Corrugated steel panels have been a cornerstone of construction for over a century. From their structural integrity to their cost-effectiveness, they’ve found applications in everything from roofing and siding to fencing and even architectural design. But what makes corrugated steel panels so special? How do you choose the right one for your project? And what should you know about their installation and maintenance? In this in-depth guide, we’ll dive into the world of corrugated steel panels—exploring everything from their types, functions, and applications to technical specifications and the most popular models available.
Overview of Corrugated Steel Panels
Corrugated steel panels are metal sheets that have been pressed or rolled into a series of ridges and grooves to improve strength and flexibility. This unique profile gives them superior durability compared to flat sheets of metal, making them a preferred choice for construction, industrial applications, and even aesthetic uses in architectural projects.
Key Features of Corrugated Steel Panels:
- Durability: The corrugation process gives the steel panel additional structural integrity, making it highly resistant to damage from environmental factors like wind, rain, and snow.
- Versatility: Used for roofing, siding, fences, and more, these panels can be customized for various designs and functions.
- Cost-Efficiency: Compared to other construction materials, corrugated steel offers a highly economical option due to its long lifespan and low maintenance costs.
- Lightweight: Despite their strength, corrugated steel panels are lightweight, making them easy to transport and install.
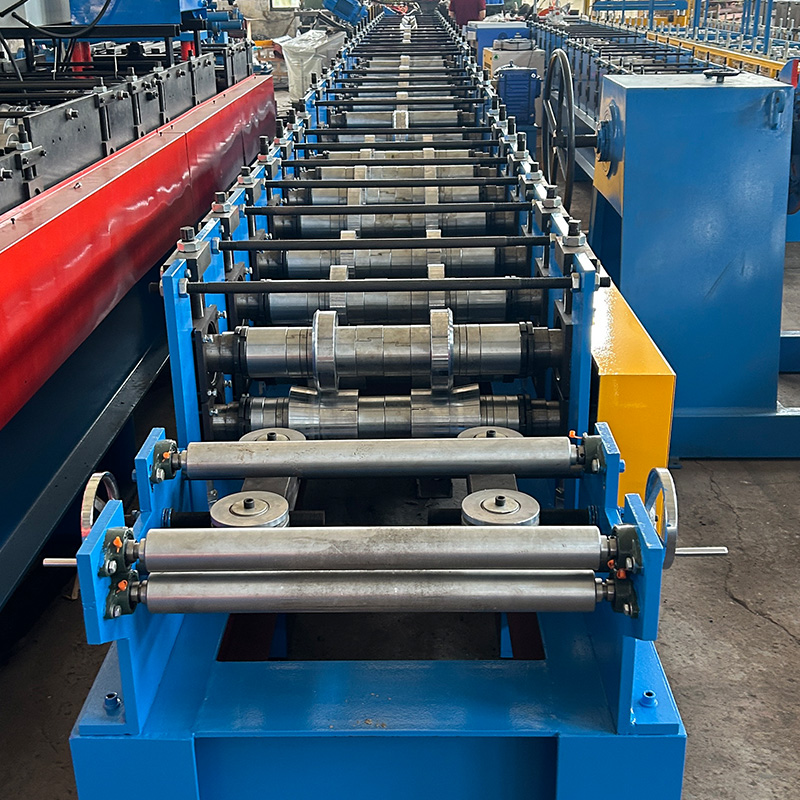
What Are Corrugated Steel Panels?
Corrugated steel panels are sheets of steel that are formed into wavy or ridged patterns using a cold-forming process. The ridges or “corrugations” add stiffness to the panel, increasing its load-bearing capabilities without significantly increasing weight. This combination of strength and low weight makes it ideal for a range of applications.
Historically, corrugated iron, the predecessor of corrugated steel, was first patented in the 1820s. Today, corrugated steel panels have evolved to include various materials, coatings, and profiles to suit modern engineering and architectural demands.
