ভূমিকা
In the world of modern manufacturing, roll forming technology plays a pivotal role in shaping various materials into functional and aesthetically appealing products. Among these materials, aluminum stands out for its exceptional properties, and an aluminum roll forming machine becomes a crucial asset for many industries. This article explores the significance, advantages, process, types, considerations, maintenance, safety, applications, and future trends of aluminum roll forming machines.
Understanding Aluminum Roll Forming
Aluminum roll forming is a highly versatile and efficient process used to create a wide range of products with uniform cross-sections. It involves feeding a flat strip of aluminum through a series of carefully designed rollers that gradually bend the material into the desired shape. The process allows for complex designs and customization while maintaining the material’s inherent properties.
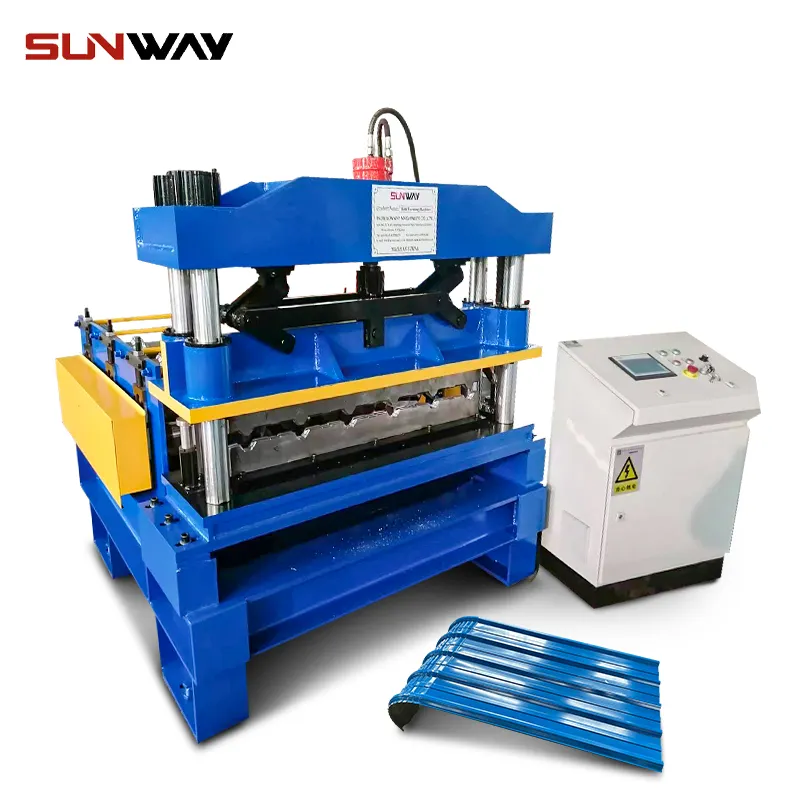
Advantages of Aluminum Roll Forming
Lightweight and Durable Properties
Aluminum’s lightweight nature combined with its inherent strength makes it an ideal material for various applications, including automotive and aerospace industries. Roll-formed aluminum components offer an excellent strength-to-weight ratio, contributing to fuel efficiency and overall performance.
Cost-Effective Manufacturing
The roll forming process optimizes material usage, reduces waste, and enhances production efficiency, making it a cost-effective manufacturing method. Its high-speed production capabilities lead to lower labor costs and increased productivity.
Versatility in Design
Aluminum roll forming allows the creation of complex profiles and shapes, providing designers and engineers with a wide array of possibilities. From simple angles to intricate cross-sections, aluminum roll forming fulfills the requirements of diverse industries.
Energy Efficiency
Roll forming consumes less energy compared to other metal forming processes, making it an eco-friendly option. The lower energy demand aligns with sustainable manufacturing practices and reduces the overall carbon footprint.
The Aluminum Roll Forming Process
The process of aluminum roll forming involves several distinct stages:
Material Preparation
Before the roll forming process begins, the aluminum coils are prepared by uncoiling and straightening them. This ensures a smooth and consistent feed into the roll forming machine.
