Double furring ceiling roll forming machines are used to produce double furring ceiling panels from coil metal sheets. This advanced equipment forms the sheet metal into specialized ceiling panel profiles with double furring features.
Double Furring Ceiling Roll Forming Machine Equipment Guide
Equipment Type | বিস্তারিত |
---|---|
Coil feeder | Unwinds metal coil and feeds into roll former |
Roll forming stations | Progressively form the sheet into desired profile with rolls |
পাঞ্চিং ইউনিট | Punches holes for installation |
Cutting machine | Cuts formed panels to required length |
This core equipment produces the double furring panels. Additional equipment can be added for automation:
- Decoilers for easy coil loading
- Coil car for moving coils
- Welding machine to weld framing
- Supporting conveyors
- Hydraulic system
- Control panel
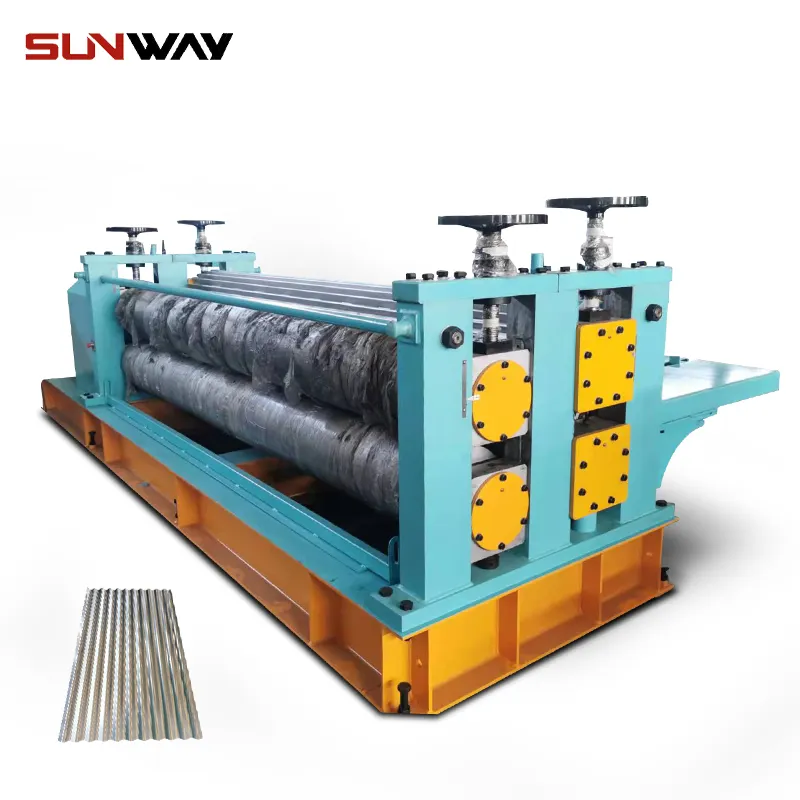
Double Furring Ceiling Roll Forming Process
The double furring ceiling roll forming process starts by loading a coil of thin gauge metal sheet into thedecoiler or coil feeder. The sheet gets unwound and fed into the rolling stations.
Each rolling station progressively forms the sheet further with precision rolls. The stations bend and shape the sheet into the desired double furring panel profile. Common profiles include box ribbed, wedge, butterfly, wave, and other geometric patterns.
As the formed sheet exits the last station, it moves through the punching unit. This punctures installation holes into the panel at fixed intervals.
Finally, the cutting machine slices the long panel at the required length into individual pieces. The finished double furring ceiling panels exit the roll former automatically.
This continuous roll forming process can create panels of any length by adjusting the cut-off position. Operators can select custom lengths per project requirements.
-
বৈদ্যুতিক মন্ত্রিসভা ফ্রেম রোল গঠনের মেশিন
-
দিন রেল রোল ফর্মিং মেশিন
-
তারের মই রোল ফর্মিং মেশিন
-
পিভি মাউন্টিং বন্ধনী সি শেপ প্রোফাইল রোল ফর্মিং মেশিন
-
তারের ট্রে রোল ফর্মিং মেশিন
-
পিভি মাউন্টিং ব্র্যাকেট রোল ফর্মিং মেশিন (HAT / ওমেগা প্রোফাইল)
-
পিভি মাউন্টিং বন্ধনী জেড শেপ প্রোফাইল রোল ফর্মিং মেশিন
-
সোলার মাউন্টিং স্ট্রট চ্যানেল রোল তৈরির মেশিন
-
স্ট্রুট চ্যানেল রোল ফর্মিং মেশিন
Double Furring Ceiling Panel Materials
Material | বৈশিষ্ট্য |
---|---|
Galvanized steel |
|
Aluminum |
|
Cold rolled steel |
|
Pre-painted steel |
|
Galvanized steel is the most common choice for roll formed double furring panels due to its optimal balance of strength, corrosion resistance, fire safety, and cost-effectiveness.
