In the ever-evolving world of metal construction, efficiency and versatility reign supreme. Double layer panel making machines, also known as double deck or double layer roll forming machines, have emerged as a game-changer, streamlining the production of complex panels in a single pass. But what exactly are these machines, and how do they revolutionize metal sheet production? Buckle up, as we delve into the fascinating world of double layer panel making machines!
Components of Double Layer Panel Making Machine
Imagine a metalworking marvel with two sets of shaping prowess. That’s essentially a double layer panel making machine. Here’s a breakdown of its key components:
- Uncoilers: These robust machines act as the feeding mechanism, unwinding metal coils (steel, aluminum, etc.) with precise control to ensure a smooth production flow.
- Leveling Devices: As the name suggests, these components ensure the metal sheets are perfectly flat and free of bends or warps. A flawless base is crucial for creating immaculate double layer panels.
- Pre-shearing Unit: This section precisely cuts the leading edge of the metal sheet, guaranteeing clean and consistent starts for the forming process.
- Double Layer Roll Forming System: The heart of the machine, this system comprises two sets of forming rolls, each meticulously designed to shape one layer of the panel simultaneously. The upper and lower rolls work in perfect harmony, transforming the flat sheets into intricate profiles.
- Hydraulic Cutting Unit: With a powerful squeeze, this unit severs the formed double layer panel to the desired length, ensuring clean cuts and production efficiency.
- Run-out Table: The finished double layer panels gracefully glide onto this extended table for easy stacking, collection, and further processing.
- PLC Control System: The brain of the operation, the PLC (Programmable Logic Controller) meticulously regulates all aspects of the machine’s operation. From feeding speed and roll forming pressure to cutting length and automatic shut-off, the PLC ensures seamless production.
Additional Considerations:
- Material Thickness Capacity: Double layer panel making machines can handle a specific range of metal sheet thicknesses. Understanding your project requirements and choosing a machine compatible with your material is crucial.
- Panel Width Capacity: Similar to thickness, the machine will have a maximum width capacity for the double layer panels it can produce. Aligning this with your desired panel dimensions is essential.
- Roll Forming Stations: Some machines offer additional roll forming stations within each layer, enabling the creation of even more complex panel profiles.

the Double Layer Panel Making Process
Imagine a well-rehearsed orchestra, each instrument playing its part in creating a harmonious melody. The double layer panel making process is remarkably similar. Here’s a glimpse into the magic:
- The Curtain Rises: Feeding the Metal Beast The metal coil, secured on the uncoiler, unwinds with measured precision, guided by the leveling device to ensure a perfectly flat sheet.
- Setting the Stage: Pre-shearing for a Clean Start The pre-shearing unit takes center stage, delivering a clean cut at the leading edge of the metal sheet, guaranteeing a flawless beginning for the forming process.
- The Double Act: Simultaneous Shaping The metal sheet enters the double layer roll forming system, where the magic truly unfolds. The upper and lower sets of rolls, meticulously designed for your specific panel profile, simultaneously shape each layer. Imagine two sculptors working in perfect unison, transforming the flat sheet into a work of art.
- The Grand Finale: Cutting the Masterpiece The formed double layer panel reaches the hydraulic cutting unit, where a powerful and precise cut severs it to the desired length. Just like a conductor bringing the orchestra to a close, the cutting unit signifies the completion of a perfectly formed double layer panel.
- A Well-deserved Applause: The Run-out Table Awaits The finished double layer panel glides gracefully onto the run-out table, ready for stacking, collection, and further processing. It’s a moment of pride, a testament to the machine’s efficiency and the precision of the entire process.
Industrial Applications of Double Layer Panel Making Machine
The versatility of double layer panel making machines extends far beyond a single application. Here are some prominent industries that leverage this technology:
- Construction: Double layer panels are ideal for roofing, wall cladding, and interior partitions. Their inherent strength, achieved through the double layer structure, makes them perfect for withstanding harsh weather conditions and providing superior insulation.
- HVAC (Heating, Ventilation, and Air Conditioning): These machines can produce double layer panels specifically designed for air handling units. The double layer construction offers superior sound dampening and thermal insulation properties, crucial for efficient HVAC system operation.
- Transportation: The automotive and aerospace industries utilize double layer panels for components requiring a lightweight yet robust structure. The double layer configuration provides exceptional strength-to-weight ratios, making it ideal for applications where weight reduction is paramount.
- Appliance Manufacturing: Double layer panels offer excellent formability and aesthetic appeal, making them suitable for manufacturing appliance bodies, refrigerator panels, and washing machine exteriors.
-
দ্রাক্ষাক্ষেত্র পোস্ট রোল ফর্মিং মেশিন
-
স্বয়ংক্রিয় আকার পরিবর্তনযোগ্য সিগমা Purlin রোল ফর্মিং মেশিন
-
সি সেকশন ব্রেসিং ওমেগা স্টোরেজ র্যাক খাড়া পোস্ট রোল ফর্মিং মেশিন
-
স্টিল বক্স প্লেট মেকিং রোল ফর্মিং মেশিন
-
বক্স মরীচি স্টীল রোল শেল্ফ কলাম জন্য মেশিন গঠন
-
প্যালেট র্যাকিং স্টেপ বিম পি বিম রোল তৈরির মেশিন
-
গুদাম শেল্ফ খাড়া রোল গঠন মেশিন
-
বৈদ্যুতিক মন্ত্রিসভা ফ্রেম রোল গঠনের মেশিন
-
দিন রেল রোল ফর্মিং মেশিন
the Advantages of Double Layer Panel Making Machines
While production speed is a significant advantage, double layer panel making machines offer a plethora of benefits that elevate them beyond ordinary roll forming machines. Here’s a closer look:
- Enhanced Structural Integrity: The double layer configuration inherently provides superior strength and rigidity compared to single layer panels. This translates to panels that can withstand greater loads, making them ideal for demanding applications.
