Metal roofing offers durability, weather resistance and long lifespan for buildings. Roll forming technology allows cost-effective, high speed production of strong metal roofing sheet profiles via continuous bending of coils through consecutive roller dies.
This guide aims to provide end-to-end technical knowledge regarding metal roofing sheet roll forming machines to help business owners select optimal solutions fitting their production needs and budget.
Overview of metal roofing sheet roll forming machine
Roll forming machines shape metal coils into various structural profiles with custom cross-sections via a series of roller stations applying incremental bends.
Key attributes of metal roofing sheet roll formers:
- Raw material: Prepainted steel, aluminum, zinc alloys
- Sheet thickness: 0.3mm to 1.2mm
- Roofing profiles: Corrugated, box-ribbed, tile patterns
- Production rate: 10 – 100 meters/minute
- Advanced PLC control systems
- High forming precision
Roll formed metal roofing combines aesthetics, lightweight and corrosion resistance to replace conventional materials like asbestos, concrete or clay tiles. Consistent quality and just-in-time supply makes it ideal for modern construction needs.
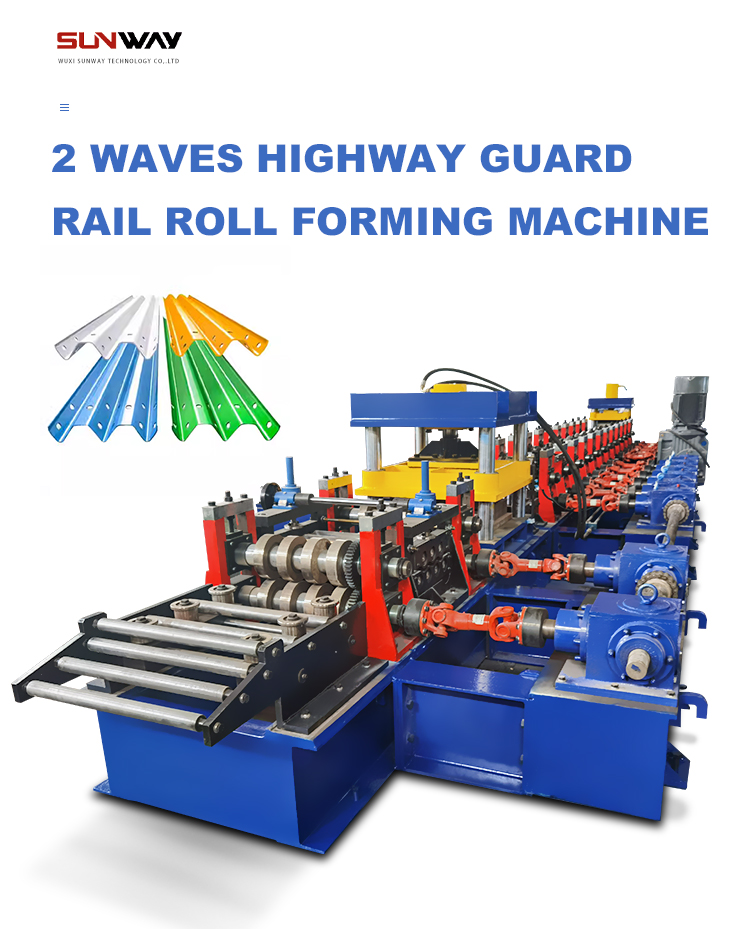
Types of Metal Roof Sheet Roll Forming Machines
Machine Type | Description |
---|---|
CNC roll former | Precision bending via software models |
Automatic cutoff line | Integrated cross-cutting unit |
In-line punching | Hole creation or embossing |
Profile roll former | For specialized roofing shapes |
Powder coating line | Cleans and color coats sheets |
Stacker/bundling line | Automates packaging tasks |
Optional capabilities:
- Printing
- Double layer lines
- Vision inspection systems
- Strip accumulators
Working Principle of Metal Roof Sheet Roll Forming
দ্য working principle involves gradually bending metal coils into roofing profiles via incremental roller stations.
