ক din rail forming machine is equipment used to roll metal strips or coils into various din rail profiles used for mounting circuit breakers and control equipment in control cabinets. This guide provides a comprehensive overview of din rail forming machine technology.
How Does a Din Rail Forming Machine Work?
A din rail forming machine works by feeding metal coil or strip stock through a series of roller dies that progressively form the stock into the desired din rail profile shape. The process involves unwinding coil stock, feeding through a straightener, then through the forming rollers, cutting to length, and final bending/punching operations.
The forming operation itself uses a series of roller dies that bend and form the strip stock incrementally into the din rail shape as it passes through. The key aspects of the working process include:
- Material Feeding: Coil stock is fed into the machine inlet, often using an uncoiler system with tension control
- Forming: Roller dies shape the strip through a series of bending/forming stations
- Cutting: A flying shear or rotary shear cuts formed rails to length
- Post-forming: End punching, bending, notching operations
- Collection: Formed din rail stock exits the other end for collection
Advanced machines allow for automated part sorting, counting, bundling as well. Microprocessor controls precisely coordinate the process for consistency.
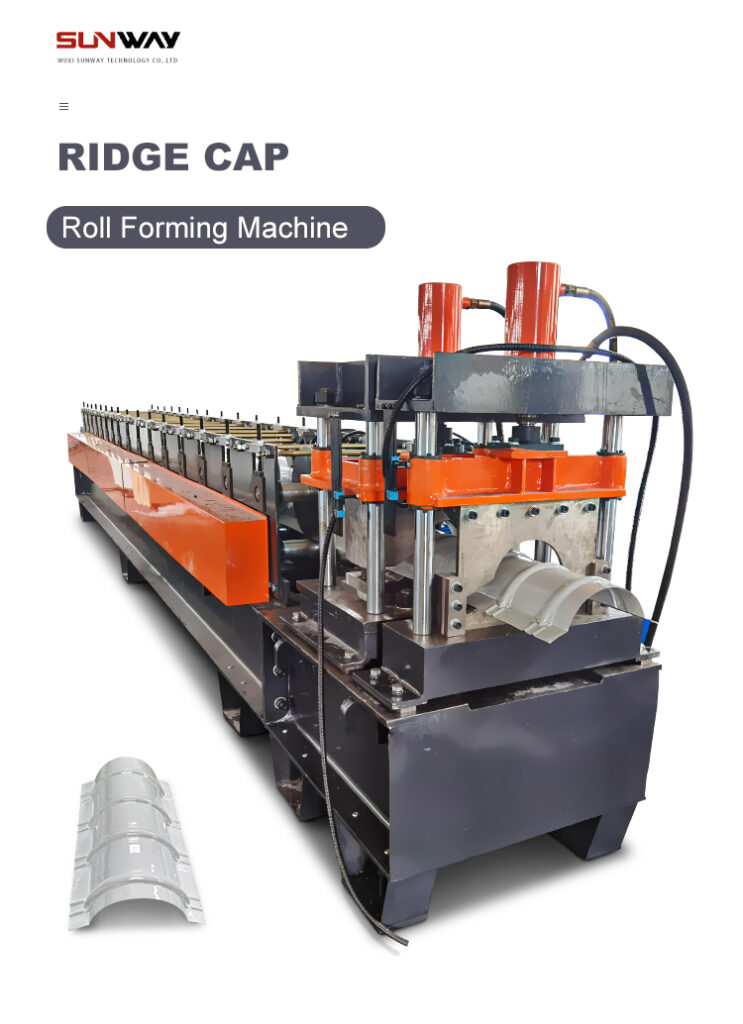
Types of Din Rail Forming Machines
There are two main types of din rail forming machines:
Type | Description |
---|---|
Manual | Basic machines for low volume production. Require manual adjustment of roller dies and settings |
Automatic | Advanced CNC-controlled machines for high volume production. Automated operation and quick die changeovers |
Key Features
Feature | Description |
---|---|
Forming stations | Number of progressive forming stations through which stock passes |
Automation level | Manual vs motorized operation and control |
Die change system | Manual or automatic die change trolleys for flexible profiles |
Production rate | Linear speed and hourly output rates |
Post-forming | Additional bending, punching, notching, counting capability |
Material capability | Thickness, width, material type (steel, stainless steel, etc) |
Control system | PLC, microprocessor, touchscreen, etc |
Din Rail Profile Design
There are many standard and custom din rail profiles that these machines can produce. Some common designs include:
- TS15
- TS32
- TS35 (EN 50 022)
- G Profile
- Top Hat Profile
- Custom shapes
Machines equipped with automated die change systems allow fast changeover between profiles. Custom profile design services are also offered by some manufacturers.
