compressed Air | Water extractor, pressure regulator |
Exhaust | Fume extractor chimney |
Safety | Warning signs, access barriers |
Commissioning | Step-by-step testing & debug |
প্রশিক্ষণ | Operator instructions manual |
Portable mobile units can work outdoors and get powered via standalone diesel generators. But fixed production lines are best situated on hardened concrete floors in covered shelters with ample provision for material staging conveyors and heavy forklift movement.
Thorough trial runs during commissioning ensure smooth performance before final handover. Technical troubleshooting support from the machine builder helps resolve initial hiccups at the start.
Clear standard operating procedures train workers manage the forming line for steady-state functioning 365 days a year.
Maintenance
Proactive inspection and preventative care minimizes unplanned downtime:
System | Action | Frequency |
---|---|---|
Rollers | Visual check for dents or cracks | Daily |
Bearings | Lubricate chains | Weekly |
Blades | Inspect shear pins and edges | Monthly |
Hydraulics | Check cylinders, valves & hoses | Quarterly |
Motors | Test load, temperature rise | Yearly |
Automation | Diagnostics & debug sequence | As needed |
Safety | Review emergency stop, access guards | Biannual |
Daily clean-ups ensure no sheet metal scrap debris interferes with the tight clearances between roller stations. Chains, sprockets and machine cutting edges need periodic replacement depending on processed tonnage.
Software bugs or servo electrical faults may intermittently require an automation specialist for troubleshooting support. But overall, the modular components make physical servicing quite straightforward.
Choosing Suppliers
Consider these aspects for selecting reliable snap lock roll form line vendors:
Parameter | বিস্তারিত | Weight |
---|---|---|
Product Quality | Material grade, precision finish | High |
Delivery Reliability | Production capacity assurance | High |
Market Reputation | Client feedback, trustworthiness | Medium |
Design Expertise | Profile innovation, process configurability | Medium |
Service Quality | Responsiveness and technical support level | Medium |
Pricing | System affordability, TCO | Low |
Build quality directly impacts output so that scores highest along with supply assurances for uninterrupted production scaleup. Design flexibility for customization also weighs in selecting manufacturers. Dealers offering proprietary panel shapes or configurations can justify premium value pricing for differentiated systems. Hence cost plays a lower consideration compared to reliability criteria.
Local country representatives help manageinventory, maintenance, training, and technical troubleshooting for imported Chinese equipment.
Limitations & Challenges
Some downsides of snap lock roll formed panel roofing to consider:
Limitations:
- Higher material cost than standard corrugated sheets
- Need periodic retensioning unlike integral systems
- Seam breaches can rapidly deteriorate large sections
- Snow buildup needs active maintenance
Challenges:
- Dust contamination can impede interlock
- Staining near vents require detergent cleaning
- Storm uplift limits unsecured sheet area
- Metal dissimilar welding during install
Joint lifecycle costs may exceed competing roof materials when accounting for extensive steel upkeep over decades. Thus snap lock roll formed panels find optimal balance for large commercial buildings despite limitations versus composite alternatives.
Pros & Cons Relative to Other Roof Types
Parameter | Standing Seam | Asphalt | Steel Tile | Composite Slate |
---|---|---|---|---|
Durability | High | Medium | High | High |
Wind Uplift Resistance | High | Low | High | Medium |
Fire Rating | Medium | High | High | High |
Seam Strength | High | Medium | Medium | Low |
Thermal Movement | Medium | High | Low | Low |
Color Options | High | Low | Medium | High |
Reusability | High | Low | Medium | Medium |
Eco-Friendliness | Medium | Low | High | High |
Installation Speed | High | High | Medium | Low |
Noise During Rain | High | Low | High | Medium |
Indicative Price Per Sq.Ft | $5 | $0.5 | $12 | $15 |
Over 60 years, snap lock standing seam metal expectations average around $3 per square foot per year – on par with conventional roofing. Superior wind loading capacity and weathertightness justify premiums over asphalt and slate. Light-weight steel tiles challenge on longevity. Easy formation of customized contours keeps architectural interest high despite drawbacks.