Steps:
- Decoiler mechanism unrolls metal coil
- Sheet feeding tables straighten and guide strip
- Forming heads bend strip by pressing it around contoured rollers
- Separate cutoff shears lengthwise sections
- Exit tables assist with downstream processes
Easy interchangeability of forming heads allows changing produced profiles fast by replacing tooling components.
Advanced PLC control coupled with precisionformed rollers ensures consistency and high tolerances during high speed mass production.
Process Flow in Metal Roof Sheet Roll Forming
The common process flow comprises:
1. Metal Coil Selection
- Aluminium, coated steel etc.
- Width ~800-1250mm
- Thickness ~0.5mm
- Coating – zinc, colors etc.
2. Decoiling & Feeding
- Ensuring proper strip guidance
3. Roll Forming
- Through series of roller stations
- Monitoring via sensors
4. Cutoff & Stamping (optional)
- Trimming sheets to length
- Stamping logos, patterns
5. Downstream Processes (optional)
- Printing
- Powder coating
- Vision inspection
- Packaging
Following standardized protocols in each stage ensures high quality finished metal roofing sheets.
-
Standing Seam Roof Panel Curving Machine
-
ব্যারেল ঢেউতোলা রোল ফর্মিং মেশিন
-
Stand Seaming Roof Panel Roll Forming Machine
-
ডাউনস্পাউট পাইপ রোল তৈরির মেশিন
-
গটার রোল তৈরির মেশিন
-
Trapezoidal Panel Roll Forming Machine
-
রিজ ক্যাপ রোল ফর্মিং মেশিন
-
ডাবল লেয়ার প্যানেল রোল তৈরির মেশিন
-
ছাদের টাইল প্যানেল রোল তৈরির মেশিন
Design Considerations for Metal Roof Sheet Roll Forming Lines
Optimizing roll former design is vital for efficient functioning. Major aspects:
Sheet Material Selection
Common metal types:
- Low carbon steel – cost effective
- Aluminium – lightweight, corrosion resistant
- Galvanized steel – moderate corrosion protection
- Prepainted steel – high durability and aesthetics
Desired width, thickness, coatings depend on application.
Roofing Profile Selection
Popular roofing profiles producible:
- Corrugated sheets
- Box ribbed
- Tile patterns
- Trapezoidal rib
- Custom crimping
More complex shapes need additional tooling stations.
Production Speed
Higher speeds via wider coils or quicker cycles increases output:
- Light duty: Up to 30 meters/minute
- Standard duty: 30-60 meters/minute
- Heavy duty: Above 60 meters/minute
Roller & Cutoff Design
- Roller materials to resist deformation
- Hardened cutoff blades for precision
- Integrated punching modules
Additional Modules
- Printing
- Powder coating
- Packaging equipment
Key Components of Metal Roof Sheet Roll Forming Machines
Component | Purpose |
---|---|
ডিকয়লার | Smooth coil holding |
Feeder | Ensures proper strip flow |
Forming assemblies | Shapes sheets into profiles |
Roller stations | Houses tooling components |
Cutoff shear | Trims sheets to length |
PLC controller | Monitoring and precision |
Sensors | Feedback signals |
Exit tables | Supports finished sheets |
Buying Considerations for Metal Roof Sheet Roll Forming Equipment
Key aspects in selecting metal roofing sheet roll forming machinery:
Parameter | Guidelines |
---|---|
Production speed | To meet market demand |
Profile types needed | Corrugated, box-ribbed etc |
Raw material width | For high productivity |
Tooling stations | More for complex sheets |
Controls sophistication | Sensor feedback for precision |
Additional modules | Printing, stacking etc |
Service support | Installation, maintenance etc |
Machine footprint | Floor space requirements |
Certifications | ISO, CE markings |
Request quotes from various machine manufacturers to find optimal balance of price versus production quality and consistency.
Installation of Metal Roof Sheet Roll Forming Machines
Correct machine positioning and assembly ensures smooth functioning.
Key steps:
- Prepare flat, leveled base
- Unload components safely
- Review electrical connections
- Arrange parts as per drawings
- Anchor machine properly
- Test run direction of movements
- Set operating parameters
- Trial with slow speed initially
Having vendors guide commissioning and train workers reduces safety risks and operational issues. Follow guidelines stringently.
