When it comes to shaping and molding metal, few machines are as versatile and indispensable as the রোল গঠনের মেশিন. If you’re in the construction or manufacturing business, or even just curious about industrial machinery, understanding the role and efficiency of roll forming machines is vital. In this in-depth guide, we’ll walk you through everything you need to know: from what roll forming machines do, to different types, their working processes, and even how to choose the best supplier.
Whether you’re just browsing for knowledge or ready to invest in this machine, this article is designed to give you all the information in one place. So, buckle up, and let’s roll—pun intended!
একটি রোল ফর্মিং মেশিন কি?
ক রোল গঠনের মেশিন is a piece of equipment designed to shape flat metal strips into precise profiles. This process, called roll forming, involves feeding the metal through a series of consecutive rollers. Each set of rollers bends the metal slightly until the desired cross-sectional shape is achieved.
This method is highly efficient, especially for producing long metal profiles in high volumes. Roll forming is primarily used for materials like steel, aluminum, and copper, and is widely employed in the construction industry for products like roofing sheets, wall panels, and door frames.
Key Features of Roll Forming Machines
- Continuous bending process
- Suitable for long profiles
- Works with metals such as steel, aluminum, and copper
- High production efficiency
- Minimal material waste
- Customizable to produce different shapes and sizes
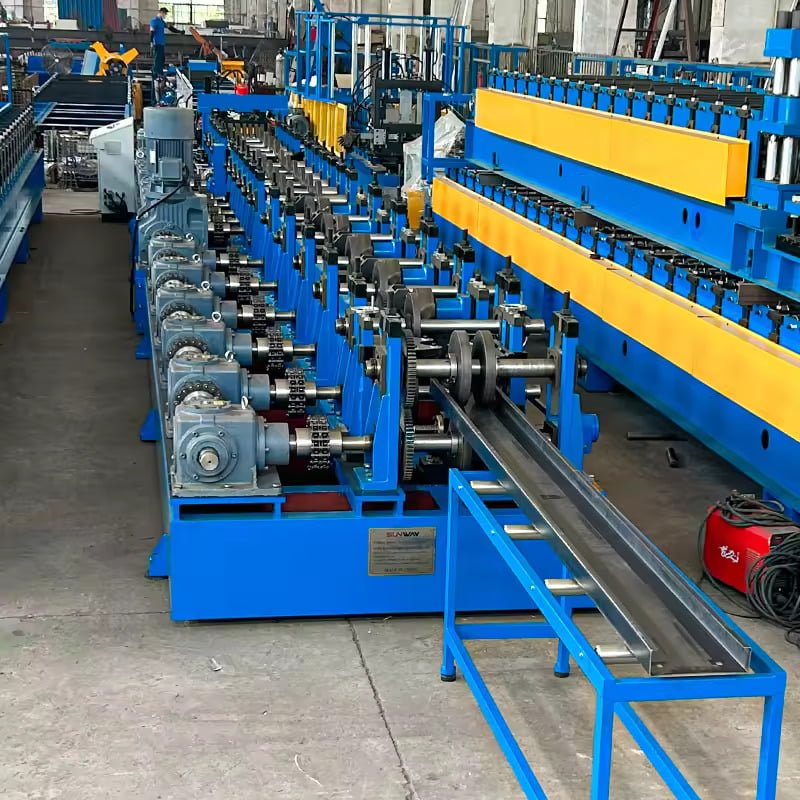
Types of Roll Forming Machines: Tailoring to Different Needs
রোল গঠন মেশিন come in various shapes and sizes, each tailored for specific applications. Here, we’ll dive into the specific types of roll forming machines, categorized by the functions they serve.
