Imagine a machine that can take a flat sheet of metal and transform it into a symphony of curves and ridges. That’s the magic of a barrel corrugated roll forming machine, a workhorse in the construction industry responsible for producing the ever-present corrugated sheets that grace roofs, walls, and even floors.
But what exactly is a barrel corrugated roll forming machine, and how does it work its wonders? Buckle up, because we’re diving deep into the world of metal shaping, exploring the different types of machines, their applications, and the nitty-gritty details that make them tick.
the Function of a ব্যারেল ঢেউতোলা রোল ফর্মিং মেশিন
At its core, a barrel corrugated roll forming machine is a metalworking marvel. It takes a continuous coil of sheet metal, feeds it through a series of precisely designed rollers, and gently bends and shapes it into a corrugated profile. Think of it like rolling out cookie dough and using patterned molds to create those delightful ridges and shapes.
Here’s a breakdown of the process:
- Feeding the Beast: The metal coil, typically made from pre-painted steel or aluminum, is loaded onto a feeding mechanism. This unwinds the coil at a controlled speed, ensuring a smooth and continuous flow of metal.
- The Shaping Symphony: The metal sheet then enters the heart of the machine – a series of strategically positioned rollers. Each roller has a unique groove or profile that progressively transforms the flat sheet into the desired corrugated shape. The number of rollers and their specific designs determine the final profile of the corrugated sheet.
- Taking Shape: As the metal sheet passes through each roller set, it’s gradually bent and molded. Imagine gently folding paper into origami shapes, but with immense precision and on a continuous metal sheet.
- The Finishing Touch: After passing through the final set of rollers, the formed corrugated sheet exits the machine. Depending on the application, the sheet might be cut to specific lengths or further processed for additional features.
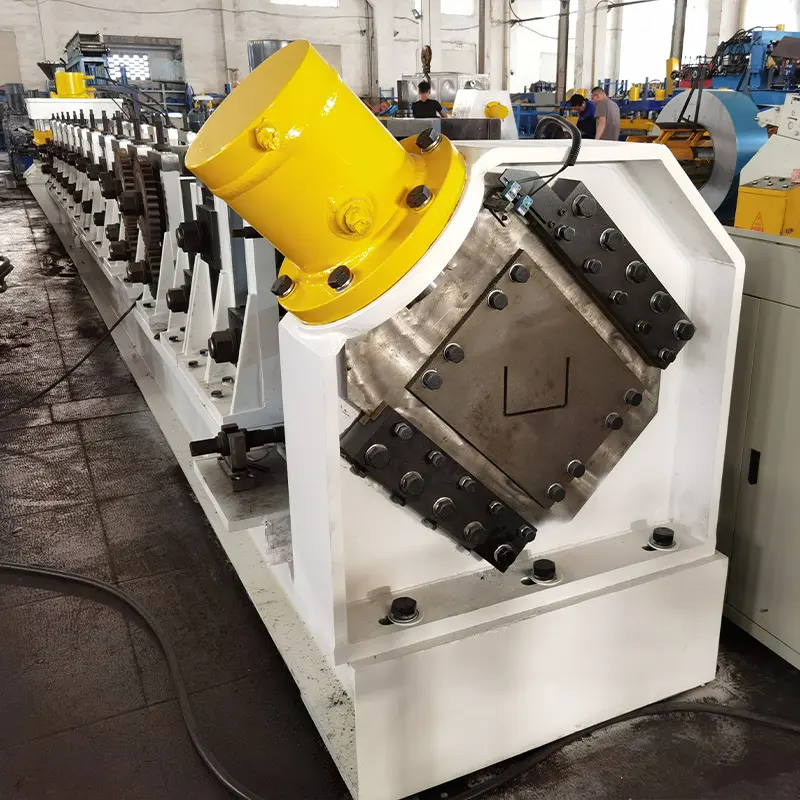
Types of Barrel Corrugated Roll Forming Machines
Not all barrel corrugated roll forming machines are created equal. Different machines cater to producing various corrugated sheet profiles, each with its own advantages and applications. Here’s a glimpse into the diverse world of these machines:
- Sinusoidal Corrugated Roll Forming Machine: This is the most common type, producing sheets with a wavy, sinusoidal profile. These sheets are known for their excellent strength-to-weight ratio, making them ideal for roofing, wall cladding, and even ceilings.
- Trapezoidal Corrugated Roll Forming Machine: This machine creates sheets with a trapezoidal profile, resembling a series of trapezoids stacked side-by-side. These sheets offer superior rigidity and are often used for industrial buildings, warehouses, and long-span applications.
