Roll forming is a continuous bending operation in which sheet or strip metal is gradually formed into a desired cross-sectional profile through a series of consecutive sets of rolls. Custom roll forming machines produce parts with cross-sections and geometries that match a customer’s specific application requirements.
Introduction to Custom Roll Forming Equipment
Roll forming equipment progressively forms metal coil or sheet stock into customized channel, rail, tube, bar, angles, plates and various structural shapes with precise custom dimensions and functional features per end use specifications using a series of configurable roll stations.
Machine Type | Description |
---|---|
Custom profile roll forming machine | Produces custom open profiles like channels and rails |
Custom structural roll forming machine | Creates angled, plate and built-up structural shapes |
Custom tube/pipe roll forming machine | Forms round, square and rectangular tube and pipe |
Custom roll forming machine with cut off | With built-in punching and cutting at the exit end |
Custom roll former with notching/slotting | Incorporates secondary inline processes |
Multi-blank custom roll forming machine | Forms multiple profile types through quick roll change |
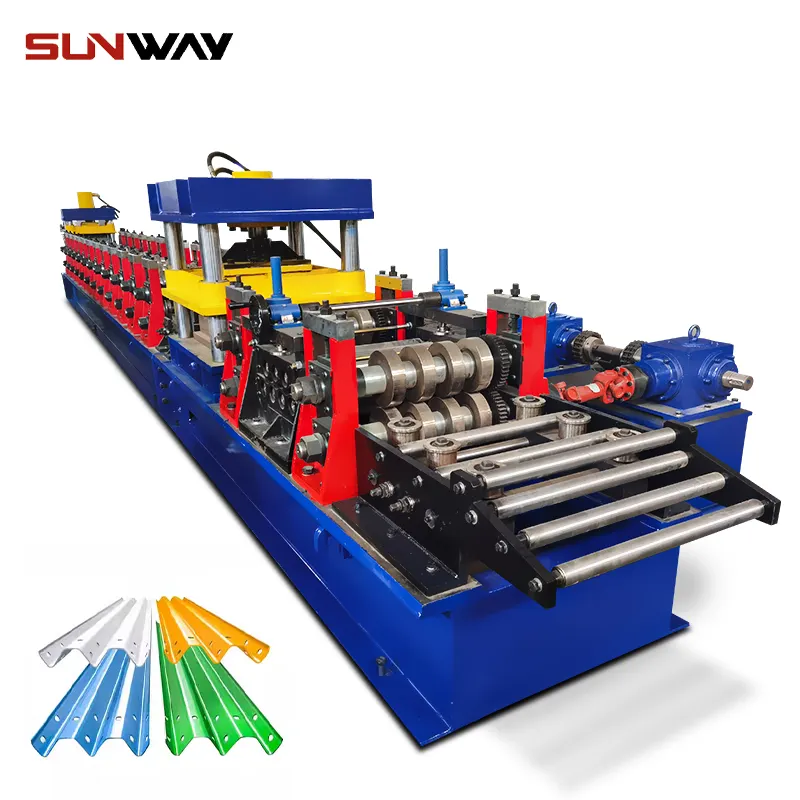
Working Principle
The roll forming process gradually forms sheet metal by progressively bending the material through consecutive sets of contoured rolls without any abrupt shape changes. This cold forming technique avoids stresses associated with hot forming or machine presses.
[Diagram showing custom roll forming working stages from unwinding coil to finished profile]
- Coil/sheet feeding
- Accumulation/degating for continuous high speed forming
- Initial shaping through pre-break rolls
- Gradual incremental bending at multiple stands via contoured rolls
- Additional integrated secondary processes like punching or notching
- Part cutting to length at exit end
- Formed profile collections and packaging
Design and Customization Capabilities
Roll forming imparts durability with uniform profiles tolerant to high loads. Custom roll formers produce parts suited to any volume through rapid design of application-specific tooling matched to end use size specs without dies required with stamping.
