Light steel frame roll forming machinery produces cold-formed steel structural framing studs and tracks for building construction from coiled sheet metal in an automated process. This comprehensive guide covers different types, working principles, capabilities, pricing, suppliers, operations and more for these important metal processing lines.
Overview of Light Steel Frame Roll Forming Machines
Roll forming machines that shape light gauge steel into C-studs, U-channel tracks, trusses and custom profiles for structural framing support offer versatility, efficiency and precision unmatched by other techniques. Key capabilities include:
- High productivity from automated forming at over 30ft/min
- Cold formed stud widths from 50mm to 300mm
- Material thickness from 18 gauge to 22 gauge
- For wall systems, roof trusses, solar mounts etc.
- Superior strength-to-weight ratio
- Custom profiles programmed through tooling
- Easy to install modular construction
- Recyclable, sustainable green building material
Light steel gives structural integrity to commercial and residential buildings with its high strength reinforcing properties. Pre-formed modular framing accelerates safe construction. The roll forming process enables mass production of studs.
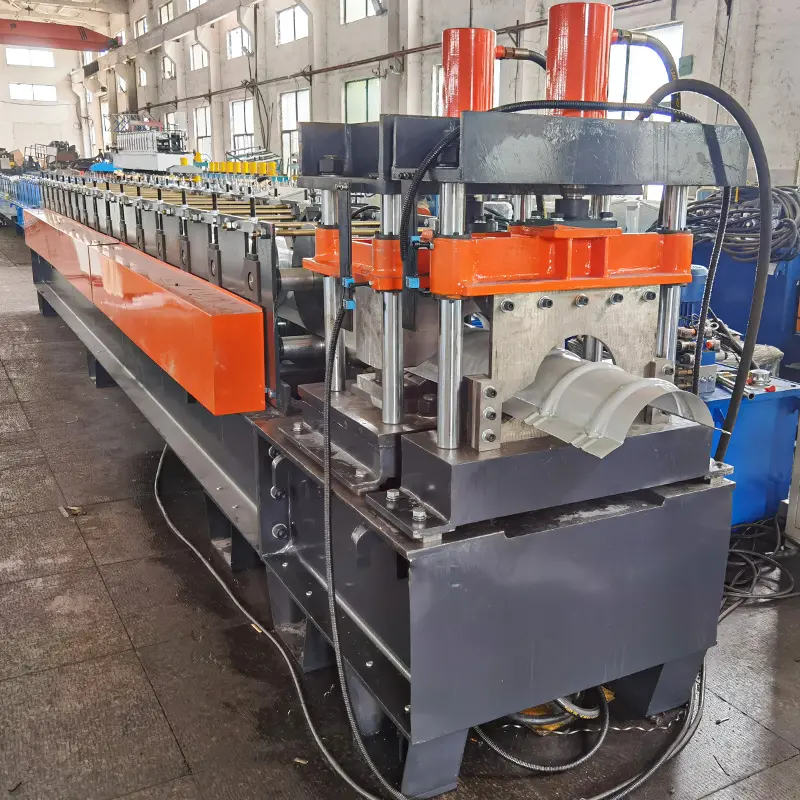
Types of Light Steel Frame Roll Forming Machines
Type | Description |
---|---|
Portable | Compact movable units with 1-3 forming heads for small scale on-site production. Lower investment cost better for remote locations and custom work. Output limited to 20-25 pieces per minute based on size. |
Stationary Industrial | Integrated high capacity lines designed for continuous high volume output exceeding 50 pieces per minute. Require permanent facility and high initial expenditure offset by productivity over time. Ideal for large orders. |
Portable Machines offer mobility in production location and meet smaller batch requirements economically while ability to create specialty profiles on-demand. Well suited for remote construction sites.
Industrial Lines engineered for 24/7 high speed mass production in fixed factory infrastructure. Parametric control allows fast reproduction of standard profiles. The high output results in lower unit cost for large orders.
Choose machine type based on expected order demand, location constraints, power availability and budget.
