Overview of C Purlin Making Machine
A C purlin making machine is a specialized roll forming equipment used to manufacture C-shaped purlin sections from coiled steel sheets. These purlins serve as important structural components in the construction of industrial buildings, warehouses, and other large-scale structures. The machine’s primary function is to continuously form and cut these C-shaped sections to desired lengths, ensuring consistency and efficiency in the manufacturing process.
C Purlin Making Machine Guide
C purlin making machines are designed to streamline the production of C-shaped purlins by integrating various processes into a single, automated system. The key components of these machines typically include:
- Decoiler: This component holds and feeds the coiled steel sheet into the machine.
- Straightening and Flattening Unit: This unit ensures the steel sheet is properly straightened and flattened before entering the roll forming section.
- Roll Forming Section: This is the heart of the machine, where a series of precisely calibrated rollers gradually shape the flat steel sheet into the desired C-shaped profile.
- Punching and Cutting Unit: This unit punches holes or creates notches in the formed purlin, as per design requirements, and cuts the purlin to the specified length.
- Stacking and Packaging Unit: The finished purlins are neatly stacked and packaged for transportation or further processing.
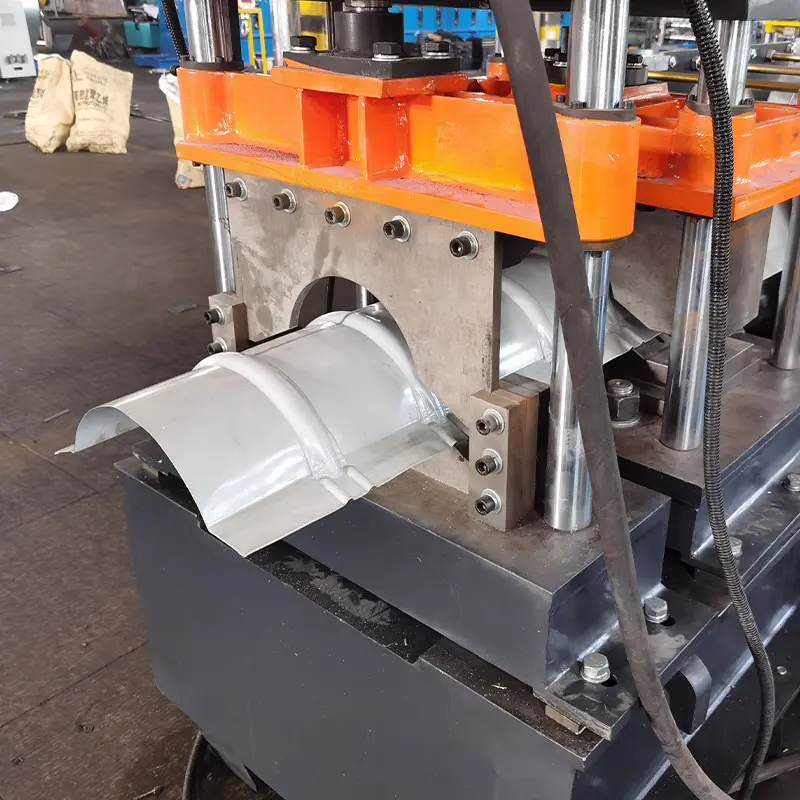
Types of C Purlin Making Machines
C purlin making machines can be broadly categorized based on their production capacity and the complexity of the purlin profiles they can manufacture. The table below outlines some common types:
Machine Type | Production Capacity | Purlin Profile Complexity |
---|---|---|
Light-duty | Up to 3 tons/hour | Simple C-shaped profiles |
Medium-duty | 3-6 tons/hour | Moderately complex profiles with punching/notching |
Heavy-duty | Above 6 tons/hour | Complex profiles with multiple bends and features |
Working Process
The working process of a C purlin making machine follows a systematic approach to transform coiled steel sheets into precisely formed C-shaped purlins. Here’s a step-by-step overview:
- Material Feeding: The coiled steel sheet is loaded onto the decoiler, which feeds the sheet into the machine at a controlled pace.
- Straightening and Flattening: The steel sheet passes through a series of rollers that straighten and flatten it, ensuring a smooth surface for the roll forming process.
