manual roll forming machine is a continuous bending process used to form metal sheet and coils into custom profiles. Manual roll formers are simple machines operated by hand to produce small batches or custom parts.
Manual Roll Former Equipment Guide
যন্ত্রপাতি | Description |
---|---|
Forming rolls | Contoured rolls mounted in housing |
Roll adjustment | Manual screws to set roll gap |
Feed table | Flat table to support material |
Hand crank | Rotates forming rolls |
Guide plates | Metal strips to guide material |
- Manual rollers use hand-adjusted forming rolls
- Material is fed through by turning hand crank
- Guide plates align strip through rolls
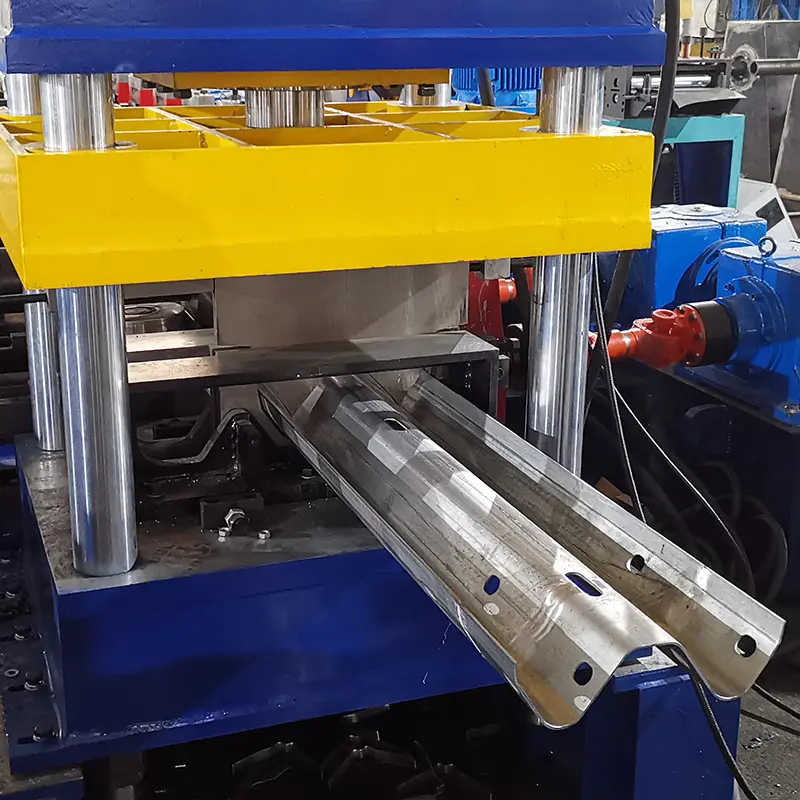
Working Process of Manual Roll Forming
The process starts by positioning the flattened strip on the feed table and inserting the leading edge into the roll gap. The hand crank is then turned continuously to rotate the rolls. As the strip passes between the contoured rolls, it begins to take the shape of the roll profiles. Once fully formed, the strip can be cut to the desired length by shears.
