In the realm of modern construction and architecture, innovation continues to reshape the landscape of roofing materials and techniques. One notable innovation that has gained remarkable traction is the corrugated roof panel roll forming machine. This marvel of engineering has revolutionized the roofing industry, streamlining the production of corrugated metal sheets that are widely used for roofing and cladding purposes.
ভূমিকা
Corrugated roof panels have been a staple in construction for their durability, weather resistance, and aesthetic appeal. However, the traditional manufacturing process was labor-intensive and time-consuming, hampering the overall efficiency of roofing projects. The advent of corrugated roof panel roll forming machines has addressed these challenges, making the manufacturing process faster, more precise, and cost-effective.
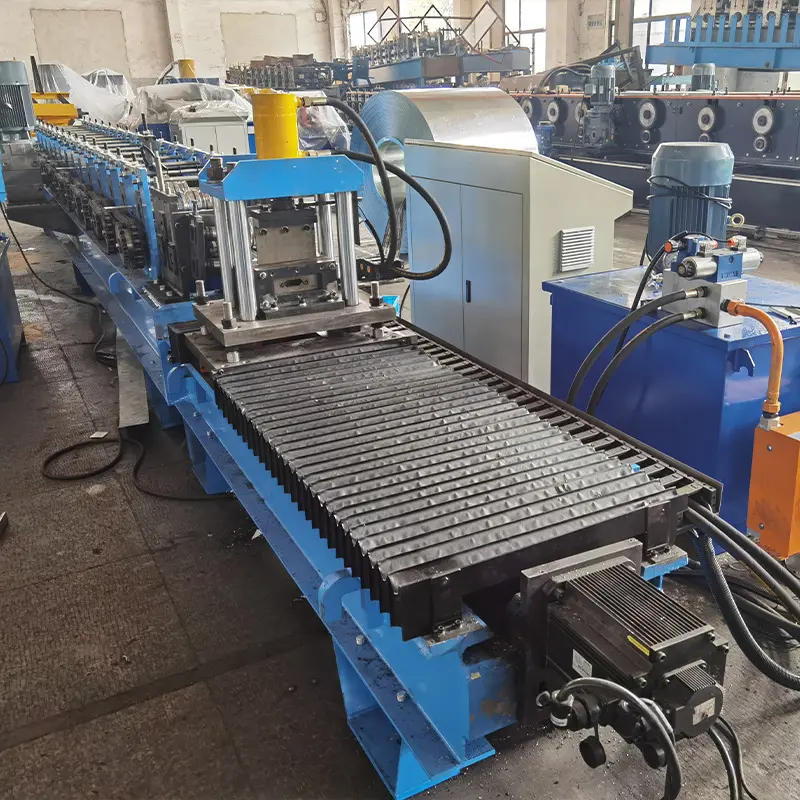
Understanding Corrugated Roof Panel Roll Forming
Corrugated roof panel roll forming is a manufacturing process that involves feeding metal coils through a series of roller dies to gradually shape them into corrugated profiles. This process is automated, precise, and highly efficient. The machine’s design allows for consistent corrugation patterns, ensuring uniformity across the produced panels.
Benefits of Using Corrugated Roof Panel Roll Forming Machines
The shift towards using corrugated roof panel roll forming machines has brought forth a multitude of benefits for the roofing industry:
- Enhanced Efficiency: Traditional methods required multiple steps and considerable time, whereas roll forming machines can produce panels in a single continuous process.
- Cost Savings: Reduced labor requirements and increased production speed lead to significant cost savings for manufacturers and consumers.
- Customization: Modern machines can be adjusted to create various corrugation profiles, catering to different architectural and design needs.
- Material Preservation: The gentle shaping process of roll forming prevents material damage, preserving the structural integrity of the metal.
- Speed and Precision: Roll forming machines can produce large quantities of panels with high precision, ensuring consistent quality.
Key Features to Look for in a Corrugated Roof Panel Roll Forming Machine
When investing in a corrugated roof panel roll forming machine, certain features are essential to consider:
- Material Compatibility: Ensure the machine is capable of handling the specific metal or alloy you intend to use for your panels.
