Din rail making machines are specialized equipment used to automatically manufacture DIN standard rails for mounting industrial control equipment. This guide provides a comprehensive overview of din rail making machine technology.
How Does a Din Rail Making Machine Work?
Din rail production lines utilize a রোল গঠন process to transform strip steel coil into formed DIN rail pieces. The key aspects of the working process are:
- Uncoiling – Sheet steel coil is loaded onto an uncoiler which feeds the strip through the line
- Forming – The metal strip passes through a series of roller dies which progressively form it into the desired DIN rail shape through bending and folding
- Cutting – Formed rails are cut to specified lengths by a cutting machine
- Hole Punching – Mounting holes are punched in the rails as needed
- Marking – Printed markings and labels can be applied
- Packaging – An exit conveyor stacks and packages completed DIN rail pieces
Modern din rail lines include various inline processes like cleaning, straightening, degreasing along with automation features to enable high efficiency production.
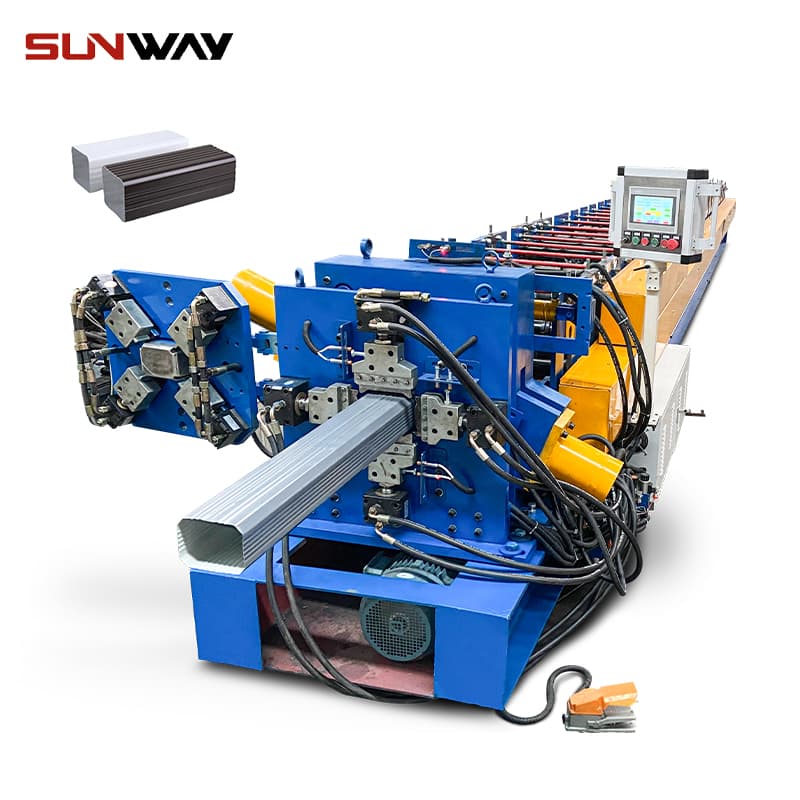
Types of Din Rail Making Machines
There are two primary types of din rail manufacturing equipment:
Machine Type | Description |
---|---|
Manual Lines | Basic machines with separate uncoiling, forming, cutting, and packaging units controlled individually. Lower output but flexible and economical. |
Automatic Lines | Fully integrated production lines with automated coil loading, forming, sensing, and packaging. Higher output rates but specialized for high volume manufacturing. |
Key Components of a Din Rail Production Line
The major components and modules in a DIN rail machine are:
- Uncoiler/Decoiler – Feeds strip steel coil stock
- Feeder/Straightener – Aligns strip stock and feeds into forming section
- Forming Stations – Progressive roller dies shape metal into rail form
- Cutting Machine – Shears formed rails to length
- Hole Punch – Punches mounting holes into rail pieces
- Inspection Unit – Checks quality standards of rails
- Printing/Marking – Applies logos, labels identification markings
- Packing Unit – Stacks and bundles output pieces
Programmable automation controllers allow monitoring and coordination of all line components.
Choosing a Din Rail Making Machine Supplier
When selecting a DIN rail production line, key factors to consider in suppliers are:
Parameter | Description |
---|---|
Production Output | Match line output to manufacturing scale (small, medium, large scale) |
Rail Specifications | Ensure machine can produce needed rail dimensions and hole patterns |
Customization Options | Availability of customized marking, sensing, automation features |
Quality Certification | ISO certified manufacturing processes for quality assurance |
Automation Level | Degree of manual versus automatic material handling and processes |
Aftersales Service | Installation support, operator training, maintenance and parts supply |
Pricing | Compare budget estimates across suppliers |
Leading global manufacturers of din rail making equipment include:
- Máquinas Ramirez
- Euromac
- EAE Tools
Reputable suppliers provide production guarantee and ensure dimensional accuracy of output rails.
