Imagine a factory floor abuzz with activity. Sheets of metal are being transformed into the sturdy frames that house vital electrical components – control panels, distribution boxes, and instrument enclosures. The unsung hero behind this metamorphosis? The electric cabinet frame roll forming machine.
In essence, this machine is a metalworking marvel that continuously bends sheet metal into complex shapes using a series of precisely contoured rollers. Think of it as an automated metal origami artist, meticulously crafting the foundation for countless electrical applications.
But these machines are far more intricate than your childhood Etch A Sketch. Delving deeper, let’s explore the world of electric cabinet frame roll forming machines.
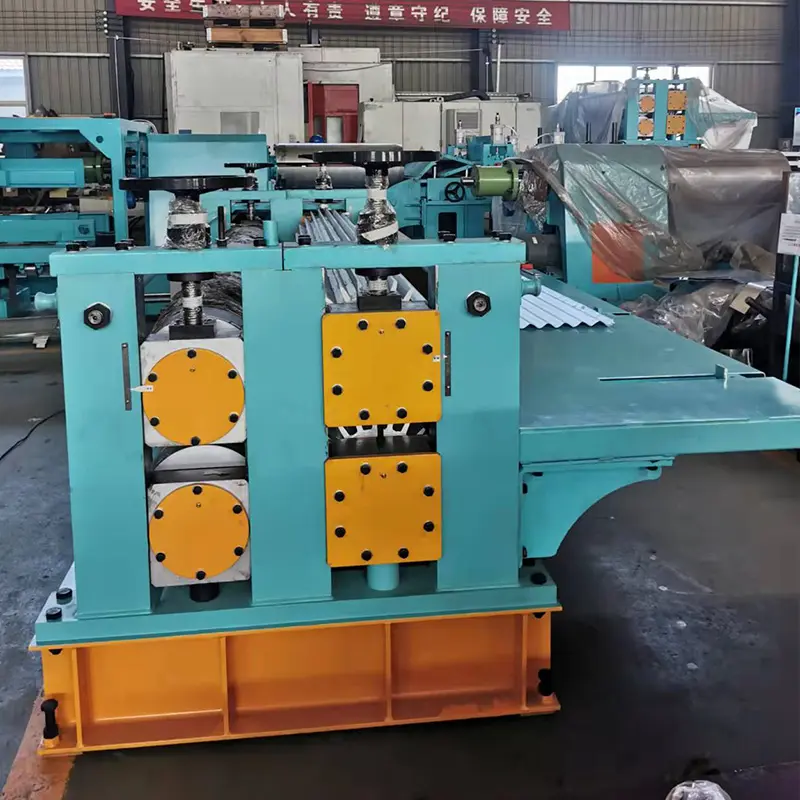
Function of Electric Cabinet Frame Roll Forming Machines
The core function of an electric cabinet frame roll forming machine is remarkably straightforward. It continuously shapes flat sheet metal into predetermined profiles through a series of rollers. These rollers, strategically arranged and grooved, progressively bend the metal, transforming it into a complex cross-section.
Imagine feeding a long sheet of paper through a series of cookie cutters, each progressively shaping it further. That’s the basic principle behind roll forming – but with immensely powerful machinery and high-precision engineering.
The specific shapes created by these machines depend on the configuration of the rollers. These profiles can be intricate, featuring bends, flanges, and holes – all formed continuously from a single sheet of metal. This eliminates the need for multiple cuts, welds, and assemblies, resulting in a streamlined and efficient production process.
Here’s a breakdown of the typical steps involved in electric cabinet frame roll forming:
- Uncoiling: The metal sheet, typically steel or aluminum, is loaded onto a reel and progressively unwound (uncoiled) as the forming process begins.
- Leveling: Any unevenness or waviness in the sheet metal is rectified by a leveling unit, ensuring a smooth and consistent surface for forming.
- Feeding: The leveled sheet is precisely fed into the roll forming mill using a motorized feeding system. This ensures accurate control over the material flow.