- Roller Design: The quality and design of the rollers will directly impact the accuracy and consistency of the corrugation.
- Automation Level: Opt for machines with advanced automation features for seamless operation and reduced manual intervention.
- Customization Options: Look for machines that allow easy adjustment of corrugation profiles and panel dimensions.
- Durability: Invest in a machine built with robust materials to withstand the demands of continuous operation.
Choosing the Right Corrugated Roof Panel Roll Forming Machine for Your Needs
Selecting the appropriate machine involves assessing your production requirements, budget constraints, and the specific features offered by different manufacturers. Conduct thorough research, read reviews, and if possible, request demonstrations to make an informed decision.
Step-by-Step Guide to Operating a Corrugated Roof Panel Roll Forming Machine
Operating a corrugated roof panel roll forming machine requires a systematic approach:
- Preparation: Set up the machine, ensuring proper alignment and material placement.
- Material Loading: Feed the metal coil into the machine, securing the ends properly.
- Adjustments: Configure the machine settings according to the desired corrugation profile and panel dimensions.
- Initiate Operation: Start the machine and monitor the initial panels to ensure they meet quality standards.
- Continuous Monitoring: Regularly inspect panels for any defects or deviations from the desired specifications.
- Collection and Stacking: As panels are produced, ensure they are collected and stacked carefully to prevent damage.
Maintenance and Care Tips for Longevity
To ensure the longevity and consistent performance of your corrugated roof panel roll forming machine:
- Regular Lubrication: Keep all moving parts adequately lubricated to prevent friction-related issues.
- Routine Inspections: Regularly inspect rollers, belts, and other components for signs of wear or damage.
- Cleaning: Keep the machine clean from debris, dust, and metal shavings that could affect its operation.
- Scheduled Maintenance: Adhere to the manufacturer’s recommended maintenance schedule for optimal performance.
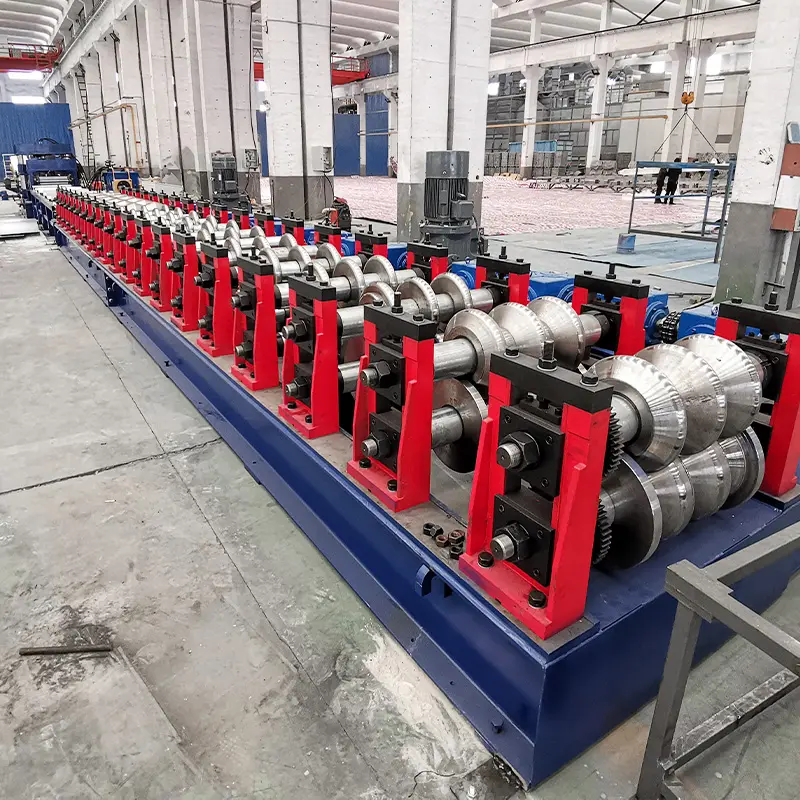
Safety Precautions When Using a Corrugated Roof Panel Roll Forming Machine
Prioritize safety when operating the machine:
- Training: Ensure operators are trained in machine operation, maintenance, and safety protocols.