Working Principle of Roll Forming Process
The common steps in the automated roll forming sequence are:
1. Decoiling – Feed stock coil loaded and sheet end aligned to entry
2. Feeding – Powered rollers pull sheet into start of line
3. Formation – Sheet formed gradually through consecutive stations
4. Cutting – Finished studs sliced to length by built-in cutter
5. Stacking – Formed pieces discharged onto table for bundling
Detailed Process Flow:
- Operator loads specified coil of sheet steel on powered de-coiler
- De-coiler feeds metal sheet into initial forming stands
- Sheet progresses through series of rolling header stations
- Stations with contoured rollers incrementally bend sheet
- Final station forms finished stud profile and desired dimensions
- End cutting machinery slices pieces to length for discharge
- Conveyor sections transport cut product for stacking
- Bundled finished goods prepared for shipment
The adjustable tooling makes changing dimensions fast for various profiles. Next we examine materials, customization and more features.
-
Highway Guardrail End Terminal Forming Machine
-
Highway U/C Post Roll Forming Machine
-
2 Waves Highway Guardrail Roll Forming Machine
-
3 Waves Highway Guardrail Roll Forming Machine
-
বৈদ্যুতিক মন্ত্রিসভা ফ্রেম রোল গঠনের মেশিন
-
দিন রেল রোল ফর্মিং মেশিন
-
দুই তরঙ্গ হাইওয়ে গার্ডেল মেশিন
-
থ্রি ওয়েভ হাইওয়ে গার্ডেল মেশিন
-
তারের মই রোল ফর্মিং মেশিন
Material, Design and Customization
Sheet metal: Hot-dipped galvanized steel, AZ steel, pre-painted coils
Thickness: 0.7mm to 1.2mm (18 to 22 gauge)
Width: 50mm to 300mm for C and U channels
Coatings: Zinc, Aluminum-Zinc alloys for corrosion protection
Standards: AISI S100, AS/NZS 4600, EN 1090, BS 5950 etc.
Performance: Fire, sound insulation; wind uplift resistance
Custom profiles: Varies based on unique tooling for special shapes
Material grade should suit strength, lifetime needs. Custom tools incur NRE costs but enable specialty sections as required.
Standard Features and Optional Accessories
Standard Features | Optional Accessories |
---|---|
10-20 Forming Stations | Decoiler Feeder |
Parametric PLC Control | Powered Conveyor Sections |
HMI Touchscreen | Punching, drilling, embossing |
Sheet Decoiler | Panel sizing side/swaging |
Initial Shear/Crop Station | Packaging Tables |
Finishing End Cutter | Custom Tooling |
Discharge Conveyors | UL/CE Compliance |
Safety Guarding | IoT Remote Monitoring |
Now we examine cost driving factors.
Light Steel Frame Roll Forming Machine Price Range
Cost Impact Factors:
Parameter | Influence |
---|---|
Type | Portable or Industrial |
Size | Width – Stud capacity |
Level of Automation | Manual or Automated |
Functions | Basic Forming vs Secondary Operations |
নিয়ন্ত্রণ ব্যবস্থা | Basic vs Parametric PLC |
Tooling | Standard or Custom |
Compliance | UL/CE Certification |
Training & Support | Included or Additional |
Budget Price Range: $35,000 to $180,000
- Portable machines
- Narrow width
- Manual stacking
- Basic forming & controls
- Standard tooling
Industrial Price Range: $230,000 to $600,000
- Integrated production lines
- Wider coils
- Automated processes
- Advanced controls, options
- Customized tooling
- Certification
Requesting multiple quotations from shortlisted suppliers gives optimal value. Guidelines for selection in next section.
Choosing Light Steel Frame Roll Forming Machine Manufacturers
Consideration | Importance |
---|---|
Company Experience | Number of years in business |
Specialization | Focus on roll forming equipment |
Range of Equipment | Overall capabilities |
Custom Profile Ability | For specialty sections |
Build Quality | ISO certifications |
Installation Support | On-site and remote options |
Pricing | Machine cost, life cycle value |
Communication | Responsiveness ease |
Recommended Suppliers:
প্রতিষ্ঠান | Location | যোগাযোগ |
---|---|---|
ECC Roll Forming Machines | Missouri, USA | +1 417 895 1334 |
ZLT Machinery | Shandong, China | +86 539 872 6629 |
Form Process Engineering | Bari, Italy | +39 0809 631 791 |
Tips when ordering:
- Provide size, quantity estimates
- Get layout, GA drawings
- Compare quotations
- Clarify delivery, payment
With the machine ordered, we look at physical installation.
