Overview
Custom roll forming machines are a cornerstone of modern manufacturing, facilitating the production of continuous lengths of metal profiles with consistent cross-sections. These machines are integral in numerous industries, from construction to automotive manufacturing. This article will provide an in-depth look at custom roll forming machines, covering everything from their operation to specific models and their applications. We’ll dive into the mechanics, explore various models, and offer guidance on selecting the best machine for your needs. Let’s get rolling!
Guide to Roll Forming Machines
Roll forming is a process where a long strip of metal is continuously bent to form a desired cross-section. This technique is known for its efficiency and ability to produce uniform products with tight tolerances. Custom roll forming machines take this process a step further by allowing for the creation of specific profiles tailored to unique applications. These machines consist of several key components and operate through a systematic process.
Types of Custom Roll Forming Machines
Type | Description |
---|---|
Standard Roll Forming Machine | General-purpose machines used for creating basic metal profiles. |
High-Precision Roll Forming Machine | Machines designed for high-accuracy applications, often used in automotive and aerospace industries. |
Multi-Profile Roll Forming Machine | Capable of producing multiple profile types without the need for extensive retooling. |
Portable Roll Forming Machine | Compact machines that can be transported easily for on-site roll forming tasks. |
Heavy-Duty Roll Forming Machine | Built for handling thick, heavy gauge metals and high-strength steel. |
Servo-Driven Roll Forming Machine | Uses servo motors for precise control over the forming process, suitable for complex profiles and materials. |
Tandem Roll Forming Machine | Comprises multiple forming stations arranged in sequence to handle complex shapes and large production volumes. |
Customizable Roll Forming Machine | Tailored machines designed to meet specific customer requirements, allowing for unique profile production. |
Quick-Change Roll Forming Machine | Features rapid tooling change capabilities, reducing downtime and enhancing production flexibility. |
In-Line Roll Forming Machine | Integrated with other processes such as punching, welding, or cutting, enabling seamless, continuous production lines. |
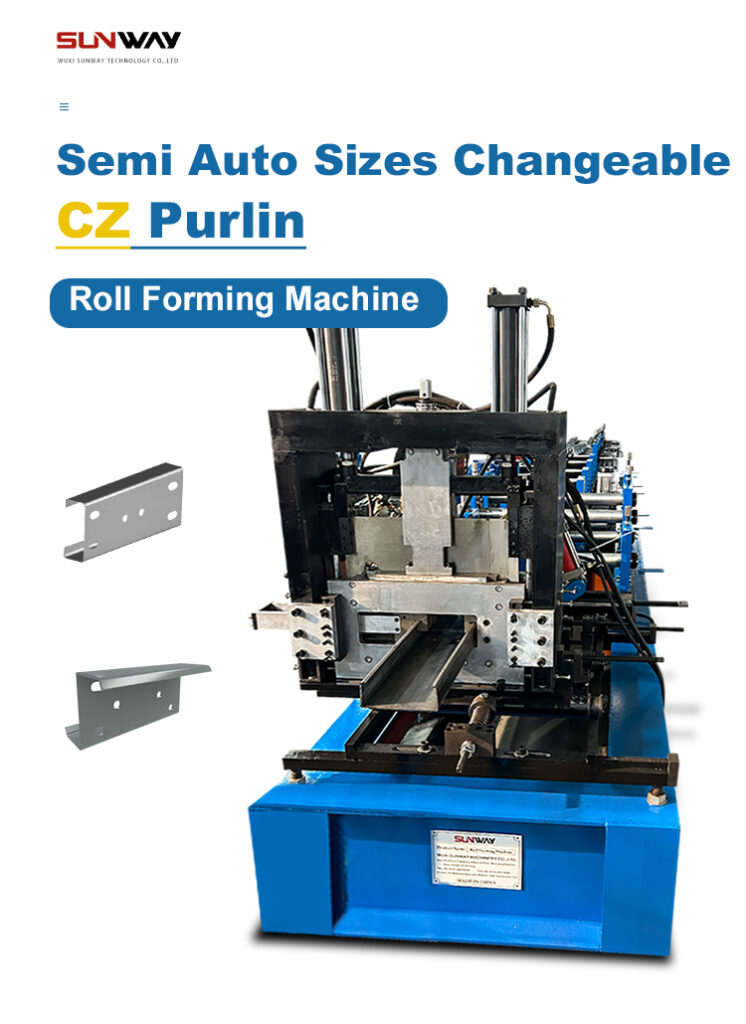
Working Process of Custom Roll Forming Machines
The working process of a custom roll forming machine involves several steps, each crucial for achieving the desired profile. Here’s a detailed look at each stage:
- Material Feeding: Metal coils are loaded onto a decoiler, which feeds the material into the roll forming machine.
