Overview of slide rail roll forming machine
Roll forming is a continuous bending operation in which sheet or strip metal is gradually formed into a desired cross-sectional profile through a series of consecutive sets of rollers. Slide rail roll forming machines are used to form slide rails through this process.
OEM slide rail roll forming machines are designed and built specifically for a customer’s unique specifications and slide rail production needs. Key details:
- Used to form metal slide rails through roll forming process
- Customized to customer’s specific requirements
- Form complex cross-sectional slide rail shapes
- High production efficiency and precision
- Automated operation for high volumes
- Material capabilities: steel, aluminum, copper, etc.
- Ideal for manufacturers producing custom slide rails
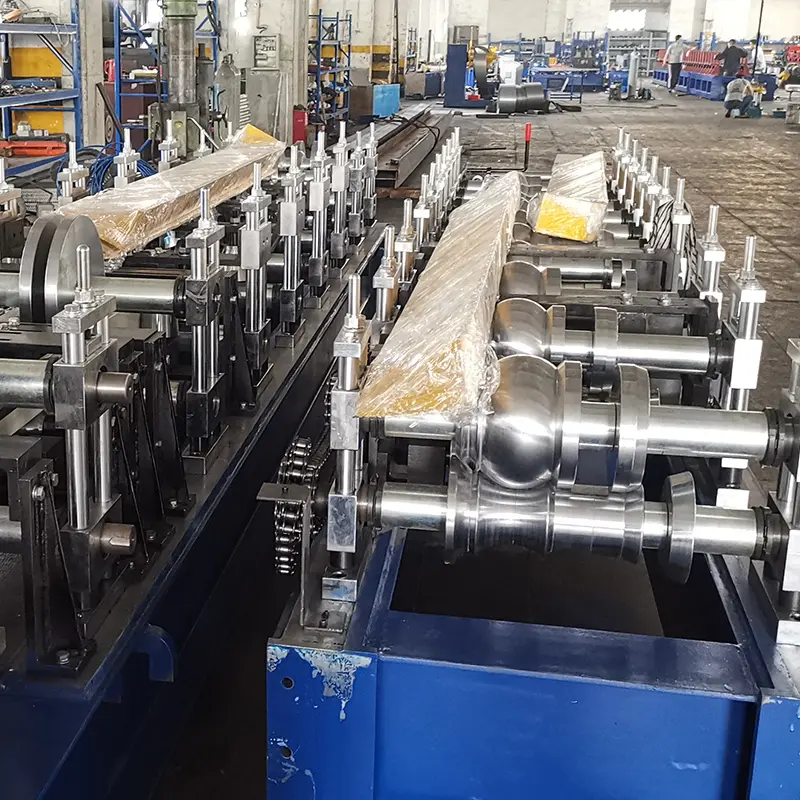
Slide Rail Roll Forming Machine Buying Guide
Types of OEM Slide Rail Roll Forming Machines
Machine Type | Description |
---|---|
Horizontal | Rollers positioned horizontally for linear feed of material |
Vertical | Rollers positioned vertically for material feed from top |
C-type | Rollers shaped like “C” for structural rigidity |
Step Down | Profiles formed in decreasing steps through machine |
Working Principle
The oem slide rail roll forming machine forms metal strips into specialized slide rail shapes through an automated, continuous roll forming process.
Sheet metal coils are the common raw material input. The process starts by feeding the sheet metal strip through a straightening mechanism to flatten any coils or curls. It then passes through a series of consecutive roller stations.
Each roller station incrementally forms the material closer to the desired profile. The cross-section gets more defined as the material keeps passing through each station. This gradual rolling action bends the material without cracks or defects.
The formed slide rail profile continuously exits the other end of the machine. It can be cut to length by built-in/separate cutoff saws. Advanced machines also integrate holes punching, notching, embossing and other secondary processing inline.
The key benefit of oem slide rail roll forming is its continuous high-speed production. Complex profiles can be mass produced via this automated process. It is ideal for manufacturers producing custom slide rails.