Forming analysis tools like CAD, FEA optimize cross-sectional design. Flexible tooling design enables cost-effective customization in dimensions, hole patterns, notches and overall part functional geometry. Common feature additions:
- Custom widths and diameters
- Lengthwise curling of edges or reinforcing ribs
- Perforations and louvers for weight reduction
- Holes, slots, notches and tabs for joining applications
- Embossing and text for branding
Materials Handled
Custom roll formers process low to high strength metals with excellent surface finishes free of flaws, tool marks or warping associated with alternative techniques. Materials include:
- Mild steel
- High strength and alloy steel
- Stainless steel
- Aluminum
- Specialty alloys
- Pre-painted/coated stock
Materials under 0.15 in (3.81 mm) thickness can be formed without splitting or tearing. Thicker materials may require slitting along the width prior to roll forming.
Components of Custom Roll Forming Lines
Material Feed Equipment
[Table of material feeding methods for custom roll forming equipment]
Feeding Method | Description |
---|---|
ডিকয়লার | Unwinds coil up to 60 in (1524 mm) width |
Sheet stacker | Handles sheet metal stacks |
Leveler | Corrects stock thickness variations via rollers or stretch leveling |
Feed table | Guides stock into machine through powered rolls |
Entry End Considerations
- Decoiler capacity suited to order volumes
- Integration of material loader, feed table, leveler for automation
- Controlled material acceleration and speed synchronization with forming section
Custom Roll Forming Stands
The forming section comprises a number of roll forming stands in series each with contoured roll sets designed to impart desired angle changes to the profiled stock.
- Rolls are machined to match calculated incremental bends
- Roll materials selected based on hardness, surface finish, durability needs
- Quick changeover architectures for rapid production changeovers
- Integrated processes like punching are built into the stands
- Forming analysis ensures material flow control on inner and outer radii
Intermediate Considerations
- Sufficient number of stands for gradual bending without defects
- Roll drives designed for torque, speed, positional accuracy needs
- Robust roll materials and bearings for prolonged high speed operation
- Quick roll change features
- Integration of secondary processing like notching or hole punching
- Stock accumulation units to enable continuous high speed forming
Exit End Equipment
The exit end cuts formed profiles to specified lengths and stacks finished parts. Additional exit line processes customize part ends or package products.
[Table of exit end equipment for custom roll formers]
যন্ত্রপাতি | Purpose |
---|---|
Flying cutoff | Precise high speed length shearing |
Self-centering cutoff | Eliminates burrs with centered blades |
Post-cut separator | Sorts parts from scrap slugs |
Part marking | Prints data like length, customer name |
Stacker | Collects cut parts for packaging |
-
দ্রাক্ষাক্ষেত্র পোস্ট রোল ফর্মিং মেশিন
-
স্বয়ংক্রিয় আকার পরিবর্তনযোগ্য সিগমা Purlin রোল ফর্মিং মেশিন
-
পিভি মাউন্টিং বন্ধনী সি শেপ প্রোফাইল রোল ফর্মিং মেশিন
-
CZ Purlin চ্যানেল কোল্ড রোল ফর্মিং মেশিন সম্পূর্ণ অটো গ্যালভানাইজড স্টিল প্রোফাইল
-
পিভি মাউন্টিং ব্র্যাকেট রোল ফর্মিং মেশিন (HAT / ওমেগা প্রোফাইল)
-
পিভি মাউন্টিং বন্ধনী জেড শেপ প্রোফাইল রোল ফর্মিং মেশিন
Added Secondary Processes
- Hole punching
- End punching / notching
- End forming / hemming
- Part embossing
- Scribing lines and metrics
- Part packaging
Exit Line Considerations
- Cutoff method suitable for material gauge and speeds
- Integrates secondary processing needs
- Stacker, conveyor, baler matched to production rates
- Length verification via encoder feedback
- Part sorting quality control
Custom Roll Forming Process Capabilities
The flexible roll tooling design enables a wide range of profiles, features, and post-forming additions matched to customer functional requirements.
