Corrugated galvanised sheets are everywhere—from roofing to siding and even industrial applications. But what makes these sheets so special? Why are they preferred for so many projects, big and small? This guide is here to answer all your questions and more, diving deep into the technical aspects, types, processes, and best practices for using corrugated galvanised sheets. We’ll take you on a journey that explains everything you need to know about this versatile material, including how to select the right sheets for your project and even what to look for when choosing suppliers.
Overview of Corrugated Galvanised Sheets
Corrugated galvanised sheets are metal sheets that have been coated with zinc to prevent rust and corrosion, while the corrugation adds structural strength. These sheets are commonly used in construction, agriculture, and industrial projects due to their durability, resistance to weather conditions, and affordability. Their design also makes them excellent for draining water, making them a popular choice for roofing. But they aren’t just for roofing; they’re also used in fencing, sheds, and even artistic projects.
At its core, galvanisation is a process that involves applying a protective zinc coating to steel or iron to prevent rusting. This process creates a barrier between the metal and the environment, making it resistant to moisture and chemicals. When this is combined with the corrugated design—those signature wavy ridges—you get a material that’s both lightweight and incredibly strong.
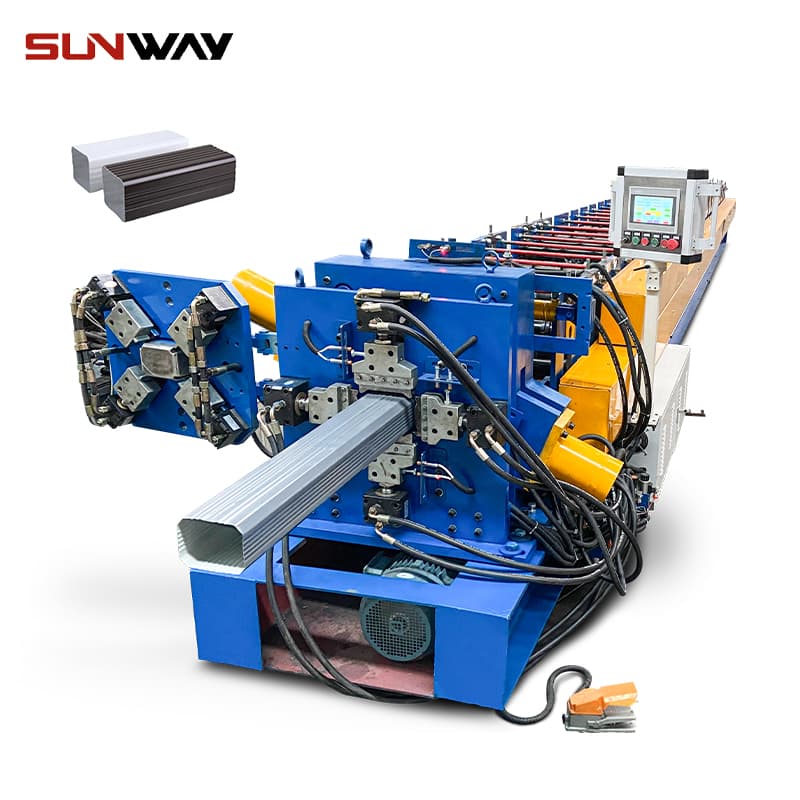
The Ultimate Guide to Corrugated Iron Sheets
Corrugated iron sheets are a staple in construction. The combination of zinc coating and corrugation means that the sheets can withstand harsh weather while remaining lightweight and easy to work with. Here’s what you need to know about these iron sheets:
- Material Composition: Made primarily from steel, these sheets undergo a galvanisation process where they are coated with zinc to prevent corrosion.
- Corrugation Process: The ridges you see on the sheets aren’t just for aesthetics. Corrugation increases the sheet’s bending strength, allowing it to span greater distances between supports.
- Zinc Coating: The zinc acts as a barrier between the steel and environmental factors like moisture and salt, which would otherwise cause the steel to rust.
Key Features of Corrugated Galvanised Sheets
- Durability: Thanks to the galvanisation process, these sheets are resistant to rust and corrosion.
- Lightweight: Despite their strength, corrugated galvanised sheets are relatively light, making them easy to transport and install.
