Overview of oem shutter roll forming machine
Roll forming is a continuous bending operation in which sheet or strip metal is gradually formed into a specified cross-sectional shape by passing it through consecutive stands of rollers. Roll forming machines are used to produce straight or curved profiles with uniform cross-sections.
An original equipment manufacturer (OEM) shutter roll forming machine is designed and built specifically to manufacture rolling shutters. These machines form metal coil into the curved shutter slats through a series of progressive dies and bending steps.
OEM shutter roll formers provide high productivity, flexibility, and reliability for producing shutters in various styles and dimensions. They enable efficient, large-scale production to meet global shutter market demands.
This guide covers key aspects of OEM shutter roll forming technology:

OEM Shutter Roll Former Equipment Guide
Main Equipment Types
যন্ত্রপাতি | Description |
---|---|
আনকোয়লার | Feeds metal coil strip into roll former |
Roll Forming Stations | Forms strip into curved shutter profile through series of roller dies |
Punch and Shear | Punches slat holes and cuts slats to length |
Manual/Auto Stacker | Stacks and counts finished shutter slats |
Working Principle
The OEM shutter roll forming process starts by loading a coil of thin gauge metal strip into an uncoiler…
Elaborate on working principle in paragraphs, covering:
- Equipement sequence from uncoiler to stacker
- Slat profile forming through progressive roller bending
- Hole punching and shearing steps
- Description of machine control and automation
OEM Shutters Roll Formed
Type | Description |
---|---|
Rolling Shutters | For doors, windows, garage doors |
Fire Shutters | Fire and smoke protection |
Security Shutters | Intruder protection |
Insulated Shutters | Noise, heat insulation |
Describe each shutter type and typical dimensions in paragraphs
Material, Design and Customization
Material Feeding
- Metal coil weights up to 5 tons
- Materials: Steel, aluminum, stainless steel
- Strip width: 50-300mm
- Thickness: 0.4-1.2mm
- Coil ID: 450-650mm
Elaborate on suitable materials, thicknesses, widths etc.
Profile Design
- CAD software for custom profile design
- Flexible manufacturing without dies
- Profile examples: Curved, flat, insulated
Include descriptions and images showing profile examples
কাস্টমাইজেশন
- Custom profiles
- Variable coil width
- Adjustable punch and shear
- Modular design for options
- Production capacity: up to 10,000 shutters per shift
Explain how machines can be customized for special profiles, dimensions etc.
Suppliers and Pricing
OEM Shutters Roll Forming Machine Manufacturers
প্রতিষ্ঠান | Location | Product Range |
---|---|---|
Company 1 | City, Country | Description of machines made |
Company 2 | City, Country | Description of machines made |
Cost Analysis
Specification | Price Range |
---|---|
Max. Coil Width | $100k – $250k |
Max. Line Speed | $150k – $350k |
Production Output | $200k – $500k |
Provide price estimates for ranges of speed, width, output etc.
Operation and Maintenance
Installation Requirements
- Floor space: X sq.ft. for Y tons/hour
- Power supply: Z kVA
- Compressed air: PSI, CFM
- Staff: Operators, maintenance, QA
Provide details on installation needs
Operation
- Typical operation procedure
- Machine control panel and HMI operation
- Systems monitoring
- Daily production planning
Explain operating procedures and best practices
Maintenance
Task | Frequency |
---|---|
Inspection | Daily |
Lubrication | Monthly |
Blade replacement | 6 months |
Describe routine maintenance schedule
Choosing an OEM Shutter Roll Former Supplier
Important criteria for selecting machine manufacturer:
- Reliability and build quality
- Experience and reputation
- Customization capabilities
- After-sales service and support
- Compliance with standards
- Total cost of ownership
Collect proposals from shortlisted suppliers evaluating above parameters
Explain selection criteria in detail with examples
Advantages of OEM Shutters Roll Forming Machines
Benefits include:
- High production speeds up to 18 m/min
- Low operation cost per shutter
- Consistent and precision formed shutters
- Easy changeover between profiles
- Compact, safe and quiet operation
- Designed for 24/7 production demands
- Manufactured to International quality standards
Outperforms manual shutter making processes in:
- Product consistency
- Labor cost saving
- Increased output
- Improved safety
Limitations of OEM Shutters Roll Forming Tech
Some drawbacks are:
- High initial capital investment
- Regular skilled maintenance required
- Limited flexibility for profile changes
- Production dependent on coil supplier
- Complex control software and settings
- Fixed installation, not portable
Manual processes have advantage for:
- Small batch or custom orders
- Thicker metal forming
- Low operation requirements
Compare with traditional and CNC bending methods
Applications of OEM Shutter Roll Forming Machines
Major application areas include:
Rolling Door and Garage Door Production
Modern high-speed residential and commercial door manufacturing relies on shutter profile roll formers feeding production and assembly lines. These machines offer reliability, efficiency and precision slat forming capabilities demanded by major manufacturers.
