China roll forming machine is an efficient method of producing long sheet metal parts with constant cross-sections. Roll formed products have widespread applications across industries like construction, infrastructure, agriculture, automobile, railways, home appliances and more. China has emerged as a major manufacturing hub and leading supplier of quality roll forming machines and components globally.
Introduction to Roll Forming Process
Roll forming is a continuous bending operation in which sheet or strip metal is progressively formed into a desired cross-sectional profile through a series of consecutive roller dies. The forming stations continuously shape the material incrementally as it passes through at a constant speed.
Benefits of roll forming include:
- High production rates and volumes
- Consistent accuracy and tolerance control
- Versatile – wide range of profiles and products
- Cost effective for long parts or large quantities
Roll formed parts are lightweight yet strong, while using less raw material than other forming processes. This makes roll forming ideal for industries focused on saving material costs and transportation weight.
Common roll formed products include roofing and siding, racking, solar panel frames, door frames, rails, panels, enclosures and more. Materials typically formed include steel, stainless steel, and aluminum.
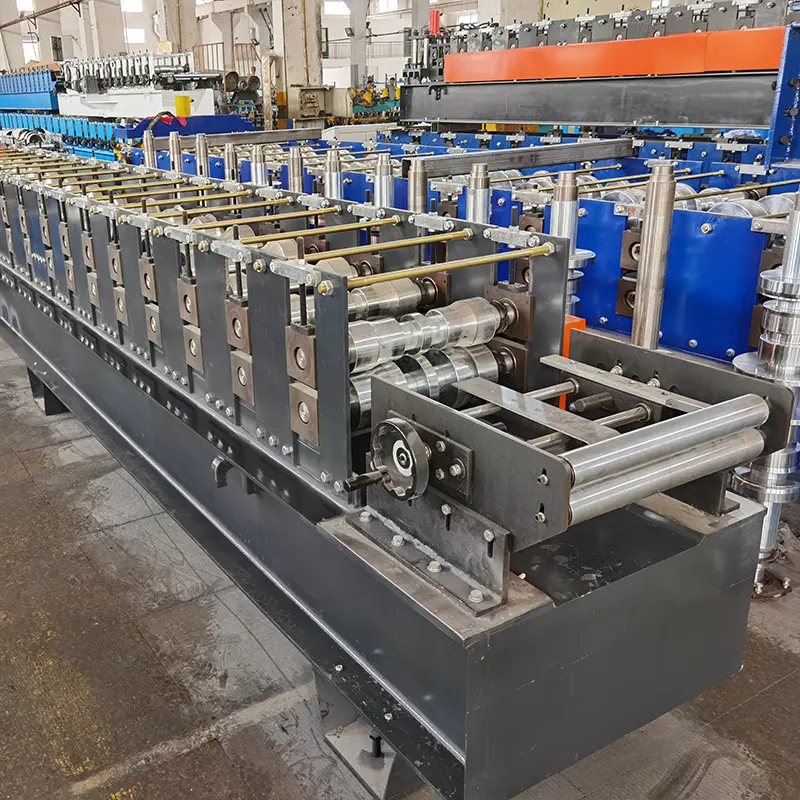
Working Principle of Roll Forming Machines
A basic roll forming line consists of the major components described below:
Material Feeding: Coiled sheet or strips of metal are loaded into an uncoiler which feeds the material into the forming section at a constant speed and tension.
Forming Section: Consecutive pairs of roller dies progressively form the material by applying bending forces as it passes through. The rollers impart the desired shape through a series of small incremental deformations along the longitudinal axis.
Cutting Unit: A rotary cutting blade slices the continuously produced formed profile into cut lengths as per specified requirements. A separate counting/stacking unit may also be integrated.
Controller: Advanced roll forming machines have PLC-based controllers for precision monitoring and control of parameters like feed speed, temperature and eccentricity during the forming process.
Optional Accessories: Decoilers, straighteners, embossing rollers, punching units, warehousing sections etc. enable customization as per end product requirements.
Forming Design and Simulation: Roll forming machines are custom configured by designers based on 3D models and simulation software to create optimal tooling layouts for achieving the desired profiles. Iterative improvements help enhance quality and accuracy.
The process allows high repetition, efficiency and flexibility in mass production of roll formed sections, with lower tooling investment costs compared to other sheet metal working methods.
Types of Roll Forming Equipment
China manufactures roll forming machines to meet diverse end-to-end production requirements:
Equipment Type | Description |
---|---|
Standard Roll Forming Lines | Most common type, configured for high volume production of metal parts with constant profile e.g. frames, enclosures. Higher speeds via fewer passes and stations. |
C- & O-Roll Forming Machines | Specialized for open profiles and frames. O- press rolls bend flanges outward simultaneously. Remove the need for deburring open tube products. |
Double Layer Roll Forming Lines | Produce hollow cavity double layer profiles utilizing two sheets concurrently through integrated welding process for channel, curved and special-shaped products. |
Flexible Roll Forming Systems | Enable easy profile changes by adjusting rollers, ideal for lower volume variable production e.g roofing profiles. Reduce tooling investment required for each shape. |
Portable Site Roll Forming Machines | Lightweight, portable rollers built for on-site installation directly near construction activity to reduce transport costs of finished products. |
CNC Roll Forming Lines | Feature advanced numeric control for precision movement of rolls, cutting length variability and complex shapes. Automated self-correction compensates for spring back effect. |
China Roll Forming Machine Suppliers
China is the largest producer of roll forming equipment worldwide, renowned for affordable pricing coupled with quality and customization.