Feeding and Pre-Punching
The prepared aluminum strip is fed into the roll forming machine, and if required, pre-punching of holes or slots is done for specific profiles.
রোল গঠন
The heart of the process, the roll forming machine’s rollers shape the aluminum strip progressively into the desired profile. The machine’s flexibility allows for multiple profiles to be produced in sequence.
Cutting and Shearing
Once the desired length of the profile is achieved, the roll-formed product is cut and sheared using various cutting mechanisms, such as flying cutoff or rotary shear.
Post-Processing and Finishing
After the roll forming process, additional operations like bending, notching, embossing, and powder coating may be performed to achieve the final product’s required specifications.
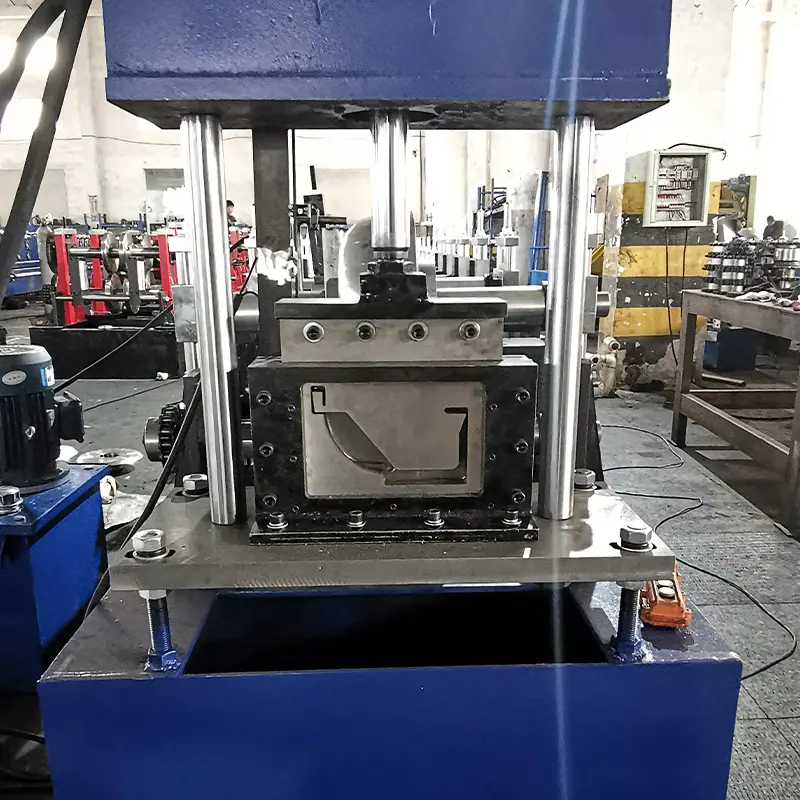
Types of Aluminum Roll Forming Machines
Aluminum roll forming machines come in different configurations to suit various production needs. The most common types are:
Single-Station Roll Forming Machines
Single-station roll forming machines are suitable for low to medium production volumes. They are cost-effective and often employed for simpler profiles.
Double-Station Roll Forming Machines
Double-station roll forming machines offer higher production capacity compared to single-station machines. They are versatile and can produce more complex profiles with increased efficiency.
Continuous Roll Forming Machines
Continuous roll forming machines are designed for high-volume production and continuous operation. They are commonly used in large-scale manufacturing plants.
Factors to Consider When Choosing an Aluminum Roll Forming Machine
Selecting the right aluminum roll forming machine for a specific application requires careful consideration of various factors:
Production Volume
Understanding the expected production volume is essential in choosing the appropriate machine type and capacity to meet demand efficiently.
Material Thickness and Width
Different roll forming machines are designed to handle specific material thicknesses and widths. Selecting a machine that suits the material dimensions is crucial for optimal performance.
Profile Complexity
More complex profiles may require machines with advanced tooling and forming capabilities to maintain precision and quality.
Automation and Control Systems
Automation features can enhance productivity and reduce manual intervention. Choosing machines with advanced control systems can lead to higher efficiency.