- U-Shaped Corrugated Roll Forming Machine: As the name suggests, this machine produces sheets with a U-shaped profile. These sheets are lightweight and provide excellent drainage capabilities, making them perfect for wall cladding and applications where moisture management is crucial.
- Custom Corrugated Roll Forming Machine: For truly unique projects, custom barrel corrugated roll forming machines can be designed. These machines can create profiles based on specific needs, offering architects and builders the freedom to explore innovative and visually striking designs.
Key Considerations When Choosing a Machine Type:
- Desired Corrugated Profile: This is the most important factor. Select a machine that can produce the specific profile you need for your project.
- Material Thickness: Different machines are designed to handle specific metal sheet thicknesses. Ensure the machine you choose can accommodate the thickness of your chosen material.
- Production Capacity: Consider the volume of corrugated sheets you need to produce. Some machines cater to high-volume production, while others are better suited for smaller projects.
- Budget: Barrel corrugated roll forming machines can range in price depending on their capabilities and complexity. Determine your budget and choose a machine that offers the best value for your needs.
Major ব্যারেল ঢেউতোলা রোল ফর্মিং মেশিন Suppliers
The market for barrel corrugated roll forming machines is a dynamic one, with several leading manufacturers vying for dominance. Here’s a peek at some of the key players:
Supplier | Location | Product Range | Estimated Price Range |
---|---|---|---|
Purlin Machinery Manufacturing Company | China | Sinusoidal, trapezoidal, U-shaped, and custom profiles | $15,000 – $200,000 |
Roll Forming Machine Manufacturers Association | International | Connects buyers with various machine manufacturers | – |
Daya Machinery | China | Focuses on high-speed and automated machines | |
Durma Machinery | Turkey | Renowned for their |
-
Highway Guardrail End Terminal Forming Machine
-
Highway U/C Post Roll Forming Machine
-
2 Waves Highway Guardrail Roll Forming Machine
-
3 Waves Highway Guardrail Roll Forming Machine
-
দ্রাক্ষাক্ষেত্র পোস্ট রোল ফর্মিং মেশিন
-
স্বয়ংক্রিয় আকার পরিবর্তনযোগ্য সিগমা Purlin রোল ফর্মিং মেশিন
-
স্বয়ংক্রিয় আকার পরিবর্তনযোগ্য CZ Purlin রোল ফর্মিং মেশিন
-
স্বয়ংক্রিয় আকার পরিবর্তনযোগ্য Z Purlin রোল তৈরির মেশিন
-
Auto Size Changeable C U Purlin Roll Forming Machine
Advantages of Barrel Corrugated Roll Forming Machines
There’s a reason why barrel corrugated roll forming machines have become an indispensable tool in the construction industry. Here’s a closer look at the compelling advantages they offer:
- Versatility Unbound: As we’ve seen, these machines can produce a wide range of corrugated profiles, catering to diverse applications. From roofing and cladding to ceilings and even flooring, the possibilities are vast.
- Strength in Every Curve: The corrugated shape itself adds inherent strength to the metal sheet. The ridges act like mini-beams, providing superior rigidity compared to flat sheets. This translates to lighter weight structures that can withstand significant loads.
- Cost-Effective Construction: Compared to traditional building materials like concrete or wood, corrugated sheets offer a cost-effective alternative. The efficient production process of roll forming machines keeps costs down, making them an attractive option for budget-conscious projects.
- Speedy Erection: Barrel corrugated roll forming machines allow for the on-site production of corrugated sheets. This eliminates the need for pre-fabricated panels, leading to faster construction times and improved project efficiency.
- Weather Warrior: Corrugated sheets are typically made from galvanized steel or pre-painted aluminum, offering excellent resistance to corrosion and harsh weather conditions. They can withstand rain, snow, and even extreme temperatures, making them ideal for diverse climates.
- Sustainable Choice: Metal sheets used in corrugated sheets are highly recyclable. Additionally, the lightweight nature of these sheets reduces the overall weight of a building, potentially leading to lower energy consumption for heating and cooling.
- Aesthetic Appeal: While often associated with industrial applications, corrugated sheets can also add a touch of modern flair to a building’s design. The variety of profiles and colors available allows for architects to explore creative possibilities and achieve a unique aesthetic.
Considerations and Potential Drawbacks
While barrel corrugated roll forming machines offer a plethora of advantages, it’s important to consider some potential drawbacks as well:
- Initial Investment: These machines can be a significant upfront investment, particularly for high-end models with advanced features.
- Expertise Required: Operating a barrel corrugated roll forming machine requires a certain level of training and expertise. Improper operation can lead to production issues and even damage to the machine.