- রোল গঠন: The flattened steel sheet enters the roll forming section, where a series of precisely calibrated rollers gradually shape it into the desired C-shaped profile.
- Punching and Cutting: Depending on the design requirements, the formed purlin may pass through a punching unit that creates holes or notches for bolt connections or other purposes. Finally, the purlin is cut to the specified length by a cutting unit.
- Stacking and Packaging: The finished purlins are neatly stacked and packaged for transportation or further processing.
Material Feeding, Forming, Design, and Customization
Aspect | Description |
---|---|
Material Feeding | C purlin making machines are designed to work with coiled steel sheets of varying thicknesses and widths. The decoiler component ensures a smooth and controlled feeding of the material into the machine. |
Forming | The roll forming section is the heart of the machine, where a series of precisely calibrated rollers gradually shape the flat steel sheet into the desired C-shaped profile. The number and configuration of these rollers can be adjusted to produce different purlin profiles. |
Design | C purlins can be designed with various features, such as punched holes, notches, or reinforcements, to accommodate specific structural requirements. The machine’s punching and cutting units can be programmed to create these features as per the design specifications. |
কাস্টমাইজেশন | Many C purlin making machines offer customization options, allowing manufacturers to produce purlins with varying dimensions, thicknesses, and features to meet specific project requirements or customer demands. |
Suppliers and Price Range
C purlin making machines are typically manufactured by specialized equipment suppliers. The table below lists some reputable suppliers and their approximate price ranges:
Supplier | Location | Price Range (USD) |
---|---|---|
স্যামকো মেশিনারি | USA | $50,000 – $250,000 |
Faygate | UK | $80,000 – $300,000 |
Zion Machinery | China | $30,000 – $150,000 |
Wiro Machine | ভারত | $40,000 – $200,000 |
Please note that the actual price may vary depending on the specific machine configuration, features, and customization requirements.
Installation, Operation, and Maintenance
Aspect | Description |
---|---|
Installation | C purlin making machines are large and complex pieces of equipment that require proper installation and setup. Most suppliers offer installation services or provide detailed instructions to ensure the machine is correctly positioned, leveled, and connected to the necessary utilities. |
Operation | Operating a C purlin making machine typically involves programming the desired purlin profile, setting the feed rate, and monitoring the production process. Skilled operators are essential for efficient and safe operation. |
Maintenance | Regular maintenance is crucial to ensure the machine’s longevity and optimal performance. This includes tasks such as lubricating moving parts, replacing worn rollers or cutting blades, and performing regular inspections and adjustments. |
-
রোলিং শাটার স্ল্যাট রোল ফর্মিং মেশিন
-
Highway Guardrail End Terminal Forming Machine
-
Highway U/C Post Roll Forming Machine
-
2 Waves Highway Guardrail Roll Forming Machine
-
3 Waves Highway Guardrail Roll Forming Machine
-
বৈদ্যুতিক মন্ত্রিসভা ফ্রেম রোল গঠনের মেশিন
-
দিন রেল রোল ফর্মিং মেশিন
-
দুই তরঙ্গ হাইওয়ে গার্ডেল মেশিন
-
থ্রি ওয়েভ হাইওয়ে গার্ডেল মেশিন
Choosing a Supplier
When selecting a supplier for a C purlin making machine, it is essential to consider the following factors:
Factor | Considerations |
---|---|
Reputation and Experience | Look for suppliers with a proven track record and extensive experience in manufacturing roll forming equipment. |