Machine Type | Description |
---|---|
Single-stand machine | One set of rollers used, suitable for simple shapes with low production volumes. |
Multi-stand machine | Consists of multiple roller stations for more complex profiles and higher output. |
Portable roll forming | Smaller, mobile machines used directly on construction sites. |
Precision roll forming | High-accuracy machines used for parts requiring tight tolerances. |
Automated roll forming | Fully automated machines with minimal human intervention, enhancing productivity. |
High-speed roll forming | Designed for high output rates, suitable for mass production environments. |
Hydraulic roll forming | Uses hydraulic force for bending heavier and thicker materials. |
Servo-driven machine | Equipped with servo motors for more precise control over the forming process. |
CNC roll forming machine | Controlled by a computer, allowing for highly customizable shapes and profiles. |
Custom roll forming | Built specifically to meet customer needs, tailored for unique product designs. |
Each type of machine has its own pros and cons, depending on the requirements of your production line. Understanding which model suits your needs can save you time, money, and headaches down the road.
How Does a Roll Forming Machine Work? The Complete Process
You may be wondering, “How exactly does a roll forming machine work?” It’s a fascinating process, one that turns raw metal into precise profiles through a continuous and automated system. Below, we’ll break down the entire working process of a roll forming machine:
Step-by-Step Roll Forming Process
- Material Loading: Raw metal strips or coils are fed into the machine. Materials like steel, aluminum, or copper are most commonly used.
- Initial Straightening: The material passes through a leveling device that flattens it out before the forming begins.
- Roller Stations: The strip passes through multiple roller stations, each station bending the metal slightly more until the final shape is achieved.
- Cutting to Length: After the desired profile is formed, the material is cut to length using cutting tools—this could be a mechanical cutter or laser.
- Collection and Stacking: The finished products are collected and stacked, ready for shipping or further processing.
This seamless operation is highly efficient and minimizes waste, making it perfect for mass production.
Key Components of a Roll Forming Machine and Their Functions
Each part of a roll forming machine plays a crucial role in ensuring it runs smoothly and efficiently. Let’s take a look at the key components and their functions.
Component | Function |
---|---|
Rollers | Responsible for shaping the metal into the desired profile. |
Material feeder | Feeds the raw metal into the machine at a consistent rate. |
Straightening unit | Flattens the material before it enters the roller stations. |
Cut-off unit | Cuts the formed metal to the required length after shaping. |
Motor (electric or hydraulic) | Powers the rollers and other mechanical parts of the machine. |
Controller (CNC or manual) | Controls the operation and adjusts parameters like speed and force. |
Guide rolls | Keep the metal strip aligned as it moves through the machine. |
আনকোয়লার | Holds and releases the metal coil into the machine. |
Punching system | Punches holes or slots into the material during the forming process. |
-
দ্রাক্ষাক্ষেত্র পোস্ট রোল ফর্মিং মেশিন
-
স্বয়ংক্রিয় আকার পরিবর্তনযোগ্য সিগমা Purlin রোল ফর্মিং মেশিন
-
বৈদ্যুতিক মন্ত্রিসভা ফ্রেম রোল গঠনের মেশিন
-
দিন রেল রোল ফর্মিং মেশিন
-
তারের মই রোল ফর্মিং মেশিন
-
পিভি মাউন্টিং বন্ধনী সি শেপ প্রোফাইল রোল ফর্মিং মেশিন
-
তারের ট্রে রোল ফর্মিং মেশিন
-
CZ Purlin চ্যানেল কোল্ড রোল ফর্মিং মেশিন সম্পূর্ণ অটো গ্যালভানাইজড স্টিল প্রোফাইল
-
পিভি মাউন্টিং ব্র্যাকেট রোল ফর্মিং মেশিন (HAT / ওমেগা প্রোফাইল)
Machine Speed and Efficiency: What to Expect from Roll Forming Machines
One of the key factors to consider when purchasing a রোল গঠনের মেশিন is its speed and efficiency. This is particularly crucial if you’re operating in a high-volume production environment. Let’s look at typical speeds and how they affect productivity.
Machine Type | Average Speed | Efficiency |
---|---|---|
Single-stand machine | 5-10 meters per minute | Lower efficiency, suited for small production runs. |
Multi-stand machine | 20-30 meters per minute | High efficiency, best for complex and high-volume tasks |
High-speed roll forming | 40-100 meters per minute | Extremely efficient for mass production. |
Precision roll forming | 10-15 meters per minute | Slower speeds but extremely high precision. |
Hydraulic roll forming | 5-15 meters per minute | Slower but ideal for heavy materials. |
Customized Mechanical Parameters for Roll Forming Machines
Every production line is different, and that’s why customization is often necessary. You can adjust several mechanical parameters to meet specific manufacturing needs.