- Cost-effective: As a long-lasting material, these sheets are a budget-friendly option for large-scale projects.
- Weather-resistant: Galvanised steel can withstand harsh conditions, including heavy rains, wind, and sun exposure.
Types of Corrugated Galvanised Sheets
There are multiple types of corrugated galvanised sheets available on the market, each with specific uses and benefits. Let’s break down the different models so you can find what’s right for your project.
Type | Description | Best Uses |
---|---|---|
CGI (Corrugated Galvanised Iron) Sheets | Standard corrugated sheets with traditional zinc coating. | Roofing, fencing, general construction |
Pre-painted Galvanised Sheets | Sheets are coated with paint for enhanced aesthetics and an extra layer of protection against corrosion. | Architectural projects, decorative applications |
Polyester Coated Sheets | Galvanised sheets with a polyester topcoat. More resistant to scratches and damage compared to standard CGI sheets. | Commercial and industrial buildings |
PVC Plastisol Coated Sheets | Galvanised sheets with a plastic coating for additional weatherproofing. Durable and comes in various colors. | Harsh environments, industrial buildings, garages |
Bitumen Coated Sheets | Sheets with a bitumen coating for sound insulation and improved waterproofing. | Soundproofing applications, industrial buildings |
Aluminium Corrugated Sheets | Lightweight alternative to galvanised steel. Resistant to corrosion but less strong than steel. | Low-load structures, coastal environments |
Zincalume Corrugated Sheets | Made from zinc and aluminium alloy, offering greater durability and corrosion resistance compared to traditional CGI sheets. | Roofing, high-performance cladding |
Fibre Reinforced Corrugated Sheets | Corrugated sheets that incorporate fibreglass for enhanced strength and flexibility. | Structural applications requiring lightweight and durable material |
Galvalume Sheets | Advanced version with aluminium, silicon, and zinc coating. More resistant to corrosion compared to standard galvanised sheets. | Industrial roofing and cladding |
Powder-coated Galvanised Sheets | High-end sheets with powder coating for an extra layer of durability and corrosion resistance. | High-end architectural projects, modern construction |
Each type of corrugated sheet offers distinct advantages depending on the needs of your project. Whether you’re looking for something lightweight like aluminium or something more durable for industrial use like Galvalume, there’s a sheet tailored to your specifications.
How Corrugated Galvanised Sheets are Made
The process of making corrugated galvanised sheets is quite intricate, involving several steps that ensure both durability and versatility. Let’s break down the production process:
Step 1: Steel Sheet Formation
Initially, flat sheets of steel are created by rolling steel at a mill. These flat steel sheets will later be processed to form corrugated patterns.
Step 2: Galvanisation Process
The steel sheets undergo a galvanisation process, where they are dipped into molten zinc. This process provides a protective zinc coating that helps to prevent rust and extends the life of the sheet.
Step 3: Corrugation
After the galvanisation process, the flat steel sheets are sent through a machine that forms the corrugated pattern. The ridges in the sheets increase the material’s strength and allow it to withstand greater forces, making it ideal for use in roofing and other applications where structural integrity is important.
Step 4: Cutting and Shaping
Once the sheets are corrugated, they are cut to the desired size. The edges are sometimes finished to remove any sharpness, ensuring that the sheets are safe to handle during installation.
Step 5: Coating and Painting (Optional)
In some cases, the sheets are coated with additional materials such as paint or plastic coatings to provide extra protection and aesthetics. This step is optional depending on the type of sheet being produced.