Types of Corrugated Steel Panels
Corrugated steel panels come in various types, each offering different features and benefits depending on the application. Let’s look at some popular types and models of corrugated steel panels, along with their descriptions:
Type of Corrugated Steel Panel | Description | Popular Metal Powder Model |
---|---|---|
Galvanized Corrugated Steel | Steel panels coated with a layer of zinc to prevent rust and corrosion, ideal for outdoor use. | G90 Zinc Coating |
Aluminum Corrugated Panels | Lightweight, corrosion-resistant, and often used in areas with high humidity or near saltwater. | 3003-H14 Aluminum Alloy |
Stainless Steel Corrugated Panels | Offers superior resistance to corrosion, making it ideal for industrial and marine applications. | 304 Stainless Steel |
Copper Corrugated Panels | Provides a distinctive aesthetic with natural patina over time; used in architectural applications. | C11000 Electrolytic Tough Pitch Copper |
Polycarbonate Steel Panels | Combines steel and polycarbonate for increased strength and translucency in applications like roofing. | PC400 Polycarbonate Alloy |
Cold Rolled Corrugated Steel | Enhanced structural strength and a smoother surface finish; used for roofing and cladding. | 1018 Carbon Steel |
Pre-Painted Corrugated Steel | Steel panels coated with paint for aesthetic purposes, available in a wide range of colors. | PVDF Coating with Colorbond® Technology |
Weathering Steel Corrugated Panels | Designed to form a protective rust layer over time, preventing further corrosion. | Corten A and B Steel |
Tin-Plated Corrugated Steel | Thin tin plating applied to steel for lightweight corrosion resistance, often used in packaging. | Tinplate ETP (Electrolytic Tinplate) |
Zinc-Aluminum Coated Steel Panels | High corrosion resistance with a combination of zinc and aluminum coatings. | AZ150 Zinc-Aluminum Alloy (Galvalume®) |
Function of Corrugated Steel Panels
Corrugated steel panels serve numerous functions depending on the application. Their structural profile allows them to bear heavier loads compared to flat sheets. Here’s a detailed look at how these panels function in different scenarios:
- Roofing: The wavy pattern of corrugated steel makes it highly effective at shedding water, which is why it’s a popular choice for roofing. It resists leaks better than flat panels, and the materials can withstand extreme weather conditions, including snow loads and high winds.
- Siding: Due to its strength, corrugated steel is often used as siding for commercial, industrial, and even residential buildings. It adds both a durable protective layer and a unique visual appeal.
- Fencing: The durability and aesthetic options make it a great choice for fencing. It’s strong enough to provide security, but lightweight enough for easier installation.
- Architectural Design: Architects often choose corrugated steel panels for their visual impact. The textured surface adds depth and dimension to modern building designs.
-
ক্যারেজ বোর্ড রোল ফর্মিং মেশিন
-
Highway Guardrail End Terminal Forming Machine
-
Highway U/C Post Roll Forming Machine
-
2 Waves Highway Guardrail Roll Forming Machine
-
3 Waves Highway Guardrail Roll Forming Machine
-
বৈদ্যুতিক মন্ত্রিসভা ফ্রেম রোল গঠনের মেশিন
-
দিন রেল রোল ফর্মিং মেশিন
-
দুই তরঙ্গ হাইওয়ে গার্ডেল মেশিন
-
থ্রি ওয়েভ হাইওয়ে গার্ডেল মেশিন
Working Process of Corrugated Steel Panels
The process of making corrugated steel panels involves several steps, with a focus on cold-forming to create the desired ridged patterns. Here’s a general breakdown of the process:
- Material Selection: High-quality steel is selected based on the specific properties needed for the panel, such as corrosion resistance or flexibility.
- Sheet Rolling: The steel sheet is rolled into the desired thickness before being processed.
- Corrugation: Using specialized machinery, the flat steel is fed into rollers that press the sheet into the iconic wavy pattern. This cold-forming process ensures that the steel retains its strength and shape.
- Cutting to Size: The corrugated steel sheets are then cut into the required lengths.