Parameter | Description |
---|---|
Material thickness | Ranges from 0.3mm to 5mm, depending on the type of metal. |
Profile width | Can vary based on customer requirements; typically ranges between 100mm to 800mm |
Forming stations | Number of stations can be customized based on profile complexity. |
Cutting length | Adjustable to produce different product sizes, typically from 0.5 meters to 12 meters. |
Punching capabilities | Customizable punching patterns for holes, slots, or notches. |
Motor power | Can be adjusted based on the material and production speed. |
Controller type | Choose between CNC, manual, or semi-automated systems. |
Applications of Roll Forming Machines: Where Are They Used?
Roll forming machines are versatile and have a broad range of applications. Here’s a list of industries and products where these machines are commonly used.
আবেদন | Description |
---|---|
Roofing and Wall Panels | Corrugated sheets used in construction for roofing and wall cladding. |
Door and Window Frames | Produces frames for both residential and industrial buildings. |
Automotive Industry | Creates metal parts for vehicle frames and structural elements. |
HVAC Ducts | Used in the production of ductwork for heating, ventilation, and air conditioning. |
Steel Furniture | Shapes metal profiles used in office and industrial furniture. |
Electrical Cabinets | Produces enclosures for electrical systems and control cabinets. |
Solar Panel Frames | Forms metal profiles for mounting solar panels on rooftops. |
Storage Systems | Creates shelves, racks, and other storage solutions. |
Fencing and Guardrails | Produces safety barriers and fences for highways and industrial settings. |
Cable Trays | Shapes metal into trays that support electrical wiring. |
Installation, Operation, and Maintenance of Roll Forming Machines
Ensuring the proper installation, operation, and maintenance of a roll forming machine is essential for achieving long-term efficiency and performance.
Process | বিস্তারিত |
---|---|
Installation | Requires proper alignment of the machine, electrical connections, and hydraulic setup. |
Operation | Typically requires trained operators who understand material feed rates and machine controls. |
Maintenance | Regular lubrication, cleaning, and replacement of worn-out components are crucial for longevity. |
Safety Measures | Include emergency stops, safety guards, and regular machine inspections. |
Troubleshooting | Problems like material misalignment or roller wear can be resolved with timely intervention. |
Choosing the Right Supplier: A Key Decision
When investing in a roll forming machine, picking the right supplier can make all the difference. Here’s a breakdown of what you should consider when choosing a supplier.
Factor | What to Look For |
---|---|
Price Range | Compare prices from different suppliers. Machines can range from $50,000 to $200,000. |
Reputation | Research customer reviews and industry reputation. |
Support and Warranty | Look for suppliers that offer extended warranties and good after-sales support. |
কাস্টমাইজেশন | Ensure the supplier can meet your specific customization needs. |
Location | Choose a supplier that can provide timely delivery and support services. |
Suppliers and Price Range
Supplier | Price Range (USD) | Location |
---|---|---|
স্যামকো মেশিনারি | $60,000 – $150,000 | Canada |
Jupiter Roll Forming | $50,000 – $180,000 | ভারত |
Yoder | $100,000 – $250,000 | USA |
Hangzhou Roll Forming | $45,000 – $120,000 | China |
ফরমটেক গ্রুপ | $80,000 – $200,000 | USA |
Pros and Cons of Roll Forming Machines: Advantages and Limitations
Like any industrial equipment, roll forming machines have their strengths and weaknesses. Let’s dive into a comparison of the pros and cons.
Advantages
- High Production Efficiency: Once set up, the machine can run continuously, producing a large volume of metal profiles with minimal downtime.
- Versatility: Can be used for a wide variety of materials and profiles.
- Minimal Waste: The continuous roll forming process reduces scrap metal waste, making it cost-effective and environmentally friendly.
- Precision: Machines are highly accurate, producing parts with tight tolerances.
- কাস্টমাইজেশন: Easily customizable to produce different shapes and sizes for various industries.