- Leveling: The metal strip passes through a leveling unit to eliminate any initial imperfections and ensure uniform thickness.
- রোল গঠন: The core of the process where the metal strip is gradually shaped by a series of roll stations, each performing incremental bends.
- Cutting: Once the desired profile is achieved, the formed metal is cut to the required length using flying cut-off saws or hydraulic shears.
- Stacking/Packaging: The finished products are stacked and packaged for shipment or further processing.
Key Components and Their Functions
Component | Function |
---|---|
ডিকয়লার | Holds and unwinds the metal coil, feeding it into the machine. |
Leveling Unit | Straightens the metal strip and ensures consistent thickness. |
Roll Stations | Series of rollers that shape the metal strip through incremental bends. |
Cut-Off System | Cuts the formed metal to the required length. |
নিয়ন্ত্রণ ব্যবস্থা | Manages the machine operations, ensuring precision and consistency. |
Drive System | Powers the rollers and other moving parts of the machine. |
Safety Guards | Protects operators from moving parts and potential hazards. |
Hydraulic System | Provides the necessary force for cutting and other high-pressure tasks. |
Punching Unit (if applicable) | Punches holes or slots in the metal strip during the forming process. |
Stacking System | Automatically stacks the finished products for easy handling and packaging. |
Machine Speed and Efficiency
Parameter | Description |
---|---|
গঠন গতি | Typically ranges from 10 to 60 meters per minute, depending on the machine. |
Changeover Time | Time required to switch profiles or retool the machine, usually 10-30 minutes. |
Production Efficiency | Measured by the machine’s uptime and the quality of the output. |
Energy Consumption | Varies by machine type; energy-efficient models are available. |
-
Standing Seam Roof Panel Curving Machine
-
ব্যারেল ঢেউতোলা রোল ফর্মিং মেশিন
-
Highway Guardrail End Terminal Forming Machine
-
Highway U/C Post Roll Forming Machine
-
2 Waves Highway Guardrail Roll Forming Machine
-
3 Waves Highway Guardrail Roll Forming Machine
-
Stand Seaming Roof Panel Roll Forming Machine
-
ডাউনস্পাউট পাইপ রোল তৈরির মেশিন
-
গটার রোল তৈরির মেশিন
Customized Mechanical Parameters
Parameter | Range/Options |
---|---|
Material Thickness | 0.3mm to 12mm |
Profile Width | 10mm to 1500mm |
Number of Roll Stations | 6 to 30 stations |
Motor Power | 5kW to 100kW |
Machine Length | 5m to 30m |
Machine Weight | 2 tons to 30 tons |
Applications and Uses
Industry | অ্যাপ্লিকেশন |
---|---|
Construction | Roof panels, wall claddings, gutters, and structural components. |
Automotive | Bumpers, frames, door beams, and other structural parts. |
Aerospace | Lightweight, high-strength profiles for aircraft structures. |
Renewable Energy | Solar panel frames, wind turbine components. |
Furniture | Metal frames for office and home furniture. |
Electrical | Enclosures, cable trays, and support structures. |
Agriculture | Farm building structures, irrigation equipment. |
Transportation | Train and bus components, rail infrastructure. |