- Material Limitations: While these machines can handle various metals, they might not be suitable for all materials. The thickness and strength of the metal sheet need to be compatible with the machine’s capabilities.
- Maintenance Needs: Like any machinery, regular maintenance is crucial for optimal performance and longevity. The cost and complexity of maintenance can vary depending on the specific machine.
- Noise Factor: The operation of a barrel corrugated roll forming machine can generate significant noise. This needs to be taken into consideration, especially when used in close proximity to residential areas.
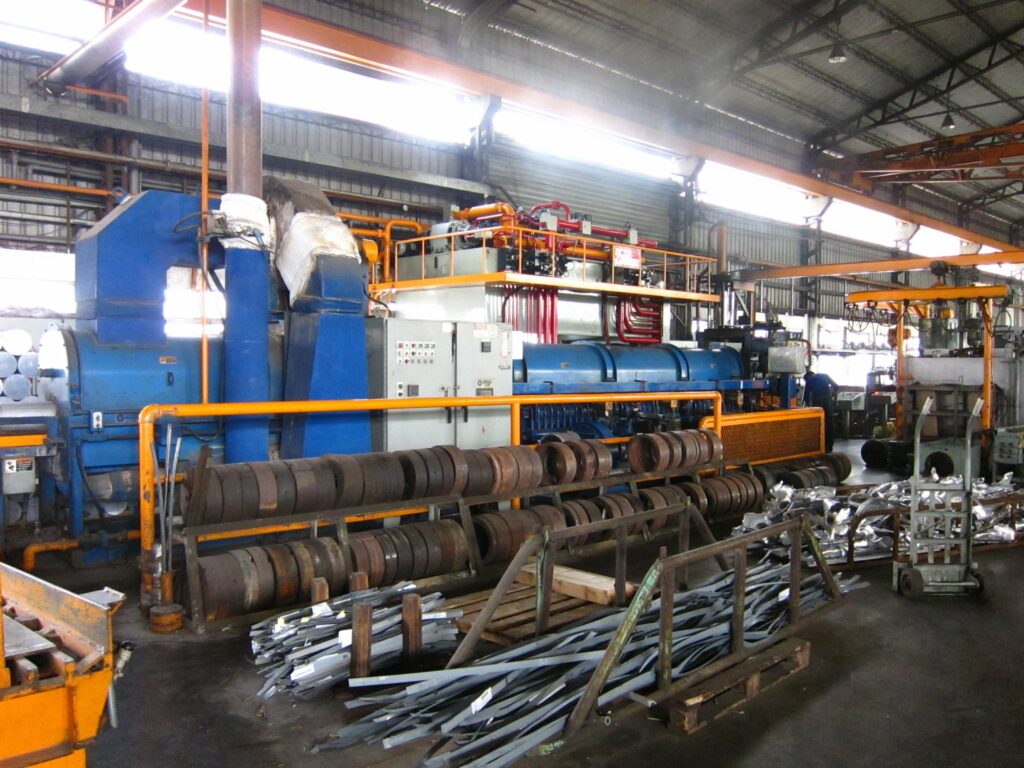
FAQ
Here are some of the most commonly asked questions regarding barrel corrugated roll forming machines, answered in a clear and concise format:
Question | Answer |
---|---|
What is the difference between a barrel corrugated roll forming machine and a regular roll forming machine? | A barrel corrugated roll forming machine specifically creates sheets with a corrugated profile, while a regular roll forming machine can produce a wider variety of shapes, including flat sheets, channels, and angles. |
Can I produce corrugated sheets with different thicknesses using the same machine? | No, in most cases, a machine is designed to handle a specific range of metal sheet thicknesses. |
How wide can the corrugated sheets be? | The width of the produced sheets will depend on the specific machine’s capabilities. Typical widths range from 3 meters to 6 meters. |
What safety precautions should be taken when operating a barrel corrugated roll forming machine? | Always wear proper personal protective equipment (PPE) like gloves, safety glasses, and ear protection. Ensure the machine is properly maintained and operated according to the manufacturer’s instructions. |
Where can I find a reliable supplier of barrel corrugated roll forming machines? | Several reputable manufacturers and distributors offer these machines. Research online marketplaces, attend industry trade shows, or consult with construction equipment specialists to find the best supplier for your needs. |
উপসংহার
Barrel corrugated roll forming machines have become a cornerstone of modern construction, offering a cost-effective, versatile, and durable solution for building projects. As technology continues to evolve, we can expect even more advancements in these machines, leading to even faster production speeds, more intricate profiles, and potentially even the ability to handle a wider range of materials.