Operation of Metal Roof Sheet Roll Forming Machines
Adhering to standardized protocols during functioning optimizes productivity and minimizes deviations.
Safety Guidelines
- Allow only certified workers to operate
- Ensure no exposure near roller gaps
- Use proper machine guarding
- Mandate gloves, shoes, glasses
Production Workflow
1. Material Loading
- Mount appropriate coils on decoiler
- Thread end through components
2. Parameter Setting
- Input product dimensions at HMI
- Configure speeds, tolerances
3. Trial Runs
- Inch slowly first
- Confirm sensor feedbacks
4. Production
- Run at specified pace
- Monitor for process deviations
- Conduct quality testing
Document all procedures clearly for easy operator reference to maintain consistency.
Maintenance of Metal Roof Sheet Roll Forming Machines
Preventative maintenance activities sustain performance, minimize unplanned downtime losses.
Activity | Method | Frequency |
---|---|---|
Decoiler inspection | Check wear, damage | Monthly |
Fastener tightening | Use torque wrenches | Quarterly |
Sensor testing | Compare values to set points | Monthly |
Hydraulics inspection | Check leaks, pressures | Monthly |
Electrical safety | Insulation testing | Quarterly |
Lubrication | Replenish gear and slideway oils | Quarterly |
Calibration | Reset benchmarks, tolerances | Yearly |
Blade sharpening | Restore shear edge condition | As needed |
Proper scheduling of these activities during planned outages optimizes production runs.
Choosing Metal Roof Sheet Roll Forming Machine Manufacturers
Guidelines for selecting reputable equipment vendors:
Consideration | Description |
---|---|
Product range | Diverse profile shapes producible |
Machine quality | Durability, precision |
Design expertise | Skill in translating needs to solutions |
Production scales | Capability to deliver committed volumes |
Solution customization | For specialized requirements |
After-sales service | Installation, maintenance etc |
Pricing and transparency | Competitive quotes, clarity |
Quality certifications | ISO compliance etc |
Talk to industry peers and evaluate options based on business growth projections too.
Pros and Cons of Metal Roof Sheet Roll Forming Machines
Advantages:
- High production rates with consistency
- Ideal for long production runs
- Automated precision control
- Limited workforce needed
- Lower costs than alternate methods
- Custom profiles feasible
Limitations:
- High initial capital investment
- Skilled staff needed for operation and maintenance
- After-sales service depends on supplier proximity
When designed and operated properly, roll forming lines offer excellent productivity and economy at scale for metal roofing manufacturers.
Cost Analysis of Metal Roof Sheet Roll Forming Equipment
Machine Rating | Price Range |
---|---|
Light duty line | $35000 to $55000 |
Standard duty line | $55000 to $95000 |
Heavy duty line | $95000 to $225000 |
Secondary processing modules | ~$5000 per station |
Influencing factors:
- Production speed rating
- Type of profiles made
- Level of automation
- Additional capabilities
- Manufacturer’s brand value
Higher investment generally viable through operational cost savings over time.
Applications of Metal Roof Sheet Roll Forming Machines
Industry areas utilizing roll formed roofing sheets:
By Sector
- Housing
- Commercial buildings
- Hospitality
- Healthcare
- Infrastructure
By Location
- Roofs
- Wall cladding
- Structural sections
- Decorative fascia
- Pergolas
By Material
- Prepainted steel
- Aluminium
- Copper
- Zinc and titanium alloys
Suitability for corrosive environments, longevity, aesthetics and insulation properties make such sheets ideal for modern needs.