Limitations
- High Initial Investment: The upfront cost of purchasing and setting up a roll forming machine can be substantial.
- Specialized Skills Required: Operators need proper training to handle the machines effectively.
- Limited to Long Production Runs: Roll forming is best suited for long production runs, making it less efficient for small batches.
How to Choose a Roll Forming Machine Supplier
Choosing the right supplier is crucial when investing in a roll forming machine. Here are the key considerations:
Factors to Consider When Choosing a Supplier
- Reputation: Always go with suppliers who have a proven track record in delivering high-quality machines.
- কাস্টমাইজেশন: Make sure the supplier can meet your exact requirements in terms of machine design and output.
- Support Services: Post-sales support, including installation, maintenance, and repairs, is essential.
- Price: While price is important, it shouldn’t be the only deciding factor. Focus on the value offered by the supplier.
- Warranties: A supplier that provides a good warranty indicates confidence in their product.
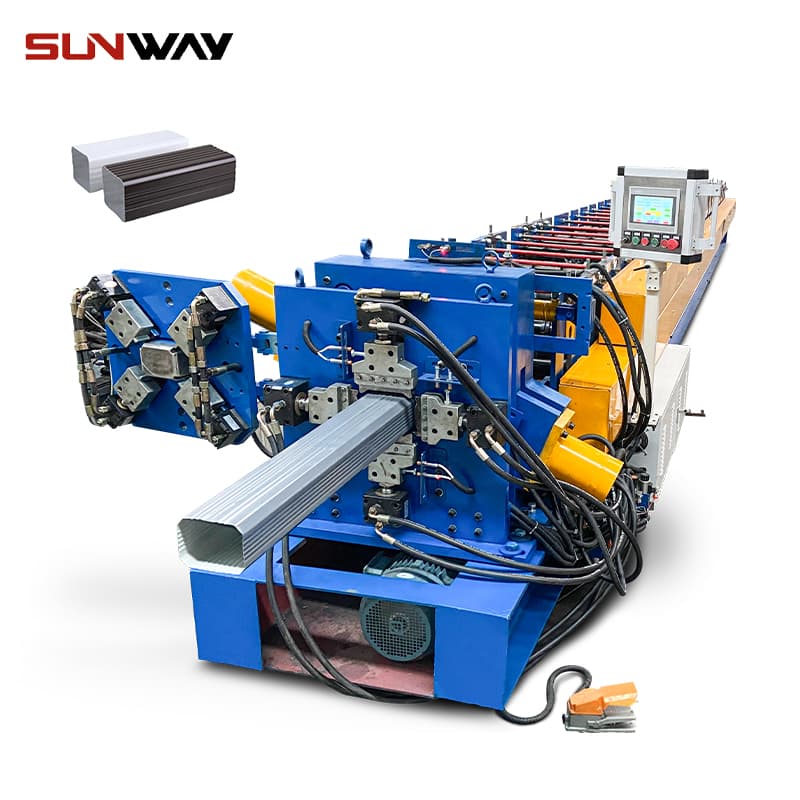
FAQs
Question | Answer |
---|---|
What is a roll forming machine used for? | A roll forming machine is used to shape flat metal strips into desired profiles for construction and industrial purposes. |
Can roll forming be customized? | Yes, roll forming machines can be customized to produce a wide range of shapes, sizes, and designs. |
What materials can be used in roll forming? | Metals such as steel, aluminum, copper, and zinc are commonly used in roll forming machines. |
How fast are roll forming machines? | Speeds can range from 5 meters to 100 meters per minute, depending on the type of machine and material. |
How much do roll forming machines cost? | Prices vary widely, from $50,000 to over $200,000, depending on the machine’s capabilities. |
উপসংহার
By now, you should have a solid understanding of what a রোল গঠনের মেশিন is, how it works, and whether it’s the right fit for your production needs. Whether you’re looking for high-volume production or intricate custom profiles, there’s a machine out there for you. The key is understanding your specific requirements and matching them with the right machine and supplier.
By following this guide, you’re well on your way to making an informed decision that will benefit your business for years to come.