Material Feeding
Method | বিস্তারিত |
---|---|
Coil Feed | Sheet metal coil loaded at one end, fed through machine |
Single Sheet Feed | Individual metal sheets loaded manually/automatically |
Automatic Feeder | Specialized feeder mechanisms for automated coil/sheet loading |
Forming Capabilities
Parameter | Capability |
---|---|
Material type | Steel, stainless steel, aluminum, copper, titanium |
Material thickness | 0.15mm to 3mm |
Material width | Up to 1650mm |
Profile width | 20mm to 400mm |
Profile height | 10mm to 200mm |
Profile type | C-shaped, Hat channel, U-channel, Slide rail |
Features formed | Hole punching, notching, embossing, bending |
-
Standing Seam Roof Panel Curving Machine
-
ব্যারেল ঢেউতোলা রোল ফর্মিং মেশিন
-
Stand Seaming Roof Panel Roll Forming Machine
-
ডাউনস্পাউট পাইপ রোল তৈরির মেশিন
-
গটার রোল তৈরির মেশিন
-
Trapezoidal Panel Roll Forming Machine
-
রিজ ক্যাপ রোল ফর্মিং মেশিন
-
ডাবল লেয়ার প্যানেল রোল তৈরির মেশিন
-
ছাদের টাইল প্যানেল রোল তৈরির মেশিন
Secondary Processing
OEM slide rail roll forming machines can integrate additional processing for finished parts:
- Cutting: Cutoff saws cut formed profile to length
- Hole punching: Punch holes of specified size/shape
- Notching: Localized cutting of small notch shapes
- Embossing: Pattern impressions on surface
- Bending: End forming or intermediate bends
Design and Customization
- Machines designed to customer’s production requirements
- CAD software creates roll sets for required profile
- CNC machining produces precise roller dies
- Quick roller changeovers for new profiles
- Custom part exit directions or secondary processing
Suppliers and Pricing
Supplier | Location | Price Range |
---|---|---|
Company 1 | China | $50,000 – $150,000 |
Company 2 | Europe | $80,000 – $250,000 |
Company 3 | United States | $100,000 – $500,000 |
Pricing varies based on:
- Machine size and capacity
- Level of automation
- Material type and thickness
- Secondary processing needs
- Production volumes
- Custom design requirements
Higher investment yields faster, high-volume production.
Installation and Operation
Parameter | বিস্তারিত |
---|---|
Installation | Level surface<br>Anchor bolts to secure machine<br>Electrical connections to control panel |
Power supply | 380V, 50Hz (machine size dependent) |
Air pressure | 6-8 bar compressed air |
Operation | Touchscreen HMI for program inputs<br>Auto operation after setup |
Safety | Emergency stop buttons<br>Guarding at roller stations<br>Operator safety training |
Routine maintenance activities:
- Visual inspection of rollers and mechanisms
- Apply oil/grease at lubrication points
- Clean accumulated metal fines
- Check filter elements
- Sensor and wiring inspections
- Hardware tightening
- Test runs
How to Select an OEM Slide Rail Roll Forming Machine Supplier
Key Criteria
- Years of experience
- Roll forming expertise
- Design customization capabilities
- Quality and precision
- Customer service and technical support
- Delivery timelines
- Past clientele and reviews
- Cost factor
Certifications to Look For
- ISO 9001
- CE markings
- UL/CSA (for electricals)
Supplier Assessment Process
- Detailed needs analysis: profile design finalized
- Review supplier equipment specifications
- Ensure speed, precision, reliability requirements are met
- Check capabilities match needs
- Compare supplier quality certifications, experience, and expertise
- Request customer references and case studies
- Review sample profiles from test runs
- Ensure adequate local technical support
Select the supplier best matching production needs through demonstrations and discussions. Sign contracts clearly detailing scope of supply, machine specifications, delivery timeline, payment terms and expected support duration.