Leading China manufacturers and popular export brands of innovative roll forming technology include:
Supplier | Year Est. | Location | Price Range |
---|---|---|---|
Botou Xianfa Roll Forming Machine Co. | 2002 | Hebei | $10,000 – $100,000 |
DINGCHENG Roll Forming Machine Co. | 1993 | Zhejiang | $20,000 – $500,000 |
JenSen Machinery Co | 1995 | Jiangsu | $30,000 – $150,000 |
JinDe Machinery Co | 1998 | Shanghai | $15,000 – $250,000 |
Golden Arrow Metal Forming Equipment Co | 2003 | Shandong | $10,000 – $200,000 |
Hebei NewVictor Special Machine Co | 2016 | Hebei | $5,000 – $50,000 |
EUROPOWER Machinery Co | 2008 | Jiangsu | $100,000+ |
UNIPRESS Machinery And Tools Co | 2009 | Hebei | $10,000 – $150,000 |
Indicative Price Range: Basic manual and semi-automatic lines from 5,000 USD while complex CNC machines exceed 100,000 USD. Wide scope of customization across all budgets.
Contact reputable suppliers before purchase to get quotes for your specific roll forming needs. On-site inspections and pre-shipment trials build confidence and validate build quality.
-
Standing Seam Roof Panel Curving Machine
-
ব্যারেল ঢেউতোলা রোল ফর্মিং মেশিন
-
Stand Seaming Roof Panel Roll Forming Machine
-
ডাউনস্পাউট পাইপ রোল তৈরির মেশিন
-
গটার রোল তৈরির মেশিন
-
Trapezoidal Panel Roll Forming Machine
-
রিজ ক্যাপ রোল ফর্মিং মেশিন
-
ডাবল লেয়ার প্যানেল রোল তৈরির মেশিন
-
ছাদের টাইল প্যানেল রোল তৈরির মেশিন
How To Choose Top China Roll Forming Machine Manufacturers?
Here are tips on selecting reliable partners for your roll forming equipment needs:
Criteria | Considerations |
---|---|
Product Quality | ISO accredited, quality control checks, stability testing data. |
Technical Expertise | Advanced R&D infrastructure, qualified engineers, proprietary innovations. |
Customization Range | Profile variability, quick changeover parts, flexible tooling designs. |
Production Capability | Capacity, batch sizes, lead times, stability. |
Components | Brand and source location of electrical, hydraulic and mechanical parts |
International Experience | Familiar with export regulations, global installations and field engineers for support. |
Services | Training, maintenance, warranty and after-sales troubleshooting support. |
Pricing | Product consistency across low to high budget equipment. Value for money. |
Reputable Chinese manufacturers offer customizable equipment catered to small and large-scale producers globally.
Roll Forming Machine Installation, Operation and Maintenance
Proper installation and routine care ensures optimal performance from your roll forming equipment over decades.
Process Stage | Guidelines |
---|---|
Site Layout Planning | Ensure adequate space for material entry, forming and exit zones. Allow operators safe movement around equipment. |
Civil Work | Prepare level concrete foundation for machine mounting, anchor bolts installation. |
Assembly | Floor mounting, sequential component connections, trial runs for working dimensions. |
Commissioning | Calibrate sensors, test emergency stops, debug control systems, validate formed profile dimensions and finishing. |
Operation | Continuous feed of clean materials, monitor sensors, lubricate moving parts, manage formed part exit and counting. |
Preventive Maintenance | Regular cleaning of scrap debris, belt tightening, fastener checks, apply lubricants, replace damaged electrical components. |
Breakdown Maintenance | Keep spare parts like forming rollers, bearings, chains, sprockets etc. Replace immediately when worn out. |
Adhering to manufacturers’ maintenance guidelines optimizes working life, minimizes breakdowns via preemptive repairs and reduces costly production downtimes.
Pros and Cons of China-Made Roll Forming Machines
Pros | Cons |
---|---|
Cost effective, economical pricing | Perception of lower build quality |
Broad customization choices | Limited proprietary technology |
Quick fabrication, mass production ability | Language barriers may hamper support |
For small and large scale buyers alike | Preference for prepayment terms |
Offer complete end-to-end equipment | Time difference can delay responses |
Innovative special application machines | Shipping damages possible |
Cater to domestic and international markets | Spare parts supply delays |
Summary: China offers versatile, affordable roll forming lines customizable for profiles, production scales and budgets. But conduct due diligence to find reliable partners.