- Roll Forming: The sheet metal passes through a series of progressively contoured rollers, each imparting a specific bend or shape. The final profile is achieved by the sequential action of these rollers.
- Punching and Shearing: Depending on the specific cabinet design, holes and cut-outs may be incorporated during the roll forming process using integrated punching and shearing units. This eliminates the need for secondary processes.
- Cutting to Length: Once the desired profile is formed, the metal is cut to a predetermined length using a flying cut-off saw, resulting in a finished cabinet frame.
the Diverse Landscape of Electric Cabinet Frame Roll Forming Machines
While the core functionality remains consistent, electric cabinet frame roll forming machines come in a variety of configurations to cater to different production needs and budget constraints. Here’s a breakdown of the prevalent types:
- Single-Line vs. Multi-Line Machines: Single-line machines are ideal for low-volume production or for creating simple profiles. Conversely, multi-line machines boast dedicated stations for uncoiling, leveling, feeding, roll forming, punching, shearing, and cutting, making them suitable for high-volume production and intricate designs.
- Manual vs. Automatic Control: Manual machines require an operator to control the feeding and cutting processes, while automatic machines are equipped with programmable logic controllers (PLCs) for automated operation. Automatic machines offer greater production consistency and efficiency, but come at a higher cost.
- Roll Forming Speed: The speed at which the sheet metal is fed through the rollers directly impacts production output. High-speed machines are ideal for large-scale production facilities, while slower machines may suffice for smaller operations.
- Material Compatibility: While typically designed for steel and aluminum, some machines can handle thicker gauge materials or even stainless steel.
Additionally, here are some factors to consider when choosing an electric cabinet frame roll forming machine:
- Production Volume: How many cabinets do you plan to produce per day, week, or month?
- Profile Complexity: The intricacy of the desired cabinet frame profile will influence the machine’s capabilities.
- Material Thickness: The machine needs to be compatible with the gauge of the sheet metal you’ll be using.
- Budget: Machine prices vary significantly depending on features, capabilities, and automation levels.
-
Highway Guardrail End Terminal Forming Machine
-
Highway U/C Post Roll Forming Machine
-
2 Waves Highway Guardrail Roll Forming Machine
-
3 Waves Highway Guardrail Roll Forming Machine
-
স্বয়ংক্রিয় আকার পরিবর্তনযোগ্য সিগমা Purlin রোল ফর্মিং মেশিন
-
স্বয়ংক্রিয় আকার পরিবর্তনযোগ্য CZ Purlin রোল ফর্মিং মেশিন
-
স্বয়ংক্রিয় আকার পরিবর্তনযোগ্য Z Purlin রোল তৈরির মেশিন
-
Auto Size Changeable C U Purlin Roll Forming Machine
-
বৈদ্যুতিক মন্ত্রিসভা ফ্রেম রোল গঠনের মেশিন
বৈদ্যুতিক মন্ত্রিসভা ফ্রেম রোল ফর্মিং মেশিন Suppliers
Absolutely, continuing the exploration of Electric Cabinet Frame Roll Forming Machines:keeping in mind that specific pricing may vary depending on factors like customization options, shipping costs, and exchange rates. Here’s a table outlining some notable suppliers:
Supplier | Location | Product Range | Target Audience |
---|---|---|---|
Boschert GmbH | Germany | High-precision, multi-line machines for complex profiles | Large-scale production facilities |
Yamazaki Mazak Corporation | Japan | Reliable and versatile machines with a focus on user-friendliness | Mid-sized to large-scale production facilities |
Dayton Superior | United States | Cost-effective machines suitable for low-volume production or simple profiles | Small to mid-sized fabrication shops |
Roll Forming China | China | Budget-friendly machines for various profile options | Price-conscious manufacturers |
Amada Machinery America | United States | Technologically advanced machines known for speed and accuracy | High-volume production facilities |
It’s important to note that this is not an exhaustive list, and numerous other reputable suppliers exist globally. Conducting thorough research and comparing offerings from various vendors is crucial to finding the machine that best aligns with your specific needs and budget.
