oem highway guardrail roll forming machines are used to transform metal coils into long W-beam guardrails for installation along roads. As an original equipment manufacturer (OEM), these roll former lines can be customized to clients’ specifications for traffic safety barrier production.
Introduction to oem highway guardrail roll forming machine
Roll forming is a continuous bending process used to convert metal coils into customized longitudinal profiles via inline feeding and roller stations. OEM guardrail roll formers shape plain sheets into corrugated W-beam rails through:
Material Feeding
- Payoff reel to unroll coiled steel/aluminum
- Feed table with edge preparation tools
- Encoder controls feed speed synchronization
Profile Forming
- Series of roller blades shape metal incrementally
- Forming stations gradually bend metal into ribs
- Specialized tooling designs for W-beam
Design and Customization
- Machines can make standard or custom rails
- Operators program PLC for parameter changes
- Quick die changeovers for new profiles
OEM guardrail lines provide:
- High speed forming up to 40 m/minute
- Integrated punching and cutting
- Automated length control systems
- Customized roll pass design ability
- Consistent quality for road projects
Guardrail roll formers deliver higher outputs plus superior performance consistency compared to manual bending methods.
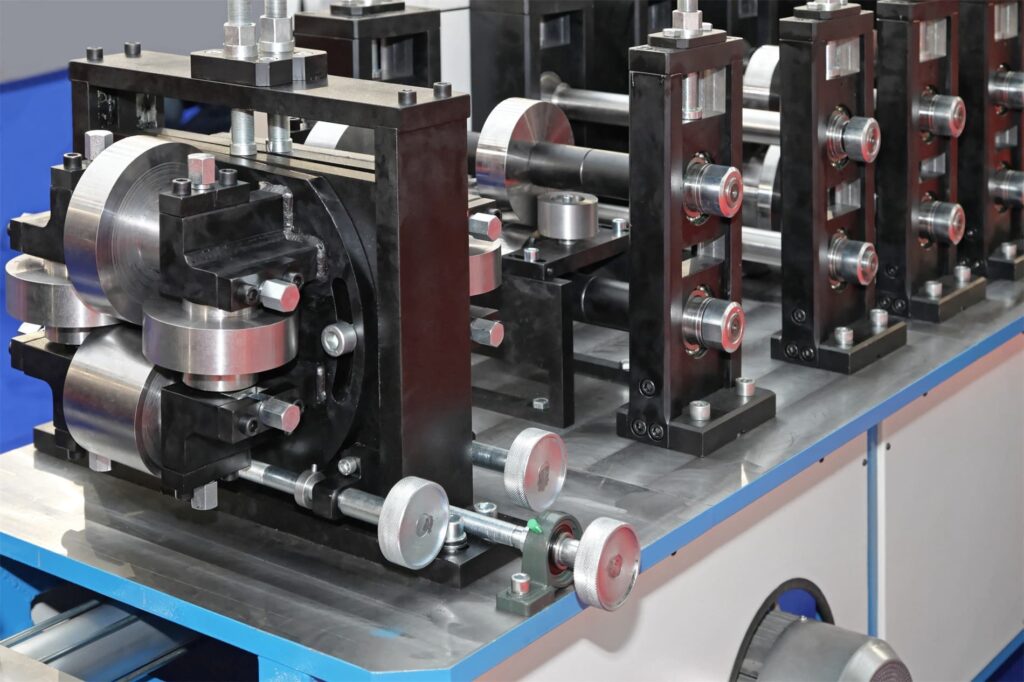
Major Components of Guardrail Lines
Component | Function |
---|---|
ডিকয়লার | Feeds raw coil stock into machine |
Straightener | Removes coil curvature for flat feeding |
Roll forming stands | Each set of rollers shape W ribs |
PLC Control | Automates production monitoring |
Flying shear | Trims rails to length after forming |
Conveyors | Safely offloads finished guardrails |
Working Process of OEM Guardrail Roll Lines
The working principle utilizes specialized roller tooling to incrementally bend metal sheets into a W corrugated shape by passing strips through consecutive forming stations:
Step 1) The leveled strip from a decoiled metal sheet enters into the initial forming stands after the feed table.
Step 2) It passes between a series of top and bottom rollers designed specifically for W-beam contours.
Step 3) At each stand, the metal is bent further into wave-like ribs that make up the cross section.