Applications of Roll Formed Products
Roll formed sections find widespread usage across these major sectors:
Construction: Roofing, cladding, safety doors, structural frameworks, scaffolding components
Infrastructure: Drainage systems, electrical conduit, cable trays, solar mounting, highway crash barriers
Transportation: Railway carriage panels, truck trailer panels, shipping container frames
Appliances: Panels, enclosures and components for white goods, kitchen appliances etc.
Commercial: Store fixture framing, racking, food/cold storage shelving, playground slides, signage, office furniture
Automotive: Light vehicle frames, wheel arches, windshield wipers, running boards, trim parts
Other Industries: Agricultural equipment, textile machinery frames, air conditioning components
Roll formed sections offer versatility spanning decorative and structural building elements to heavy load bearing automotive and industrial hardware applications.
Roll Forming Vs Sheet Metal Processing Differences
Here we compare the core differences between roll forming and other sheet metal fabrication processes:
Criteria | রোল গঠন | Sheet Metal Processing |
---|---|---|
Method | Roller dies bend moving coil continuously | Presses stamp stationary blanks |
Lead Time | Forming speed under a minute | Slower batch processing |
Labor | Automated, low operator dependency | Manual handling between steps |
Equipment Cost | Low, only requires linear rolls | High initial tooling investment |
End Finish | Smoothened polish finish | May have pressed markings |
Dimensional Accuracy | Tight tolerance control via incremental bends | More batch-to-batch variability |
Profile Flexibility | Adjustable flexible tooling | New tools needed for each part |
Strength | Consistent, multiaxial grain flow | Lower directional strength |
Batch Size | Ideal even for large quantities | Higher volumes increase tooling wear |
অ্যাপ্লিকেশন | Mainly linear and curved profiles | Complex 3D shapes possible |
Summary: Roll forming excels for producing long lightweight parts with simple to complex cross-sections benefitting from automated high speed production. Stamping and other sheet metal processing offer benefits for small batch and intricate 3D components.
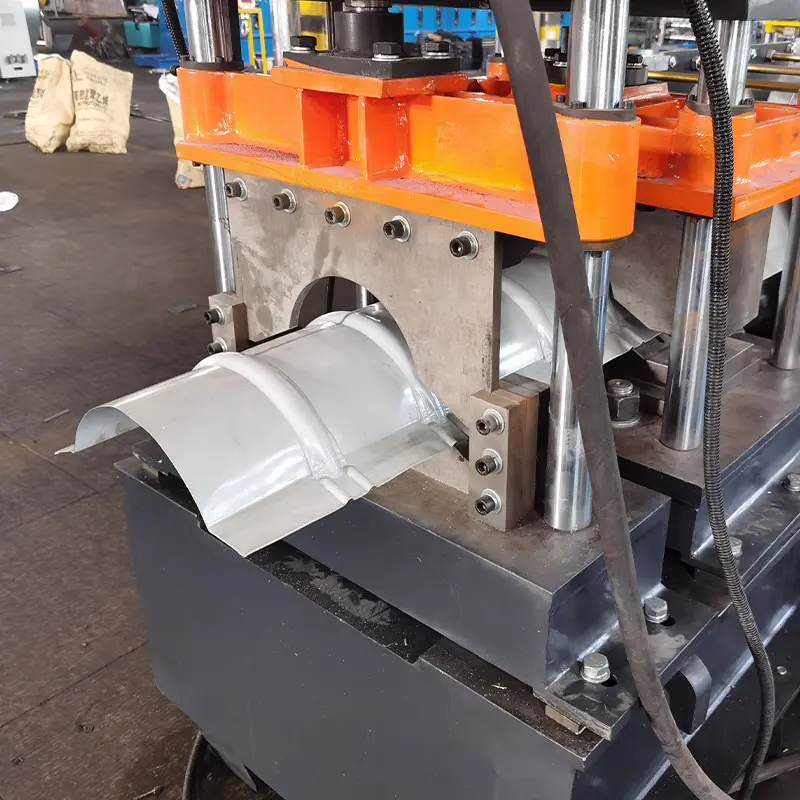
FAQ
What thickness of sheets can be roll formed? | From thin 0.15mm foils to as thick as 25mm metal plates and most alloys. Mild steel is commonly roll formed around 0.5 to 2mm thickness. |
What shapes can be roll formed? | A wide range shapes from basic circles, squares, rectangles to complex louvred profiles are possible depending upon tooling, number of roller stations and levels of automation. |
Is surface finish an issue in roll forming process? | No, the deforming rollers actually tend to smooth and brighten sheet metal. An added lubricant gives traditionally preferred matte silver metallic finish. |
Does roll forming cause thickness variations? | Overall thickness remains uniform as material uniformly stretches under tension without compression or gaps during forming. Advanced machines correct for minimal springback electronically. |
How to correct twist or shape defects? | Profile distortions can be minimized by optimizing roller layouts during design stage, plus real time PLC monitoring and adjustment of roller alignment and sheet tension levels. |
What roll forming safety measures are necessary? | Emergency stop buttons, safety barriers near moving parts, operator training. Automated lines reduce direct human involvement in the process area. |