- Surface Treatment: Depending on the application, the steel may undergo galvanization, painting, or other surface treatments to improve its resistance to corrosion or to achieve a particular aesthetic.
Key Components and Their Function in Corrugated Steel Panels
Each corrugated steel panel is designed with certain components and materials that contribute to its overall performance. Here’s a look at the key components:
Component | Function |
---|---|
Steel Base | Provides the core strength and structure of the panel, which determines load-bearing capacity and flexibility. |
Corrugated Pattern | The ridges and grooves in the sheet increase its stiffness and strength, allowing it to bear greater loads. |
Zinc Coating (Galvanized) | A protective layer that helps prevent rust and corrosion, making the panel suitable for outdoor applications. |
Paint or Surface Coating | Adds an extra layer of protection and improves the panel’s appearance, available in different colors and finishes. |
Fasteners | Specialized screws or bolts used to attach the panels to the underlying structure, ensuring secure installation without damaging the metal. |
Flashings and Trim | Additional components used at the edges of the roof or wall to prevent water intrusion and give a finished appearance. |
Machine Speed and Efficiency of Corrugated Steel Panel Production
The production of corrugated steel panels involves high-speed machinery that ensures consistency and precision. Below is a breakdown of the machine speed and production efficiency:
Machine Type | Average Speed | Efficiency Rating |
---|---|---|
রোল ফর্মিং মেশিন | 15-20 meters per minute | High (Automated with low waste) |
Cutting Machine | 5-10 cuts per minute | High (Accurate precision) |
Coating Machine | 10-15 meters per minute | Moderate (Requires drying time) |
Customized Mechanical Parameters for Corrugated Steel Panels
Corrugated steel panels can be customized based on specific project requirements, such as thickness, width, and material. Here’s a table with some typical mechanical parameters that can be adjusted:
Parameter | Range |
---|---|
Panel Thickness | 0.4mm – 1.2mm |
Panel Width | 600mm – 1200mm |
Panel Length | Customizable (up to 12m) |
Coating Thickness (Zinc) | 40g/m² – 275g/m² |
Profile Height | 16mm – 45mm |
Ridge Spacing | 76mm – 150mm |
Applications and Uses of Corrugated Steel Panels
Corrugated steel panels have a wide range of uses, spanning both industrial and residential projects. Below are some of the most common applications:
Application Area | Description |
---|---|
Roofing | Provides durable, weather-resistant roofing solutions for homes, warehouses, and industrial buildings. |
Wall Cladding | Used as an exterior or interior wall covering, offering both protection and a modern aesthetic. |
Fencing | Popular for security and privacy fencing, especially in industrial areas. |
Agricultural Buildings | Used in barns, sheds, and stables due to their durability and low maintenance. |
Greenhouses | Polycarbonate steel panels are often used for greenhouses, combining light transmission and strength. |