Profile Dimension and Feature Variety
Any cross-sectional dimensions within machine limits can be closely held with custom roll sets for each profile parameter:
- Width sizes under 60 inches (1520 mm)
- Height sizes within 15 inches (380 mm)
- Wall thicknesses down to 0.05 inch (1.3 mm)
- Inside bend radii ratios from 0% to over 8% of material thickness
Common profile characteristics imparted:
- Closed tubular and built-up shapes
- Formed complex edge features like ribs, lips, flanges and curls
- Reinforcing beads, corrugations and emboss patterns
- Perforations, holes, notches, louver patterns
Secondary Integrated Processes
Inline stages expand fabricated part functionality:
Punching
- Bolt connection holes
- Lifting point holes
- Lightening cutouts
- Drainage holes
Notching and Slotting
- Joining tabs and brackets
- Mounting slots
- Reinforcing closed plane ends
End Conditioning
- Hemming and finishing
- Hole punching
- Stamping logos
Curling and Bending
- Edge reinforcement
- Interlocking seam creation
- Mounting flange addition
Part Marking
- Printed metrics and text
- Length verification
- Part numbers
- Customer name
Material, Finish and Tolerance Control
Key advantages of custom roll forming include:
[Table comparing custom roll forming process capabilities]
শ্রেণী | Capability |
---|---|
Material type | All common metals from low carbon steel to stainless steel |
Material gauge | Down to 0.13 mm with special thinner gauge lines |
Surface finish | Smooth deformations free of flaws or tool marks |
Dimensional accuracy | Tolerances down to ±0.5 mm maintained consistently |
Feature detail | Sharp corners and edges maintained without distortion |
Production rate | High speed continuous processing up to 120 m/min |
Setup time | Rapid quick changeovers with programmable tooling parameters |
Secondary integration | Inline processing expands part functionality |
Volume flexibility | Scales from low volume custom jobs to high volume OEM parts |
Design change | Rapid tooling adjustments to fine tune or modify profiles |
Custom Roll Forming Machine Suppliers
Global custom roll former manufacturers offer end-to-end design, manufacturing and integration capabilities to produce equipment matched to customer production objectives.
Leading Custom Roll Forming Machine Brands
[Table of major suppliers of custom roll forming equipment]
Supplier | Location |
---|---|
Techniform | Canada |
Shanghai Strength Machinery | China |
Zhongli Roll Forming Machine | China |
Roll Forming Machine & Metal Building Machinery | ভারত |
Gasparini | ইতালি |
Dimeco | USA |
Formtek | USA |
Roundo | USA |
Selection Criteria
Customers evaluate capabilities in:
- Engineering consultation services
- 3D modeling and FEA design analysis
- Fabrication expertise for custom tooling
- Precision machining and extensive QA
- Custom control software development
- Line integration, installation and operator training
- Responsive aftermarket support structure
In addition to technical competencies, customers assess:
- Years of industry application experience
- Supply record consistency and lead times
- Line customization scalability
- Overall value proposition against cost
Purchasing Considerations for Custom Roll Forming Equipment
Key considerations when investing in new or upgrading existing custom roll forming machine capabilities:
Required Production Parameters and Specifications
- Annual or monthly volume targets
- Product mix complexity and changeover needs
- Material specifications like gauge range, widths
- Custom feature requirements – holes, notches, curls etc.
- Secondary process integration needs – punching, marking etc.
- Dimensional precision and surface finish needs
- Line speed and efficiency expectations
- Available space constraints
Estimated Budget Range
[Table of price range guide for custom roll forming machines]
Line Type | Price Range |
---|---|
Standard roll former | $100,000 to $500,000 |
Complex profile multi-blank line | $500,000 to $5 million |
Max width and speed lines | Over $5 million |
In general, pricing rises with:
- Material width and thickness range
- Number of tooling heads and stands
- Secondary process integration complexity
- Degree of associated automation
- Production monitoring and data systems
Key Supplier Evaluation Metrics
[Table detailing key supplier selection criteria]
শ্রেণী | Selection Criteria |
---|---|
Engineering expertise | Design analysis with FEA, formability assessment, process simulation capabilities |
Manufacturing | Vertically integrated, stringent QA, safety compliant fabrication |
Experience record | Years in business, number of lines supplied, customer reference checks |
Customization range | Ability to handle low to high complexity and volumes |
Responsiveness | Lead times, transparent project updates and issue resolution |
Services | Installation coordination, operator training programs |
Support infrastructure | Manuals, troubleshooting assistance, spare parts supply |
Overall value | Total cost of ownership against production objectives |
Carefully vet supplier production expertise, customization scalability, and service reliability to ensure selected partner can deliver a roll forming solution matching needs.