Budget and ROI Analysis
Considering the initial investment, operating costs, and potential return on investment is vital in selecting an economically viable solution.
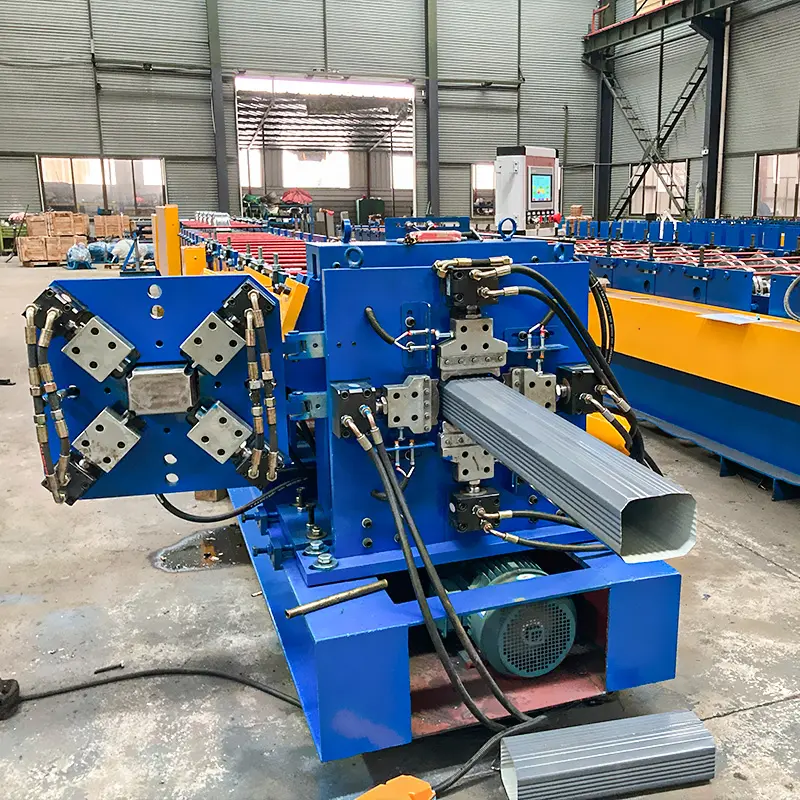
Maintenance and Troubleshooting of Aluminum Roll Forming Machines
Ensuring the smooth operation and longevity of aluminum roll forming machines involves regular maintenance and addressing common issues:
Regular Maintenance Practices
Routine maintenance includes cleaning, lubricating, and inspecting the machine components to prevent wear and tear.
Identifying Common Issues
Understanding common issues, such as misalignment, material defects, or tool wear, can aid in proactive troubleshooting.
Troubleshooting Tips
Having a troubleshooting plan in place can minimize downtime and ensure continuous production.
Safety Considerations in Aluminum Roll Forming
Safety is of utmost importance in any manufacturing process, including aluminum roll forming:
Machine Safety Features
Ensuring the machine is equipped with necessary safety features like guards and emergency stop buttons protects operators from potential hazards.
Operator Safety Guidelines
Providing adequate training and safety guidelines for machine operators helps prevent accidents and injuries.
Applications of Aluminum Roll Forming Products
The versatility of aluminum roll forming makes it suitable for various industries:
Automotive Industry
Aluminum roll-formed parts are widely used in vehicle frames, bumpers, and structural components to reduce weight and improve fuel efficiency.
Construction Sector
In construction, aluminum roll-formed profiles find applications in curtain walls, roofing, and window frames due to their strength and corrosion resistance.
Aerospace and Aviation
Aluminum roll-formed components are prevalent in aircraft structures, contributing to lighter and more fuel-efficient planes.
Electronics and Electrical
In the electronics industry, roll-formed aluminum is used for heat sinks and electrical enclosures due to its thermal conductivity and electrical insulation properties.
Furniture and Decorative
The furniture and decorative industries utilize aluminum roll-formed profiles for various designs, offering both aesthetics and durability.