Double Furring Ceiling Panel Design
The double furring panel design is engineered for:
- Structural strength and rigidity
- Acoustic insulation properties
- Integration with lighting, HVAC, fire prevention systems
- Aesthetic appearance
- Ease of installation
Critical design factors include:
- Metal thickness and grade
- Panel height
- Furring dimensions and geometry
- Hole spacing and size
- Curvature – linear or tapered
- Surface coating – galvanized, painted etc.
Complex software simulations help optimize the panel parameters to meet architectural and engineering specifications.
Double Furring Ceiling Roll Forming Process Automation
Level | Description |
---|---|
Manual | Operators control all functions like feeding, cutting, part handling |
Semi-automatic | Some tasks automated like coiling feed, cutting length |
Fully automatic | Complete in-line production with automated material flow |
Higher automation reduces labor and increases output, but also raises investment costs. The optimal level depends on production volume and cost targets.
Double Furring Ceiling Roll Forming Production Rate
Metal Thickness | Max. Speed | Output |
---|---|---|
0.3 mm | 18 m/min | 500 m2/hr |
0.4 mm | 15 m/min | 400 m2/hr |
0.5 mm | 12 m/min | 300 m2/hr |
Thinner gauges can run at higher speeds and output. Heavier gauges like 0.6-0.8 mm can go up to 8 m/min.
Double Furring Ceiling Roll Forming Equipment Suppliers
প্রতিষ্ঠান | Location |
---|---|
Btianjing | China |
Zhongliang | China |
JinDeLi | China |
Eagle National | United States |
Metform | Turkey |
China has the most double furring roll forming equipment manufacturers, offering cost-effective machines. Western suppliers provide higher precision and automation options.
Double Furring Ceiling Roll Forming Equipment Costs
Production Rate | Automation | Price Range |
---|---|---|
100 m2/hr | Manual | $8,000 – $15,000 |
300 m2/hr | Semi-auto | $18,000 – $25,000 |
500 m2/hr | Fully auto | $28,000 – $38,000 |
Higher production volumes and automation levels increase costs. Additional equipment for decoiling, conveying, and fabrication can further raise investment.
Installing Double Furring Ceiling Roll Forming Equipment
- Carefully plan equipment layout to optimize material and part flow
- Ensure adequate space on all sides for operation and maintenance access
- Prepare level concrete foundations as per floor plan
- Lifting equipment may be needed to position heavy parts
- Assemble sections as per supplier instructions
- Install hydraulic, pneumatic, lubrication, and electrical systems
- Connect to power supply and grounding
- Test run the line and make adjustments as needed
Proper installation is key for smooth functioning. Take suppliers’ help or hire experienced mechanical contractors.
Operating Double Furring Ceiling Roll Forming Lines
- Strictly follow the supplier manual for pre-checks and start-up
- Load coils using overhead crane or forklift
- Thread coil end through decoiler and guides into roll former
- Set forming speed and cut-off length as required
- Adjust guides, rolls, and pressure as needed
- Monitor line operation and finished panels
- Safety protocols are critical – wear PPE, use safety guards
- Schedule periodic maintenance and lubrication
- Ensure sufficient material inventory and trained staffing
- Adjust parameters to change profiles if desired
Trained operators are essential for efficient roll forming operation.
Maintaining Double Furring Ceiling Roll Forming Equipment
Activity | Frequency |
---|---|
Inspect roll condition | Monthly |
Check hydraulic system | 3 months |
Lubricate bearings | 3 months |
Verify alignments | 6 months |
Change damaged rolls | As needed |
Calibrate sensors | Annually |
Preventative maintenance minimizes unplanned downtime and improves performance.
How to Select a Double Furring Ceiling Roll Forming Equipment Supplier
Factor | Criteria |
---|---|
Production rate | Match to required output volume |
Panel profiles | Equipment capable of specific designs needed |
Automation level | Manual, semi or fully automatic |
Precision | Tolerances, repeatability, precision of forming |
Reliability | Reputable brand with proven quality |
Cost | Budget targets and value for money |
Lead time | Delivery schedule requirements |
Evaluate suppliers based on both technical specifications and commercial factors.