Installing a Custom Roll Forming Machine
Proper planning is key for smooth installation coordinating activities between customer facilities staff, contractors, and machine builder teams.
Installation Planning Checklist
Documentation
- Review equipment drawings, manuals, risk assessments
- Structural engineer approval of floor and overhead requests
Site Readiness
- Allocate required space with access routes
- Pour new slabs or floor coating if needed
- Install power supply boxes, disconnects to code
- Set up air, water drops and drainage as specified
- Ready rigging path, staging area and crane equipment
Incoming Inspection
- Unpack and inspect components for damage
- Document any repair or replacement needs
- Check electrical parts, labels match drawings
- Inspect linear guides, spindles and drives prior to assembly
Positioning and Connections
- Site machine components to match layout drawings
- Make anchor bolt hole locations
- Level stands, tightly bolt groups per specs
- Pull wires and make conduit connections
- Attach air, water and drain lines
Testing and Turnover
- Power up drives and test interfaces
- Cycle machine through motions at low speed first
- Monitor current, voltage, flow rates and make adjustments
- Repeat at full production speed and load
- Confirm emergency stops, guards and safety circuits function
- Review operational manuals, obtain signoffs on training
Careful staging, inspection, precision installation and methodical checkout steps結果 in optimized uptime.
Operating a Custom Roll Forming System
Efficient operation requires consistent monitoring, scheduled maintenance and quick issue resolution to keep roll forming production on track.
Run Preparation
Perform start of shift readiness checks:
- Walk inspection of guards, material feeds and tooling
- Review program for production job, make any edits
- Jog machine and check space guards engage
- Start support systems – hydraulic unit, lube pumps
- Load coil on de-coiler securing lift straps
- Thread lead end ensuring edge alignment
- Set feed length and speed parameters
Run Monitoring
During operation:
- Monitor line speed, look/listen for inconsistent forming noise
- Watch for end kickout activating reliably
- Periodically check profile dimensions and features
- Log produced quantity versus target
- Watch for drive faults or unusual vibrations
System Care
Post run maintenance steps:
- Allow machine to fully stop, engage locks
- Clear line of remaining scrap pieces
- Clean deposits from forming heads
- Lubricate rollers, guides per schedule
- Inspect consumables like blades, belts
- Log hours and production counts
Proper operating discipline maximizes uptime and end product quality.
Maintenance of Custom Roll Formers
Preventative, predictive and reactive maintenance protects uptime, output consistency and safety.
Planned Upkeep
Execute scheduled inspection and replacement:
[Table listing maintenance tasks and frequencies for custom roll forming equipment]
Task | Frequency |
---|---|
Roll and belt inspection | Monthly |
Hydraulic fluid testing | Quarterly |
Line calibration | Quarterly |
Drive oil changes | Annually or per OEM spec |
Control software updates | As available |
Full safety audit | Biannually |
Monitor metrics like drive loads, vibration and oil analysis for early issue detection.
Breakdown Response
For faults follow lockout steps:
- Engage emergency stop and power isolation
- Allow equipment to fully halt movement
- Lockout electrical and hydraulics before inspection
- Clear jams, replace faulty parts, test fixes
- Document incident details for root cause investigation
Improvement Implementation
- Review fault history
- Identify failure prone subsystems like certain seals or cylinders
- Evaluate operation and maintenance practices
- Consider upgrades to higher rated components or redundancies
Continuous improvement mindset improves safety and productivity.
Comparing Roll Forming with Stamping
Both roll forming and stamping offer rapid, repeatable metal forming suited for high volume production. Choosing best method depends on product specifications.