-
স্বয়ংক্রিয় আকার পরিবর্তনযোগ্য সিগমা Purlin রোল ফর্মিং মেশিন
-
স্বয়ংক্রিয় আকার পরিবর্তনযোগ্য CZ Purlin রোল ফর্মিং মেশিন
-
স্বয়ংক্রিয় আকার পরিবর্তনযোগ্য Z Purlin রোল তৈরির মেশিন
-
Auto Size Changeable C U Purlin Roll Forming Machine
-
সি সেকশন ব্রেসিং ওমেগা স্টোরেজ র্যাক খাড়া পোস্ট রোল ফর্মিং মেশিন
-
স্টিল বক্স প্লেট মেকিং রোল ফর্মিং মেশিন
-
বক্স মরীচি স্টীল রোল শেল্ফ কলাম জন্য মেশিন গঠন
-
প্যালেট র্যাকিং স্টেপ বিম পি বিম রোল তৈরির মেশিন
-
গুদাম শেল্ফ খাড়া রোল গঠন মেশিন
Advantages of Automated Din Rail Production Lines
Modern high speed automated din rail making machines offer various benefits:
Higher Productivity
- Produce up to 120 m/min allowing large volume manufacturing
- Automated coil handling improves efficiency
Improved Consistency
- Programmable forming parameters ensures uniform rail geometry
- Automatic sensing checks quality standards
Flexible Production
- Quick roll die changeovers enables different rail types
- Simple size and length adjustments
Cost-Competitive
- Higher yields and lower labor due to automation
- Scales efficiently from small to large batch production
Overall, automated DIN rail lines enable efficient mass production while maintaining dimensional accuracy and customization flexibility.
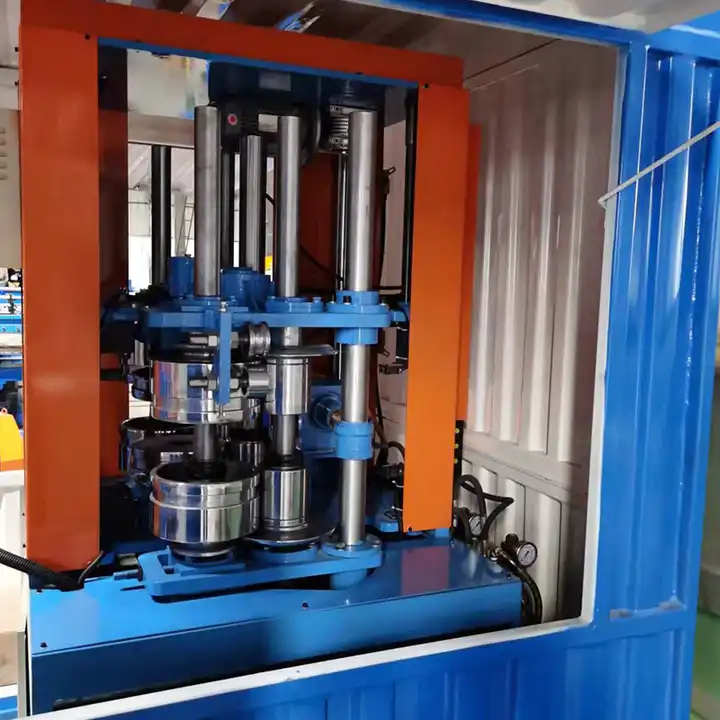
Industrial Applications of DIN Rail
DIN rail is a mounting system used to install industrial control equipment, power distribution, and automation components in factories, infrastructure facilities, commercial complexes and utilities.
Typical application areas include:
- Manufacturing Industries – Factory assembly lines, CNC machines, robotic arms
- Process Industries – Power plants, refineries, waste water facilities
- Commercial Buildings – Offices, malls, hospitals, data centers
- Infrastructure – Metro rail systems, airports, cellular base stations
All these industries utilize specialized control gear, circuit protection devices, connectivity hardware mounted on DIN rail for monitoring, operating and optimizing systems.
FAQs
Q: What materials can be used to manufacture DIN rails?
A: Cold rolled low carbon steel strips with galvanized or stainless steel variants are commonly used.
Q: What international quality standards are followed for din rails?
A: DIN EN 60715 and IEC 60715 standards specify mechanical and dimensional requirements.
Q: What are the key operation parameters to set in a DIN rail line?
A: Forming speed, steel strip feed length, shear cut length, hole punch spacing, and hole diameter are the primary parameters.
Q: How to maintain forming rollers and tooling in a din rail machine?
A: Regular cleaning and replacing worn forming rollers preserves dimensional accuracy of produced DIN rails. Lubricating rollers reduces friction and tool wear.