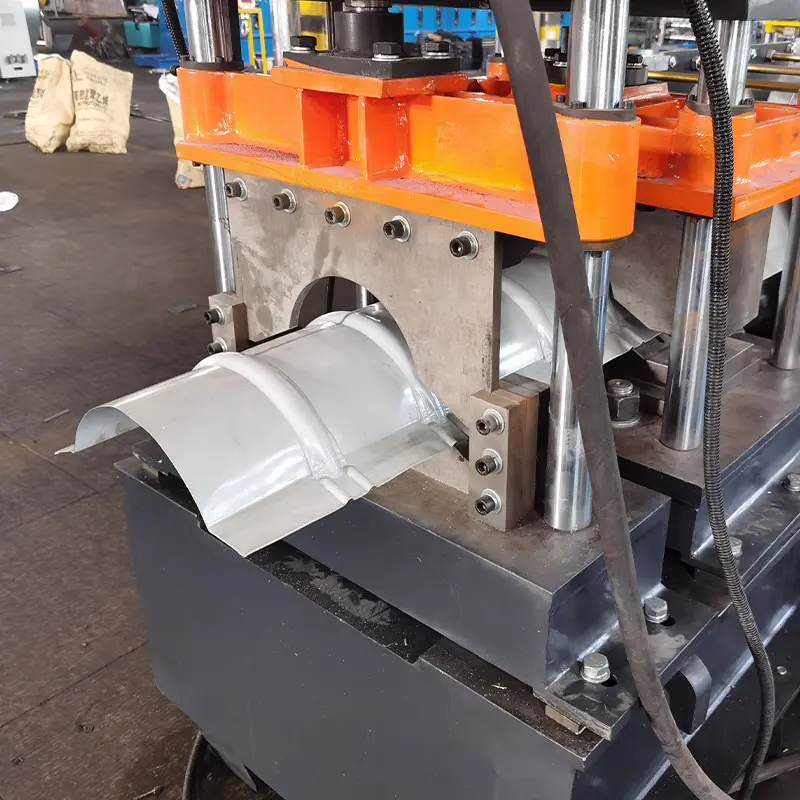
Future Outlook
Industry 4.0 technologies will drive the next evolution of snap lock roll forming:
- IoT monitoring via sensors for predictive maintenance
- Smart servos & drives for self-tuning performance
- Automated inspection & sorting of panels
- AI-generated designs and machine programming
- AR/VR simulations for virtual factory modeling
- Carbon composites producing lighter seam sheets
- High speed laser welding for stronger locks
- Hybrid metal/polymer panels for green buildings
- Higher recycling to combat environmental waste
With such advances, snap lock roll formed standing seam cladding retains cost competitiveness while meeting sustainability goals into the foreseeable future.
FAQs
Question | Answer |
---|---|
Do panels come with insulation backing? | Integrated multi-layer sandwich panels with foam insulation cores minimize heat gain/loss versus field laminated assemblies. Many machines can insert sheets during forming itself. |
Does oil canning distort reflections? | Minor waviness in flat profile areas causes issues only for mirror finish facades. Deeper seaming rigidity reduces this oil canning disturbance for most applications. |
How long do these roofs last? | With periodic resealing and assuming no weather catastrophes or abusive damage, snap lock panels retain integrity over 60+ years matching expected building lifespan. |
Is heavy snow sliding dangerous? | Avalanche stops, mounted snow guards, lowered pitch angles ensure metal sheeting does not release accumulated frozen sheets aggressively. Maintenance clears excess buildup. |
Can standing seams get retrofitted? | Full structural analysis would evaluate load capacities for overlaying new snapped panels or retainers atop existing builds. Superior durability recoups costs long term. |