Product Quality and Reliability | Evaluate the supplier’s quality control measures and the reliability of their machines based on customer reviews and industry reputation. |
Service and Support | Consider the supplier’s after-sales service, availability of spare parts, and technical support, as these are crucial for maintaining the machine’s performance. |
Customization Options | Assess the supplier’s ability to offer customization options to meet your specific requirements for purlin profiles, production capacity, and automation features. |
Pricing and Delivery | Compare pricing and delivery timelines across multiple suppliers to ensure you get a competitive deal without compromising on quality or features. |
Pros and Cons
Like any industrial equipment, C purlin making machines have their advantages and limitations. Here’s a comparison:
Pros | Cons |
---|---|
High Production Efficiency | Significant Initial Investment |
Consistent Product Quality | Specialized Maintenance Requirements |
Versatility in Purlin Profiles | Potential Noise and Environmental Impact |
Automation and Labor Savings | Limited Flexibility for Small Batches |
Scalability for Increased Demand | Steep Learning Curve for Operators |
Advantages and Limitations
C purlin making machines offer several advantages over traditional manual or semi-automated methods of purlin manufacturing:
Advantages:
- Increased production efficiency and output
- Consistent product quality and dimensional accuracy
- Ability to produce complex purlin profiles with punching/notching features
- Automation and reduced labor requirements
- Scalability to meet increasing demand
- Improved safety for workers (reduced manual handling)
Limitations:
- Significant initial investment in machinery and installation
- Specialized maintenance and operator training requirements
- Potential environmental impact (noise, emissions, energy consumption)
- Limited flexibility for small batch production or frequent design changes
- Dependence on a reliable supply of coiled steel sheets
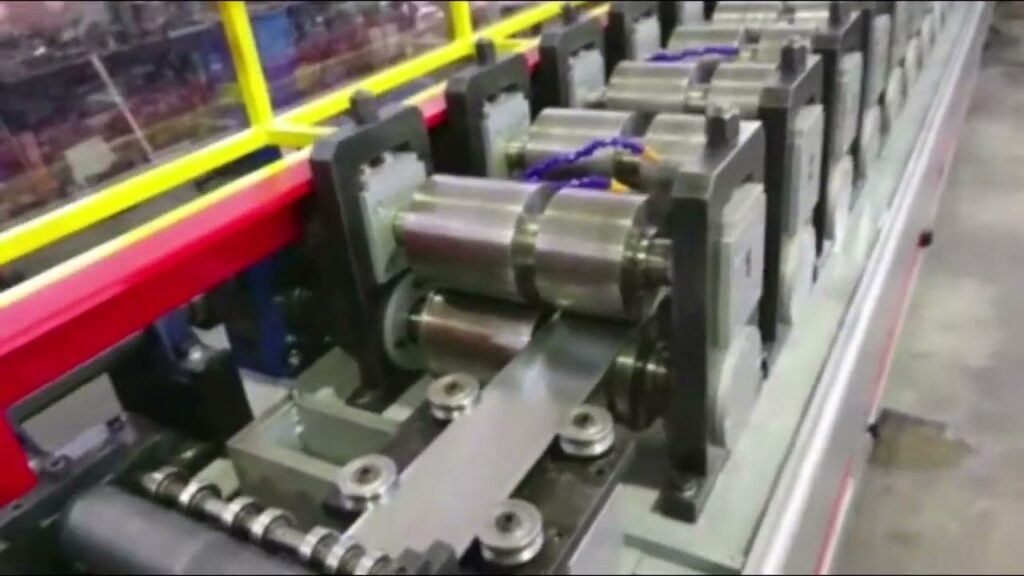
Industrial Applications
C purlins manufactured by these machines find widespread applications in various industrial sectors, including:
- Construction of industrial buildings, warehouses, and large-scale structures
- Automotive and transportation infrastructure (e.g., assembly plants, hangars)
- Power generation facilities (e.g., power plants, substations)
- Mining and mineral processing plants
- Agricultural and storage facilities
The versatility and strength of C purlins make them suitable for a wide range of structural applications, contributing to the overall integrity and durability of these industrial projects.
FAQ
Question | Answer |
---|---|
What is the typical production capacity of C purlin making machines? | Production capacity can range from a few tons per hour for light-duty machines to over 6 tons per hour for heavy-duty machines. |
Can these machines produce purlins with different profiles or dimensions? | Yes, most C purlin making machines can be adjusted to produce various purlin profiles and dimensions by changing the roller configuration and settings. |
What types of steel can be used in these machines? | C purlin making machines are typically designed to work with coiled steel sheets of varying thicknesses and grades, including hot-rolled and cold-rolled steel. |
How important is regular maintenance for these machines? | Regular maintenance is crucial to ensure the machine’s longevity and optimal performance. It helps prevent breakdowns, maintain product quality, and extend the machine’s lifespan. |
Can C purlin making machines be customized to meet specific requirements? | Yes, many suppliers offer customization options to tailor the machine’s features, automation levels, and purlin profiles to meet specific project requirements or customer demands. |