- Improved Thermal Insulation: The air gap trapped between the two layers acts as a natural thermal insulator. This translates to superior energy efficiency in buildings and HVAC systems, leading to potential cost savings on heating and cooling.
- Reduced Noise Transmission: Similar to thermal insulation, the double layer construction effectively dampens sound waves. This is particularly beneficial in applications where noise reduction is crucial, such as HVAC systems and wall partitions in buildings.
- Material Optimization: Double layer panels can achieve similar strength and rigidity to single layer panels using less material. This translates to cost savings on raw materials and potentially reduces the overall weight of the final product.
- Design Versatility: Double layer panel making machines offer the ability to create panels with complex profiles on both layers simultaneously. This opens doors for innovative and aesthetically pleasing designs in various industries.
Considerations of Double Layer Panel Making Machine
While double layer panel making machines offer a compelling array of advantages, it’s crucial to consider specific factors before making an investment. Here are some key points to ponder:
- Production Needs: Evaluate your current and projected production volume. Double layer machines excel in high-volume production scenarios where efficiency is paramount.
- Panel Specifications: Ensure the machine’s capabilities align with your desired panel profiles, dimensions, and material thickness requirements.
- Machine Footprint: These machines can have a significant footprint. Consider your available factory space and ensure proper installation and operation clearances.
- Operational Costs: While double layer machines offer long-term benefits, factor in the initial investment cost, maintenance requirements, and energy consumption.
- Return on Investment (ROI): Carefully analyze the projected increase in production efficiency and potential material savings to determine the machine’s payback period and overall ROI.
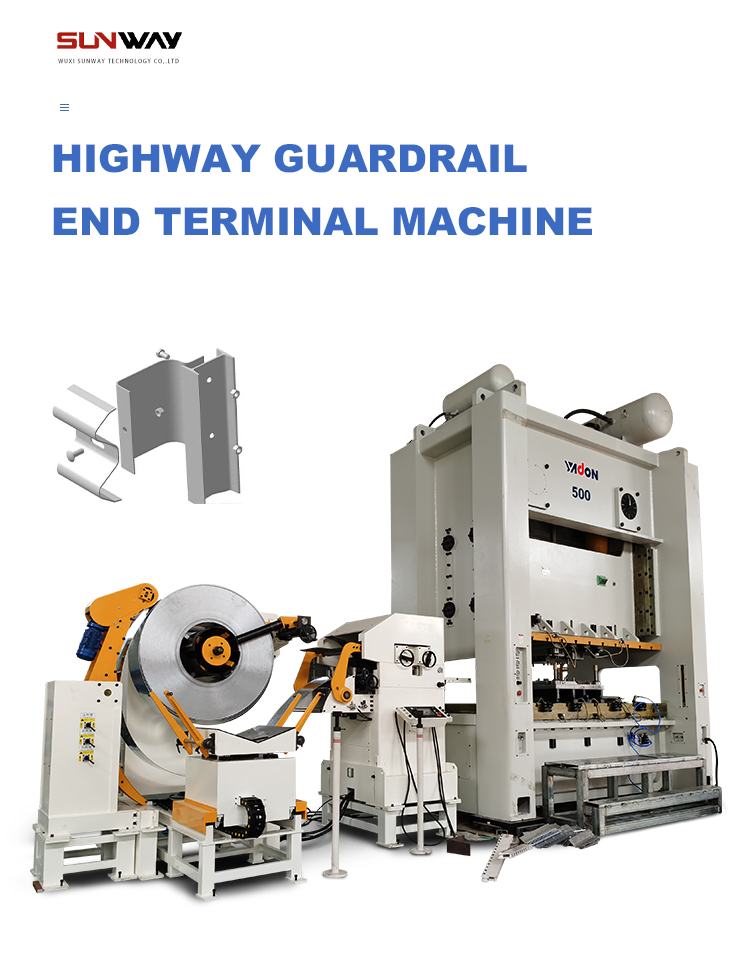
FAQ
Question | Answer |
---|---|
What are the typical materials used with double layer panel making machines? | Steel and aluminum are the most common materials used. However, some machines can handle other metals depending on the manufacturer’s specifications. |
Can double layer panel making machines handle pre-painted or coated metals? | Yes, many machines are compatible with pre-painted or pre-coated metals. However, it’s crucial to consult the manufacturer’ |
How complex can the panel profiles be? | The complexity depends on the machine’s capabilities. Some machines offer multiple roll forming stations within each layer, enabling intricate designs. |
Do double layer panel making machines require skilled operators? | While basic operation can be learned relatively quickly, in-depth knowledge of the machine and metal forming processes is beneficial for maximizing efficiency and maintaining optimal panel quality. |
What safety features are typically included in double layer panel making machines? | Standard safety features include emergency stop buttons, guards around pinch points, and light curtains to prevent operator accidents. |
By carefully considering these factors and consulting with reputable double layer panel making machine manufacturers, you can make an informed decision that empowers your business to achieve new levels of efficiency and innovation in metal sheet production.