Advantages of OEM Slide Rail Roll Forming Machines
High productivity through automated, high speed forming
Advanced profiling capability to produce complex slide rail shapes
Superior precision & quality from accurately calibrated roller dies
Ideal repeatability for large volume production demands
Quick changeovers to alternate slide rail configurations
Significant material savings due to low scrap rates
High line speeds upto 100m/minute by configuration
Adaptable features like holes punching, notching and more
Limitations of OEM Slide Rail Roll Forming Machines
- High setup costs for custom roller die production
- Individual operator training needed for oversight
- Safety hazards from rotating mechanisms require precautions
- Production dependent on consistent raw material input
- Limited fine bend radius control compared to press brakes
- Secondary machining still needed for fabrication of final parts
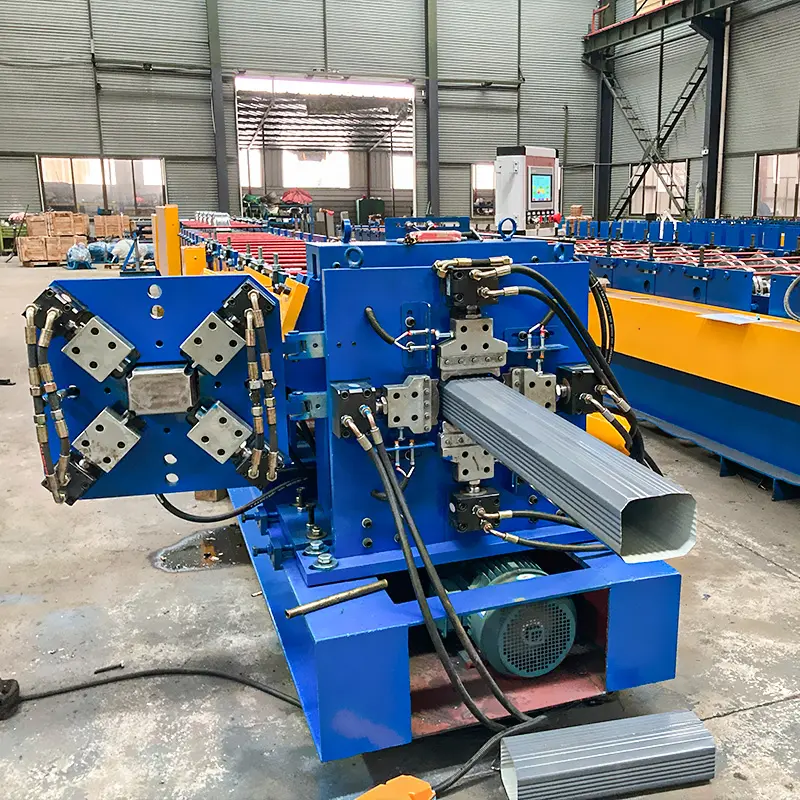
FAQs
What materials can you use?
Roll formed slide rails are typically made from steel, stainless steel, galvanized steel, aluminum or copper. Some applications use Titanium and other exotic alloys too. Material thickness usually ranges from 0.3mm to 2mm.
What shape profiles be formed?
Common shapes include various rail configurations like C channels, U channels, rectangular tubes and specialized asymmetric curvilinear shapes. Advanced profile features like notches, holes and intermediate offsets can also be formed.
How is the quality checked?
Automated feedback process control with sensors across the machine inspect shape accuracy. Operators must additionally visually verify key characteristics using go/no-go gauges for critical features. Destructive bend tests on sample pieces ensure required strength is achieved.
What are the different ways to feed stock material?
Entry-level machines rely on manual feeding of individual sheets. Intermediate setups use automatic decoilers to unroll steel coils in sync with the roller speed. Industrial units have automated loading and uncoilng mechanisms for 24/7 material feed.
How to calculate the machine price?
Key factors determining price include annual part volumes, material specifications, shape complexity, line speed, secondary processing needs and overall accuracy/precision requirements. Small machines with manual operation for low volume, basic components start from around $50,000. Fully automatic, CNC controlled industrial roll forming lines for mass production cost over $500,000.
What secondary processes are possible?
Holes punching, offset notching, louvre and emboss impressions can be integrated inline through additional processing stations. Common additions also include cutoff saws for cutting parts to length, bending for flanges, specialized exit conveyors and pick-and-place packing/stacking mechanisms.
Summary
OEM slide rail roll forming machines deliver automated, precise slide rail part production through a continuous bending process. They can be tailored to match unique slide rail design needs with efficient changeovers. The right supplier selection ensures the production technology aligns closely with manufacturing goals now and in future. When supported by qualified technicians and operators, slide rail roll forming lines generate complex, repeatable and efficient part fabrication.