-
ক্যারেজ বোর্ড রোল ফর্মিং মেশিন
-
Highway Guardrail End Terminal Forming Machine
-
Highway U/C Post Roll Forming Machine
-
2 Waves Highway Guardrail Roll Forming Machine
-
3 Waves Highway Guardrail Roll Forming Machine
-
সি সেকশন ব্রেসিং ওমেগা স্টোরেজ র্যাক খাড়া পোস্ট রোল ফর্মিং মেশিন
-
স্টিল বক্স প্লেট মেকিং রোল ফর্মিং মেশিন
-
বক্স মরীচি স্টীল রোল শেল্ফ কলাম জন্য মেশিন গঠন
-
প্যালেট র্যাকিং স্টেপ বিম পি বিম রোল তৈরির মেশিন
Key Components of Corrugated Galvanised Sheets
Corrugated galvanised sheets are made up of several critical components that give them their unique properties:
Component | Function |
---|---|
Steel Core | The base material providing strength and flexibility to the sheet. |
Zinc Coating | Protects the steel from rusting by acting as a barrier between the steel and environmental factors. |
Corrugation | Adds structural strength to the sheet, allowing it to span greater distances without support. |
Additional Coatings (Optional) | Extra coatings, like polyester or plastisol, add durability and can enhance resistance to weather and chemicals. |
These components work together to provide the sheet with its durability, weather resistance, and strength, making it a popular choice for a wide range of applications.
Understanding Machine Speed and Efficiency for Corrugated Sheets
When producing corrugated galvanised sheets, the speed and efficiency of the machinery are critical factors that can affect production costs and the final quality of the sheets. Here’s a breakdown of typical machine parameters:
Machine Parameter | Range |
---|---|
Speed | 15 – 60 meters per minute |
Sheet Thickness | 0.14 mm – 1.2 mm |
Corrugation Depth | 10 mm – 25 mm |
Power Requirement | 5 KW – 10 KW |
Efficiency | 85% – 95% (depending on the type of machine and operator skill) |
Customized Mechanical Parameters for Specific Needs
If you need corrugated sheets for specific requirements, there’s room for customization:
Custom Parameter | Adjustable Range |
---|---|
Sheet Length | Customizable from 1 meter to 12 meters |
Corrugation Profile | Various designs available, including wave, trapezoidal, and sinusoidal patterns |
Coating Thickness | Zinc coating from 120 GSM (grams per square meter) to 500 GSM for added durability |
Color Coating | Available in multiple RAL colors for aesthetic appeal |
Surface Finish | Matte, gloss, or textured finishes can be applied depending on the project |
Applications and Uses of Corrugated Galvanised Sheets
Corrugated galvanised sheets are used across various sectors, thanks to their strength, weather resistance, and versatility. Let’s take a look at where these sheets are commonly employed:
আবেদন | Use Case |
---|---|
Roofing | Industrial buildings, agricultural barns, residential homes, commercial spaces |
Fencing | Perimeter walls, privacy barriers, and security fencing |
Cladding | Exterior walls for commercial buildings, warehouses, and manufacturing facilities |
Agricultural Structures | Animal shelters, greenhouses, and storage sheds |
Water Storage Tanks | Corrosion-resistant tanks for water storage in rural or remote areas |
Garages and Workshops | Lightweight and durable material for garage construction |
Decorative Use | Used in modern architecture for aesthetic appeal and texture in design |
Installation, Operation, and Maintenance of Corrugated Galvanised Sheets
Proper installation, operation, and maintenance are key to ensuring the longevity and performance of corrugated galvanised sheets. Here’s what you need to know:
Aspect | Best Practice |
---|---|
Installation | Secure sheets using appropriate fasteners, maintain proper overlap (around 150 mm) to ensure waterproofing. |
Operation | Avoid walking directly on the sheets, use planks to distribute weight evenly during maintenance or installation. |
Maintenance | Inspect sheets periodically for signs of corrosion, repaint or coat areas where the zinc layer has worn thin. |
Supplier Selection and Price Range for Corrugated Galvanised Sheets
Finding the right supplier is crucial for getting high-quality sheets at a reasonable price. Here are some factors to consider:
Supplier | Price Range per Sheet (USD) |
---|---|
Local Steel Mills | $8 – $20 |
International Suppliers | $12 – $25 (depending on shipping and customisation options) |
Online Retailers | $10 – $22 |
Bulk Distributors | $7 – $18 (price reduction for bulk orders) |
How to Choose the Right Supplier for Corrugated Galvanised Sheets
Choosing a supplier can feel overwhelming, but here’s a quick breakdown of what to look for:
- Reputation: Check reviews and testimonials to ensure that the supplier is reliable.
- Product Variety: Look for suppliers that offer a wide range of corrugated sheet types and customization options.