Heavy Machinery | Structural parts for construction and mining equipment. |
Consumer Goods | Shelving units, appliance components. |
Installation, Operation, and Maintenance
Aspect | বিস্তারিত |
---|---|
Installation | Typically involves professional setup, calibration, and initial testing by the manufacturer. |
Operation | Requires trained operators to handle material loading, machine settings, and monitoring. |
Maintenance | Regular maintenance includes lubrication, alignment checks, and part replacements to ensure longevity. |
Suppliers and Price Range
Supplier | Price Range (USD) |
---|---|
ABC Roll Forming | $50,000 – $200,000 |
XYZ Machinery | $70,000 – $250,000 |
RollTech Solutions | $60,000 – $300,000 |
FormMaster Inc. | $80,000 – $350,000 |
MetalForm Technologies | $90,000 – $400,000 |
Choosing the Right Supplier
When selecting a supplier for custom roll forming machines, consider the following factors:
Factor | Description |
---|---|
Quality and Reputation | Look for suppliers with a strong track record and positive customer reviews. |
Customization Options | Ensure the supplier can tailor the machine to your specific needs. |
Technical Support | Availability of comprehensive technical support and training. |
Price and Value | Compare prices relative to the features and benefits offered. |
Delivery Time | Consider the lead time for delivery and installation. |
After-Sales Service | Check for robust after-sales support, including maintenance and spare parts availability. |
Pros and Cons
Aspect | Advantages | Disadvantages |
---|---|---|
কাস্টমাইজেশন | Tailored to specific profiles and applications. | Higher initial cost compared to standard machines. |
Efficiency | High production speeds and consistent quality. | Requires skilled operators and regular maintenance. |
Versatility | Capable of producing a wide range of profiles. | Changeover time can impact productivity. |
Durability | Built to handle heavy-duty applications and materials. | Larger machines require significant space. |
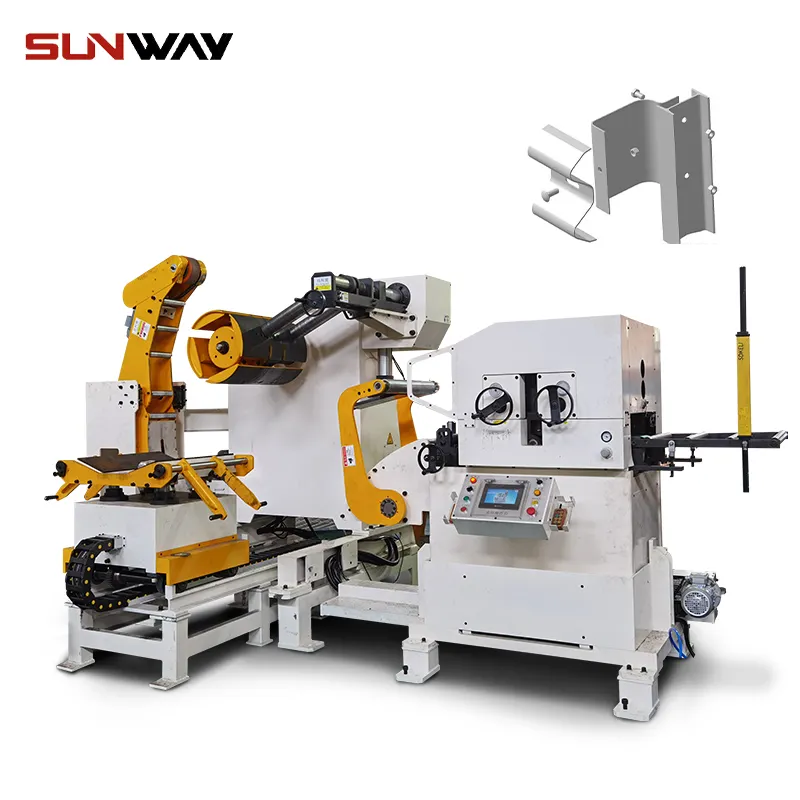
FAQ
Question | Answer |
---|---|
What materials can be processed with custom roll forming machines? | Various metals including steel, aluminum, copper, and more. |
How do I choose the right custom roll forming machine? | Consider your specific profile requirements, material type, production volume, and budget. |
What are the maintenance requirements? | Regular lubrication, alignment checks, and part replacements are essential for optimal performance. |
Can these machines be integrated with other manufacturing processes? | Yes, in-line roll forming machines can integrate processes like punching, welding, and cutting. |
What is the typical lead time for a custom roll forming machine? | Lead times vary but generally range from a few months to a year, depending on customization level. |
Are there portable roll forming machine options? | Yes, portable options are available for on-site forming tasks. |
How does the material thickness affect the machine selection? | Machines are designed to handle specific thickness ranges; ensure your machine matches your material specs. |