China double layer roll forming machines refer to equipment engineered in China that continuously forms structural metal panels, roofing, decking and cladding products consisting of two distinct layers from steel coil substrates.
This guide covers standard China double layer roll former offerings, the progressive roll forming process basics, machine component technical summaries, operational guidance procedures, customization options available, supplier pricing comparisons, machine selection factors, pros vs cons considerations, and commonly asked questions regarding these lines.
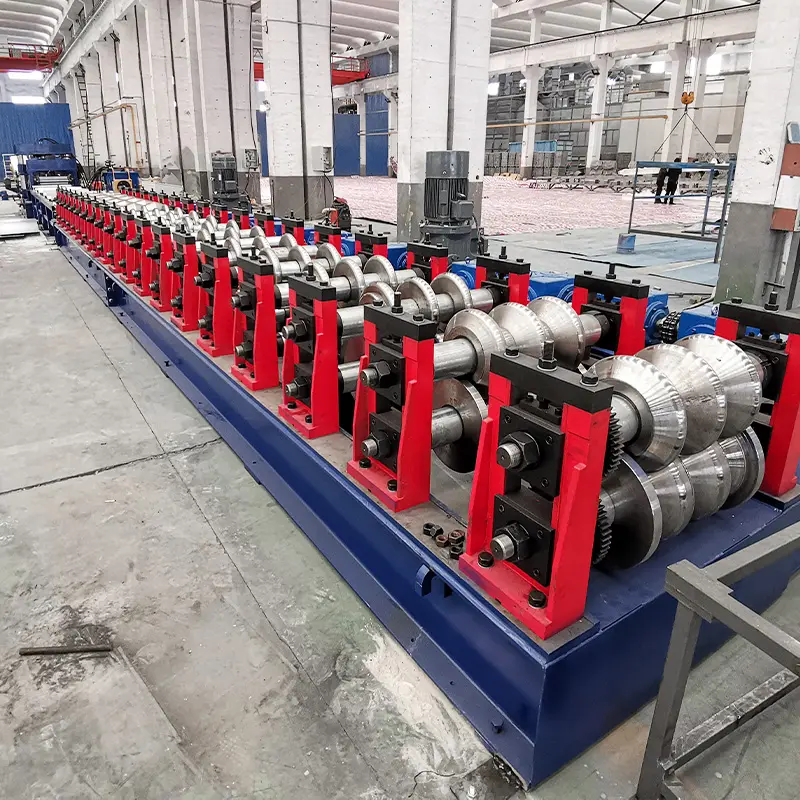
China Double Layer Roll Former Equipment Types
China double layer roll formers are offered in manual, automatic CNC programmable, and customized machine types (Table 1):
Type | Description |
---|---|
Manual | Basic manually adjustable roll dies |
Automatic | Servo feed controls with auto gauging |
Standard | Common roofing and wall panel profiles |
Customized | Unique roll sets for proprietary products |
Table 1. China Double Layer Roll Former Model Options
Configurations utilize various supporting equipment like decoilers, sheet levelers, pre-punches, cutoff tables.
How China Double Layer Roll Forming Works
The roll forming process utilizes successive sets of roller dies to progressively cold form distinct connected top and bottom metal layers from a single strip simultaneously as the coil feedstock passes through the line (Figure 1). Steps include:
- Feeding raw coiled sheet into system
- Progressively bending material through upper and lower contouring rollers
- Forming distinct but integrated panel layers
- Calibrating overall profile thickness and flatness
- Shearing cutoff panels to specified lengths
- Accumulating or coiling finished panels
Figure 1. Double Layer Roll Forming Diagram
The number of shaping stations, tool dimensional details, and process settings determine the final formed product specifications.
China double layer roll forming machine Component Details
Key China double layer roll former system components include (Table 2):
Component | Descriptions |
---|---|
Forming rollers | Solid CNC machined roller dies with profile details |
Roller stations | Upper/lower matched die sets for each layer |
Roller shafts | Gear or chain driven roller die rotation |
Sheet guides | Split guides for registered top/bottom tracking |
Feeding system | Pulls or pushes feedstock through stands |
Shearing | Hydraulic presses cut panels to length |
Leveling | Corrects incoming coil coil flatness |
Automation | Servo feed controls, gauging sensors |
Table 2. China Double Layer Roll Former Parts Summary
Customizing China double layer roll forming machine
Specialized architectural metal panel requirements involve customized roll forming solutions including:
Area | Customization Possibilities |
---|---|
Profile geometries | Unique top/bottom dimensions |
Layer configurations | Beyond two layers, multi-tiered |
Width capacity | Machines over 2.5m component widths |
Metal alloys | Custom materials from stainless steel to copper |
Added operations | Hole punching, drilling, tapping, swaging |
Automation | Advanced statistical and operational controls |
Safety | Expanded guarding, maintenance platforms |
Close design engineering collaboration between technical teams enables specialty panels.
China Double Layer Roll Former Suppliers and Pricing
Manufacturer | Location | Price Range |
---|---|---|
Foshan YSD | Foshan, China | $ |
Botou Xianfa | Botou, China | $ |
SIPNIC | Shanghai, China | $$ |
XCMG | Jiangsu, Chin | $$ |
CustomPartNet | California, USA | $$$$ |
Table 3. China Double Layer Roll Forming Machine Vendors and Ballpark Equipment Costs
Price ranges span from $8,000 for basic Chinese machinery up to the low six figures for sophisticated American engineered production lines.
Operational Procedures for China Double Layer Roll Lines
Efficient ongoing operation procedures include:
Activity | Descriptions |
---|---|
Setup | Stage strip coils, thread through stands roller guides, program automation settings, test run panels, optimize calibrations |
Operation | Monitor sheet tracking/alignment, confirm output dimensional uniformity, document any errors |
Maintenance | Replace worn rollers, lubricate bearings/slides, calibrate sensors and feed controls |
Table 4. China Double Layer Roll Former Procedures
Schedule preventative maintenance appropriately to minimize unplanned downtime losses. Continuously verify output product dimensional conformance.
Selection Factors for China Double Layer Roll Equipment
Consideration | বিস্তারিত |
---|---|
Annual volume | Match acceptable line speeds to output targets |
Part dimensions | Check against machine width capacities |
Material properties | Strength, allowable thickness range |
Added operations | Requirements for hole punching/cutting |
Budget constraints | Throughput objectives vs capital outlays |
Location factors | Available China machinery supply sources |
Expandability | Secondary future tooling, capacity increases |
Analyze current and projected manufacturing requirements against machine specifications and vendor expertise.
Evaluating Pros and Cons of China Double Layer Roll Lines
Advantages | Disadvantages |
---|---|
High speed continuous processing | Initial machinery capital investments |
Consistent uniform output quality | Customized tooling costs |
High dimensional precision standards | Setup/changeover down time requirements |
Retention of base material properties | Operation and maintenance skill needs |
Limited raw material waste | Size range constraints by model |
Scalability via added stations | Require precision monitoring |
Table 5. China Double Layer Roll Former Benefits vs Limitations
When applied appropriately for sufficient volumes, roll forming offers unparalleled manufacturing performance and efficiency advantages over alternate approaches.
Frequently Asked Questions
What thickness range can China double layer lines accommodate?
Standard models process material thicknesses from 0.5mm – ~5mm hot rolled coils and metal sheet products depending on required bend radii, drive power, and designed clearances between layers and tooling.
How fast can these China lines operate?
Average line speed production rates span 10-15 meters per minute for common materials and profiles. Appropriate feed power settings prevent tearing or distortion issues.