Material Feeding in Manual Roll Formers
Method | Description |
---|---|
Feed table | Flat table to support coils/sheets |
Guide plates | Attach to table to keep alignment |
Hand feeding | Operator feeds strip through rolls |
Support rollers | Reduce friction when feeding |
- Feed table supports the material
- Guide plates keep strip alignment
- Operator manually feeds the strip
- Support rollers ease material flow
Profile Forming in Manual Roll Benders
Method | Description |
---|---|
Forming rolls | Contoured rolls mounted in housing |
Roll materials | Various steel alloys |
Roll adjustment | Set roll gap spacing |
Control | Hand crank for rotating rolls |
- Forming done by hardened steel rolls
- Rolls machined to required profiles
- Roll gap spacing is hand adjusted
- Hand crank control to turn rolls
Common Profiles from Manual Roll Formers
Shape | Description |
---|---|
Angles | L shaped profiles |
Channels | U shaped profiles |
Round tubes | Hollow circular tubes |
Square tubes | Hollow square tubes |
Custom | Unique shapes |
- Angle, channel and tube profiles commonly produced
- Capability for custom shapes as needed
- Usually simpler profiles due to process limits
-
Standing Seam Roof Panel Curving Machine
-
ব্যারেল ঢেউতোলা রোল ফর্মিং মেশিন
-
Stand Seaming Roof Panel Roll Forming Machine
-
ডাউনস্পাউট পাইপ রোল তৈরির মেশিন
-
গটার রোল তৈরির মেশিন
-
Trapezoidal Panel Roll Forming Machine
-
রিজ ক্যাপ রোল ফর্মিং মেশিন
-
ডাবল লেয়ার প্যানেল রোল তৈরির মেশিন
-
ছাদের টাইল প্যানেল রোল তৈরির মেশিন
Cutoff Method for Manual Roll Formers
Method | Description |
---|---|
Shear | Hand operated shear |
Saw | Portable saw |
Support tables | Tables to collect cut parts |
- Cutoff done manually via shear or saw
- Tables to safely collect cut pieces
Customization Options in Manual Roll Benders
Option | Description |
---|---|
Custom rolls | Profile specific rolls |
Quick change | Roll changes without reassembly |
Size adjustment | Spacers for roll adjustment |
Tooling kits | Special forming accessories |
- Custom roll sets for unique profiles
- Quick roll changes possible with clamp housings
- Spacers inserted to adjust sizing
- Tooling kits offered for specialty forming
Suppliers of Manual Roll Forming Machines
Manufacturer | Location | Price Range |
---|---|---|
Acro Metal Stamping | Canada | $3k – $7k |
Carell Corp | USA | $5k – $15k |
Durma | Turkey | $3k – $10k |
Gasparini | ইতালি | $10k – $30k |
Sahinler Roll Forming | Turkey | $4k – $12k |
- Many manual roll bender models available
- Prices range from a few thousand to tens of thousands
- Quality varies greatly, durability is key factor
Installation and Operation
Activity | Description |
---|---|
Positioning | Accessible location for operation |
Leveling | Use shims to level feed tables |
Test run | Confirm forming with sample material |
Operation | Control direction and feed rate |
Safety | Follow guards, precautions |
- Position for ease of loading/unloading
- Levelness is critical for proper feeding
- Test runs validate forming process
- Controlled hand feeding minimizes issues
- Strict safety protocols are essential
Maintenance of Manual Roll Benders
Method | Description | Frequency |
---|---|---|
Cleaning | Remove dirt, metal chips | Daily |
Lubrication | Apply oil to gears, bearings | Monthly |
Inspection | Check roll surface, alignment | Quarterly |
Roll change | Replace worn rolls | As needed |
Overhaul | Major repairs | If breakdown |
- Regular cleaning of metal fines
- Lubrication reduces wear and noise
- Inspection catches issues early
- Roll sets replaced when excessively worn
- Overhauls done if major failure occurs
Choosing a Manual Roll Former Supplier
Factor | Description |
---|---|
Price | Upfront cost more important than operating cost |
Lead time | Quick delivery enables fast setup |
অভিজ্ঞতা | Know-how with specialty profiles preferred |
কাস্টমাইজেশন | Ease of producing custom tooling |
সমর্থন | Install guidance and operator training useful |
Manuals | Clear instructions on operation, safety |
Standards | Meets applicable quality and safety codes |
- Seek balance of price versus longevity
- Quick delivery is advantageous
- Custom roll capability essential
- Look for responsive technical support
- Clear manuals reduce learning curve
- Reputable firms meet regulatory standards
Pros and Cons of Manual Roll Benders
Advantages
- Very economical for low volume production
- Fast design iteration with rapid tooling changes
- Allows small batch custom profiles
- Flexible setup for different product sizes
- Low power consumption versus motorized equipment
- Compact size fits production environments with space constraints
- Simplified design gives high uptime and availability
Limitations
- Labor intensive manual operation
- Inconsistent throughput dependent on operator skill
- Heightened safety hazards from hand feeding
- Limits on part size and forming complexity
- Repeated handling can reduce end quality
- Not practical for high volume production needs
Applications of Manual Roll Benders
Typical applications include:
- Custom electrical enclosures
- Specialty HVAC ductwork
- Low quantity metal furniture parts
- Short run metal artwork frames
- Custom architectural facade elements
- Unique ornamental iron components
- Small specialty automotive accessories
- Experimental and rapid prototype sections
Common materials formed are steel, aluminum, copper, and brass in gauges from 0.5 mm to 3 mm thickness.