the Advantages and Potential Drawbacks of Electric Cabinet Frame Roll Forming Machines
Electric cabinet frame roll forming machines offer a compelling array of benefits that have revolutionized enclosure production. Let’s delve into some of the key advantages:
- Enhanced Efficiency: Compared to traditional fabrication methods involving multiple cuts, welds, and assemblies, roll forming offers a streamlined and significantly faster production process. This translates to increased output and reduced labor costs.
- Improved Precision: The precise control offered by roll forming machinery ensures consistent and uniform cabinet frame dimensions, minimizing the need for rework and enhancing overall product quality.
- Material Savings: Since roll forming utilizes continuous sheet metal, there’s minimal material waste compared to traditional cut-and-weld methods. This translates to cost savings and reduced environmental impact.
- Design Flexibility: Modern roll forming machines can create a wide range of complex profiles, allowing for the production of cabinets in various shapes and sizes to suit diverse applications.
- Reduced Labor Dependence: Automated roll forming machines minimize the need for manual intervention, leading to lower labor costs and increased production consistency.
However, like any industrial equipment, electric cabinet frame roll forming machines also have some potential drawbacks to consider:
- High Initial Investment: The upfront cost of purchasing a roll forming machine can be substantial, especially for high-end, multi-line machines with sophisticated features.
- Limited Production Flexibility: While offering design flexibility within a range, each machine is typically designed to create specific profiles. If your production needs encompass a wide variety of cabinet designs, you may require multiple machines or a highly configurable one.
- Maintenance Requirements: Like all machinery, roll forming machines require regular maintenance to ensure optimal performance and longevity. The complexity of the maintenance will vary depending on the specific machine.
- Skillset for Operation: While some machines boast user-friendly interfaces, operating a roll forming machine effectively may require specialized training, especially for complex configurations.

FAQ
To shed light on some common inquiries regarding electric cabinet frame roll forming machines, here’s a table incorporating frequently asked questions (FAQs):
Question | Answer |
---|---|
What is the typical lifespan of an electric cabinet frame roll forming machine? | With proper maintenance, a well-built electric cabinet frame roll forming machine can last for decades. |
What safety precautions are necessary when operating a roll forming machine? | Standard metalworking safety protocols apply, including wearing safety glasses, gloves, and appropriate clothing. Following the manufacturer’s safety guidelines specific to the machine is crucial. |
Can electric cabinet frame roll forming machines be integrated into automated production lines? | Absolutely! Many modern machines are designed to seamlessly integrate into automated production lines, featuring interfaces for communication with other equipment like cutting machines and robots. |
What are some factors to consider when setting up and operating a roll forming machine? | Proper material selection, accurate machine calibration, and using the correct tooling for the desired profile are all essential for achieving optimal results. |
Where can I find training resources for operating a roll forming machine? | Many machine suppliers offer training programs for their customers. Additionally, industry associations and online resources can provide valuable training materials. |
By delving into these questions and considerations, you can gain a deeper understanding of electric cabinet frame roll forming machines and make informed decisions to optimize your enclosure production process.
উপসংহার
Electric cabinet frame roll forming machines are the workhorses of the enclosure production industry, offering a potent blend of speed, precision, and efficiency. They have demonstrably transformed the way cabinets are manufactured, enabling:
- Mass production: The ability to churn out cabinets at a rapid pace caters to the ever-growing demand for electrical enclosures in various sectors.
- Consistent quality: The precise control inherent in roll forming ensures consistent frame dimensions and quality, leading to reliable and dependable enclosures.
- Reduced costs: By minimizing material waste and streamlining the production process, roll forming machines contribute to significant cost savings in the long run.
- Design innovation: The ability to create complex profiles opens doors for innovative cabinet designs that meet the evolving needs of electrical applications.