- Delivery Times: Timely delivery is crucial for keeping your project on schedule.
- Price: Compare prices, but don’t sacrifice quality for a lower cost—cheap sheets may cost more in repairs or replacements down the line.
- After-Sales Service: Ensure that the supplier offers customer support and has a clear returns or warranty policy.
Pros and Cons of Corrugated Galvanised Sheets
Here’s a comparison of the advantages and limitations:
Pros | Cons |
---|---|
Durable and Weather-Resistant | May require additional coating in harsh environments |
Lightweight and Easy to Install | Can be noisy during rain or hail |
খরচ-কার্যকর | Zinc coating can wear off over time if not maintained properly |
Versatile Applications | Some types may not offer as much insulation as required in colder climates |
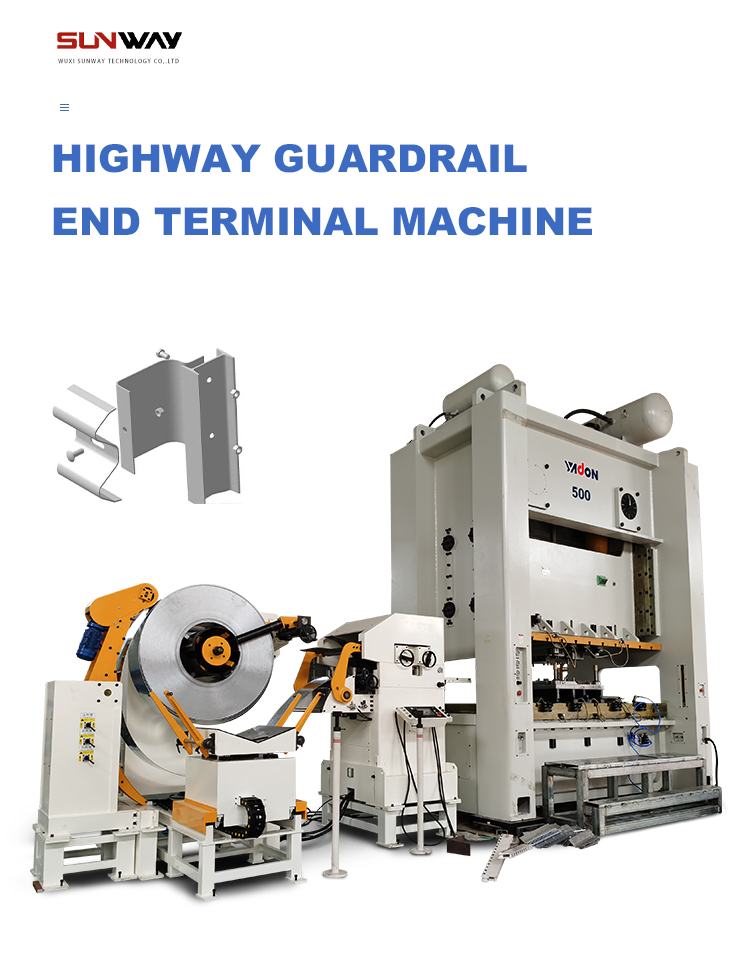
FAQs
Question | Answer |
---|---|
What is the lifespan of corrugated galvanised sheets? | Depending on maintenance and environmental factors, these sheets can last anywhere from 20 to 50 years. |
Can corrugated galvanised sheets be painted? | Yes, many types come pre-painted or can be coated with additional paint after installation. |
What is the thickness of galvanised sheets typically used in roofing? | Most commonly, thicknesses range from 0.45 mm to 1.2 mm for roofing applications. |
Are corrugated galvanised sheets environmentally friendly? | They are recyclable and have a low carbon footprint compared to other roofing materials. |
How much overlap should be used during installation? | It’s recommended to have an overlap of at least 150 mm for proper water sealing. |
উপসংহার
Corrugated galvanised sheets are a reliable, cost-effective material for a wide range of applications, from roofing to cladding. Understanding the types, benefits, and processes behind these sheets can help you make the right choice for your project. With this comprehensive guide, you’re now equipped with the knowledge to choose the right sheet, find the best supplier, and ensure long-term performance through proper installation and maintenance.