Installation and Setup
On-Site Placement Sequence
- Coordinate delivery logistics
- Unload components safely
- Inspect hardware for defects
- Assemble base frame on leveled surface
- Position and bolt forming stands
- Install decoiler, straightener
- Mount control panel, connect wires
Programming and Configuration
- Enter product dimensions
- Adjust forming rollers
- Inch material through slowly initially
- Test sample pieces for quality
- Refine pressure settings, speeds
- Store optimized recipes
Trial and Training
- Manual operation testing
- Automatic run sampling
- Operator controls tutorial
- Overview preventive maintenance
- Review safety procedures
Careful calibration and runoff builds consistency before entering full production. Running properly also requires adhering to operational best practices.
Operation and Maintenance
Running Guidelines
- Select appropriate width coil material
- Inspect quality – no burnt edges, warp
- Monitor line operation, stop on faults
- Clear scrap pieces to avoid jamming
- Lubricate machinery daily
- Manage cut piece stacking/bundling
Upkeep Activities
- Schedule preventative maintenance
- Inspect electrical, mechanical systems
- Check chain/gear wear; tension properly
- Test emergency stop circuit
- Backup control parameters
- Replace worn forming rollers
- Touch up paint chips
Proper practices maximize production uptime and line longevity. The next section answers common queries.
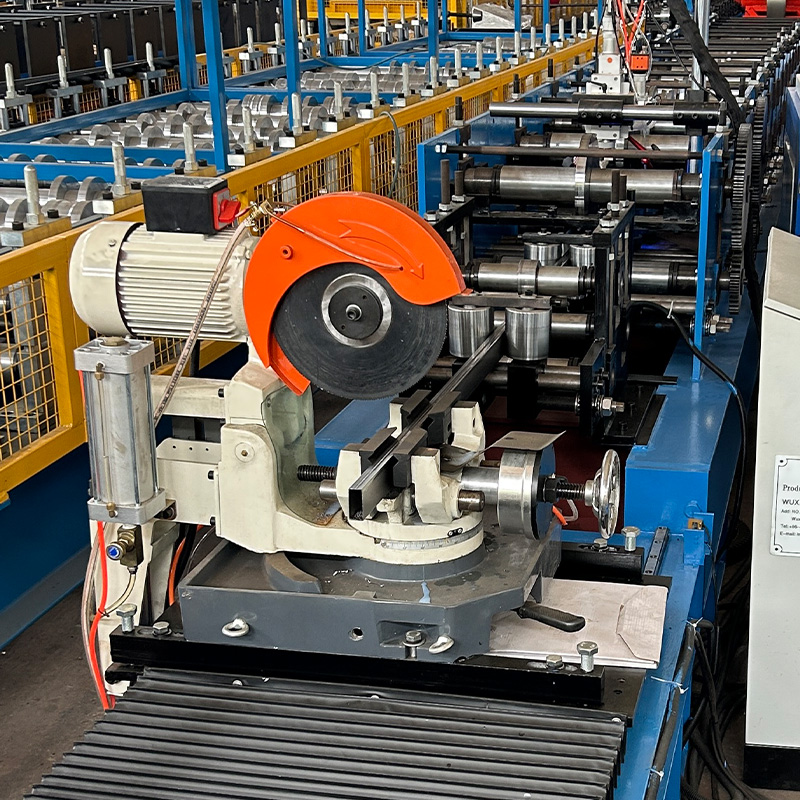
FAQ
Q: What safety mechanisms are incorporated?
A: Light curtains, E-stops, guards, control reliability to PLd per ISO 13849 at minimum.
Q: What length accuracy is possible for cut studs?
A: Within +/- 3mm tolerance based on machine capability.
Q: How often should forming heads be changed?
A: After 300,000 linear feet under normal CFS grade material use.
Q: What climate control is recommended?
A: Temperature regulation to 18-22°C, humidity control prevents coil corrosion.
Q: What output rates are viable?
A: 16-50+ finished pieces per minute based on width and automation level.
Q: What are limitations?
A: Thicker or multilayer coils require bigger capacity machines.
Please reach out for any other questions!
উপসংহার
In summary, this guide has provided a comprehensive overview of light steel frame roll forming machine types, configurations, working principles, features, customization options, approximate pricing, supplier selection, installation and operational best practices. Engineered for efficiency, precision and speed, these metal processing lines enable mass production of cold-formed framing studs and tracks from coiled steel to serve the construction industry worldwide through sustainable buildings. With appropriate machine selection, setup and maintenance, manufacturers can reap productivity and quality benefits from the automated forming process for years.