Step 4) Reduced openings between rollers at each station provide needed clearances during shaping.
Step 5) Automatic gauges monitor strip alignment throughout the process.
Step 6) The formed W profile then goes for precision cutting as per length specifications.
Step 7) Formed guardrails exit the line on outfeed tables for bundling.
OEM machines enable pre-programmed recipes for efficient high speed production cycles to achieve construction project requirements.
Main Technical Parameters
Specifications | বিস্তারিত |
---|---|
Production Speed | 35-40 meters per minute |
Material Thickness | 1.2 – 4 mm steel coils |
Finished Size | 150 mm x 75 mm Guardrails |
Machine Power | 37 kw main motor |
Line Voltage | 380V, 50 Hz AC 3-phase |
Structure | Welded steel frame |
বেলন উপাদান | 45# high-carbon steel |
Roll Stands | 18 minimum; 25 stands typical |
Length Accuracy | ± 2 mm tolerance |
Hydraulic Power | 11 kw pump capacity |
Operation Mode | Automatic PLC recipes |
-
Standing Seam Roof Panel Curving Machine
-
ব্যারেল ঢেউতোলা রোল ফর্মিং মেশিন
-
রোলিং শাটার স্ল্যাট রোল ফর্মিং মেশিন
-
Stand Seaming Roof Panel Roll Forming Machine
-
ডাউনস্পাউট পাইপ রোল তৈরির মেশিন
-
গটার রোল তৈরির মেশিন
-
Trapezoidal Panel Roll Forming Machine
-
রিজ ক্যাপ রোল ফর্মিং মেশিন
-
ডাবল লেয়ার প্যানেল রোল তৈরির মেশিন
Choosing OEM Guardrail Roll Formers
Road construction companies looking to manufacture guardrails should evaluate suppliers on:
Product Quality
- Material thickness capacity
- Profile dimensions and finish
- Length cutting precision
- Wave consistency along rails
- Corner rounding control
Production Volumes
- Line speeds achievable
- Quick die changeover ability
- Easy size adjustments
- Reliable material feeding
Customization Offered
- Range of guardrail sizes
- Special wave contours
- Custom roll pass design
- Additional punching/bending
Automation Features
- User-friendly HMI for monitoring
- Preset recipes for fast changeovers
- Real-time diagnostics for errors
- Motor overload protection
Service Support
- Operator training assistance
- Quick response to breakdowns
- Local suppliers preferred
Evaluating manufacturers on these parameters increases chances of selecting ideal OEM guardrail roll former in line with road project requirements.
OEM Guardrail Roll Former Suppliers
প্রতিষ্ঠান | Location | যোগাযোগ | Price Range |
---|---|---|---|
Boditech Machines | China | +86 18902969559 | $150,000 – $350,000 |
Rollex Group | ভারত | +91 98106456329 | $200,000 – $500,000 |
Installing OEM Guardrail Roll Lines
Correct installation is vital for optimum working of guardrail roll formers. Primary steps include:
Site Preparation
- Level concrete or steel base
- Working room for safe functioning
- Adequate shed for equipment
- Sufficient power supply
Component Positioning
- Assemble machine as per drawings
- Precision alignment of roll stands
- Proper anchoring for stability
Electrical Connections
- Individual drives for motors
- Control wiring as per schematics
- Safe earthing of panels, motors
Trial Production
- Parameter adjustment without coil
- Check strip feeding, shear, sensors
- Monitor current, hydraulic levels
- Ensure specifications are achieved
Taking suitable precautions during commissioning prevents issues afterward when functioning.
Best Practices for Operation and Maintenance
Activity | Frequency | Purpose |
---|---|---|
Visual Inspection | Daily | Check for component wear, safety |
Sensor Calibration | Monthly | Ensure correct strip positioning |
Hydraulic Oil Change | Quarterly | Prevent leakage or overflow |
Machine Lubrication | Weekly | Reduce friction, enable smooth running |
Software Upgrades | As available | Enhance working parameters, features |
Wear Analysis | Yearly | Assess if rollers need grinding, replacing |
Benefits of OEM Guardrail Roll Lines
- High speed production saves time/costs
- Superior consistency versus manual bending
- Quality remains uniform batch after batch
- Programmable PLC enables process automation
- Swift recipe changes for new sizes
- Safer versus site metal working
- Scalability for larger order volumes
- Limited operators needed
- Lower maintenance without dies
- Compact equipment reduces space
Limitations of Roll Formed Guardrails
- Substantial initial capital investment
- Sophisticated components prone to damage
- Qualified technicians required for service
- Restricted flexibility compared to custom fabrication
- Fine tuning needs expertise during setup
- Auxiliary tools needed for added complexity
- Space constraints can restrict line lengths
- Limitations on material thickness
Mitigation measures during selection and preventive maintenance in working lifecycle minimizes these limitations for maximum ROI from guardrail roll line assets.