Roll Forming Benefits
[Table listing advantages of roll forming process]
শ্রেণী | Roll Forming Advantages |
---|---|
Setup | No dies needed enables fast changeovers |
Flexibility | Easily adjusted tooling for design changes |
Cost | Lower initial tooling investment |
Materials | Wider thickness and hardness range |
বৈশিষ্ট্য | More profile options with secondary operations |
Accuracy | Excellent tolerance control |
Finishes | Smooth uniform finishes without tool marks |
Stamping Benefits
[Table listing advantages of stamping process]
শ্রেণী | Stamping Advantages |
---|---|
Speed | Very high cycle rates |
Automation | Easy part unload and transfer |
Single hit | Entire shape formed in one stroke |
Capital cost | Lower machine expense for some volumes |
Wall angles | Better suited for sharp angle walls |
Typical Application Areas
রোল গঠন – Channels, doorframes, roofing panels, racks, structural shapes, poles, complex tubes
Stamping – Brackets, plates, enclosures, hinges, clips, rings, simple shapes
Each process suits different product geometries, features sets and economic factors.
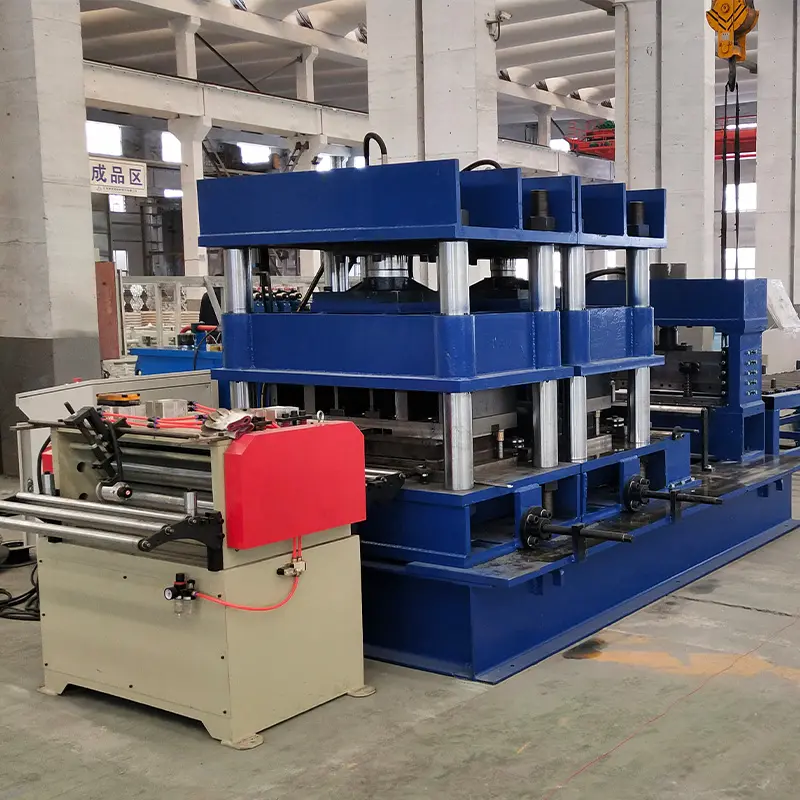
Limitations of Roll Forming
Understanding constraints in forming capabilities, secondary processing and line setups helps guide appropriate application areas.
Dimensional Limits
[Table listing thickness, width and speed constraints]
Parameter | Typical Range Limits |
---|---|
Material thickness | 0.15 – 2 mm mild steel |
Harder material thickness | 1 mm grade threshold |
Process width | Up to 1520 mm standard |
Wheel authority | Gradual not abrupt bends |
Profile height | 380 mm max |
Machine speed | Up to 120 m/min (400 ft/min) |
Design Restrictions
- Material splitting risk on tight radii
- Profile springback factors
- Wheel size impacts contour cutoff points
- Roll flange impacts inside dimension minimums
Secondary Process Limitations
- Holes limited to max punch tonnage
- Slot length depends on blade and rotation
- Marking quality affected by material speed
- Feature spacing requirements
Each process selection involves balancing strengths against practical constraints.