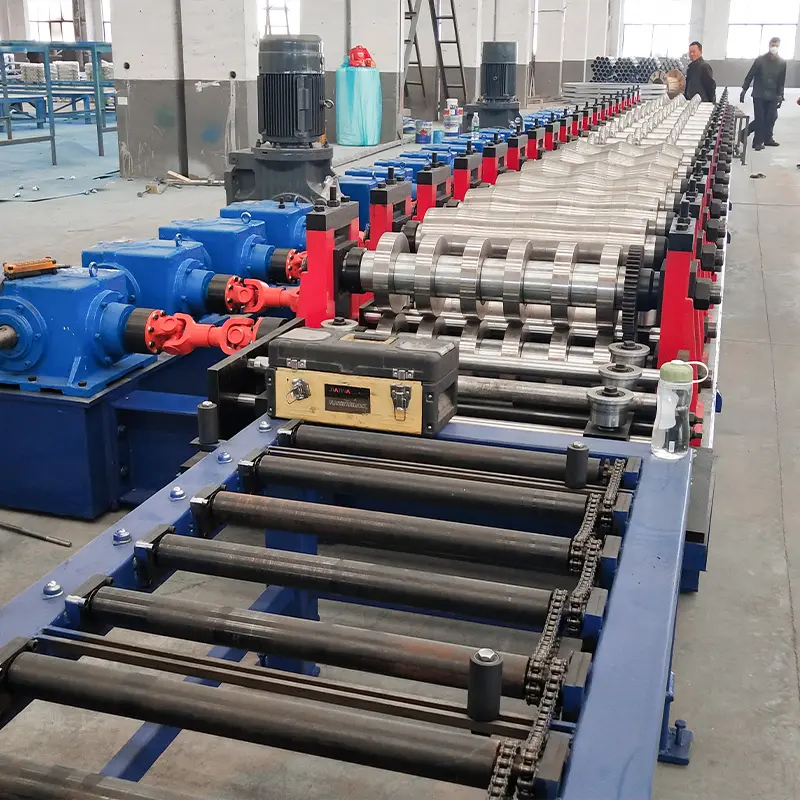
উপসংহার
Metal roof sheet roll forming lines enable efficient automated production of strong yet lightweight profiles for cladding, roofing, siding and structural sections across residential and commercial buildings.
When designed appropriately around production volume, line speed, profile type/complexity and secondary processing needs – they consistently manufacture high quality metal roofing components matching construction sector demand.
Careful equipment selection plus standardized installation, operation and maintenance best practices results in good ROI via scrap reduction, energy efficiency and consistent quality output.
Partnering with expert roll forming machinery manufacturers helps translate functionality needs into tailored equipment solutions boosting productivity and competitiveness through manufacturing innovation.
FAQs
Q: What metal properties are ideal for roofing sheet roll forming?
A: Ductility for extensive bending, moderate strength and hardness for holding shape, corrosion resistance for weatherability, weldability for downstream operations and coatability to enhance longevity.
Q: What post-forming operations help enhance roof sheet durability?
A: Pre-painting, metallic/organic coatings, anti-fingerprint treatment, embossing aesthetic patterns, applying protective film, crimping and corrugation help improve visual appeal while resisting weather effects.
Q: What regular maintenance helps sustain roll formed roofing quality?
A: Activities like machine cleaning, belt tensioning, lubrication, visual inspection, sensor calibration, shear sharpening etc. are vital for uninterrupted high speed production without quality fluctuations.
Q: How does roll forming compare with other metal roofing production methods?
A: It avoids limitations in versatility of casting and restrictions on part size of stamping. Unlike plastic extrusion, it offers higher strength. Roll forming also keeps costs lower than alternate approaches like machining or laser cutting.
Q: Can solar cells be integrated with roll formed roofing metal sheets?
A: Yes, photovoltaic films and wiring can potentially be embedded between substrate layers using secondary processing add-ons to produce integrated solar panel metal roofing on demand.
Q: How can metal roof performance be enhanced further through coatings?
A: Thermal spray methods allow embedding ceramic granules within roofing coatings to improve solar reflectance along with anti-corrosion and mechanical resistance properties.
Q: What testing standards are used to evaluate metal roof sheet quality?
A: Parameters like bend testing, corrosion testing in salt spray chambers, weather-ometer accelerated aging, cross-hatch adhesion, puncture resistance, chalk-testing etc. per ASTM specs ensure durability.
Q: How to optimize cutting length after roll forming for lowest scrap?
A: Negative scrap methods dynamically regulate production pace to minimize end remnants. Positive scrap methods utilize vision inspection plus forced delays to synchronize cutoff.