- Protective Gear: Provide operators with appropriate personal protective equipment, including gloves, goggles, and ear protection.
- Emergency Stop: The machine should be equipped with an easily accessible emergency stop button.
- Proper Ventilation: If the machine produces fumes or heat, ensure the workspace is well-ventilated.
Future Trends in Corrugated Roof Panel Manufacturing
The future of corrugated roof panel manufacturing is poised for more technological advancements. Anticipate:
- Smart Automation: Integration of AI and IoT for real-time monitoring and predictive maintenance.
- Sustainable Practices: Emphasis on eco-friendly materials and energy-efficient production processes.
- Advanced Materials: Exploration of new materials with enhanced durability and performance characteristics.
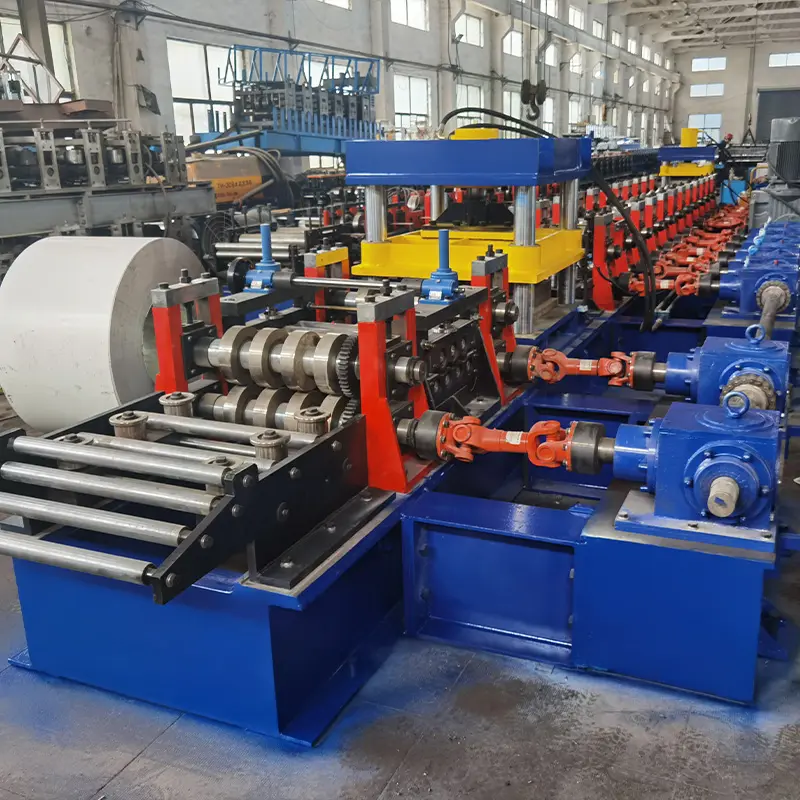
উপসংহার
The corrugated roof panel roll forming machine has undeniably transformed the roofing industry. Its efficiency, precision, and cost-effectiveness make it a cornerstone of modern construction. As technology advances, we can expect even more innovative strides in corrugated roof panel manufacturing, pushing the boundaries of what’s possible in roofing solutions.
FAQs
- What materials can be used with a corrugated roof panel roll forming machine?
- These machines can work with various metals, including steel, aluminum, and copper.
- Can I create custom corrugation profiles for unique designs?
- Yes, modern machines allow for easy customization of corrugation patterns to suit different design preferences.
- Are there safety considerations when operating these machines?
- Absolutely, operators should be trained, wear protective gear, and follow safety protocols to prevent accidents.
- How do I choose the right machine for my production needs?
- Evaluate your production requirements, budget, and the features offered by different machines before making a decision.
- What does the future hold for corrugated roofing technology?
- The future will likely bring more automation, sustainable practices, and the exploration of advanced materials for better roofing solutions.