Carports | Lightweight and durable, corrugated panels make excellent roofing for carports and sheds. |
Architectural Design | Frequently used in modern architecture for creating textured, visually striking surfaces. |
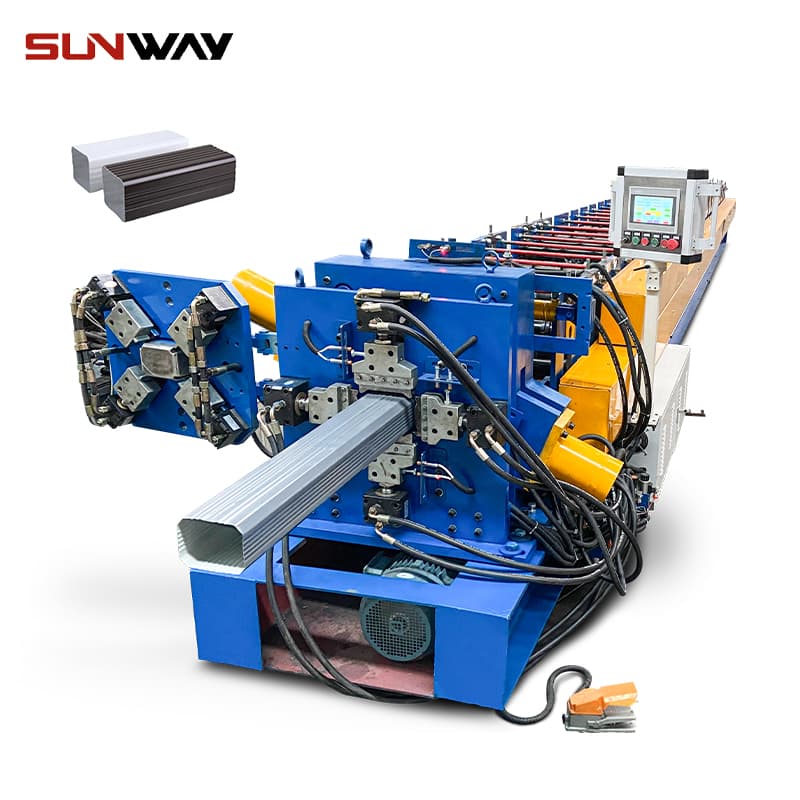
Installation, Operation, and Maintenance of Corrugated Steel Panels
Proper installation and maintenance of corrugated steel panels ensure their longevity and performance. Below is a summary of installation steps, operational tips, and maintenance requirements:
Installation | Operation | Maintenance |
---|---|---|
Panels are attached using fasteners that penetrate both the panel and the underlying frame or purlins. | Ensure proper overlap between panels to prevent water intrusion. | Inspect panels regularly for signs of rust or corrosion, especially in coastal environments. |
Use of appropriate flashing and trim at edges and seams is essential to waterproof the structure. | Panels should be installed in a way that allows for thermal expansion and contraction. | Reapply protective coatings (paint or sealants) as needed to maintain corrosion resistance. |
Always follow manufacturer guidelines for screw placement and sealing. | Avoid over-tightening fasteners, which could warp the panels. | Clean panels periodically to remove debris, dirt, and potential sources of corrosion. |
Suppliers and Price Range of Corrugated Steel Panels
Corrugated steel panels can vary significantly in price depending on the material, coating, and customization. Below is a general overview of the price range and some popular suppliers:
Supplier | Price Range (Per Sq. Ft.) | Specialties |
---|---|---|
ABC Metal Roofing | $1.50 – $3.00 | Offers galvanized and pre-painted steel panels. |
Bridger Steel | $2.00 – $5.00 | Custom metal panels in various profiles, including rustic and modern styles. |
Mueller, Inc. | $1.80 – $4.50 | Specializes in both commercial and residential metal roofing solutions. |
Metal Sales Manufacturing | $1.60 – $4.00 | Provides high-quality metal panels with numerous coating and color options. |
Metal Roofing Supply | $1.70 – $3.80 | Focuses on fast delivery and custom panel sizes. |
How to Choose the Right Supplier for Corrugated Steel Panels
Selecting the right supplier for your corrugated steel panels involves considering several factors such as product quality, customer service, and delivery options. Here’s a checklist to guide you:
- Product Range: Does the supplier offer the specific type of panel you need? Look for options like galvanized, pre-painted, or stainless steel.
- Customizability: If your project requires non-standard sizes or coatings, choose a supplier that can accommodate these needs.
- Reputation: Check online reviews, ask for references, or look for industry certifications to ensure the supplier is reliable.
- Lead Time: Can the supplier meet your project deadline? Make sure they can deliver the products on time.
- Cost: Price should be competitive, but also consider the long-term value of the product.