Pros and Cons of Double Furring Ceiling Roll Forming
Pros
- Highly productive continuous process
- Consistent quality panels in long lengths
- Versatile – can produce varied panel profiles
- Lower material waste versus sheet stamping
- Lower investment cost versus extrusions
- Flexible production volumes with quick changeovers
- Automation possible for high-volume needs
- Proven and mature roll forming technology
Cons
- Upfront design and tooling cost for new profiles
- Repeating initial set-up for short runs
- Skill needed for specialized machine operation
- Size limitations of roll forming line
- Limited material strength versus extrusions
- Complex double furring shapes can be challenging
Double Furring Ceiling Panels vs Extruded Panels
Roll Formed Panels | Extruded Panels | |
---|---|---|
Cost | Lower equipment investment | Higher capital costs |
Flexibility | Faster changeovers between profiles | Limited profile shapes |
Strength | Suitable for light to medium duty | Stronger for heavy duty applications |
Throughput | Up to 500 m2/hr | Up to 600 m2/hr |
Finish | Secondary painting required | Excellent surface finish |
Panel size | Limitations on width and height | Unlimited panel dimensions |
Roll forming strikes an optimal balance of cost, flexibility and speed for double furring ceiling panel production.
Double Furring Ceiling Panel Installation Tips
- Carefully inspect panels before installation for any defects
- Measure ceiling dimensions and cut panels to fit if needed
- Plan the panel layout pattern and sequence
- Lift panels safely using straps around perimeter – do not bend
- Fasten to ceiling frame using self-tapping screws into holes
- Level and align each panel as you go
- Install edge trim and end caps for finished look
- Seal any gaps for enhanced thermal insulation
- Touch up scratches with matching paint if needed
Proper planning, handling and fastening ensure the roll formed panels come out looking great.
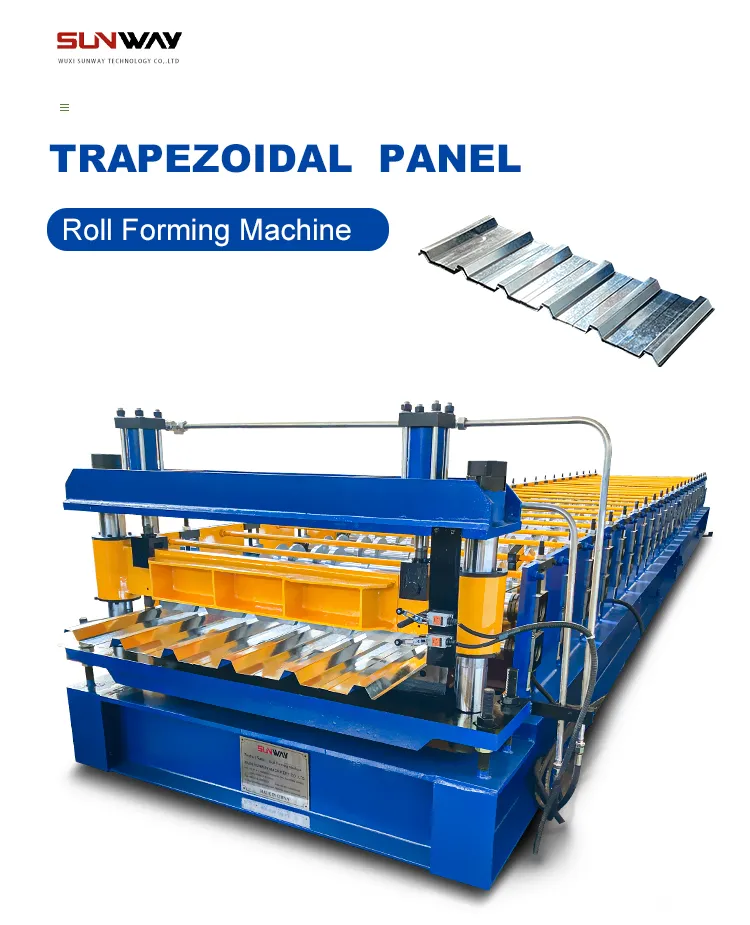
FAQ
Question | Answer |
---|---|
What types of metal can be roll formed into double furring panels? | Galvanized steel, aluminum, cold rolled steel and pre-painted steel sheets are commonly used. |
What thickness of coils can be processed? | Typically 0.3 mm to 1 mm thickness sheets are suitable for these panels. |
How long can the roll formed panels be? | Standard lengths range from 2 to 12 meters. Custom lengths are possible. |
What safety precautions are important? |