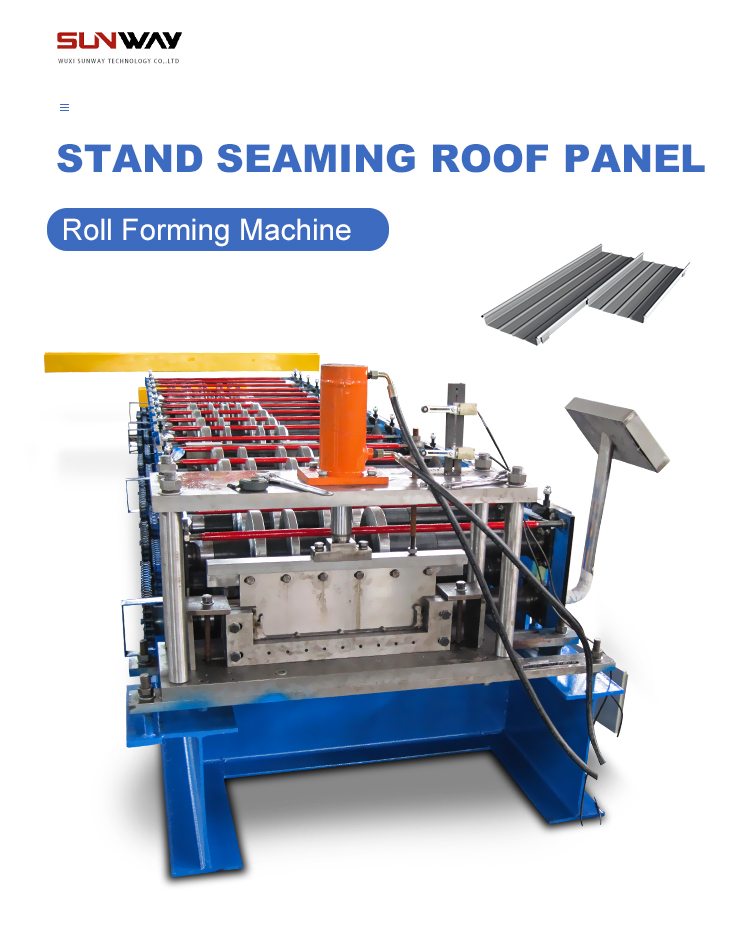
FAQ
Q: What thickness of coils can be formed into guardrails?
A: These machines typically process 1.2 to 4 mm strength steel coils for longitudinal barrier specifications. Up to 6 mm capacity is possible with customized roller design.
Q: What processes connect individual guardrail pieces?
A: Slotted joints with splice bolts are commonly used. Punching machines make slots in sides before anti-burst tubes get inserted and bolted on site.
Q: How is length of guardrails controlled during production?
A: Encoders feed strip at set speeds in sync with cutters. Length compensation via PLC ensures precision trimming matched to vehicle impact requirements.
Q: What factors affect choice of line speed for quality?
A: Roller material, frame rigidity, strip width, steel grade, thickness, straightness, and tensioning determine maximum line speed for defect-free ribbons.
Q: How can additional complexity be built into guardrails?
A: Secondary presses, punches, drilling machines, bending stations can be integrated in the line for custom holes, slots, contours if needed.
উপসংহার
OEM guardrail roll forming lines represent an optimal balance between efficiency, quality, and customization for companies looking to produce road safety barriers. Careful evaluation of product robustness and after-sales support while selecting suppliers goes a long way in determining outcomes. Periodic auditing of machines combined with good maintenance practices ensures maximum working life. When appropriately configured and operated, these roll former assets provide substantial productivity gains versus other approaches of guardrail fabrication.