Future Trends in Aluminum Roll Forming Technology
As technology continues to advance, the future of aluminum roll forming holds exciting developments:
Advancements in materials, tooling, and automation will lead to more efficient production processes.
Integrating artificial intelligence and data analytics into roll forming machines can optimize performance and enhance quality control.
The exploration of sustainable practices and materials will align with the growing demand for eco-friendly solutions.
Environmental Impact and Sustainability
Aluminum roll forming, with its recyclability and energy-efficient nature, contributes to reducing the environmental impact of manufacturing.
Sustainable practices, such as sourcing recycled aluminum and optimizing material usage, can further enhance the industry’s eco-friendliness.
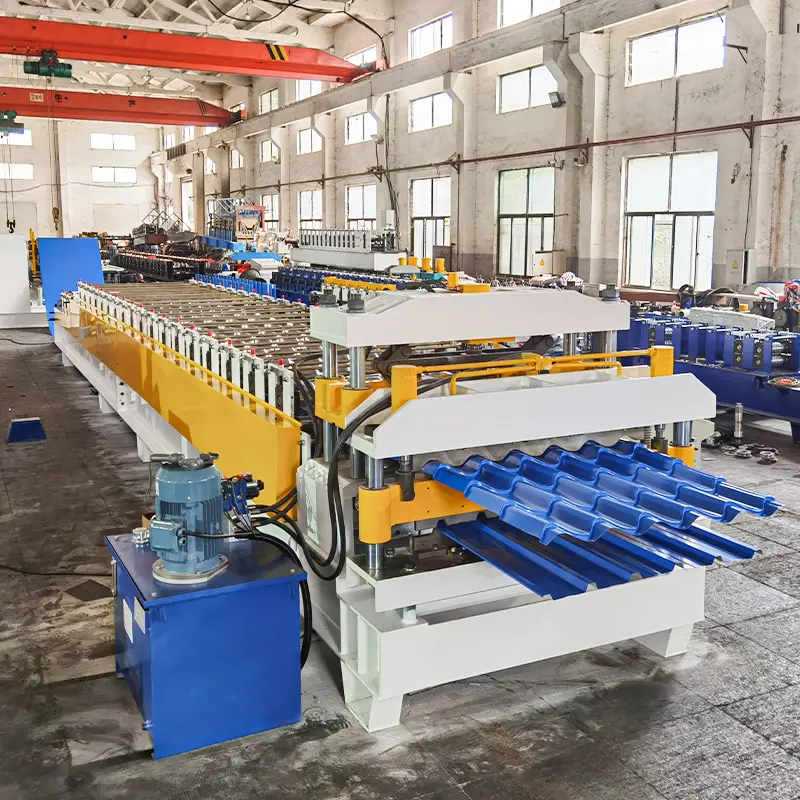
উপসংহার
Aluminum roll forming machines have revolutionized the manufacturing landscape, enabling the production of a wide range of aluminum products with precision, efficiency, and versatility. From automotive to aerospace, their impact spans across various industries, and as technology progresses, the future holds even more possibilities. By adhering to safety guidelines, considering essential factors, and embracing sustainable practices, manufacturers can harness the full potential of aluminum roll forming technology.
FAQs
Q1. What makes aluminum an ideal material for roll forming?
Aluminum’s lightweight and durable properties make it an ideal material for roll forming. Its strength-to-weight ratio and corrosion resistance contribute to its widespread usage in various industries.
Q2. Can roll-formed aluminum products be recycled?
Yes, aluminum is highly recyclable, and roll-formed products can be easily recycled, making it an environmentally friendly option.
Q3. What are some common maintenance practices for aluminum roll forming machines?
Regular cleaning, lubrication, and inspection of machine components are common maintenance practices to ensure smooth and efficient operation.
Q4. Are aluminum roll forming machines suitable for high-volume production?
Yes, there are continuous roll forming machines specifically designed for high-volume production that can operate continuously with minimal downtime.
Q5. How does aluminum roll forming contribute to sustainability?
Aluminum roll forming’s energy efficiency, recyclability, and reduced material wastage contribute to its sustainability, aligning with the global push for eco-friendly manufacturing processes.