Typical configurations have multiple roll former lines supplying automated punching presses and injection molding machines to produce ready-to-fit shutter door kits.
Rolling steel or insulated aluminum garage door profiles are also roll formed on similar OEM equipment built specifically for the garage door industry standards.
Steel Fire Shutter and Smoke Protection Doors
Fire rated steel rolling shutters play a vital life safety role across commercial and industrial facilities. Heat and fire resistant doors prevent flashover and stop smoke penetrating other areas.
OEM roll formers in this niche produce specialized insulated, interlocking shutter profiles certified to fire resistance ratings from 30 minutes up to 4 hours. These machines feed downstream processes to manufacture complete fire door sets.
Steel Security Shutters and Grilles
Shutter doors, grilles and counter shutters providing intruder resistance and asset protection rely on heavy gauge cold roll formed steel profiles.
Hardened slat profiles with drill-proof joining tabs and cut-out designs make forced entry extremely difficult. High tensile steel alloys give further resistance against attack while maintaining good roll forming capability.
Dedicated security shutter OEM rolling lines provide the robust forming and precision hole punching required to manufacture blast and ballistics-rated products.
Choosing OEM Shutters Roll Forming Machine Specifications
Determine Production Target
- Required annual volume
- Operating hours per day
- Product dimensions and sizes
Perform throughput calculations to define machine capacity
Select Suitable Line Speed
Higher speeds increase output but limit material and thickness range
Speed | Output | পুরুত্ব |
---|---|---|
10 m/min | 6,000 shutters/shift | ≤ 0.7mm |
15 m/min | 9,000 shutters/shift | ≤ 0.5mm |
-
দ্রাক্ষাক্ষেত্র পোস্ট রোল ফর্মিং মেশিন
-
স্বয়ংক্রিয় আকার পরিবর্তনযোগ্য সিগমা Purlin রোল ফর্মিং মেশিন
-
বৈদ্যুতিক মন্ত্রিসভা ফ্রেম রোল গঠনের মেশিন
-
দিন রেল রোল ফর্মিং মেশিন
-
তারের মই রোল ফর্মিং মেশিন
-
পিভি মাউন্টিং বন্ধনী সি শেপ প্রোফাইল রোল ফর্মিং মেশিন
-
তারের ট্রে রোল ফর্মিং মেশিন
-
CZ Purlin চ্যানেল কোল্ড রোল ফর্মিং মেশিন সম্পূর্ণ অটো গ্যালভানাইজড স্টিল প্রোফাইল
-
পিভি মাউন্টিং ব্র্যাকেট রোল ফর্মিং মেশিন (HAT / ওমেগা প্রোফাইল)
Choose Number of Forming Stands
More stands support tighter profile radii but reduce speed
Stands | Min. Bending Radius |
---|---|
10 | 20mm |
15 | 15mm |
20 | 10mm |
Define Coil Width and Weight
Standard widths between 50-300mm
Common weights 1-5 metric tons
Larger coils mean fewer changeovers
Allow for Future Expansion
Select base specification to allow upgraded:
- Line speed
- Forming capability
- Automation
Right-size initial investment for growth
Prioritize Safety Features
Guarding, interfaces, training procedures
CE marked per EN safety standards
Purchasing OEM Shutters Roll Forming Equipment
Define Requirements
Create accurate machine specifications reflecting:
- Product dimensions
- Outputs needed
- Material parameters
- Operation environment
Develop Bid Specification
Provide to prequalified suppliers for proposals
Document includes:
- Functional requirements
- Layout constraints
- Standards compliance
- Acceptance conditions
Evaluate Supplier Proposals
Assess each supplier response focusing on:
- Technical solution
- Experience credentials
- Services offered
- Total project cost
Visit Supplier Facilities
Inspect roll former manufacturing:
- Production capabilities
- Quality control
- Testing facilities
- Past installations
Negotiate Final Contract
Clearly specify:
- Equipment cost breakdown
- Implementation schedule
- Training and support
- Service level agreement
- Warranties
Carefully review all commercial terms
উপসংহার
OEM shutter roll forming lines engineered specifically for rolling doors provide efficiency, precision and reliability advantages over general metal forming equipment. They enable manufacturers to meetlatest market expectations.