Choosing A Din Rail Forming Machine Supplier
When selecting a din rail forming machine, key factors to consider include:
Reputation & Experience
- Industry experience level
- R&D and manufacturing capabilities
- Past client feedback and satisfaction
Range of Equipment
- Breadth of machines and tooling for various profiles
- Customization available
- Production volume scalability
Service & Support
- Responsiveness to inquiries/requests
- Manuals, training, installation support offered
- Maintenance and parts availability
Costs
- Pricing models – upfront, leasing available
- Total cost of ownership
- Cost of spare parts, consumables
- Value compared to capabilities
Parameter | Importance |
---|---|
Brand reputation | High |
Technical expertise | High |
Equipment quality | High |
Customization capability | Medium |
After-sales service | High |
Delivery time | Medium |
Pricing | Medium |
-
দ্রাক্ষাক্ষেত্র পোস্ট রোল ফর্মিং মেশিন
-
স্বয়ংক্রিয় আকার পরিবর্তনযোগ্য সিগমা Purlin রোল ফর্মিং মেশিন
-
স্বয়ংক্রিয় আকার পরিবর্তনযোগ্য CZ Purlin রোল ফর্মিং মেশিন
-
স্বয়ংক্রিয় আকার পরিবর্তনযোগ্য Z Purlin রোল তৈরির মেশিন
-
Auto Size Changeable C U Purlin Roll Forming Machine
-
সি সেকশন ব্রেসিং ওমেগা স্টোরেজ র্যাক খাড়া পোস্ট রোল ফর্মিং মেশিন
-
স্টিল বক্স প্লেট মেকিং রোল ফর্মিং মেশিন
-
বক্স মরীচি স্টীল রোল শেল্ফ কলাম জন্য মেশিন গঠন
-
প্যালেট র্যাকিং স্টেপ বিম পি বিম রোল তৈরির মেশিন
Leading Din Rail Forming Machine Manufacturers
Some of the top global suppliers of din rail forming equipment include:
প্রতিষ্ঠান | Location |
---|---|
Transfluid Maschinenbau GmbH | Germany |
Techno Bright Engg | ভারত |
Ge Emme SRL | ইতালি |
স্যামকো মেশিনারি | China |
Feuer Powelectric | China |
Price ranges may start around $10,000 for basic manual machines ranging up to $100,000+ for fully automated CNC din rail forming lines. When requesting quotations, be sure to provide details on production volumes and specifics shapes/sizes required.
Operating Instructions
Proper operation and maintenance helps maximize uptime and performance. Follow manufacturer guidelines for:
- Machine setup and installation
- Parameter settings
- Daily/weekly maintenance checks
- Lubrication schedule
- Recommended spare parts
- Die setup and changeover
- Troubleshooting tips
- Operator training
Advantages of Din Rail Forming Machines
- High production volumes possible in automated lines
- Flexible equipment allows fast die changeovers
- Consistent quality compared to manual methods
- Reduced labor involvement frees up workforce
- Small footprint compared to press brakes
- Lower tooling costs than press brakes
- Safer operation compared to hydraulic presses
- User-friendly controls and diagnostics
Limitations of Din Rail Forming Machines
- Higher initial capital investment
- Complex programming/setup on advanced models
- Potential bottlenecks if capacity exceeded
- Dependent on material type/thickness
- Limited size range depending on tooling
- Not suited for low volume or prototype work
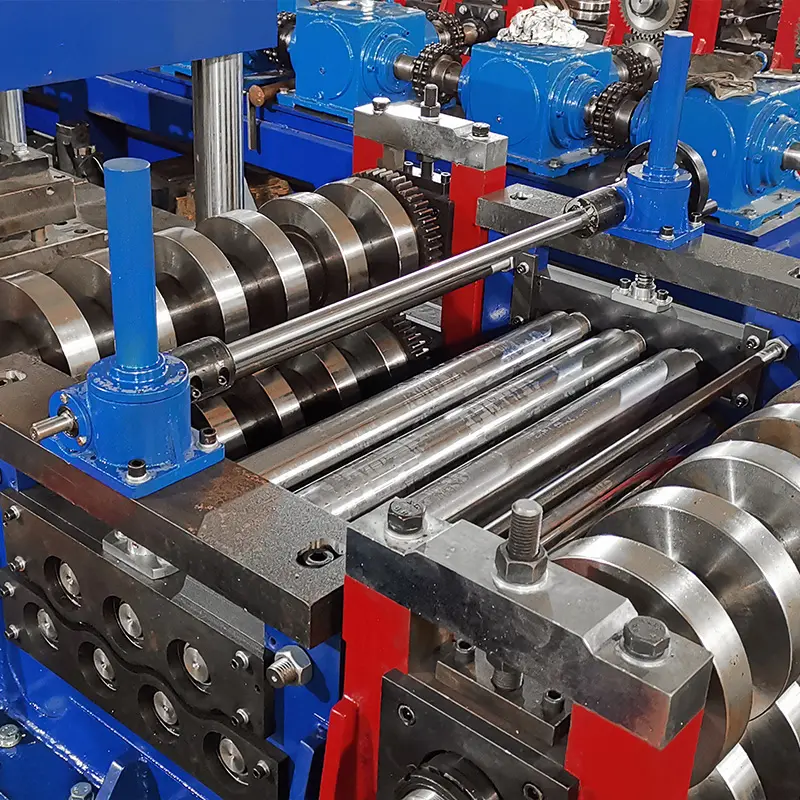
FAQ
Q: What materials can be formed on a din rail machine?
A: Most commonly steel and stainless steel strips/coils from 0.5mm to 3mm thickness. Some machines support thicker gauges up to 5mm as well.
Q: What production rates are possible?
A: Production rates vary widely but around 10-20 meters/minute is common. Larger automated lines with multiple forming heads can achieve over 50 meters/minute.
Q: Can custom and special profiles be produced?
A: Yes, custom profile tooling can be manufactured for most machines. Special profiles may require an engineered solution.
Q: What should I budget for a din rail forming system?
A: Budgets can range from around $10,000 for basic machines to over $100,000 for fully automated production lines. Discuss requirements with suppliers.
Q: What maintenance is required?
A: Daily inspections, scheduled lubrication, spare/wear parts (blades, rollers, bearings), and cleaning/adjustment as needed. Tooling must be changed over time.