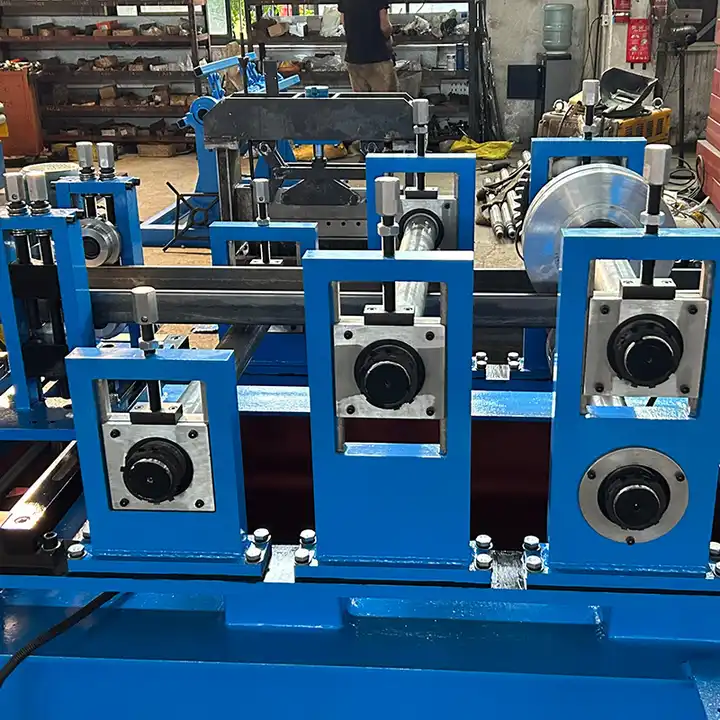
FAQ
What profiles can be formed on manual roll benders?
Common shapes are angles, channels, square/rectangular tubes, round tubes and cones. Custom profiles are possible but complexity is limited by the manual process.
What thickness of metals can be manually formed?
Standard models typically form material from 0.5 mm to 3 mm thickness. Extended ranges available on some heavy duty models.
How accurate are the profiles created from manual rolling processes?
Precision is heavily dependent on operator skill, but properly leveled machines with adequate guides can achieve tolerances around +/- 0.5 mm.
How much power is required to operate manual roll benders?
No external power source is required. The hand crank mechanism provides the motive force to drive the forming rolls.
What determines the production rate of manual rolling?
Throughput is limited by the speed the operator can safely feed the material through the rollers, typically less than 10 feet per minute.
What are important safety guidelines for manual roll operations?
Guards around rolls, guide plates to avoid pinching, gloves to protect hands, strict one operator policy, and emergency stops are critical to safety.
What is the biggest factor impacting quality and longevity of these machines?
The quality of the roll bearings is often the main determinant of lifespan, performance, and durability under prolonged use.
How much do replacement custom roll sets cost for specialty profiles?
Roll sets can range from $500 for common shapes to $5000 or more for complex custom shapes requiring specialized machining.
Are manual roll benders suitable for small scale commercial production?
They can be appropriate for limited commercial work depending on volumes. Automated machines are preferred for scale production.