Shutter profile requirements continue getting more stringent in fire, security and sound insulation segments in particular. This drives further innovation in purpose-built roll former design.
With sound specification, supplier selection and maintenance practices, today’s advanced OEM rolling shutter machines represent a cost-effective production solution. They are proven to handle intensive 24-hour shutter manufacturing cycles over prolonged periods.
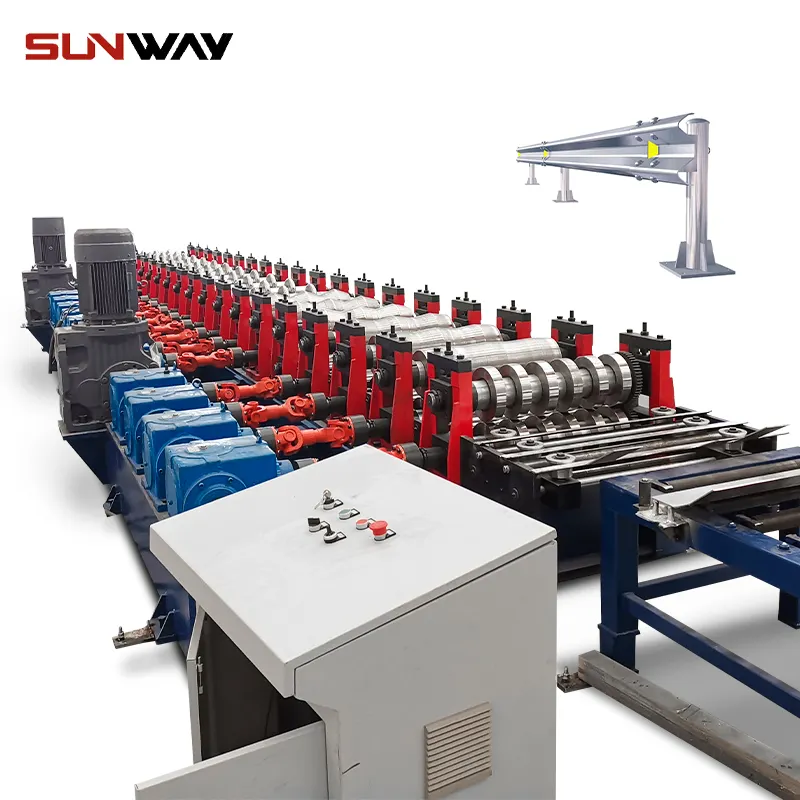
FAQ
What thickness of metal sheet can be roll formed into shutter slats?
OEM shutter roll forming machines can typically process metal coil from 0.4mm up to 1.2mm thickness. More heavy duty configurations are available to form 1.5-2mm thick material.
What degree of customization is possible for shutter profile design?
These roll formers provide flexibility to create custom profiles within certain limitations. CAD software expedites developing and proving new concepts. Modular tooling and machine adjustments suit many non-standard dimensions.
What safety measures are incorporated?
Industry guards, emergency stops, control reliability features and operational protocols minimize risk. Staff should receive full training. Proper PPE gear must be mandated. CE certification confirms all hazards safeguarded to EU machinery directives.
What is the typical return on investment timeline for these machines?
Dependent on annual operating hours and product pricing, ROI periods average 2-3 years to recoup shutter roll former costs at suitable production volumes.
What factors determine OEM shutter roll forming machine prices?
Major elements include coil width capacity, line speed, number of forming stations, automation level, reputation of manufacturer, overall output capability and options chosen. Turnkey pricing starts around $100k, reaching $500k for high-end configurations.