Advantages and Disadvantages of Corrugated Steel Panels
Corrugated steel panels are known for their durability and versatility, but they do come with both pros and cons. Here’s a comparison:
Advantages | Disadvantages |
---|---|
Durability: Highly resistant to weather and wear. | Corrosion Risk: Without proper treatment, steel can rust, especially in harsh environments. |
খরচ-কার্যকর: Long lifespan with minimal maintenance. | Noise: May be noisy during rain or hail without proper insulation. |
Lightweight: Easy to install, reducing labor costs. | Aesthetic Limitations: Some may find the industrial look unappealing for residential use. |
পরিবেশগত ভাবে নিরাপদ: Often made from recyclable materials. | Heat Retention: Steel can become hot in direct sunlight, increasing cooling costs. |
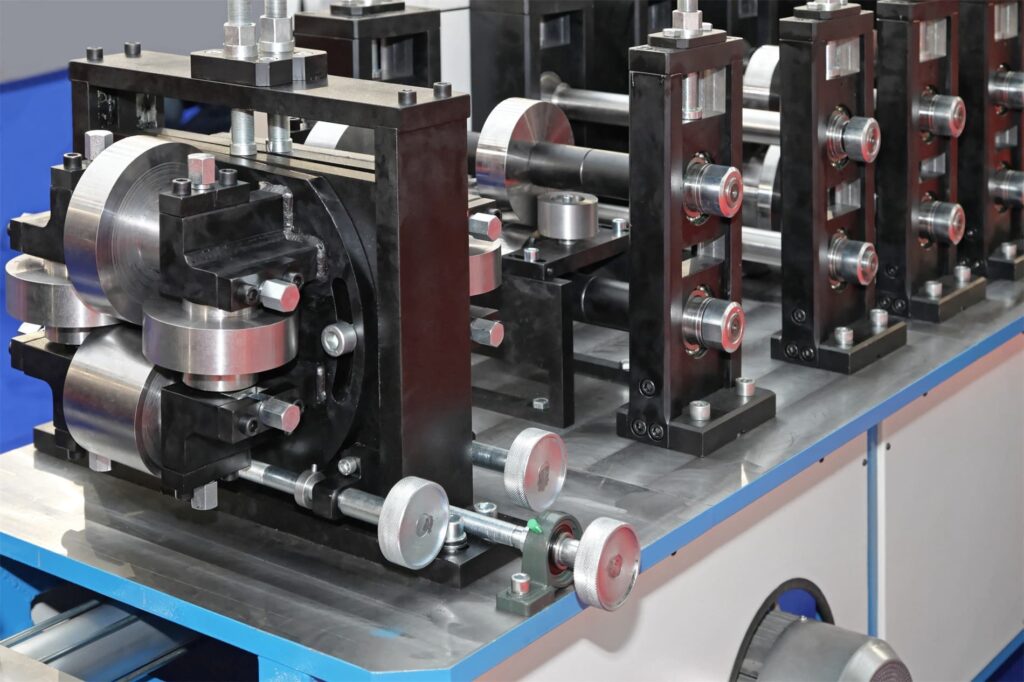
FAQ
Question | Answer |
---|---|
What is the lifespan of corrugated steel panels? | Corrugated steel panels can last between 40 to 70 years, depending on the material, coating, and environmental conditions. |
Can corrugated steel panels be painted? | Yes, many corrugated steel panels are available pre-painted, but you can also paint them yourself using appropriate paint designed for metal surfaces. |
Are corrugated steel panels suitable for DIY projects? | Yes, with the right tools and some basic knowledge, corrugated steel panels can be installed as a DIY project, particularly for roofing or siding. |
How do you prevent rust on corrugated steel panels? | Regular maintenance, such as cleaning and applying protective coatings, can help prevent rust. Galvanized and coated panels are also rust-resistant. |
What thickness should I choose for corrugated steel panels? | The thickness depends on your application, but generally, thicker panels (around 0.7mm to 1.2mm) are used for roofing, while thinner panels can be used for siding. |
উপসংহার
Corrugated steel panels are a versatile and durable choice for a wide variety of construction projects. Whether you’re looking to roof a home, build a fence, or design an architectural masterpiece, these panels provide both functional and aesthetic benefits. By understanding the different types, functions, and key specifications, you can choose the right corrugated steel panels for your project with confidence.